What Welding Rod to Use? Tips for Mild Steel, Thin Metal, and More
Published on: April 2, 2025 | Last modified: March 4, 2025
By: Joe Carter
A welding rod is a metal stick used in the welding process. It supplies filler material, helping to join two pieces of metal together.
One question I get asked a lot is, what welding rod to use? Choosing the right welding rod is crucial for a solid weld. From my experience, using the wrong rod can lead to weak joints and costly repairs.
In this guide, I’ll cover what types of welding rods are available, how to choose the right one, factors that affect your choice, and frequently asked questions. So, whether you’re curious about what is a good all purpose welding rod or what welding rod for mild steel, you’ll find the information you need here.
Contents
What Welding Rod Should You Use?
Selecting the right welding rod depends on your material. Generally, 6011 and 7018 rods work well for mild steel, providing strong welds. For aluminum, use 4047 or 4045 rods, ideal for thin sections or special applications.
How Does Choosing the Right Welding Rod Work?
When you pick a welding rod, you’re deciding how to join materials. A welding rod transforms into molten metal during the process, creating a strong bond. Typically, rods come in various types, including 6011, 7018, and 308L. These numbers indicate the type of metal they can weld, their tensile strength, and usability. For example, a 7018 rod is effective with mild steel at a tensile strength of 70,000 psi (482.6 Mpa) and performs well for overhead jobs.
Choosing the right welding rod requires understanding the application and metal type. A good rule is to select a rod that matches your project’s specific conditions and requirements. For instance, if you’re working with thin metal, use a 6013 rod for better penetration without warping.
If I were you, I’d start with a versatile welding rod like 6013. It’s suitable for many projects, including mild steel and overhead welding. Get accustomed to it, and you’ll quickly learn which rod to use for tasks like welding aluminum or hardened steel!
Types Of Welding Rods
What are the different types of welding rods? Let’s break it down.
-
MIG Welding Rods
MIG welding rods are easy to use. Select a 0.030 to 0.035 inch (0.76 To 0.89 Mm) diameter MIG wire for thin materials like mild steel. For a clean weld, set the welder correctly and use shielding gas like argon or carbon dioxide.
-
TIG Welding Rods
TIG welding rods provide precision for detailed work. Use a 4047 rod for aluminum and a 308L rod for mild steel. Maintain a steady hand and use an AC power supply for aluminum to prevent overheating.
-
Stick Welding Rods
Stick welding rods are versatile and ideal for outdoor applications. For mild steel, use an E6011 or E6013 electrode. Maintain a consistent arc length of about 1/8 inch (3.2 Mm) and adjust your speed to avoid burn-through.
-
Semi-automatic Welding Rods
Semi-automatic rods blend manual control with automated feed. Use MIG wires ranging from 0.035 to 0.045 inch (0.89 To 1.14 Mm) for construction jobs. Set up the machine correctly, feed the wire smoothly, and ensure proper voltage settings.
-
Flux-cored Welding Rods
Flux-cored rods are excellent for outdoor welding, especially in windy conditions. Choose E71T-1 for faster welding. For optimal results, select the right diameter (Often 0.035 Inch or 0.9 Mm) and adjust your electrical settings for material thickness. When tackling more challenging positions, understanding how to weld vertically becomes crucial.
We have now covered various types of welding rods. Next, we will examine how to select the right welding rod.
Steps for Choosing a Welding Rod
Here are steps to select the right welding rod for your project.
-
Identify Your Base Material
Start by identifying the material you’re planning to weld. Common options are mild steel, stainless steel, aluminum, and cast iron. For instance, if you’re working with mild steel, consider a rod like E6013, which is suitable for general use. It fuses well at around 130-180 Amps for thicknesses between 1/8 inch (3.2 Mm) and 1/4 inch (6.3 Mm).
Another important factor to consider during the welding process is the occurrence of defects such as porosity, which can affect the strength and appearance of the weld. To tackle this issue, understanding what causes porosity in welding can be crucial for producing high-quality welds.
Each material has a preferred welding rod. For hard steel, rods like E7018 perform better. The best welders know that matching the rod to the base material is essential for strong joints. To ensure optimal results, selecting the right welding equipment is crucial. Don’t skip this key step!
Precision is crucial when working with thinner materials and it becomes increasingly important to understand how to weld thin metal.
-
Determine Welding Position
Consider your welding position: flat, overhead, or vertical. Different rods perform differently based on position. For overhead welding, an E6011 rod is ideal due to its good arc stability and penetration. The rod should handle any sag that may occur.
Mastering the technique for different orientations, such as welding uphill, can enhance your welding capabilities significantly. For additional technical guidance on this specific method, explore the effective techniques for welding uphill.
The welding position also influences your choice. E7018 rods can be challenging in vertical positions but excel in flat ones. Understanding positions is crucial for achieving strong results.
-
Choose the Right Diameter
Select a rod size that matches your project’s thickness. For thin sheet metal, use a 1/16 inch (1.6 Mm) rod. Larger projects may require 3/32 inch (2.4 Mm) or 1/8 inch (3.2 Mm). Avoid over-welding or undercutting by using the correct size.
It’s wise to keep a few sizes on hand. High-frequency welding works with a variety of metals and thicknesses. Using the wrong size can lead to weak welds. You’ll appreciate it later when your joints remain strong! Understanding the potential health risks associated with welding, it’s crucial to adopt cancer prevention measures to ensure a safer work environment.
-
Assess the Amperage Settings
Determine the appropriate amperage for your welding process, based on the type and size of the rod. For example, a 1/8 inch (3.2 Mm) E6011 rod typically requires an amperage between 70-130 Amps. Going too low or too high can result in an uneven or weak weld. When dealing with galvanized steel, understanding potential health risks like those associated with zinc fumes is crucial, as it can affect your safety during welding operations. A deeper exploration into welding galvanized steel risks is essential.
.
Test on scrap pieces first to find the perfect setting. You’ll prevent headaches by identifying the right amperage before working on your main piece. Adjust as needed for clean, professional results.
-
Consider Special Coatings
Check the coating on your welding rods. Some rods have special coatings for specific conditions, like moisture or contaminants. For instance, rods with low-hydrogen coatings, like E7018, reduce the risk of cracking, especially in mild steel repairs. Seam welding is another essential technique that should be understood in the context of using the correct rods for varying welding environments and demands.
Using the right coating can significantly enhance the strength of your weld. I found that using the wrong coating on aluminum caused serious problems; the welds didn’t hold. Match the coating to the working conditions and material type!
We covered the steps for selecting a welding rod. Next, we will explore which welding rod is best for specific applications.
Choosing the Right Welding Rod for Specific Applications
It’s essential to align the welding rod with your specific application. Let’s explore some common scenarios and the matching rods.
Application | Recommended Welding Rod | Key Features |
---|---|---|
General Purpose (Mild Steel) | E6013 | Easy to use, all-position, produces smooth beads. |
Heavy Structural Steel | E7018 | Low-hydrogen, strong welds, ideal for stress applications. |
Thin Sheet Metal | E6012 | Good penetration, minimizes warping, fast travel speed. |
Aluminum Welding | 4047 | Excellent fusion, good for thin sections and repairs. |
Cast Iron | Nickel 99 | High strength, good for repairing cast iron components. |
Outdoors in Windy Conditions | E6011 | Good arc stability, less affected by drafts. |
We covered selecting the appropriate welding rod for various applications. Next, we will discuss the factors influencing your rod selection.
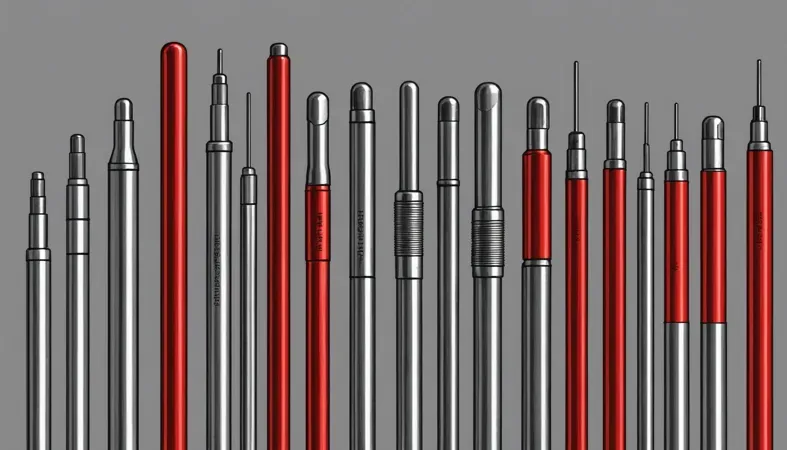
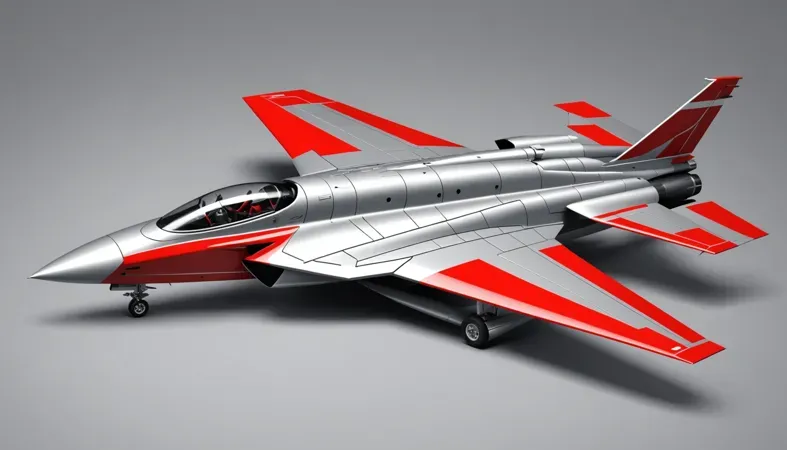
Factors Affecting Your Choice Of Welding Rod
What factors impact your choice of welding rod?
-
Material Compatibility
Using the right rod for the base metal is crucial. For instance, mild steel rods (E6011, E6013) excel on mild steel. For high-strength steel, you’ll need an electrode like E7018.
-
Welding Position
The welding position—flat, horizontal, vertical, or overhead—affects your rod choice. Some rods, like E6011, are versatile for various positions. However, for overhead welding, E7018 offers better control and less spatter. In welding processes, a hot pass is crucial for ensuring a clean weld, removing impurities and enhancing fusion. Learn more about what a hot pass in welding entails.
-
Electrode Coating
Pay attention to the coating on the rod. Coated rods provide a shielding gas that helps prevent oxidation. For example, cellulose-based rods (E6010) are great for deep penetration, while low-hydrogen rods (E7018) are ideal for sensitive applications.
-
Base Metal Thickness
The base metal thickness dictates the rod diameter you’ll need. For metal under 3 mm (1/8 Inch), a smaller rod (E6013 1.6 Mm – 2.4 Mm) works well. For welding over 6 mm (1/4 Inch), choose a larger rod (E7018 3.2 Mm or Larger) to ensure proper fusion.
-
Environmental Conditions
Welding in wind or moisture can affect weld quality. For outdoor welding, use rods like E6013, which are formulated to withstand adverse weather. Indoors, you have more options and can use rods designed for stability.
We have now covered the factors influencing your selection of welding rods. Next, we will examine common questions and answers.
Frequently Asked Questions (FAQs)
Now let us look at some questions I typically get asked.
How Do I Know Which Welding Rod to Use?
How do I know which welding rod to use? You can determine which welding rod to use based on the materials you’re working with. For different metal types, like steel or aluminum, there’s a rod that’s optimized for each, ensuring a strong weld.
Which Welding Rod is Better, 6011 or 6013?
Which welding rod is better, 6011 or 6013? The 6011 rod is better for dirty or rusty surfaces, while 6013 works great on cleaner materials. Choosing one depends on your project needs and the condition of the metal.
What is a 7018 Welding Rod Used for?
What is a 7018 welding rod used for? The 7018 welding rod is commonly used for mild steel welding. It provides high strength and low hydrogen, which cuts down on cracking in critical applications.
What Welding Rod Should a Beginner Use?
What welding rod should a beginner use? Beginners should start with 6013 rods as they are easy to control. They also produce a smooth bead and require less skill to use effectively.
What Welding Rod Do I Use for Aluminum?
What welding rod do I use for aluminum? Use a 4047 or 5356 rod for welding aluminum. They provide good strength and weld quality, ensuring a solid connection in your aluminum projects.
What Welding Rod Do I Use for Overhead Work?
What welding rod do I use for overhead work? For overhead welding, the 7018 rod works best as it has better slag control, preventing drip and ensuring a clean finish.
Conclusion
We covered various topics related to what welding rod to use, such as types of welding rods, choosing the right one for your project, and factors that affect your choice. We also discussed the steps for selecting a welding rod and answered some common FAQs. These elements can help you make the best decision.
Hopefully, I was able to impart some of my experience in selecting the right welding rod. To put it simply, if you’re welding mild steel, aim for an E6011 or E7018 rod. For thinner materials, consider an E6013. Remember, each project has unique needs, so the right welding rod varies based on factors like material thickness and position.
If you’ve found this information helpful, consider exploring more resources on What is Welding to enhance your knowledge further.
References
- American Welding Society. (2015). AWS D1.1/D1.1M: Structural Welding Code – Steel. Miami, FL: AWS.
- Lancaster, J. F. (1999). The Physics of Welding (2nd ed.). Oxford, UK: Pergamon Press.
- American Welding Society. (2020). AWS Welding Handbook: Welding Science and Technology (Vol. 1). Miami, FL: American Welding Society.
Joe Carter is a retired welding professional with over 40 years of hands-on experience in the industry, spanning ship repair, structural welding, and even underwater projects. Joe is a master of MIG, TIG, and Stick welding. Passionate about mentoring the next generation of welders, Joe now shares his decades of expertise and practical insights to help others build rewarding careers in welding.
Aluminum Welding, American Welding Society, Construction, MIG Welding, Mild Steel, TIG Welding, Welding, Welding Rods, Welding Safety, Welding Techniques