How to Weld Uphill? Techniques, Tips, Challenges, and Tools
Published on: February 11, 2025 | Last modified: March 4, 2025
By: Joe Carter
Uphill refers to the process of welding in an upward direction. It means you’re applying heat and filler material while moving your welding torch or rod against gravity.
A question that keeps coming up is how to weld uphill. It’s vital to know how to weld uphill since it affects joint strength and prevents defects. In my own experience, mastering uphill welding gives you better control and creates cleaner welds.
In this guide on how to weld uphill, we’ll cover the types of uphill welding, tools you’ll need, step-by-step instructions, precautions to take, various techniques, factors affecting the process, common issues and troubleshooting, as well as aftercare and advanced tips. We’ll also discuss the advantages, applications, and what alternatives exist. For instance, have you ever wondered can you weld 7018 downhill?
Contents
- How to Weld Uphill?
- What is Uphill Welding?
- Types Of Uphill Welding
- Things You’ll Need
- Precautions
- Steps to Weld Uphill
- Types Of Welding Techniques for Uphill
- Factors Influencing Uphill Welding
- Common Issues and Troubleshooting
- Aftercare, Inspection, and Advanced Tips for Uphill Welding
- Uphill Welding Equipment Comparisons
- Advantages Of Uphill Welding
- Applications Of Uphill Welding
- What Are the Alternatives to Uphill Welding?
- Frequently Asked Questions (FAQs)
- Conclusion
- References
How to Weld Uphill?
Welding uphill means working vertically against gravity. To weld uphill, maintain a steady travel speed, keep an angle of 10-15 degrees, and use a low amperage like 120-160A. It’s tough but great for structural steel and pipes. For more detailed techniques, consider mastering how to weld uphill effectively.
What is Uphill Welding?
Uphill welding is a technique where the welder works from a lower point to a higher point. This method is common for vertical or sloped joints. When welding uphill, you typically use a specific approach to manage the molten pool. Welds made in this manner show improved penetration and strength, especially with E7018 electrodes, which are used in 70% of structural welds.
To weld uphill, use the proper technique. For instance, working at a slight angle helps control the molten metal better. Adjusting the travel speed and voltage makes a significant difference when welding uphill.
I’ve seen a friend use this technique for a heavy-duty frame at a construction site. He chose to stick weld uphill with E7018, and the results were impressive. It’s fascinating how the choice of methods can impact the outcome; if you’ve ever wondered, “Can you weld uphill with E7018?” the answer is yes! Proper technique enhances durability and weld quality.
Types Of Uphill Welding
What types of welding can you do uphill?
-
Uphill MIG Welding
Uphill MIG welding connects metals on vertical surfaces. Set your MIG machine to a higher voltage for better penetration. Maintain a 15-30 degree angle and move your gun upward, adjusting your speed for a consistent bead.
-
Uphill TIG Welding
Uphill TIG welding offers precise control for thin materials. Use a smaller tungsten electrode for accuracy. Employ a stringer bead (Narrow Bead) motion upward, adding small amounts of filler metal to keep the weld pool steady.
-
Uphill Stick Welding
Uphill stick welding is ideal for structural jobs. Select a 7018 rod for quality results. Keep a 10-15 degree drag angle upwards and move slowly to maintain a strong arc for clean penetration.
-
Uphill Flux-cored Welding
Uphill flux-cored welding is useful for outdoor work. Choose self-shielded flux to minimize wind issues. Various materials serve as flux to ensure a stable arc and reduce spatter. Keep an upright torch angle and adjust your wire feed speed.
-
Uphill Pipe Welding
Uphill pipe welding is essential in construction. Use 6010 or 7018 rods for this type. Maintain a steady arc length, push the electrode, and use a whip technique to lay a strong bead on the pipe.
We’ve wrapped up the types of uphill welding here. Next up, we’ll look at the necessary materials and tools.
Things You’ll Need
What do you need to weld uphill effectively?
- Welding Machine: You’ll need a robust machine like the Lincoln Electric POWER MIG 210 MP. It’s essential for producing the right heat and stability while welding uphill.
- Welding Rods: Choose a high-quality rod like E7018. This rod offers excellent tensile strength of about 70,000 psi, making it ideal for uphill welding.
- Heat Shielding Spray: Use a product like Weld-Aid 188-M. This prevents spatter and bead issues when welding uphill, ensuring smoother results.
- Wire Feed Speed Control: Opt for a digital unit like the Miller Multimatic 215. Controlling the feed speed is crucial for maintaining a steady travel while tackling the uphill angle.
- Cleaning Equipment: Get a wire brush like the Eastwood Dual Head. Properly prepping your metal surfaces ensures maximum adhesion and strength. Don’t skip this step!
You should now have a good understanding of the materials required for this task. In the next part, we’ll discuss safety measures.
Precautions
Let’s cover essential safety measures for uphill welding.
- Clear Workspace: Keep your area tidy. Use tools like magnets to hold parts in place and prevent hazards.
- Wear Proper Gear: Always wear your helmet and gloves. Consider the Lincoln Electric K2988 for eye and skin protection.
- Verify Equipment Ratings: Check your welder’s amperage setting. For 7018 rods, settings between 85-150 Amps (Around 300-400 A) work great, depending on thickness.
- Protective Fume Extraction: Use a fume extractor like the Lincoln Electric Easy MIG 180. It provides clean air and reduces health risks.
Take safety precautions; they’re a priority for you and those around you!
So far we covered safety measures. Next, let’s look at techniques for welding on inclined surfaces.
Steps to Weld Uphill
We’ll cover how to weld at an upward angle for strong and solid joints.
-
Set Your Amperage
Start by adjusting your amperage to 115-135 amps for the 7018 electrode, depending on material thickness. Use a higher setting for thicker materials. Welding with 80 amps can also be effective for thinner materials with proper adjustments. A higher amp allows for better penetration while welding uphill.
Getting the settings right is crucial. Too low results in weak welds; too high causes burn-through or excessive spatter. Always check your settings before starting!
-
Choose Your Welding Technique
Pick a technique that fits your skill level, such as the whip-and-rag method or stringer bead. Beginners may find dragging up (Or Pulling) easier for better control when welding uphill.
Starting with a whip creates a wider bead, enhancing both the appearance and strength of the weld. Practice on scrap pieces first to find the method that feels right for you.
-
Maintain an Even Pace
Keep a steady pace of about 3-4 inches (7.6-10.2 Cm) per minute. Consistent speed prevents overheating and ensures good penetration. Going too fast risks undercutting the weld.
When I rush, I end up with more cleanup later. Slow and steady truly wins the race in uphill welding. Watch your puddle—it should have a slight wave motion without drips.
-
Use the Correct Overall Geometry
Pay attention to your welding angle. For uphill welds, maintain your torch at a 10-15 degree angle to effectively combat gravity. Move in a circular or oscillating motion while welding.
This geometry prevents slag inclusion and improves penetration. Adjust your angle as needed based on your position and the joint. Small tweaks can lead to significant improvements.
-
Control Slag Removal
After welding, always remove the slag. Slag in welding plays a crucial role in protecting the weld from contamination. This cleanup should occur in stages. Use a chipping hammer and brush immediately after the weld cools but is still warm. Remove as much slag as possible to reveal any defects.
A clean weld is a happy weld! I’ve learned that leaving slag can lead to issues like porosity or weak bonds. Patience during this step pays off.
We covered techniques for uphill welding here. Next, we will explore various types of welding methods for uphill processes.
Types Of Welding Techniques for Uphill
Let’s discuss the different types of welding techniques for uphill: Vertical Uphill, Overhead Uphill, 45-Degree Uphill, Weaving Technique, and the Stringer Bead Method.
-
Vertical Uphill Welding
In vertical uphill welding, you weld from the bottom to the top of a vertical seam. This technique typically uses a 3.2 mm (1/8 Inch) electrode, like 7018, which provides excellent penetration. A steady hand is necessary to ensure proper fill and avoid sagging. For those refining their skills, understanding how to weld vertical efficiently is essential.
-
Overhead Uphill Welding
Overhead uphill welding involves working beneath weld seams in a vertical position. You often use consumables suited for overhead applications, such as 6010 or 7018 rods. It’s challenging because of gravity, but with practice, you can achieve good penetration and clean beads. Learning the techniques for overhead welding is essential for producing quality work in difficult positions.
-
45-degree Uphill Welding
This technique involves welding at a 45-degree angle for better visibility of the joint. You can use various electrodes, but 7018 is great for a smooth finish. Always angle the puddle upward to maintain good fusion without burning through.
-
Weaving Technique for Uphill Welding
Weaving involves moving your welding torch side-to-side while going uphill. This method helps fill wider joints. I’ve noticed that weaving allows for better heat control, resulting in a more even bead appearance on wider joints.
-
Stringer Bead Method
The stringer bead method creates a straight line weld without oscillation. It’s effective for thin materials, where a narrow bead is sufficient. High heat input ensures deep penetration, which is crucial for uphill welding. For more detailed guidance, you can refer to the techniques for welding a straight bead.
Factors Influencing Uphill Welding
What factors affect your technique and quality when welding upwards?
-
Welding Position
Your position significantly affects control and visibility. When welding uphill, a vertical position requires precise electrode angle and motion to prevent sagging. Practice with a 10 to 15-degree drag angle for a better bead appearance.
-
Material Thickness
Thicker materials require more heat and coordination. For example, welding 1/4 inch (6 Mm) steel often needs more current and slower speeds to ensure proper penetration and fusion.
-
Welding Speed
Speed is crucial in uphill welding! If you go too fast, the bead may not fill well; if you’re too slow, you could burn through. A speed of about 4 to 6 inches per minute (10 to 15 Cm/min) is ideal, especially with rods like 7018.
-
Heat Input
Heat input is key for penetration and bead quality. Use this formula: Heat Input = Voltage x Current x 60 ÷ Travel Speed. Ideal values typically range from 20 to 30 kJ/m (6 to 9 Kj/ft), affecting how well your steel bonds.
-
Shielding Gas Type
Your choice of shielding gas impacts penetration. For instance, using pure CO2 creates deeper penetration compared to argon blends, which are better for smoother aesthetics. Choosing the right gas is crucial for quality in MIG welding uphill. For specific applications, understanding what shielding gas is used for MIG welding can optimize your welding results.
Common Issues and Troubleshooting
Let’s look at specific technical problems when you weld uphill.
-
Poor Penetration
While welding uphill, you may experience poor penetration due to inadequate heat input. Check your amperage. A common fix is to increase the current by 10-20%. Use the correct technique as well.
-
Excessive Spatter
Increasing the wire feed speed (WFS) can help reduce excessive spatter while welding uphill. Adjust the voltage settings downward for cleaner results.
-
Inconsistent Bead Appearance
Inconsistent beads can occur when welding uphill due to improper travel speed. Maintain a steady speed and angle. Aim for a 5-10° forehand angle to improve bead uniformity.
-
Difficulty in Maintaining Arc
In uphill welding, maintaining a stable arc can be challenging. If you can’t keep the arc, check your electrode angle and keep it within 10° for support. Adjusting your grip may also help.
-
Weld Defects
Upgrading the shielding gas or electrode can reduce defects like slag inclusions. Regularly inspect your work to identify these issues early. Consistency is crucial; catch problems before they escalate!
Aftercare, Inspection, and Advanced Tips for Uphill Welding
Here’s expert advice on aftercare, inspection, and strategies to optimize your uphill welding skills.
Aftercare Tips
After finishing your welding work, allow at least 15 minutes for cooling to prevent distortion and warping. Clean the weld area with a wire brush to remove slag and impurities, ensuring consistent quality.
Inspection Strategies
Inspect the cross-section of your weld with a file-like gauge at two locations: midway and at both ends. Look for undercutting or notches greater than 1/16 inch (1.6 Mm) to eliminate weak points. Use an oxide grinder process, like TEP, for efficiency; I recommend the DEWALT DWE4206, which has served me well.
Expert Tips
If you’ve got a few years under your helmet like I do, focus on controlling your travel speed at about 5-7 inches per minute (12-18 Cm/min). Track your heat input closely; stay between 12-18 kJ/m (5-10 Kj/ft) for optimal penetration while keeping an eye on bead width. For those looking to refine their skills further, helpful welding guidance can enhance your technique. Finally, practice staggered welding elements—flip your feed direction for a smoother joint.
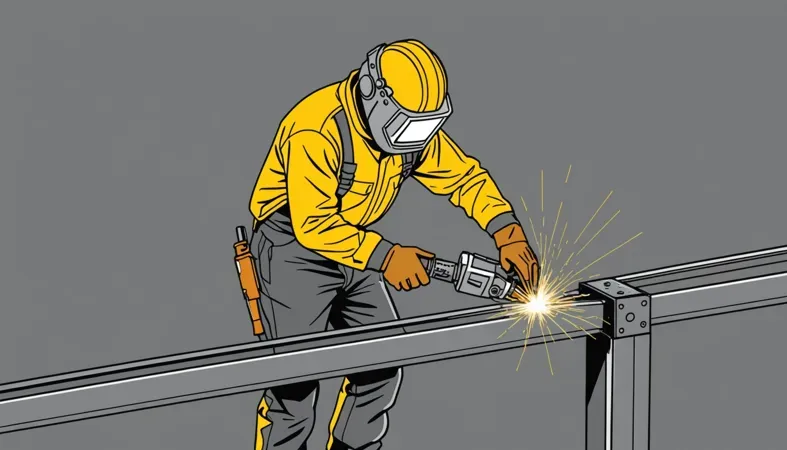
Uphill Welding Equipment Comparisons
Let’s dive into the best equipment for uphill welding, focusing on the welding machines and electrodes. Understanding the differences can help you choose what’s right for your projects.
Equipment Type | Best Options | Key Features | Ideal Application |
---|---|---|---|
Welding Machine | Lincoln Electric POWER MIG 210 MP | Versatile, easy to switch between MIG and flux-cored, lightweight at 40 lbs (18 kg). | Home projects, DIY, and light industrial work. |
Welding Machine | Miller Multimatic 215 | Multi-process capability, adjustable settings for better control, weighs 38 lbs (17 kg). | Small to medium fabrication, including uphill welding. |
Electrode | E7018 | Low hydrogen, high tensile strength, ideal for structural applications. | Thick steel plate and high-stress applications. |
Electrode | E6010 | Deep penetration with a fast-freezing slag, perfect for vertical builds. | Pipe welding and outdoor work. |
Electrode | E6013 | Easy to use, produces a smooth finish, good for thinner materials. | General light fabrication and DIY projects. |
Choosing the right welding machine and electrode significantly influences the outcome of uphill welding. Make sure to select tools based on your specific needs for the best results!
Advantages Of Uphill Welding
The main benefit of uphill welding is enhanced control. I’ve seen a friend use it for tricky joint configurations, and it worked well.
Additionally, it promotes better penetration, reduces slag inclusions, and allows for stronger welds. Plus, it’s effective for vertical positions and helps keep the weld pool where you want it.
Applications Of Uphill Welding
I’ve known people to use uphill welding for structural purposes. It has many applications, such as:
- Pipeline Construction: Used for welding pipelines that transport oil or gas. It minimizes slag defects and enhances joint integrity, making it popular in the industry.
- Heavy Equipment Repair: Common for repairing chassis and frames. Uphill welding improves bead placement and reduces heat input, preventing warping.
- Shipbuilding: Essential for constructing and repairing hulls. The uphill technique allows control over the weld pool in vertical joints, ensuring stronger, more reliable seams.
- Bridges and Steel Structures: Often used for joining vertical and overhead connections. Uphill welding helps achieve better penetration and stability, increasing durability.
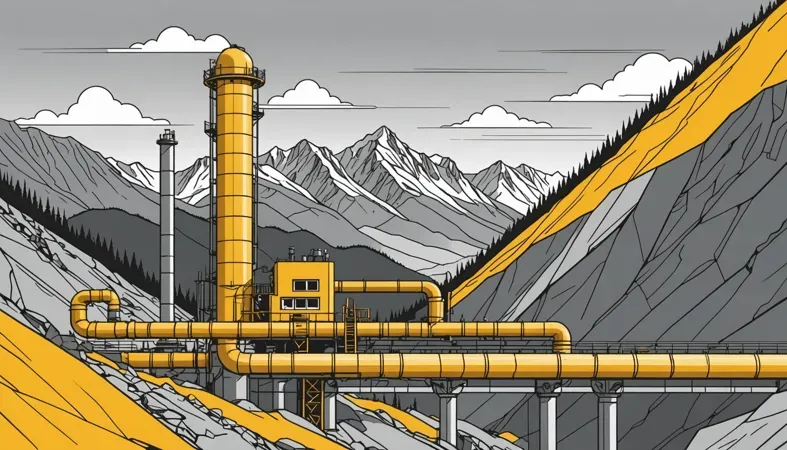
What Are the Alternatives to Uphill Welding?
There are other methods you can use to achieve similar results. Techniques like downhill welding with 7018 are preferred in certain cases because they can save time and reduce heat input. Consider reviewing how to MIG weld with a MIG machine, such as the Lincoln Electric Power MIG 210MP, to make vertical welds easier and more controlled.
From my unique perspective, I’ve noticed many beginners opt for vertical up stick welding amps for better control. You can get faster travel speeds with some equipment and conditions. It’s essential to evaluate your technique and tool options to see what works best for your project.
Frequently Asked Questions (FAQs)
Now let us look at some questions I typically get asked.
Can You Weld With 7018 Downhill?
Yes, you can weld with 7018 downhill. This technique is used when you want faster travel speeds and reduced heat input, which helps minimize distortion, particularly in sheet metal. However, it poses a higher risk of inclusions if not done correctly.
What is the Main Rule When Welding Vertical Uphill?
The main rule when welding vertical uphill is to maintain a steady travel speed and proper electrode angle. This ensures better penetration and a stronger weld bead because the molten metal has time to fuse properly and cool evenly.
What Does Drag Up Mean in Welding?
Drag up in welding refers to the technique of pulling the electrode towards you while you weld. This method helps control the molten pool, reducing the risk of excess spatter and ensuring even distribution in the weld bead. It’s key for vertical and overhead jobs.
How to MIG Weld Uphill?
You should use a push technique when MIG welding uphill. This allows better visibility and control over the weld pool. Additionally, set your wire speed higher and maintain a short arc length to prevent defects in the bead. Running a bead effectively with MIG welding requires understanding these techniques thoroughly.
What is the Angle for Uphill Welding?
The angle for uphill welding typically ranges from 5 to 15 degrees upward from vertical. This orientation assists gravity in directing the molten weld pool and improves bead appearance and penetration, especially in thicker materials.
Can You Weld Downhill With 7018?
Yes, you can weld downhill with 7018 electrodes, though it requires skill to prevent defects. This approach offers advantages like lower heat input and faster travel speeds, useful in thin materials or when minimizing warping is essential.
Conclusion
We’ve covered a lot about how to weld uphill. We discussed what uphill welding is, looked at types of uphill welding, outlined required tools, and went through the steps. We also talked about precautions, techniques, factors influencing welding, common issues, and advanced tips.
To weld uphill, you need to keep a steady hand and control your heat. Use rods like 7018 or techniques like MIG welding for best results. Remember, paying attention to angles and speed makes a huge difference in your weld quality.
For further expert insights and tips on welding, be sure to visit What is Welding.
References
- Lincoln Electric. (2020). The Procedure Handbook of Arc Welding (15th ed.). Cleveland, OH: Lincoln Electric Company.
- American Welding Society. (2021). AWS SENSE: Guidelines for Entry-Level Welders. Miami, FL: AWS.
- National Fire Protection Association. (2022). NFPA 51B: Standard for Fire Prevention During Welding, Cutting, and Other Hot Work. Quincy, MA: NFPA.
Joe Carter is a retired welding professional with over 40 years of hands-on experience in the industry, spanning ship repair, structural welding, and even underwater projects. Joe is a master of MIG, TIG, and Stick welding. Passionate about mentoring the next generation of welders, Joe now shares his decades of expertise and practical insights to help others build rewarding careers in welding.
American Welding Society, Home Projects, MIG Welding, Pipe Welding, Safety Measures, Techniques, Troubleshooting Welding, Uphill Welding, Welding, Welding Equipment