How to Bond Metal to Metal Without Welding? Techniques, Types, and Tips
Bonding is joining two materials together using adhesives or other methods. Unlike welding, it doesn’t involve melting the metals.
If you thought about how to bond metal to metal without welding, you’re not alone. It’s crucial to know how to effectively bond metals, ensuring strong, durable results. In my experience, taking the right steps made all the difference for lasting welding fundamentals and constructions.
In this guide, I’ll cover types of bonding methods, prerequisites, steps to bond metal to metal without welding, precautions to take, and common issues. You’ll learn about factors that affect metal bonding, aftercare tips, advantages of various methods, and typical uses of bonding. This information will help anyone looking for solutions on how to bond metal without welding.
Contents
- How to Bond Metal to Metal Without Welding?
- What is Bonding?
- Types Of Bonding in Metal-to-metal Applications
- Prerequisites
- Steps to Bond Metal to Metal Without Welding
- Precautions
- Types Of Bonding Methods
- Factors Affecting Metal Bonding
- Common Issues
- Advanced Bonding Techniques Without Welding
- Advantages Of Metal Bonding Methods
- Typical Uses Of Bonding Metal
- Alternatives for Bonding Metal to Metal Without Welding
- Frequently Asked Questions (FAQs)
- Conclusion
- Additional Reading
How to Bond Metal to Metal Without Welding?
Bonding means joining materials together. So, how to bond metal to metal without welding? Use adhesives like epoxy (1-2 Hours Cure Time) or mechanical fasteners, like rivets. It’s easier than welding and great for repairs.
Nevertheless, for those who prefer a traditional approach to metal fabrication at home, finding the most suitable equipment is essential, especially when seeking the best welding machine.
What is Bonding?
Bonding is a process where two or more materials join at a molecular level. This occurs through adhesives, soldering, or mechanical fitting. For example, epoxy adhesives can withstand tensile strengths of 60-100 MPa (Megapascals) or 8700-14500 psi (Pounds Per Square Inch). It’s important to consider environmental factors; some bonds weaken at high temperatures, while others resist corrosion.
Let’s explore how to bond metal to metal without welding. You can use techniques like adhesives or mechanical joining methods. I’ve tackled several DIY projects using epoxy glue to bond metal pieces, and it worked like a charm!
For work, I bonded steel to steel without welding. I was amazed at how effective adhesives can be! Using a high-strength adhesive, I joined two steel plates effortlessly, creating a strong joint. Products like Loctite Epoxy Weld or other metal glues can make a significant difference. They can bond aluminum, steel, and more without the heat of welding.
Types Of Bonding in Metal-to-metal Applications
What are the types of bonding methods?
-
Adhesive Bonding
Adhesive bonding uses glue or adhesive to join metals. For a strong bond, use products like Loctite Epoxy Weld Bonding Compound. Clean the metal surfaces, apply the adhesive, and press them together for the recommended curing time (Often 24 Hours).
-
Mechanical Bonding
Mechanical bonding uses fasteners or clips to hold metals together. This can be done with screws, bolts, or rivets. To bond metal without welding, drill holes in both metals, align them, and secure with fasteners, ensuring they’re tight. For those interested in the technical aspects of welding, you might explore how to make a welding machine transformer.
-
Thermal Bonding
Thermal bonding involves using heat to join metals, not via welding. For example, to bond aluminum, heat both surfaces and apply an appropriate filler material. Heat the area until it’s bright, then introduce the filler to melt and flow into the gaps. Understanding the various costs associated with different welding methods can be crucial, especially when considering how much MIG welding gas costs.
-
Soldering
Soldering uses a low-melting-point alloy to join metals. Tin-lead solder works well. Clean the surfaces, heat them, and apply solder. Let it cool to form a solid connection.
-
Brazing
Brazing uses a filler metal with a higher melting point than soldering. It can bond steel, copper, and more. Clean the surfaces, heat them, and melt a brazing alloy. After cooling, you’ll have a strong bond. If you encounter issues with a welding machine, understanding how to address these effectively can be crucial, and you may find it helpful to explore how to fix a welding machine.
You should now have a good understanding of metal-to-metal bonding types, including their applications. In the next part, we’ll discuss prerequisites.

Prerequisites
What do you need to bond metal to metal without welding?
- Loctite Epoxy Weld Bonding Compound: You’ll need Loctite Epoxy Weld for its strong, steel-filled formula that creates a nearly indestructible bond.
- Sandpaper (80-grit): Grab some 80-grit sandpaper to roughen the metal surfaces for better adhesion.
- Isopropyl Alcohol: Use isopropyl alcohol, such as 91% solution, to clean the metal surfaces before applying the adhesive.
- Clamps: Use clamps, like C-clamps, to hold the pieces tightly together as the bond cures, reducing the risk of a weak joint.
We’ve wrapped up the prerequisites here. Next up, we’ll look at the steps to bond metal to metal without welding.
Steps to Bond Metal to Metal Without Welding
Here are the steps to bond metal to metal effectively without welding.
-
Prepare Metal Surfaces
Start by cleaning both metal surfaces thoroughly. Use a degreaser to remove oil and grime; 99% isopropyl alcohol works well. Ensure there’s no rust or oxidation, as it can weaken the bond. A clean, roughened surface provides a better grip for adhesives.
Use sandpaper or a wire brush to abrade the surfaces. Rough surfaces enhance adhesion. Aim for a surface roughness of about 0.5 to 1.0 micrometers for optimal bonding strength. The more thorough your preparation, the stronger your bond will be.
-
Select Suitable Bonding Method
Choose a bonding method based on the types of metals involved. For aluminum, use an epoxy adhesive like Loctite Epoxy Weld Bonding Compound, which is designed for metal. If joining dissimilar metals, consider a hybrid adhesive that combines epoxy and cyanoacrylate. This hybrid approach increases strength and compatibility.
For steel bonding, single-component adhesives work well. A polyurethane adhesive can flex and absorb shock better than standard epoxies. These materials handle pressure between 1,000 and 3,000 PSI (Pounds Per Square Inch) effectively.
-
Apply Bonding Agent
Apply the adhesive evenly on one surface using a spatula or brush. A thin layer works best to avoid excess product seeping out when pressing the two pieces together. Follow the manufacturer’s instructions for curing times and thickness.
Dive into application quickly, as open time can range from 5 to 30 minutes for many epoxy compounds. Temperature and humidity can significantly alter curing times. Ideally, apply in a controlled environment at about 20°C (68°F) and 40-60% humidity.
-
Clamp and Cure
After applying the adhesive, press the two metal pieces together firmly. Use clamps or heavy weights to ensure a consistent bond. Apply enough pressure to minimize gaps, ensuring full contact and preventing air pockets, which can weaken the bond.
Allow the bond to cure as per the instructions, typically 24 hours for full strength. If you’re in a hurry, some adhesives can achieve handling strength in as little as 30 minutes. Post-curing conditions like heat can enhance bond durability, but let it cure undisturbed initially.
We’ve wrapped up the methods for bonding metal without welding here. Next up, we’ll look at important precautions to take.
Precautions
Let’s cover essential precautions for bonding metal without welding.
- Ventilation: Work in a well-ventilated area to avoid inhaling toxic fumes, like those from epoxy. Open windows or work outdoors, as I do.
- Personal Protective Equipment (PPE): Always wear gloves and goggles to protect your skin and eyes from chemical burns and heat. I recommend 3M safety goggles for durability.
- Surface Preparation: Ensure metal surfaces are clean and free of oil to improve adhesion. A smooth, clean surface is vital.
- Follow Instructions: Read product guidelines before use. Each adhesive works differently; cure times may vary based on temperature and humidity.
Always take safety seriously for a smooth bonding experience!
We have now covered important precautions. Next, we will examine various types of bonding methods.
Types Of Bonding Methods
Let’s move on to the types of bonding methods. We’ll cover adhesive bonding, brazing, soldering, mechanical fastening, and heat treatment.
-
Adhesive Bonding
Adhesive bonding uses substances like glue or epoxy to join metal without welding. Strong adhesives can handle loads from 1379 to 2068 kPa (2000 to 3000 Psi), depending on the material. This method is ideal for smooth surfaces and can bond dissimilar metals, such as stainless steel to aluminum.
-
Brazing
Brazing joins metals by melting a filler metal above 450°C (842°F) that flows into the joint. It creates strong, durable joints, especially for high-temperature applications. I often use brass or silver solders for their effective bonding and versatility. Understanding techniques like peening in welding can further enhance the strength and durability of metal joints.
-
Soldering
Soldering is similar to brazing but uses lower temperatures (Below 450°C/842°F) and softer solders, like tin-lead or lead-free alternatives. It’s perfect for thin metals and electronics but isn’t as strong as brazing, making it ideal for heat-sensitive applications.
-
Mechanical Fastening
This method uses fasteners like bolts, screws, or rivets to hold metals together. It’s quick and allows for disassembly. Mechanical fastening can support loads, but joints may loosen over time if not secured properly.
-
Heat Treatment
Heat treatment changes the properties of metals to improve strength or ductility. Processes like annealing or hardening enhance the joint’s resilience. Over the years, I’ve learned that selecting the right heat treatment is crucial for achieving desired performance in final products.
Factors Affecting Metal Bonding
What factors affect how different metals stick together without welding?
-
Surface Preparation Quality
Cleaning surfaces is essential. Remove rust, paint, or grease—an unclean surface can reduce bond strength by up to 70%!
-
Bonding Material Selection
Choose the right adhesive for the metals you’re using. For instance, epoxy works well with aluminum, while urethane is effective for stainless steel.
-
Temperature Conditions
Temperature impacts bond strength. Most adhesives perform best between 10°C (50°F) and 30°C (86°F). Extreme cold or heat can weaken the bond.
-
Gap Fillers and Spacing
Use appropriate fillers to close gaps and maintain a strong bond. Ideally, keep gaps under 0.25 mm for proper adhesive penetration.
-
Environmental Factors
Humidity and chemical exposure can weaken bonds over time. Regular checks ensure durability, especially in harsh environments.
Common Issues
Let’s look at some specific problems related to bonding.
-
Poor Surface Adhesion
Poor surface adhesion results in weak bonds. Check for contaminants like dirt or oil. To fix this, clean the surfaces with a solvent and roughen them for better grip.
-
Inadequate Curing Time
Inadequate curing time can lead to bonding failure. Always follow manufacturer instructions. Allow the recommended time for full strength before applying stress.
-
Incorrect Material Compatibility
Using incompatible materials can cause reactions. Check compatibility charts. If they’re mismatched, switch to suitable adhesives or bonding materials.
-
Temperature Fluctuations
Temperature fluctuations affect bonding effectiveness. Aim for stable conditions between 20°C-30°C (68°F-86°F). If temperatures drop, consider heating the workspace or using heat-resistant adhesives.
-
Moisture and Contamination
Moisture can ruin bonding processes. Always ensure surfaces are dry. If moisture is present, use a heat gun to evaporate it before applying bonding material.
Advanced Bonding Techniques Without Welding
Besides basic methods, advanced techniques can enhance your metal bonding experience.
Surface Treatment for Enhanced Bond Strength
Consider these treatments to improve adhesion:
- Plasma Treatment: This technique cleans and modifies surfaces at a molecular level, boosting bonding strength.
- Sandblasting: Abrading the surface can increase the surface area, leading to improved adhesion.
- Coating Removal: Always strip off coatings like paint to ensure a clean bond; even a 0.1 mm layer can reduce bond strength significantly.
Comparative Strength Table of Bonding Methods
Bonding Method | Typical Strength (psi) | Benefits | Limitations |
---|---|---|---|
Epoxy Adhesives | 3000-4000(20.7-27.6 MPa) | High durability, waterproof | Long curing time |
Soldering | 600-800(4.1-5.5 MPa) | Low-cost, quick process | Less strength than other methods |
Brazing | 18000-25000(124.1-172.4 MPa) | Strong for similar/dissimilar metals | Requires heat management |
Mechanical Fastening | 1000-3000(6.9-20.7 MPa) | Reassemble easily, no curing needed | Possible loosening over time |
Use of Accelerators and Primers
Accelerators and primers can speed up curing and enhance bonding. Here are some options:
- Bonding Primers: Help improve adhesion on difficult surfaces.
- Accelerators: Reduce curing time from 24 hours to as little as 5 minutes!
Advantages Of Metal Bonding Methods
The main benefit of bonding metal to metal without welding is that it’s easier and quicker. In my work, it helped me complete projects that needed faster turnarounds without compromising strength.
Moreover, bonding techniques reduce distortion, lower heat input, and often require less equipment. It’s also effective for joining dissimilar metals, minimizing cleanup, and producing clean, smooth surfaces.
Typical Uses Of Bonding Metal
Bonding metal is used for structural repairs and has many applications, including:
- Aerospace Components: Specialized adhesives bond metals like aluminum and titanium due to their lightweight and strength. They’re popular for reducing weight and improving fuel efficiency.
- Automotive Repairs: Use epoxy to bond metal parts in car frames and body panels. It saves time and weight, which is crucial for performance.
- Electronics Assembly: Conductive adhesives bond metal contacts on circuit boards, especially in waterproof designs. This method is gaining popularity for its durability and precision.
- Fabricated Stairs and Railings: Metal bonding agents join steel parts without welding. They’re popular for quicker assembly and clean finishes, avoiding the heat distortion that welding can cause.
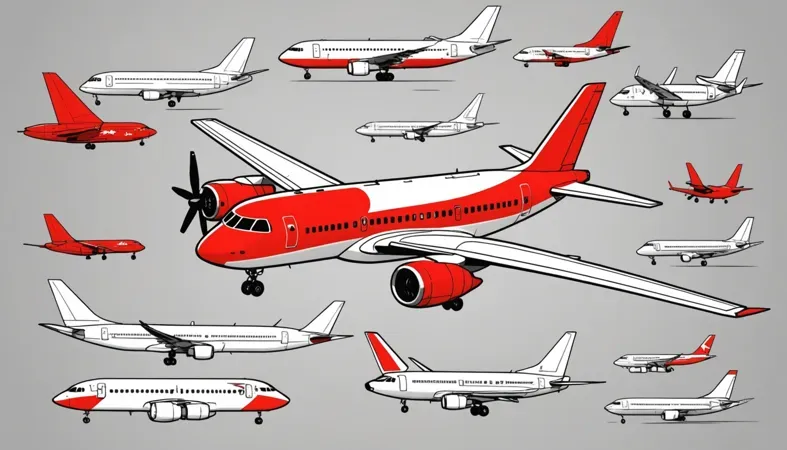
Alternatives for Bonding Metal to Metal Without Welding
There are several effective options to achieve strong bonds without welding. Consider using products like Loctite Epoxy Weld Bonding Compound, which creates a durable bond on various metals. Through years of practice, I’ve come to understand that some methods, like using epoxy, are preferred in situations where heat-sensitive components are nearby or when you need a quick fix. However, in situations where a more permanent and reliable joint is required, understanding techniques like a socket weld connection can be crucial.
Another alternative is specialty adhesives designed for specific metals. For example, if you’re working with aluminum, you might try epoxy glue specifically for aluminum bonding. These options provide reliable results and are handy in DIY projects. You see, not every job needs a welding torch!
Frequently Asked Questions (FAQs)
Now let us look at some common queries. I typically get asked about bonding methods, alternatives to welding, and related techniques.
What is the Best Way to Bond Metal to Metal?
Yes, the best way to bond metal to metal often involves using epoxy or adhesive systems designed for metals. These adhesives can create strong bonds that resist shock and tension. For instance, certain epoxies can achieve strengths up to 4,000 psi (27.6 Mpa), making them reliable alternatives to welding.
However, in cases where a more permanent and metal-to-metal solution is necessary, understanding how to weld sheet metal can be crucial.
How to Join Two Metal Pipes Without Welding?
You can join two metal pipes without welding by using coupling fittings or adhesive bonding techniques. Couplings, commonly made from PVC or metal, provide a mechanical connection while adhesive methods, like two-part epoxies, can seal joints permanently. This approach can simplify repairs and installations. For those curious about the energy efficiency of traditional welding tools, it’s useful to explore how many watts a welder uses.
What is the Best Glue Instead Of Welding?
The best glue instead of welding is often a high-performance epoxy. These adhesives offer excellent strength and resistance to various factors like temperature and moisture. Some glues can handle extreme conditions, making them fit for demanding applications, often up to 500°F (260°C).
How Do You Reconnect Metal to Metal?
You can reconnect metal to metal using adhesives or mechanical fasteners like screws and clamps. Adhesives create a seamless bond, while screws provide a controllable connection. Depending on your requirements, choose what fits best—for quick fixes, adhesives tend to work wonders!
How to Bond Aluminum to Aluminum Without Welding?
You can bond aluminum to aluminum without welding by using specialized adhesives or mechanical methods. For instance, some adhesives are formulated to chemically react with aluminum, ensuring a strong bond. This method is crucial for applications where welding might not be suitable, like thin sheet metal.
Conclusion
We covered how to bond metal to metal without welding, exploring various types of bonding, crucial prerequisites, and important methods. We looked at practical tips for aftercare, common issues, and key factors affecting bonding success. Lastly, I shared advantages and typical uses, alongside alternatives if needed.
Hopefully, I was able to impart some of my experience on how to bond metal to metal without welding using techniques like adhesives, mechanical fastening, and soldering. By following clear steps and considering essential precautions, you can securely bond materials like aluminum and steel without the heat of welding. So, remember the tips and methods discussed to achieve strong and lasting bonds!
If you’re seeking additional insights, What is Welding provides extensive information on related topics.
Additional Reading
- Howard B. Cary. (1997). Welding Manual. Upper Saddle River, NJ: Prentice Hall.
- American Welding Society. (2015). AWS D1.1/D1.1M: Structural Welding Code – Steel. Miami, FL: AWS.
Tyler is a passionate DIY welder and self-taught metal artist with years of hands-on experience transforming raw materials into functional and artistic creations. Specializing in MIG welding, Tyler crafts everything from custom furniture to outdoor sculptures, blending creativity with technical skill. Committed to making welding accessible, Tyler shares practical insights and project inspiration to help beginners and hobbyists confidently explore the world of metalworking.
Adhesive Bonding, Adhesive Techniques, American Welding Society, Brazing, DIY Projects, Mechanical Fastening, Metal Bonding, MIG Welding, Personal Protective Equipment, Soldering, Welding