How to Weld Thin Metal? A Guide to Techniques, Equipment, and Common Issues
Published on: January 21, 2025 | Last modified: March 4, 2025
By: Joe Carter
I often hear people ask how to weld thin metal. It’s vital to learn this skill to avoid damaging the material. From my own experience, using the wrong technique can lead to burn-throughs, so understanding the right approach is a must.
In this guide on how to weld thin metal, we’ll cover what thin metal is, types of thin metals and their weldability, necessary tools, steps to weld, precautions to take, types of welding suitable for these materials, factors that affect welding, solutions for common problems, aftercare, and some key benefits. Plus, I’ll touch on typical applications of thin metal welding and other options for joining these materials.
Contents
- How to Weld Thin Metal?
- What is Thin Metal?
- Types Of Thin Metals and Their Weldability
- Prerequisites: What Do You Need?
- Steps to Weld Thin Metal
- Precautions
- Types Of Welding for Thin Metals
- Factors Affecting Thin Metal Welding
- How to Address Common Problems With Thin Metal
- Aftercare, Inspection, and Advanced Tips for Welding Thin Metal
- Advanced Techniques for Welding Thin Metal
- Key Benefits Of Welding Thin Metal
- Typical Applications Of Thin Metal Welding
- Other Options for Joining Thin Metal
- Frequently Asked Questions (FAQs)
- Conclusion
- References
How to Weld Thin Metal?
Thin metal refers to sheets that are less than 1/8 inch (3.2 Mm) thick. To weld thin metal, use MIG or TIG methods at low settings, like 50–70 amps. Applications include auto repairs and HVAC systems. It’s tricky, but doable!
What is Thin Metal?
Thin metal refers to sheets or sections of metal with low thickness, typically less than 1/8 inch (3.175 Mm). Common examples include aluminum, steel, and stainless steel sheets ranging from 0.008 inch (0.2 Mm) to 0.080 inch (2 Mm). Thin metal is essential in applications requiring lightweight, high-strength materials, often used in the automotive and aerospace industries. According to ASTM standards, metals classified as thin are usually less than 3 mm thick, significantly affecting their welding and fabrication properties.
When you start welding thin metal, consider techniques to avoid warping or burning through it. Personal experience shows that using the right amperage and travel speed is key; too much heat can ruin your project. Choosing the right welding method, like MIG (Metal Inert Gas) or TIG (Tungsten Inert Gas), can determine your success with thin metal.
I remember using thin aluminum sheets for a custom project on my motorcycle. The challenge was figuring out how to weld thin aluminum without burning through. I learned that maintaining a steady hand and the right settings—about 100 amps for a 1 mm sheet—helped a lot. Mastering your technique is crucial for welding thin metal effectively, whether for fun projects or more extensive builds.
Types Of Thin Metals and Their Weldability
What types of thin metals will you be welding?
-
Aluminum
Aluminum is lightweight and corrosion-resistant. Use a TIG (Tungsten Inert Gas) welder at 130-180 amps for thin sheets (1-3 Mm). Start with clean materials.
-
Stainless Steel
Stainless steel is strong and rust-resistant. Use a MIG welder set to about 14 volts and a wire speed of 150-260 inches per minute. Keep it clean, and consider using argon gas for better penetration. If you’re curious about techniques for MIG welding stainless steel, integrating argon can enhance your welds.
-
Carbon Steel
Carbon steel is tough and versatile, suitable for various applications. Use a MIG welder set at 70-90 amps. Ensure you have the right gas mix, like 75% argon and 25% CO2, for effective welding.
-
Galvanized Steel
Galvanized steel has a zinc coating for rust protection but can be tricky to weld. Use a MIG welder with E70S-6 wire at around 70 amps. Work in a well-ventilated area, as zinc fumes can be harmful. Explore techniques for welding galvanized steel to ensure safe and effective results.
-
Cast Iron
Cast iron is brittle but strong, often used in pipes and machinery. Preheat to about 500°F (260°C) before using a stick welder with a specialized rod like E308. Keep the heat low to prevent cracking.
You should now have a good understanding of thin metal types and their weldability. In the next part, we’ll discuss necessary tools and requirements.
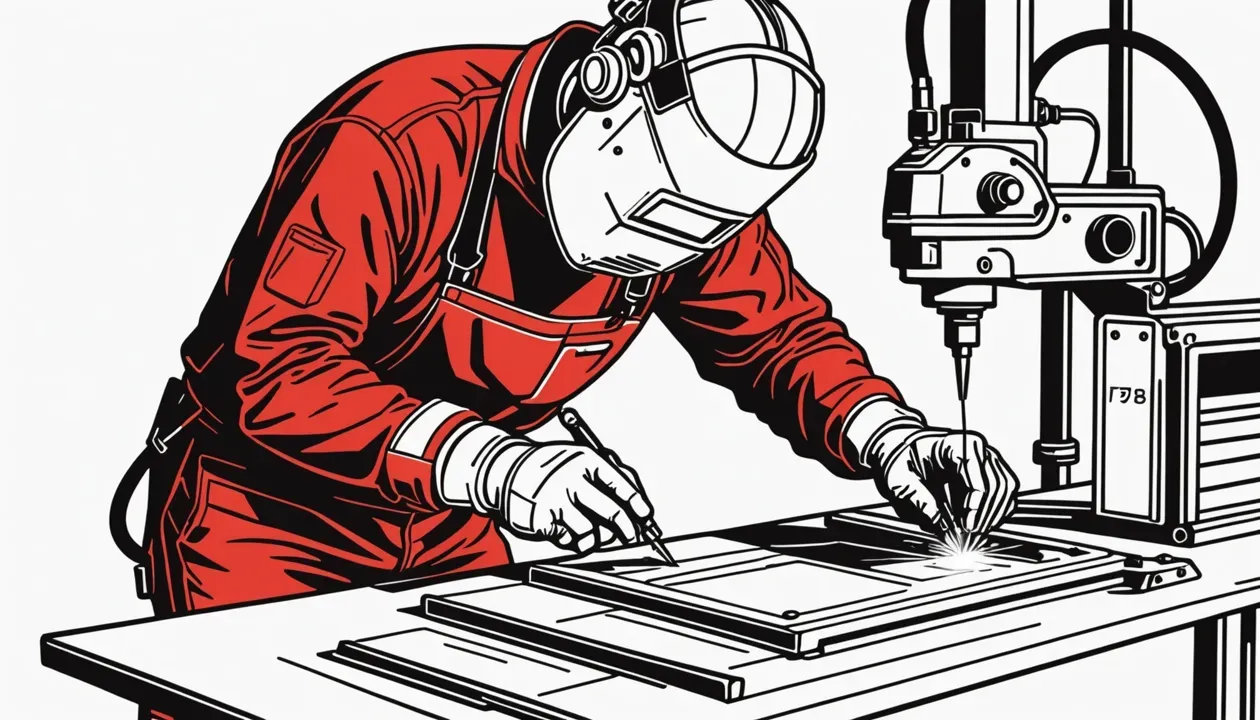
Prerequisites: What Do You Need?
What do you need to start welding thin metal?
- MIG Welder: You’ll need a MIG welder, like the Lincoln Electric Power MIG 210 MP. It’s essential for smooth, controlled welding of thin metal, typically offering settings for 0.6 mm (0.023 In) wire.
- Welding Wire: Use ER70S-6 welding wire, such as the Lincoln Electric 0.030″ Spool. This wire’s effective for thin materials because it provides a strong, clean weld.
- Shielding Gas: A blend of 75% Argon and 25% CO2, like Lincoln Electric C25, is important. It protects the weld pool from contamination, which is crucial for thin materials.
- Welding Cart: A sturdy welder cart, such as the Eastwood Deluxe Welding Cart, keeps your welder and gas bottles organized. You want everything within reach to focus on perfect welding.
- Metal Surface Prep: Use a wire brush or flap disk. Cleaning the surface with a 40-grit flap disk is vital for a strong bond on thin metals—no rust or grease!
We have now covered the necessary requirements for welding. Next, we will examine the steps to weld thin metal.
Steps to Weld Thin Metal
Here are the steps for effectively welding thin metal. Follow them closely for excellent results.
-
Prepare the Metal Surface
Clean your metal surface thoroughly. Remove rust, dirt, or grease using a grinder or solvent. A clean surface ensures a good bond. If your metal is 1 mm (0.04 In) thick or less, use a wire brush for a delicate touch. A smooth surface aids penetration, which is crucial for thin metals that warp easily. Understanding how to weld thin metal can also help determine the best techniques for minimizing warping. Lightly scuffing the area can help the weld hold better. The cleaner, the better!
.
-
Select the Appropriate Welding Technique
Choose the right method based on the metal type. For thin steel, I often prefer MIG (Metal Inert Gas) welding due to its speed and ease. For aluminum, flux-cored welding is popular but more challenging. Each method requires different gas settings, so pay attention! I’ve learned that using an argon gas mix with MIG on aluminum yields smoother welds. Set your welder to the lowest heat setting to avoid burning through the metal. Understanding the best welder for aluminum is vital to achieving quality results. It’s often a balancing act!
-
Set Up the Welding Machine
Configure your welding machine for the metal thickness. Set your MIG welder to a wire feed speed of 275 inches per minute (7 Mm/sec) for thin steel. Adjust the voltage setting to around 17-18 volts. These settings help produce a nice bead without excessive heat. Properly setting up your MIG welder for sheet metal ensures effective welding with minimized heat distortion. Consider using a backing bar or piece of scrap metal behind the work. This reduces warping and provides support—it’s a handy trick that makes a noticeable difference when welding thin sheet metals!
.
-
Start the Welding Process
Begin welding by tacking the joints in several spots before moving along the seam. This keeps everything aligned and prevents warping. Hold the torch at a 10-15 degree angle to the work. Move steadily for a consistent bead, stopping briefly at corners for a quick pulse to control the metal’s heat.
Practice moving in a small circular pattern to distribute heat evenly. Don’t linger too long in one spot. If you see white smoke, you might be burning through; ease up and adjust your technique on the fly!
We’ve wrapped up the steps for welding thin metal here. Next up, we’ll look at important precautions to take.
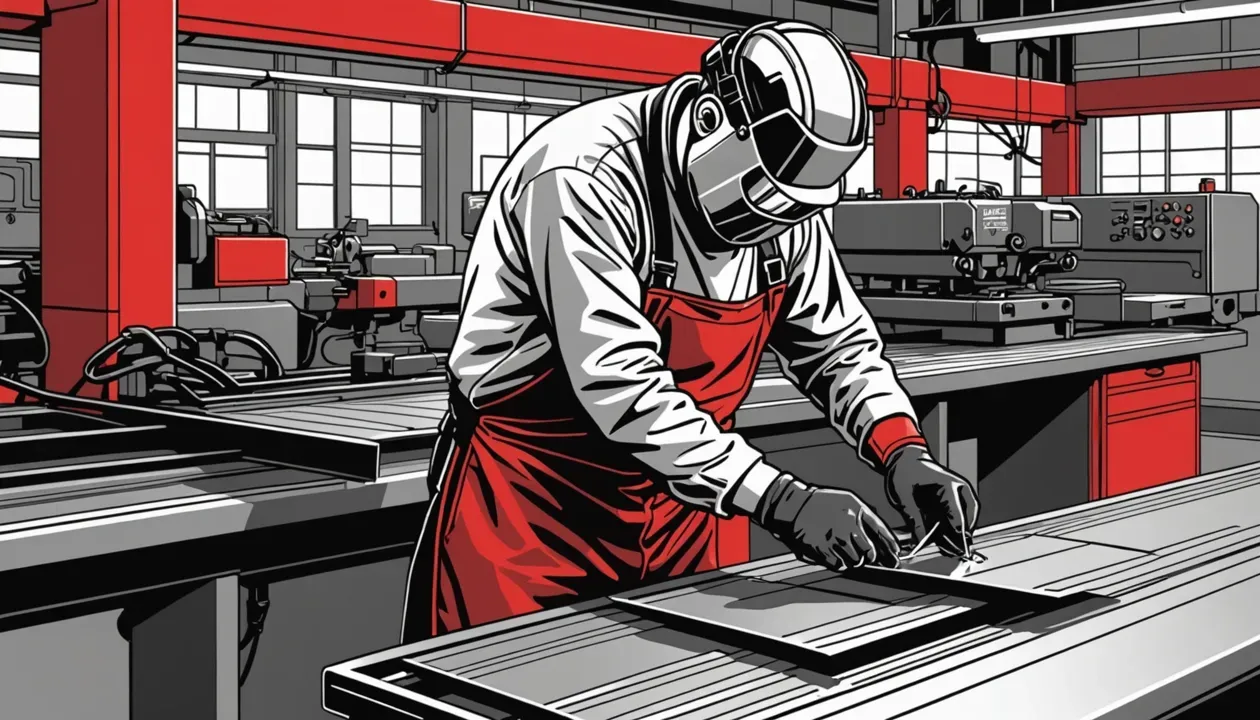
Precautions
Let’s cover essential safety measures for welding thin metal.
- Use Appropriate Filler Material: A lighter filler minimizes heat. I recommend ER70S-2 for MIG welding.
- Ventilation: Ensure good airflow to avoid fumes and gas buildup. Use a fan or work outside when possible.
- Wear Protective Gear: Always wear gloves and a welding helmet. Leather gloves, like Miller Welding Gloves, protect your hands.
- Keep a Fire Extinguisher Nearby: Accidents happen; be prepared. A Type ABC extinguisher works well.
Remember, safety is your top priority—I take it seriously.
We have now covered precautions for welding. Next, we will examine different types of welding suitable for thin metals.
Types Of Welding for Thin Metals
Let’s discuss the types of welding suitable for thin metals: MIG, TIG, Stick, Spot, and Flux-Cored Arc Welding.
-
MIG Welding
MIG welding, or Gas Metal Arc Welding (GMAW), uses a continuous solid wire to melt and join metals. It’s ideal for thin metal because you can control heat easily, reducing the risk of burn-through. Typical wire speeds range from 3.5 to 22.5 m/min (12 to 74 Ft/min), giving you flexibility when welding thin steel or aluminum. Discover more about how MIG welding is best utilized in various applications to maximize efficiency.
-
TIG Welding
TIG welding, or Gas Tungsten Arc Welding (GTAW), uses a non-consumable tungsten electrode to create the weld. TIG produces cleaner and more precise welds than other methods, making it perfect for very thin metals. You can set the amperage from 5 to 200 amps to match the material’s thickness and type.
-
Stick Welding
Stick welding, or Shielded Metal Arc Welding (SMAW), uses a melting electrode to form the weld. It’s typically better for thicker metals, but you can use it for thin materials by choosing the right electrode type and diameter. A 3/32” (2.4 Mm) electrode often works well, operating around 40 to 60 amps for thin steel.
-
Spot Welding
Spot welding joins two or more metal pieces by applying heat and pressure at specific points. This method is effective for thin metals because it minimizes heat input to surrounding areas, preventing burns. Spot welding is common in the automotive industry, typically achieving depths of 0.5 mm or less for optimal results.
-
Flux-cored Arc Welding
Flux-Cored Arc Welding (FCAW) uses a hollow wire filled with flux to create a weld pool. It’s excellent for outdoor work and can handle dirty or rusty surfaces. A detailed understanding of FCAW’s unique process can enhance technique and efficiency. However, be cautious; when welding thin metals, set your wire feed speed to 3.0 to 5.2 m/min (10 to 17 Ft/min) for better control and to avoid burn-through.
Factors Affecting Thin Metal Welding
What factors impact your ability to weld thin metal effectively?
-
Material Thickness
Welding thin metal typically involves materials under 3 mm (0.12 In). For example, aluminum around 1 mm (0.04 In) requires precise heat control to prevent burn-through.
-
Welding Speed
Your speed during welding is crucial. Go too fast, and you risk weak joints; go too slow, and you can melt through the metal.
-
Heat Input
I’ve experienced this before. Using a MIG welder with settings under 100 A (Amps) helps maintain control while welding thin materials.
-
Welding Technique
Techniques vary for different metals. For instance, oscillating the torch can reduce heat concentration and prevent distortion in thin steel during welding.
-
Joint Design
Joint design affects weld strength. A beveled joint can increase penetration but must be balanced with control to avoid excessive heat on thinner pieces.
How to Address Common Problems With Thin Metal
Let’s examine specific issues when working with thin metal.
-
Burn-through
Thin metal can melt too quickly. Adjust your welder settings to a lower amperage (15-40 Amps) and move faster. Check for holes after welding for signs of burn-through.
-
Inadequate Penetration
I’ve encountered this issue with thin metal. Slightly increase the amperage and clean the surface. Check for penetration visually and perform a bend test on a scrap piece.
-
Distortion
The light weight of thin metal causes warping. Use tacks to hold pieces together and stitch weld. Inspect welds carefully and use clamps to reduce movement.
-
Weak Welds
Proper technique is crucial for thin metal. Maintain a consistent travel speed and keep the arc short. Test the strength with a pull test.
-
Porosity
Thin metal can trap contaminants. Clean surfaces and ensure good shielding gas coverage. Look for holes or pinholes to identify porosity.
Aftercare, Inspection, and Advanced Tips for Welding Thin Metal
Here are crucial aftercare and inspection tips for your projects, plus advanced techniques for experienced welders.
Aftercare Techniques
After welding thin metal, clean the weld joints immediately with a wire brush, around 0.08 mm thick. This helps remove spatter, reveals potential defects, and improves corrosion resistance. Clamp your pieces for at least five minutes while they cool to ensure optimal integrity.
Inspection Methods
Start inspection with a visual check for undercuts or craters—even as small as 0.5 mm can compromise strength. Use tools like a magnifying glass for detailed examination. I recommend the GSI 3D Inspection Gauge, which simplifies this process and allows for secure evaluations in tight spaces.
Advanced Techniques for Welding Thin Metal
Welding thin metal can be tricky. Here are some advanced techniques that elevate your welding game.
Pulsed MIG Welding
Pulsed MIG welding allows for better heat control. This technique cycles the welding current between a high peak and a low background. By doing this, you minimize the heat input, reducing the risk of burn-through. Learn about the advantages of MIG welding that make it a preferred choice for many applications. Here’s a quick comparison:
Setting | Effect |
---|---|
High Peak (e.g., 120 A) | Penetration for the weld |
Low Background (e.g., 30 A) | Less burn-through on thin materials |
Stitch Welding
Stitch welding involves creating short, intermittent welds rather than a continuous bead. This technique helps control heat and can prevent warping. Discover more about what stitch welding entails, especially its application on thin sheets, reducing the overall heat input, and providing better control over the weld’s appearance.
Backing Bars
Using backing bars is another expert trick. Place a piece of scrap metal behind your weld. It can absorb the excess heat and offer support to prevent warping. This technique is particularly effective when working with thin sections that tend to twist under heat.
Cooling Techniques
After welding, let your workpiece cool slowly. Rapid cooling can lead to brittleness and cracking. Consider placing it on a heat sink to maintain appropriate temperatures.
Key Benefits Of Welding Thin Metal
The biggest advantage of welding thin metal is precision. I used it for a delicate art project, and the results were stunning.
You also gain several auxiliary benefits. First, it minimizes warping, ensuring your pieces fit perfectly. Second, it’s cost-effective since you use less material. Third, it’s great for joining different metals. Last but not least, it speeds up production with less cleanup required.
Typical Applications Of Thin Metal Welding
Thin metal welding serves various specific tasks, including:
- Automotive Repair: Used for patching and fabricating lightweight panels. It minimizes weight without compromising strength.
- HVAC Ductwork: Ideal for joining thin sheets of stainless steel or aluminum. It’s durable and resistant to corrosion.
- Art and Sculpture: Artists use thin metal welding for intricate designs. It allows for fine detail and creative expression while keeping pieces lightweight.
- Aerospace Components: Essential for assembling parts where low weight and precision are crucial. This application requires high skill and accuracy.
Other Options for Joining Thin Metal
There are alternatives to consider if you need to join thin metal without traditional welding. You might try adhesive bonding, such as Loctite Epoxy, which works great for thin materials and provides strong results. Brazing is another viable option, with products like Harris Safety-Silv, effective for high-strength joints and less heat risk. If you’re working with aluminum, consider using a rivet gun or self-tapping screws, which can deliver quick results without melting the metal. For those looking to work with thin steel, you might experiment with techniques like using a soldering iron and solder specifically formulated for metal. I’ve found these methods often beat the dilemma of how to bond metal to metal without welding.
Frequently Asked Questions (FAQs)
Now let us look at some common questions I typically get asked about welding thin metal.
What is the Best Welding Method for Thin Metal?
The best welding method for thin metal is usually MIG welding. MIG welding offers a fast process and produces clean welds with minimal distortion, ideal for thinner materials.
Can Metal Be Too Thin to Weld?
Yes, metal can be too thin to weld properly. If it’s too thin, you risk burning through or creating weak joints, and that can mess up the structural integrity.
What Welding Rod Do I Use for Thin Metal?
You should use a rod designed specifically for the type and thickness of metal you’re welding. Generally, a 1.6 mm (1/16 Inch) rod is recommended for thinner metals to avoid excess heat.
What Should I Set My MIG Welder to for Thin Metal?
If you’re welding thin metal, set your MIG welder to a low voltage, typically between 13–16 volts. This ensures a smooth arc and prevents burn-through.
How to Weld Thin Aluminum?
Welding thin aluminum requires precision and care. Using a low amp setting and keeping a short arc length helps avoid burn-through, and using argon as shielding gas provides better protection from contamination.
How to Weld Thin Stainless Steel?
You can weld thin stainless steel using TIG welding for the best results. This method provides a focused heat source, which reduces the risk of burn-through and gives you control over the weld puddle.
Conclusion
I’m glad we could cover this together. We discussed what thin metal is, types of thin metals and how weldability changes with each, necessary prerequisites, steps to weld thin metal, precautions, and types of welding best suited for thin materials. Additionally, we explored factors affecting welding, common problems and their solutions, aftercare, and advanced tips for a quality finish.
To summarize, learning how to weld thin metal comes down to understanding the right tools and techniques. Whether you’re tackling thin aluminum or stainless steel, keep the heat low, use a proper fit-up, and pay attention to your speed. Don’t hesitate to reach out if you need further assistance with any of your welding challenges.
For more information, be sure to explore What is Welding, where you’ll find a wealth of resources on welding techniques, tips, and best practices.
References
- ISO. (2017). ISO 3834: Quality Requirements for Fusion Welding of Metallic Materials. Geneva, Switzerland: ISO.
- Norrish, J. (2006). Advanced Welding Processes. Boca Raton, FL: CRC Press.
- American Welding Society. (2021). AWS SENSE: Guidelines for Entry-Level Welders. Miami, FL: AWS.
Joe Carter is a retired welding professional with over 40 years of hands-on experience in the industry, spanning ship repair, structural welding, and even underwater projects. Joe is a master of MIG, TIG, and Stick welding. Passionate about mentoring the next generation of welders, Joe now shares his decades of expertise and practical insights to help others build rewarding careers in welding.
American Welding Society, Metal Fabrication, MIG Welding, Thin Metal, TIG Welding, Welding, Welding Techniques, Welding Wire