What Gas is Used for Welding? Discover Welding Gas Types, Uses, and Tips
Published on: May 7, 2025 | Last modified: March 4, 2025
By: Joe Carter
Welding gas is a type of gas used during the welding process. It helps create a protective atmosphere around the weld, which is crucial for a strong bond.
One thing people often ask me about is what gas is used for welding? Choosing the right welding gas is super important because it can affect the quality of your welds. In my experience, using the right gas means you’ll have fewer defects and a cleaner finish.
In this blog, I’ll cover how welding gas works, different types of welding gas, preparation steps, factors that affect gas selection, common issues, aftercare tips, applications of welding gas, and alternative methods for achieving your desired welding results. You’ll find info on what is the gas used in welding and what is the most common gas used in welding, making it easier to choose what gas to use for welding.
Contents
- What Gas is Used for Welding?
- How Does Welding Gas Work?
- Types Of Welding Gas
- Steps to Prepare for Welding
- Factors Influencing Gas Selection for Welding
- What Could Go Wrong: Common Issues
- Applications Of Welding Gas
- Other Options for Achieving Desired Welding Results
- Advanced Welding Gas Techniques
- Frequently Asked Questions (FAQs)
- Conclusion
- Additional Reading
What Gas is Used for Welding?
Welding gas refers to gasses like argon and carbon dioxide, which shield the weld from contamination. They help ensure strong seams and durable joints. Common uses include MIG and TIG welding for steel, aluminum, and other metals.
How Does Welding Gas Work?
Welding gas refers to the gases used to shield the weld pool from contamination during welding. Common gases include Argon (Ar) and Carbon Dioxide (CO₂). For MIG (Metal Inert Gas) welding, a mix of 75% Argon and 25% CO₂ is often used to enhance stability and penetration. Over 75% of MIG welders prefer this blend for excellent results.
In TIG (Tungsten Inert Gas) welding, pure Argon is typically used due to its effectiveness in creating a clean and precise arc. This gas works well with stainless steel and aluminum alloys.
I’ve been down this road before; using the right gas significantly improves your weld’s quality. In my experience, a good blend reduces spatter and enhances the finish. When considering what gas to use, remember: Argon is essential for TIG, while mixtures are preferred for MIG!
Types Of Welding Gas
What are the different types of welding gas?
-
Acetylene
Acetylene is a colorless gas used for high-temperature welding. It’s commonly paired with oxygen for oxy-fuel welding. To use acetylene, set up your cutting torch, mix it with oxygen in a 1:1 ratio, and ignite it to create a flame that can exceed 3,000 °C (5,432 °F).
-
Argon
Argon is an inert gas that provides a shielding effect during welding. It’s typically used in TIG and MIG welding. To apply argon, connect your gas cylinder to the welder, adjust the flow rate to about 15-20 cubic feet per hour (CFH), and start welding.
-
Carbon Dioxide
Carbon dioxide is often used as a shielding gas in MIG welding, helping to create a stable arc and improve weld quality. To use it, set the regulator to a flow rate of around 20-30 CFH and feed it through the welding gun while maintaining an even distance from the workpiece. Selecting the right welding rod is crucial for ensuring strong and durable joints, depending on the specific requirements of your welding project. Learn more about what welding rod to use.
-
Helium
Helium is another inert gas mostly used in TIG welding. It provides deeper penetration and higher heat input. To use helium, adjust your gas flow between 15-30 CFH, depending on your application, and ensure a proper mix if combining it with argon. Selecting the appropriate welding rod is crucial for achieving high-quality welds, and learning about cost considerations for welding rods can guide your choices.
-
Hydrogen
Hydrogen is used in specialized welding applications, especially with stainless steel. It promotes clean, strong welds. To utilize hydrogen, use it alongside oxygen in controlled conditions, monitoring temperatures closely to avoid contamination.
We’ve wrapped up the different types of welding gases here. Next up, we’ll look at the steps to prepare for welding.
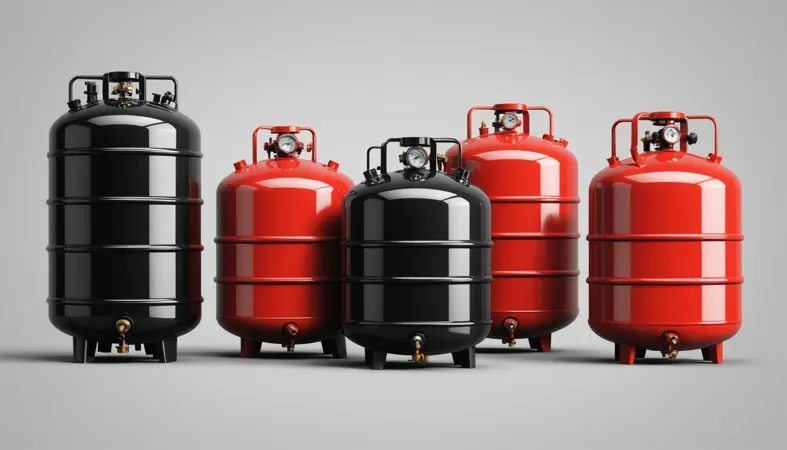
Steps to Prepare for Welding
Now, we’ll cover steps to determine the gas used for welding. Be sure to follow them all for a successful process.
-
Gather Equipment
Start by collecting your welding equipment. You’ll need a welder compatible with gas types, a welding torch, and the right hoses. Don’t forget the regulators for accurate gas flow. Ensure each component is in good shape.
If you’re using MIG welding, get a spool gun for aluminum to avoid feeding issues and work more efficiently.
-
Choose Appropriate Gas
Select the gas that suits your project. For MIG welding steel, a mix of 75% Argon and 25% CO2 works best, known as “C25.” For TIG welding, use 100% Argon. Each gas affects penetration and heat, so choose wisely based on your material and method.
Pure CO2 can be an alternative for budget welding. Remember that while CO2 provides deeper penetration, it may create more spatter. Consider the trade-offs for your specific needs.
-
Set Up the Welding Area
Arrange your workspace for convenience and safety. Ensure proper ventilation for gas buildup. The optimal gas flow range for most MIG operations is about 10-20 cubic feet per hour (Cfh).
Using a windbreak can dramatically improve gas shielding for outdoor welding. If it’s breezy, setting up a sheet of plywood can help direct the gas to the weld joint effectively.
-
Adjust Gas Flow Rate
Next, fine-tune the gas flow rate. This is crucial for achieving clean welds. A flow rate that’s too low will cause contamination, while one that’s too high can create turbulence. Use recommended rates—typically 10-18 cfh for MIG welding—and adjust according to your environment. Welders should also consider how electrode classification impacts welding processes, specifically how the E316-16 specification can influence technique and performance.
After some trial and error, starting at 15 cfh and adjusting based on performance is effective. Watch for any hissing sound; it means you may need to lower the flow.
-
Test the Equipment
Finally, test your setup. Turn on the gas and listen for any leaks. A quick dunk in soapy water can reveal hidden leaks. Once you confirm everything’s tight, light it up!
A successful test will prepare you for excellent welds. Remember, testing helps prevent unpleasant surprises during your work.
You should now have a good understanding of welding preparation steps. In the next part, we’ll discuss factors affecting gas choice for welding.
Factors Influencing Gas Selection for Welding
What factors influence the choice of gas for welding?
-
Material Type
The material you’re welding is crucial for gas selection. For example, carbon steel often uses argon and CO2 mixtures, while stainless steel benefits from pure argon.
-
Welding Process
Your welding method dictates the required gas. MIG welding usually needs a mix of argon and CO2, while TIG welding typically uses pure argon for a cleaner finish.
-
Environmental Conditions
Outdoor conditions can affect your weld. Wind, for example, can disperse shielding gases, leading to defects. In these cases, consider using heavier gases or windbreaks.
-
Desired Weld Quality
The quality of your weld influences gas choice too. For high-quality welds, such as in aerospace applications, choose a more stable gas mixture to ensure a clean, strong bead.
-
Cost Considerations
Weighing cost versus performance is key. While argon is effective, it can be expensive; mixing it with CO2 can save money while still providing good results.
That covers the factors affecting gas choice for welding. Let’s now take a look at potential problems and common issues.
What Could Go Wrong: Common Issues
Let’s explore the unique issues related to welding gas.
-
Inadequate Gas Coverage
Welding gas might not cover the weld area properly, leading to contamination. You can identify this by observing defects like porosity. Resolve it by adjusting the gas flow rate, ideally between 15-20 cubic feet per hour (425-567 Liters Per Hour). It is crucial to know the type of fire extinguisher suitable for welding to ensure safety in case of an accident; consider reviewing the appropriate fire extinguisher class.
-
Incorrect Gas Mixtures
Welding gas mixtures can be incorrect, affecting weld quality. I’ve experienced this—high carbon dioxide levels can result in weak welds. Always check the mixture for your specific welding process. For MIG, a blend of 75% Argon and 25% CO2 works well. Understanding the various techniques and challenges in removing unwanted welds is crucial for maintaining quality.
-
Regulator Malfunctions
Your welding gas regulator might fail, leading to incorrect pressure. Check the gauge; it should read between 5-15 psi (34-103 Kpa) during operation. If it fluctuates, replace the regulator.
-
Contaminated Gas Supply
Welding gas can be contaminated, causing weak arcs. Test your gas supply with an arc test—look for unusual sparks or color changes during welding. Use a filtration system to ensure clean gas flow. It’s also important to understand the factors contributing to spatter, which can be explored further in what causes weld spatter.
-
Poor Flame Control
Welding gas can create an unstable flame. If you notice varying flame properties, check for leaks or misaligned tips. The flame should be bright and stable; adjust the nozzle distance as needed.
Before welding on a vehicle, it’s crucial to understand the components that need disconnection to ensure safety and prevent damage. For specific details on what to disconnect when welding, make sure to follow proper guidelines.
We have now covered potential problems and common issues in welding. Next, we will examine the applications of welding gas.
Applications Of Welding Gas
I know welders use argon for TIG (Tungsten Inert Gas) welding, but it has many other applications, including:
- Shielding in TIG Welding: Argon offers excellent protection against contamination, especially for stainless steel and aluminum. Its inert nature makes it ideal for precision work.
- Gas Mixtures for MIG Welding: A blend of CO2 and argon is common in MIG welding, improving bead appearance and penetration. This mix works well for various ferrous metals.
- Flux-Cored Arc Welding (FCAW): Using CO2 gas enhances penetration and welding speed. It’s preferred in heavy fabrication for its efficiency.
- Oxy-Acetylene Cutting: This gas mixture cuts through thick materials quickly. Many favor it for its versatility and portability in metal workshops.
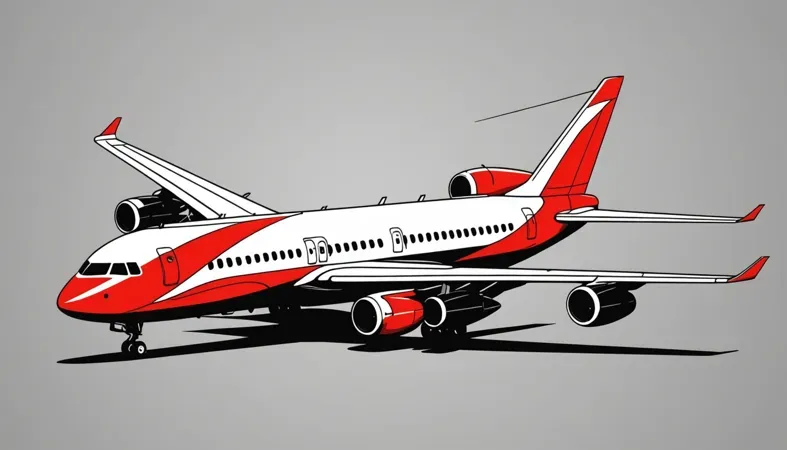
Other Options for Achieving Desired Welding Results
There are alternatives to achieving the same results when you’re not using conventional welding gases. For example, you can opt for flux-cored arc welding (FCAW) with wires like E71T-1, which doesn’t require shielding gas. Speaking from my own experience, these methods are often preferred in outdoor settings where wind can disrupt gas flow. When working with different welding environments, it’s crucial to know how to adjust welding helmets to maintain safety and efficiency.
Additionally, consider stick welding (SMAW) using electrodes such as E6011 or E7018. This approach provides excellent penetration and works in challenging conditions. Each option has its benefits, and choices depend on your project’s specific needs and conditions.
Advanced Welding Gas Techniques
Understanding advanced techniques can significantly enhance your welding skills. Let’s dive into two key aspects: gas mixes and specialized uses.
Gas Mixtures for Optimal Performance
Gas Mix | Typical Use | Benefits | Recommended Flow Rate (CFH) |
---|---|---|---|
75% Argon, 25% CO₂ | MIG Welding Steel | Stable arc, good penetration | 15-20 |
100% Argon | TIG Welding Aluminum | Clean welds, less spatter | 10-15 |
Helium and Argon | High-Heat Applications | Deeper penetration | 20-30 |
50% Argon, 50% Helium | Welding Non-Ferrous Metals | Increased heat input | 15-25 |
Specialized Gas Applications
- Stainless Steel Welding: Using a mix of argon and helium offers better heat control, ideal for strong, clean joints.
- MIG Welding in Windy Conditions: Up to 100% CO₂ can provide better shielding while outdoors; monitor for spatter.
- Plasma Cutting: High-purity argon is essential for narrow cuts with minimal thermal distortion, saving time and materials.
Frequently Asked Questions (FAQs)
Now let us look at some questions I typically get asked about welding gas.
Which Gas is Commonly Used in Welding?
Yes, the most common gas used in welding is actually a mixture of argon and carbon dioxide (CO2). This mixture can improve penetration and bead appearance significantly. Argon makes up about 75% to 80% of this popular blend, providing excellent arc stability. In some welding processes, understanding the purpose of a hot pass in welding can be crucial for achieving desired results.
What Kind Of Gas Do I Need for My Welder?
You need specific gas types for different welding processes. For MIG welding, a mix of argon and CO2 is best, whereas TIG welding mostly uses pure argon. Choosing the right gas ensures better weld quality and reduces spatter during the process.
How Much Does Argon Gas Cost?
The cost of argon gas generally ranges from $30 to $75 for a standard 40 cubic feet (1,134 Liters) tank. Prices depend on your location and supplier. It’s a small investment for achieving high-quality welds.
Is CO2 or Argon Better for MIG Welding?
Yes, both CO2 and argon can be used, but argon offers a cleaner, smoother weld. CO2 may be lower in cost, but using a blend of argon and CO2 improves overall weld quality. Many professionals prefer this mix for its superior performance.
What Welding Wire to Use With Gas?
You should use ER70S-6 wire when using a gas mix for MIG welding. It works well with argon and CO2 mixtures. This wire ensures excellent welds with less clean-up on the job, making it a favorite among welders.
What Gas Do You Weld With for Flux Core Welding?
For flux core welding, you typically don’t need external gas. Flux-cored wire contains a flux that protects the weld pool. However, if needed, you can use CO2 for better penetration on thicker materials.
Conclusion
We’ve covered a lot about what gas is used for welding. We discussed how welding gas works, the various types, essential preparation steps, factors that influence gas selection, common issues, aftercare, inspection, and application tips. You now know what’s needed for successful welding, from shielding gases to their applications.
So, what gas do you use for welding? Generally, you’ll find argon and carbon dioxide at the forefront, often combined as a mixture that suits many welding processes. In flux-cored welding, plain CO2 might be your go-to for its effectiveness. Ultimately, choosing the right welding gas blends quality and results, ensuring solid welds across multiple projects.
To expand your understanding of the welding process and explore more topics, be sure to visit What is Welding.
Additional Reading
- American Welding Society. (2021). AWS SENSE: Guidelines for Entry-Level Welders. Miami, FL: AWS.
Joe Carter is a retired welding professional with over 40 years of hands-on experience in the industry, spanning ship repair, structural welding, and even underwater projects. Joe is a master of MIG, TIG, and Stick welding. Passionate about mentoring the next generation of welders, Joe now shares his decades of expertise and practical insights to help others build rewarding careers in welding.
American Welding Society, MIG Welding, TIG Welding, Types Of Welding Gas, Welding, Welding Applications, Welding Gas, Welding Skills, Welding Techniques