Can You Weld Galvanized Steel? Understanding Weldability, Safety, and Techniques
Published on: November 23, 2024 | Last modified: March 4, 2025
By: Joe Carter
Galvanized steel is steel coated with a layer of zinc to prevent rusting. This coating makes it durable and perfect for outdoor use.
A common question I hear is, can you weld galvanized steel? It’s crucial to discuss this because welding can affect the zinc layer and the metal’s strength. In my experience, not every welding method works well for galvanized steel, so it’s important to choose wisely to avoid issues later on.
In this guide, I’ll cover what galvanized steel is, different types of galvanized steel and their weldability, essential prerequisites, steps for welding, safety precautions, and factors that affect weldability. You’ll also learn about aftercare, inspection tips, and key benefits of welding galvanized steel. You might wonder, can you mig weld galvanized steel? We’ll address that and explore alternatives to welding galvanized steel.
Contents
- Can You Weld Galvanized Steel?
- What is Galvanized Steel?
- Types Of Galvanized Steel and Their Weldability
- Essential Prerequisites to Get Started
- Steps for Welding Galvanized Steel
- Precautions
- Types Of Welding for Galvanized Steel
- Factors Affecting Galvanized Steel Weldability
- Unique Issues Related to Welding Galvanized Steel
- Important Considerations When Welding Galvanized Steel
- Aftercare, Inspection, and Advanced Tips for Welding Galvanized Steel
- Key Benefits Of Welding Galvanized Steel
- Where is Galvanized Steel Used?
- Are There Any Alternatives to Welding Galvanized Steel?
- Frequently Asked Questions (FAQs)
- Conclusion
- References
Can You Weld Galvanized Steel?
Yes, you can weld galvanized steel. It can be tricky due to zinc fumes; they’re toxic. Always use a ventilated area and proper gear. For best results, remove the galvanized coating from the weld area first.
What is Galvanized Steel?
Galvanized steel is a type of steel coated with a layer of zinc. This process, called galvanization, protects the steel from corrosion (Rust). The zinc coating typically ranges from 30 to 100 micrometers (Μm) thick, or about 0.0012 to 0.004 inches. Generally, galvanized steel is used in outdoor construction because it extends the material’s life and reduces maintenance costs by up to 50%.
I’ve worked with galvanized steel on many projects. When you see it, you might wonder, “Can you weld galvanized steel?” It’s a common question. Honestly, it can feel tricky because the welding process affects the zinc coating.
I found it very helpful when I used galvanized steel in a recent fence project. The durability was impressive, but I was careful to understand the risks of welding galvanized steel. The fumes released during welding can be harmful, so always ensure proper ventilation. Knowing how to address the question—can galvanized steel be welded—can make a real difference.
Types Of Galvanized Steel and Their Weldability
What are the types of galvanized steel and how do they perform during welding?
-
Hot-dip Galvanized Steel
Hot-dip galvanized steel has a thick zinc coating for protection. You can weld this type of steel. To prevent spattering and ensure a strong weld, clean the surface and use suitable flux-core wire for better results.
-
Electro-galvanized Steel
Electro-galvanized steel uses electricity to apply a thinner zinc coating. You can weld it, but do so carefully. To achieve a clean weld on this type of material, set lower heat settings and clean the surface to remove excess zinc before welding. Understanding the different methods can enhance your skills, particularly when it comes to welding by metals.
-
Mechanical Galvanized Steel
This type receives its zinc coating through a mechanical process, making it durable. You can weld it effectively. Ensure to grind or wire brush the weld area to improve adhesion and ensure a solid bond.
-
Galvannealed Steel
Galvannealed steel combines hot dipping and heating for a smooth finish. You can weld it easily. Use low heat settings and keep the weld area free from contaminants to ensure quality.
-
Pre-galvanized Steel
Pre-galvanized steel is coated before fabrication, making it ready for use. You can weld it, but be cautious. Remove the coating in the weld area with a grinder for stronger weld penetration and optimal results. Welding upside down presents unique challenges but can be mastered with proper technique and practice. Find more details on how to weld upside down.
We’ve wrapped up the various types of galvanized steel and their weldability. Next up, we’ll look at key prerequisites to get started.
Essential Prerequisites to Get Started
What do you need to weld galvanized steel?
- Welding Machine: You need a reliable machine, such as the Miller Multimatic 215. It’s essential for providing the right amperage and power to weld galvanized steel effectively.
- Flux-Cored Wire: Use quality wire, like Lincoln NR-211-MP. It’s crucial for achieving a solid, clean weld on galvanized surfaces.
- Galvanized Steel Cleaner: Get solvents, such as Rust-Oleum 215164. Cleaning is vital for removing the zinc coating and ensuring a strong bond.
- Welding Rods: Use E6011 or E6013 rods. These help penetrate zinc residue effectively during the welding process.
We have now covered the essential prerequisites to get started. Next, we will examine the steps for welding galvanized steel.
Steps for Welding Galvanized Steel
Here are the steps for successfully welding galvanized steel. Follow them closely for the best results.
-
Prepare the Work Area
First, clear your work area of debris and clutter. A clean space helps you stay focused and reduces exposure to welding fumes. Ensure proper ventilation; a well-ventilated area lowers health risks from these fumes. Check that your electrical outlets can handle the welding machine’s power needs, typically around 220V (Or 110V for Small Machines).
-
Gather Necessary Equipment
Choose the right welding technique. MIG welding is effective but can leave zinc in the weld area, causing porosity. Alternatively, flux-cored welding often offers better penetration for thicker galvanized steel. Ensure your rig can manage sufficient amperage—around 190A is a good starting point for general mild steel thickness.
-
Clean the Surface Of the Steel
Remove the galvanization where the weld will occur. Use a flap disc, grinder, or chemical cleaner to strip the zinc coating. A grinder usually leaves a cleaner surface than chemicals. Don’t skip this step; welding through the coating can produce harmful fumes and weaken the weld. Aim for a surface profile of 0.01 inches (0.25 Mm) for better adhesion.
-
Set Up the Welding Machine
Properly configuring your welding machine is crucial. Depending on thickness, set the amperage between 125A and 175A for MIG. Adjust the wire speed accordingly; a general rule of thumb is about 200 inches per minute (5 M/min). Double-check polarity settings; for MIG welding of galvanized steel, reverse polarity usually works best.
-
Wear Appropriate Safety Gear
Never weld without proper personal protective equipment (PPE). Invest in a quality welding helmet with the appropriate shade— ideally, shade 10-12 for MIG welding. Don’t forget gloves and flame-resistant clothing to protect against spatters. Safety gear may seem like a hassle, but it’s worth it for your health.
You should now have a good understanding of welding techniques for galvanized steel and important steps involved. In the next part, we’ll discuss safety precautions.
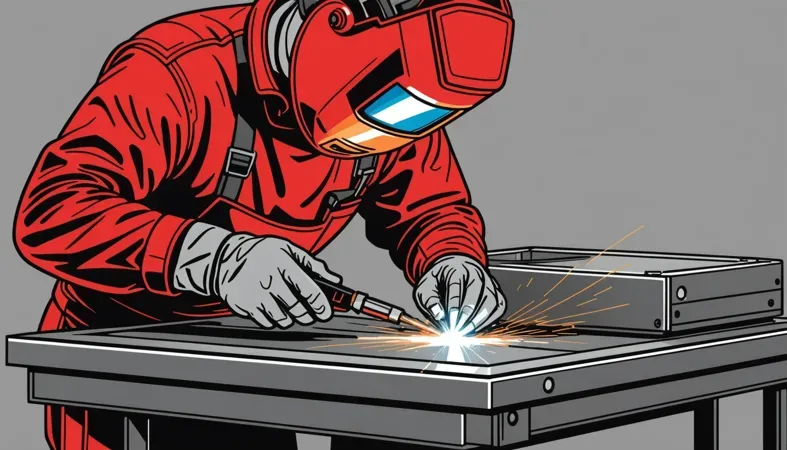
Precautions
Let’s quickly cover vital safety measures for welding galvanized steel.
- Ventilation: Good airflow clears toxic fumes. Use a fan, like the Tornado 2, to enhance fresh airflow.
- Respiratory Protection: Protect your lungs from zinc fumes. An N95 respirator is crucial for safety.
- Fire Safety: Sparks can cause fires. Keep an ABC-rated fire extinguisher nearby at all times.
- Surface Preparation: Clean surfaces to minimize risks. Use a wire brush or grinder for better weld contact.
Always prioritize safety when welding—we only get one chance to stay safe!
That covers safety measures and guidelines. Let’s now take a look at the different types of welding for galvanized steel.
Types Of Welding for Galvanized Steel
Let’s explore the types of welding suitable for galvanized steel: MIG welding, TIG welding, Stick welding, Flux-Cored Arc welding, and Spot welding.
-
MIG Welding
MIG welding, or Gas Metal Arc Welding (GMAW), uses a continuous wire electrode and shielding gas. It’s effective for welding galvanized steel since it minimizes heat input, reducing the risk of damaging the zinc coating. Typically, set the voltage between 18 and 25 volts for optimal results.
-
TIG Welding
TIG welding, or Tungsten Inert Gas Welding (GTAW), allows for precise, clean welds. It works well on thin galvanized steel but requires skill. Use around 15 to 20 amps, and monitor the heat; excess can vaporize the protective zinc layer.
-
Stick Welding
Stick welding, or Shielded Metal Arc Welding (SMAW), can be challenging with galvanized steel due to the release of zinc fumes. These fumes can create defects like porosity. If you choose Stick welding, a suitable electrode like E6013 at about 70 to 90 amps may be effective. When welding galvanized steel, it’s crucial to consider the potential health risks associated with exposure to zinc fumes, which is further explored in the article on hazards of zinc fumes.
-
Flux-cored Arc Welding
Flux-Cored Arc Welding (FCAW) is similar to MIG, providing good penetration and speed. However, ensure proper shielding to reduce zinc fumes. Aim for a voltage of 18 to 20 for a well-controlled bead. Operating welding equipment without proper safety gear can cause serious harm; consider the dangers of welding mask omission.
-
Spot Welding
Spot welding is excellent for joining sheet metal pieces without full penetration. It’s fast and efficient, mainly used in automotive applications with galvanized steel. The strength depends on the electrode width and heat settings.
Factors Affecting Galvanized Steel Weldability
What factors should you consider for welding galvanized steel?
-
Thickness Of the Galvanized Coating
The coating’s thickness impacts weld quality and strength. Thicker layers can lead to poor weld penetration, affecting heat distribution and causing weak joints.
-
Welding Method Used
MIG welding works well, while stick welding can cause issues. Each method has its own heat input, which affects your ability to melt through the zinc layer.
-
Heat Input
Too much heat can vaporize zinc, creating harmful fumes. Keeping heat levels controlled—around 250°C to 320°C (482°F to 608°F)—results in better welds and safer conditions.
-
Type Of Filler Material
Using the right filler material is crucial. Aluminum-based rods can react negatively with zinc, leading to dull or weak welds. Choose materials designed for galvanized applications.
-
Environmental Conditions
Humidity and wind can affect your welding process. High moisture may cause corrosion, while wind can chill the weld area, altering the results and efficiency of the operation.
Unique Issues Related to Welding Galvanized Steel
Let’s look at issues that arise when working with galvanized steel.
-
Fume Generation
Welding galvanized steel produces harsh fumes from zinc. Use proper ventilation and a respirator to reduce inhalation risks.
-
Loss Of Zinc Coating Integrity
Welding melts the zinc coating, which can lead to corrosion. Inspect the welded area and reapply zinc with cold spray or paint.
-
Porosity in Welds
Welds on galvanized steel often have porosity, meaning holes in the bead. Use electric arc positions to control gas input and reduce contamination.
-
Incompatibility With Certain Filler Metals
Using the wrong filler metal on galvanized steel can create weak joints. For best results, select filler metals compatible with zinc.
-
Cracking Risks
Welding galvanized steel poses a risk of cracking. Preheat the material to 150°F (65°C) to minimize stresses during welding.
Important Considerations When Welding Galvanized Steel
Before you start welding, it’s crucial to understand some key aspects that affect the process.
Weld Pool Properties
- Liquid Slag Formation: When welding galvanized steel, liquid slag can form above the weld pool. This can hinder the quality of the weld bead. You can mitigate this by selecting the right welding parameters and techniques.
- Puddle Control: Maintaining control over the weld puddle is vital. Too much heat can lead to a wider puddle and unexpected weld defects. Aim for a narrow, controlled puddle for better results.
Technical Specifications for Effective Welding
Here are some critical technical specifications to ensure a successful weld:
Aspect | Recommended Settings | Explanation |
---|---|---|
Voltage for MIG Welding | 18-22 volts | This range allows optimal penetration without burning the zinc too much. |
Wire Speed | 200 inches/min (5 M/min) | Adjust this based on thickness and welding speed for smooth operation. |
Travel Speed | 100 mm/min (3.94 inches/min) | Slower speeds allow better heat control and penetration. |
Preheat Temperature | 65°C (150°F) | This minimizes the risk of cracking, especially in thicker materials. |
Aftercare, Inspection, and Advanced Tips for Welding Galvanized Steel
Here’s essential guidance for maintaining quality after welding galvanized steel.
Aftercare Tips
After welding galvanized steel, clean the joint area promptly with a wire brush and some TSP (Trisodium Phosphate). It’ll help remove zinc oxide residues. Apply a zinc-rich primer like Rust-Oleum® Cold Galvanizing Compound (Spray Application)—it provides excellent corrosion protection while keeping your weld intact.
Inspection
Inspect welded joints for proper penetration, ensuring at least 2–3 mm (0.08–0.12 inches) of fusion on both sides. Use a 30x magnifying glass to check for cracks or insufficient zinc coverage. I recommend using a flap disc from Dewalt® for clear visibility and easy cleanup after welding. For precise joint alignment in projects, learn how to weld 45 degree angles.
Expert Tips
Ensure you’re using an argon-rich gas mixture while welding (60% Argon, 40% CO₂ Works Great). Maintain a travel speed under 100 mm/min (3.94 Inches/min) to prevent excessive heat input, which can alter the protective coating. Add a dedicated cooling period between passes—30 seconds to 1 minute—this prevents degradation of the coating’s properties.
Key Benefits Of Welding Galvanized Steel
The main benefit of welding galvanized steel is its corrosion resistance. I found it very helpful for outdoor structures, as it lasts longer in harsh weather conditions.
Additionally, you get faster project completion, strong joints, lower maintenance costs, and improved longevity. Plus, it’s environmentally friendly since you create less waste through repairs.
Where is Galvanized Steel Used?
Many people use galvanized steel for various projects. However, it has unique applications such as:
- Construction: Galvanized steel is used in roofing structures. Its corrosion resistance ensures durability in harsh weather, making it a popular choice.
- Automotive Industry: Many car parts, like body panels, are made from galvanized steel. This reduces rust and enhances vehicle lifespan.
- Farming Equipment: Galvanized steel tanks and equipment resist rust, ensuring they last longer outdoors, which is essential for farms.
- Infrastructure Repairs: Galvanized steel is often used in bridges and railings, helping maintain safety and integrity under stress.
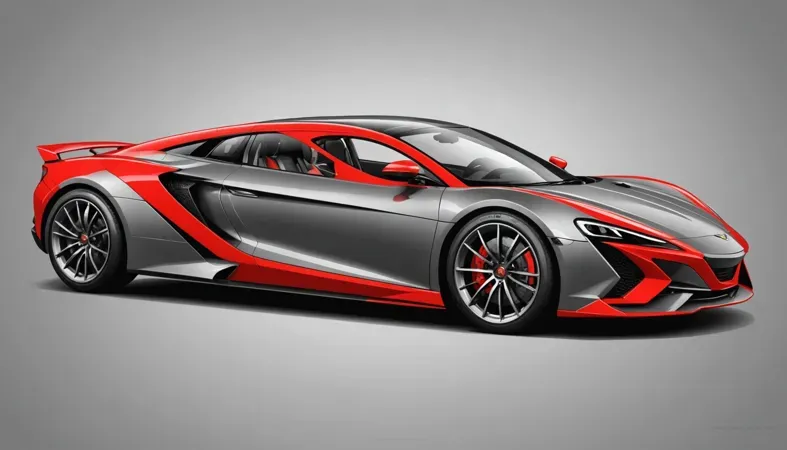
Explore the importance of welding galvanized steel in automotive design.
Are There Any Alternatives to Welding Galvanized Steel?
There are a few methods that can achieve results similar to welding galvanized steel. Techniques like soldering can work well, especially for smaller jobs, and products like Harris Stay-Silv 15 can create strong joints without the heat of welding. Another option is using mechanical fasteners such as bolts or rivets; they’re often preferred for larger structures where the heat from welding might damage the zinc coating.
Additionally, some acetylene-based braze can offer a good bond without risking harmful fumes. For instance, with a product like Bernzomatic’s Silver-Braze, you can effectively join metals without melting them. Each option has its place, so choose based on your project’s specific needs.
Frequently Asked Questions (FAQs)
Now let us look at the questions I typically get asked about welding, particularly with galvanized steel.
What is the Best Way to Weld Galvanized Steel?
Yes, the best way to weld galvanized steel is MIG welding. This method provides good penetration and a clean finish, which is crucial for metal coated in zinc. Welding with a solid wire MIG (0.030 In or 0.8 Mm Diameter) at 18-22 volts gives optimal results. Forge welding can also create strong bonds in metalwork and you can explore the detailed techniques of how to forge weld.
Is Galvanized Steel Harder to Weld?
Yes, galvanized steel is harder to weld due to the zinc coating. The coating can create fumes and porosity, complicating the welding process. Exposure to high heat can also lead to a weaker weld joint, so proper technique is vital. When considering projects that involve vehicles, it is important to understand the legality of welding a car frame to ensure compliance with safety standards.
What Happens if You Weld Galvanized Steel?
Welding galvanized steel can release toxic zinc fumes. If inhaled, these fumes can cause metal fume fever, which presents flu-like symptoms. Consequently, it’s critical to work in a well-ventilated area while welding.
Will a MIG Welder Weld Galvanized Steel?
Yes, a MIG welder can effectively weld galvanized steel. Use a 75/25 argon/CO₂ gas mixture for better shielding. Ensure you set the welder for 2-3 mm of thickness—this prevents burn-through while maintaining joint integrity.
Can I Weld Galvanized Steel Without Removing the Coating?
Yes, you can weld galvanized steel without removing the coating, but you should avoid overheating it. Overheating can vaporize the zinc, leading to poor welds. Many pros simply clean the area to be welded, minimizing fume exposure.
Conclusion
We’ve reached the end, and I appreciate you sticking around. We covered what galvanized steel is, its types and weldability, essential prerequisites, steps for welding, precautions to take, types of welding methods, factors that affect weldability, and unique issues you’ll face. We also touched on aftercare, advanced tips, key benefits, where you’ll find galvanized steel, and alternatives to welding it.
So, can you weld galvanized steel? Yes, but remember to prepare properly since fumes develop from the zinc coating. Techniques like MIG welding or using a TIG welder work best. Feel free to reach out if you have further questions about any specific steps or safety measures when you tackle this project.
To build on your understanding of welding techniques and enhance your skills, I encourage you to explore more at What is Welding.
References
- International Organization for Standardization. (2017). ISO 3834: Quality Requirements for Fusion Welding of Metallic Materials. Geneva, Switzerland: ISO.
Joe Carter is a retired welding professional with over 40 years of hands-on experience in the industry, spanning ship repair, structural welding, and even underwater projects. Joe is a master of MIG, TIG, and Stick welding. Passionate about mentoring the next generation of welders, Joe now shares his decades of expertise and practical insights to help others build rewarding careers in welding.
Metalworking, MIG Welding, Personal Protective Equipment, Safety Precautions, Welding, Welding Equipment, Welding Galvanized Steel, Welding Techniques, Zinc Coating