What is a Socket Weld? Understand Socket Welding, Applications, and Techniques
Published on: November 16, 2024 | Last modified: March 4, 2025
By: Joe Carter
A socket weld is a type of pipe joint used in piping systems. It’s done by inserting a pipe into a socket of a fitting and then welding the two parts together.
One question I was asked a lot is: what is a socket weld? It’s important because using the right welding technique ensures strong, leak-free joints. To truly understand the nuances of various methods, from my own experience, when the weld is done correctly, the system operates reliably, preventing costly downtime. This highlights the importance of mastering welding fundamentals in any project.
In this guide, I’ll cover several key aspects: how socket welding works, types of socket welds, steps for performing socket welding, factors that influence socket welds, how to troubleshoot common issues, aftercare and inspection tips, industry applications, and alternatives to socket welding. You’ll also find useful details on how to weld socket weld fittings and what is a socket weld flange.

Contents
- What is a Socket Weld?
- How Does a Socket Weld Work?
- Types Of Socket Welds
- Steps for Performing Socket Welding
- Factors Influencing Socket Welds
- How to Address Common Problems
- Aftercare, Inspection, and Advanced Tips for Socket Welds
- Industry Applications for Socket Welds
- Are There Any Alternatives to Socket Welding?
- Socket Weld Standards and Regulations
- Frequently Asked Questions (FAQs)
- Wrapping Up
- References
What is a Socket Weld?
A socket weld is a type of welding used to join pipes and fittings. It involves inserting a pipe into a recessed area of a fitting, then welding around the joint. Typically used in high-pressure applications, it provides a strong, reliable connection. While working with welding equipment, it’s helpful to know about possible modifications, such as how a 220 welder can be converted to 110.
How Does a Socket Weld Work?
A socket weld is a joint used to connect two pipes or fittings. It’s created by inserting one pipe into another, forming a socket. The weld occurs around the outside of the socket, melting the filler material and fusing the surfaces together. Typically, socket welds are used in smaller diameter piping systems, usually 2 inches (51 Mm) or smaller, under high-pressure conditions.
These welds are ideal for systems requiring strong, leak-proof connections. They’re especially useful in industries like oil and gas, where pressure ratings can reach up to 2500 psi (17237 Kpa). The process involves proper alignment and controlled heat to ensure a solid bond.
I once handled a maintenance job replacing socket weld fittings in a pipeline. It was fascinating to see how a well-executed socket weld ensures structural integrity under pressure. Understanding how to socket weld requires skill, precision, and careful attention to detail to prevent failures during operation.
Types Of Socket Welds
What are the types of socket welds?
-
High-pressure Socket Welds
High-pressure socket welds are for pipes handling high internal pressure. They create strong joints to prevent leaks and failures. To make these, heat the joint area before inserting the pipe into the fitting, then apply heat and pressure to fuse them together. Using socket welds in high-pressure applications requires understanding the power requirements of welder machines.
-
Low-pressure Socket Welds
Low-pressure socket welds are used for applications like water lines. They provide adequate strength without the complexity of high-pressure setups. To create these, align the matching joints and apply heat around the edges to ensure a solid bond. When selecting welding rods for socket welds it is essential to compare specifications like those between 6010 and 6011 welding rod.
-
Pipe Socket Welds
Pipe socket welds connect pipes smoothly, making them ideal for industrial settings. They reduce turbulence and pressure drops. To perform a pipe socket weld, insert the pipe into the fitting and apply heat evenly around the connection until they fuse into one unit.
-
Tube Socket Welds
Tube socket welds are used in HVAC systems and food processing. They maintain clean connections critical for hygiene. To achieve this, ensure the tube fits snugly in the socket, then heat the joint evenly for a neat, effective fusion.
Selecting the appropriate power source for your welding equipment is crucial. Knowing what size generator to run a 140 amp welder ensures optimal performance and efficiency.
-
Flange Socket Welds
Flange socket welds allow easy disassembly of pipelines or assemblies. They’re used in applications requiring routine maintenance. To create one, fit the flange to the pipe end and apply heat evenly at the junction for a strong yet removable connection.
You should now have a good understanding of the various types of socket welds. In the next part, we’ll discuss the steps for performing socket welding.
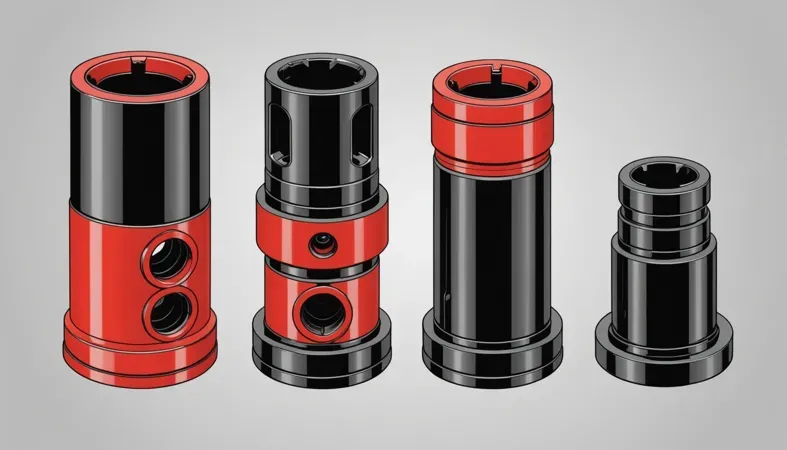
Steps for Performing Socket Welding
Now, we’ll cover the steps to perform a socket weld effectively.
-
Prepare the Pipe Ends
Start by cleaning the pipe ends thoroughly. Use a wire brush or grinder to remove rust, dirt, or oil—it’s crucial for a strong weld. Ensure the inside diameter (ID) matches the socket fitting. Pipe sizes vary, but a common size is 1 inch (2.54 Cm) nominal.
Align the pipe with the fitting properly to maintain a tight fit. Improper alignment can create weak spots in the weld. Spend extra time here; alignment sets the stage for success.
-
Insert Pipe Into the Fitting
Carefully slide the prepared pipe into the socket of the fitting. Leave about 1/8 inch (0.32 Cm) of gap between the end of the pipe and the bottom of the socket to provide space for the molten weld. Keep verifying alignment as you go; any shift can disrupt your project.
Once positioned, hold it steady. If you’re using a metallic fitting, check for thermal expansion, especially in larger diameters—this affects function and integrity.
-
Weld the Joint
Heat your welding torch to between 400°F and 1,000°F (204°C and 538°C). Make several passes around the joint, creating consistent, even beads. Choose a filler rod if specified; a thin rod is typically best. Using the right welding guidance ensures that a rod matching the base metal leads to a smoother finish.
Weld using a circular motion to ensure the molten metal flows evenly. Experiment with speed; too fast can create voids, and too slow may cause excessive buildup. Aim for a weld that smoothly integrates with your base metal. When setting up a home workshop, consider the best welding machine for home use to enhance your projects.
-
Let the Weld Cool
After completing the weld, allow it to cool naturally. Rapid cooling can cause cracks due to thermal shock, especially with larger fittings. Ideally, wait 15-30 minutes for small to medium joints. Remember: patience pays off here. To further enhance your understanding of diverse techniques, consider exploring the different types of welding.
Watch for changes in color or texture as it cools; a uniform finish indicates a solid joint. If any warping occurs, it’s often due to uneven cooling, so ensure heat circulates evenly.
So far we covered steps for executing socket welding. Next, let’s look at the factors that impact socket welds.
Factors Influencing Socket Welds
What factors affect socket welding performance and reliability?
-
Material Composition
The material type influences socket weld properties. Stainless steel (SS) often resists corrosion better than carbon steel (CS), resulting in a more durable weld.
-
Joint Design
The joint design affects stress distribution during and after welding. A well-designed joint can handle higher pressures, which is crucial in piping systems.
-
Weld Size
Adequate weld size maximizes strength. Ensure the weld effectively covers the gap, aiming for a minimum size of 3 mm (0.12 In) to create a robust connection.
-
Heat Input
Excessive heat can warp materials, leading to cracks. Control the heat input between 60 and 80 J/mm to avoid these issues.
-
Cooling Rates
Fast cooling can result in brittle welds, while slow cooling reduces residual stress. Aim for a cooling rate of around 50°C/min for optimal results.
You should now have a good understanding of elements affecting socket welds. In the next part, we’ll discuss solutions to frequent issues.
How to Address Common Problems
Let’s look at some specific issues with socket welds.
-
Cracking in the Welds
Socket welds can crack due to rapid cooling. Look for visible cracks or misalignment. Maintain proper heat settings and slow the cooling process with torches.
-
Inconsistent Weld Quality
Socket welds may vary in quality, showing rough surfaces or weak points. Use correct techniques: maintain a smooth travel speed and clean the surfaces before welding.
-
Excessive Porosity
Socket weld defects include excessive porosity caused by contaminants. Check for pinholes or bubbles in the weld. Clean all connections thoroughly and verify gas flow settings.
-
Alignment Issues
Socket welds can suffer from misalignment. Hold the pieces firmly together; otherwise, you’ll have uneven joints. Use clamps and fixtures to keep everything aligned during welding.
-
Incomplete Fusion
With socket welds, you may find areas where the welds didn’t fuse completely, which can weaken joints. Visually check for gaps and adjust the heat. You might need to re-weld or add more filler material.
We have now covered solutions for common issues. Next, we will examine aftercare, inspections, and advanced tips for socket welds.
Aftercare, Inspection, and Advanced Tips for Socket Welds
Here are essential aftercare, inspection, and expert tips for socket welds to ensure longevity and reliability.
Aftercare Tips
After welding socket joints, cool them slowly to avoid cracks. Keep the weld area free from dirt and moisture, ideally below 20% humidity. Apply a suitable anti-corrosion spray, like Rust-Oleum, for added protection; this shields the weld from harsh environments, keeping it strong.
Inspection Procedures
Inspect socket welds with a black light to identify cracks. Areas should be smooth; rough spots may indicate faulty penetration. Use an ultrasonic thickness gauge for integrity checks up to 0.1 mm. I recommend GE Inspection Technologies tools for accurate readings during spot checks.
Advanced Tips
Monitor heat input closely when welding—aim for 6 to 12 Joules/mm to prevent warping. Use the right filler material; ER309L is ideal for stainless steels. If working in high-stress environments, consider post-weld heat treatment at 700°F (371°C) to enhance strength and significantly reduce stress. When precision and complete penetration are necessary, it is essential to understand what a CJP weld entails.
Industry Applications for Socket Welds
I’ve seen people use socket welds for pipe fittings in various industries. They have many applications, including:
- High-Pressure Systems: In oil and gas pipelines, socket welds create strong joints that can handle pressures up to 10,000 psi (68.9 Mpa). They’re favored for their leak-tight features.
- Power Generation: Socket welds are vital in boiler systems. They connect valves and fittings, ensuring a secure fit at extreme temperatures.
- Chemical Processing: In this field, socket welds resist corrosion. They’re commonly used to connect stainless steel pipes in chemical reactors.
- Water Treatment Plants: Socket-welded joints are utilized in high-floor piping systems. They ensure durability and prevent leaks, keeping maintenance costs low.
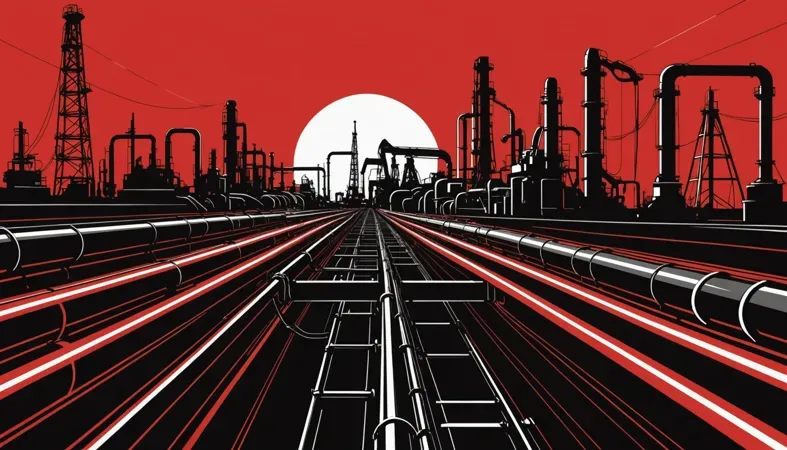
Understanding socket welds is crucial for ensuring strong, leak-free connections in piping.
Are There Any Alternatives to Socket Welding?
There are several methods to achieve similar results to socket welding. Options like butt welding and threaded joints are often considered based on the project specs. Over time, I’ve observed that butt welding, such as with ASTM A234 fittings, offers a smoother finish and is sometimes easier in tight spaces.
Another alternative is using socket weld flanges. By employing flanges, you gain flexibility in assembly and disassembly, which can be crucial for maintenance. While socket welding provides a solid connection, using flanged connections can be practical in certain conditions.
Socket Weld Standards and Regulations
Understanding the standards and regulations around socket welding is crucial for compliance and quality assurance.
Standard/Regulation | Description | Application Area |
---|---|---|
ASME B16.11 | Covers socket-weld fittings and the requirements for their dimensions, tolerances, and material. | General piping systems |
API 5L | Specifies requirements for piping in the oil and gas industry. | Pipeline construction |
ASTM A234 | Details the requirements for pipe fittings of wrought carbon steel and alloy steel. | Structural applications |
MSS SP-45 | Standard that includes requirements for the design and fabrication of socket-weld fittings. | Plant piping systems |
ISO 14122 | Safety standards for permanent means of access to machinery, including piping systems. | Safety in industrial settings |
Compliance with these standards ensures safety, integrity, and reliability in socket welding projects. Understanding these can set you apart as a knowledgeable welder.
Frequently Asked Questions (FAQs)
We have covered some key points. Here are some unique questions I typically get asked.
What is the Difference Between Socket Weld and Butt Weld?
The difference between socket weld and butt weld lies in their design and application. Socket welds join pipes through a socket fitting, making them compact and ideal for high-pressure systems. Butt welds require aligning and welding the pipe ends, providing a stronger joint suitable for heavy-duty applications. Argon plays a crucial role in metalwork processes, serving as a shielding gas to protect welds from contamination, and you can explore more about argon in welding applications.
What is the Difference Between Socket Weld and Fillet Weld?
The difference between socket weld and fillet weld concerns their connections. A socket weld involves welding around the circumference of a pipe fitting inside a socket, while a fillet weld forms a right angle joint between two surfaces. Socket welds are common in high-pressure contexts, while fillet welds are versatile across various applications. When setting up your welding equipment, it is crucial to know the right gauge wire to ensure efficient and safe operations.
What is the Difference Between Socket Weld and Flange?
The difference between socket weld and flange relates to their connection types. Socket welds are typically used in permanent connections with fittings, while flanges provide removable joints, allowing for easier access and maintenance. Socket weld fittings suit high-pressure systems, while flanges are essential in ensuring flexibility.
What Schedule is Socket Weld?
Socket welds typically use schedules 40 and 80 for fittings. Schedule refers to the wall thickness of pipes; thicker walls provide better strength and pressure ratings. A socket weld fitting made to schedule 40 has a nominal pressure rating of around 300 pounds per square inch (Psi) at room temperature.
How to Weld Socket Weld Fittings?
Welding socket weld fittings involves several steps. First, clean the surface to ensure a proper bond. Then, align the fitting, insert the pipe, and tack weld in place. Finally, complete the weld around the joint perimeter. Ensure you use the correct electrode and settings for the material for maximum strength.
How to Socket Weld?
Socket welding involves inserting a pipe into a fitting and welding around the joint. Preparation includes cleaning excess material. Selecting the right welding technique is crucial for durability. Commonly, you would use a TIG or MIG welding process, depending on the materials being joined for effective results.
Wrapping Up
Phew, we covered a lot. We talked about what a socket weld is, how it works, different types of socket welds, and the steps for performing socket welding. We also looked at factors influencing socket welds, addressed common problems, discussed aftercare and inspection, and explored industry applications and alternatives.
So, what is a socket weld again? In simple terms, it’s a type of welding used mainly for joining pipes and fittings. We learned about socket weld flanges, the basic steps to how to socket weld, and even touched on inspection methods to ensure quality. This information not only helps you understand socket welding better but also prepares you for practical applications in various industries.
If you’d like to deepen your understanding of other welding techniques, we invite you to explore more at What is Welding.
References
- Lincoln Electric. (2020). The Procedure Handbook of Arc Welding (15th ed.). Cleveland, OH: Lincoln Electric Company.
Joe Carter is a retired welding professional with over 40 years of hands-on experience in the industry, spanning ship repair, structural welding, and even underwater projects. Joe is a master of MIG, TIG, and Stick welding. Passionate about mentoring the next generation of welders, Joe now shares his decades of expertise and practical insights to help others build rewarding careers in welding.
High-pressure Applications, Industrial Applications, MIG Welding, Pipe Joining, Socket Weld, Welding, Welding Applications, Welding Equipment, Welding Fundamentals, Welding Techniques