What is Slag in Welding? Understanding Types, Functions, and Removal
Published on: March 19, 2025 | Last modified: March 4, 2025
By: Joe Carter
Slag is the waste material formed during welding. It consists of impurities that are eliminated from the metal as it melts.
People are frequently curious about what is slag in welding. Understanding slag is crucial because it affects the quality and strength of your weld. From my experience, ignoring slag can lead to weak joins and costly repairs.
In this article, you’ll learn about how slag in welding works, different types of slag, the steps for welding with slag, factors affecting slag, and unique issues related to slag. We’ll also cover aftercare, inspection, advanced tips, applications, and alternatives to slag in welding. Dive deeper into related topics like what is weld slag and how to remove welding slag for a comprehensive understanding.
Contents
- What is Slag in Welding?
- How Does Slag in Welding Work?
- Types Of Slag in Welding
- Steps for Welding With Slag
- Factors Affecting Slag in Welding
- Understanding Slag Characteristics in Welding
- Unique Issues Related to Slag in Welding
- Aftercare, Inspection, and Advanced Tips for Slag in Welding
- Exploring Alternatives to Slag in Welding
- Frequently Asked Questions (FAQs)
- Conclusion
- References
What is Slag in Welding?
Slag is the byproduct formed during welding. It appears as a crust or layer on the weld bead, providing protection and insulation. Typical applications include shielded metal arc welding (SMAW) and flux-cored arc welding (FCAW) due to its protective qualities.
How Does Slag in Welding Work?
Slag in welding is a byproduct formed when the flux coating on the electrode burns during the welding process. It mainly consists of silica, metal oxides, and impurities that float on the molten weld pool. The slag layer typically ranges from 1 to 3 mm (0.04 To 0.12 In) thick, depending on the welding process and materials used. It protects the weld as it cools and solidifies, preventing contamination from the air.
Understanding slag’s role is vital for any welder. Slag acts as an insulator, shielding the weld from oxygen and nitrogen. This is crucial since these elements can weaken the weld’s integrity by mixing with the molten metal.
Dealing with slag isn’t just an afterthought; it’s essential for a strong weld. Many welders struggle with excess slag due to improper technique. Knowing how to remove welding slag properly can significantly enhance your work’s quality.
Types Of Slag in Welding
What are the different types of slag?
-
Ferro Slags
These slags contain a high percentage of iron oxides. In welding, they shield molten metal from oxidation and contamination. Use iron-rich flux materials when welding steel to generate ferro slag effectively.
-
Silicate Slags
Silicate slags are mainly formed from silica and clay. They act as insulating layers that protect the weld pool during cooling. Mix silica sand into your welding rod to produce silicate slag when welding cast iron.
-
Basic Slags
This type of slag is made from materials like limestone and dolomite. Basic slags neutralize acidic impurities in the molten weld. Incorporate low-acid flux materials into your welding setup to optimize weld quality. Additionally, understanding the specific roles of gases can enhance welding processes; nitrogen gas is often crucial in operations aimed at improving weld characteristics, and exploring what nitrogen gas is used for in welding highlights its importance in such applications.
-
Acidic Slags
As the name suggests, these slags contain acidic components like silica. They’re often used for welding codes that require high-strength joints. Use high-silica fluxes when welding certain types of steel to achieve acidic slag.
-
Composite Slags
Composite slags are a mix of several slag types designed for specific applications. They combine properties to improve weld strength and durability. Blend various flux materials tailored to your welding needs for enhanced performance.
We covered the various types of slag in welding. Next, we will cover the steps for welding with slag.
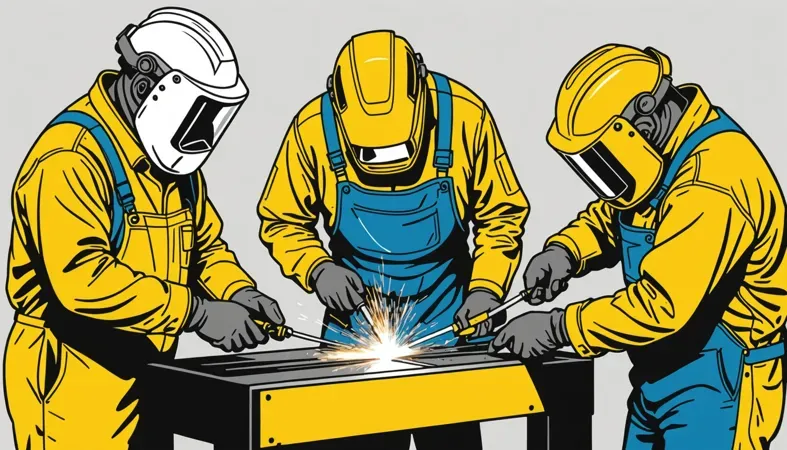
Steps for Welding With Slag
This section covers steps for understanding and managing slag in welding.
-
Select the Right Electrode
Choosing the right electrode is vital for controlling slag formation. Use electrodes with coatings made of inorganic materials. The AWS class and current type dictate your choice. High-quality electrodes create less slag; for example, E7018 has less slag compared to E6010.
Select electrodes based on your steel type and thickness. For 6mm (0.25 In) thick steel, I recommend E7018. Higher alloy content can lead to more slag, so align your selection with the material requirements. The importance of picking the right electrode can’t be overstated; trust me!
-
Prepare the Workpiece
Cleaning the workpiece is essential to minimize slag production. Remove oils and contaminants with a wire brush or grinder. The cleaner your base metal, the less slag you’ll encounter during welding. Aim for a surface profile of about 25 to 76 micrometers (1 to 3 Mils) for the best adhesion. Proper surface preparation can also drastically reduce spatter issues, avoiding spatter in welding.
Ensure the edges fit correctly, and the gaps are small. A tight fit reduces waste and minimizes excessive slag. With a clean workpiece, you’ll see where quality welding truly begins.
-
Perform the Welding Process
Start your welding process with consistent settings. Set your voltage around 20-30V; amperage should suit your electrode—generally 60-120A for E7018 rods. Move steadily, using a stringer bead or weave pattern to manage the molten pool. I usually prefer a stringer weld because it produces less slag than a wider weave. For more tips on achieving better results, refer to the section on welding guidance.
Understanding the nuances and methods of welding can help improve your technique; learn more in this comprehensive overview of welding.
Maintain a proper travel angle of about 10-15 degrees to help control slag. Observe your heat input; too much can generate more slag. Adjusting your technique as you go can significantly affect the final results. Always strive for a uniform bead to keep slag production minimal.
-
Allow the Slag to Cool
After welding, let the slag solidify on its own, usually taking about 10-15 minutes. This cooling period is important for slag strength and separation. If you rush this step, you risk issues with porosity (Small Holes) and defects in the weld. The right cooling time creates a stronger bond between the weld and the base material. Understanding the different types of welding processes can further enhance your welding technique and also improve the quality of the final product, which you can explore in the different types of welding.
Watch the cooling process; some slag can turn powdery if cooled too quickly, making it hard to remove later. A stable environment helps maintain uniform temperature around your weld, ensuring even solidification. Trust me; giving it some time pays off.
-
Remove the Slag
Once cooled, carefully chip off the slag with a hammer or chisel. Follow up with a wire brush to remove finer slag particles. Aim for thorough cleaning; residual slag can lead to future issues like cracks or weakness in the joint. Always check for coverage; you should have a clean weld appearance.
Manual removal might take effort, but it’s crucial for quality results. You can also use a grinder with a flap disc for stubborn areas, making the job easier. The end goal is a smooth surface for any potential inspections or additional coatings.
We have now covered the steps for welding with slag. Next, we will examine the factors that influence slag in welding.
Factors Affecting Slag in Welding
What factors influence the properties of slag produced during welding?
-
Type Of Electrode
The choice of electrode significantly impacts the quality of welding slag. For example, a low-hydrogen electrode produces less slag than a standard stick, which leads to better welds and stronger joints.
-
Welding Technique
Your welding method affects the amount of slag produced. Techniques like TIG (Tungsten Inert Gas) welding create less slag than MIG (Metal Inert Gas) welding, which can alter how the molten metal flows and cools during the process. When welding in various positions, understanding the specifics of 3G welding technique can significantly impact the outcome.
-
Heat Input
Higher heat input can lead to more extensive slag formation. More energy causes the base material and filler to melt together, resulting in variations in slag types and characteristics.
-
Protective Gas Used
The protective gas you use can dramatically change the slag’s characteristics. Inert gases like argon help create cleaner welds with less slag compared to non-inert options.
-
Material Composition
The base materials you’re welding play a crucial role. Metals with high sulfur content can produce more slag, which can compromise the integrity of your weld.
That covers the factors influencing slag in welding. Let’s now take a look at the characteristics of slag in welding.
Understanding Slag Characteristics in Welding
To grasp the essence of slag in welding, you should know its distinct characteristics and how they impact your work.
Key Characteristics of Slag
Characteristic | Description | Impact on Welding |
---|---|---|
Density | Slag density varies between 2.2 to 3.5 g/cm³ (grams per cubic centimeter). | Higher density can provide better protection but may require more effort to remove. |
Viscosity | Viscosity affects how easily slag flows. It can range from thin to very thick. | Thicker slag can trap impurities; understanding its viscosity helps control bead profiling. |
Color | Slag can appear in various colors: dark green, black, or even white depending on composition. | Color often indicates the composition; for instance, dark slag usually signals iron-rich materials. |
Thermal Stability | Stable slag retains heat well, mitigating rapid cooling. | This stability prevents cracking in welds but can delay clean-up processes. |
Influence of Slag Properties on Weld Quality
- Improved Weld Penetration: Certain slag types enhance heat retention, promoting deeper penetration in welds.
- Reduced Oxidation: The insulating layer formed by slag shields the molten metal, reducing oxidation and contamination.
- Slag Fluidity: Fluid slag can assist in self-leveling, leading to smoother weld surfaces and less rework.
That covers the features and properties of slag in welding. Let’s now take a look at specific challenges associated with slag.
Unique Issues Related to Slag in Welding
Let’s look at the unique technical problems related to slag.
-
Slag Inclusion in Welds
Slag inclusion in welds can weaken the joint. To identify this, look for dark spots in the weld. Use a grinder to remove the slag and re-weld for a strong seam.
-
Difficulties in Slag Removal
Slag removal can be tricky. A chipping hammer and wire brush are helpful. Don’t forget to clean between weld layers.
-
Inconsistent Slag Properties
Inconsistent slag properties can result from poor material. Check for abnormal color and texture. Maintain correct heat settings for uniformity.
-
Slag Leakage Impact
Slag leakage can create air pockets that weaken the weld. Look for exposed areas to identify it. Use proper welding techniques to seal the gaps tightly.
-
Slag Formation During Overlapping
Slag formation during overlapping can happen if you overlap too much. Look for uneven beads. Adjust your travel speed and angle to minimize this issue.
Aftercare, Inspection, and Advanced Tips for Slag in Welding
Here’s key guidance on aftercare, inspection, and expert strategies for dealing with slag.
Aftercare Tips
After completing a weld, wait 15 to 30 minutes for the joint to cool before removing slag. Use a wire brush or scraper, like the Lincoln Electric 99A62, for effective slag removal. Always wear gloves when handling welding equipment, and ensure your cleaning tools are in good condition to prevent damage.
Inspection Techniques
Inspect the weld for lingering slag inclusions using a tool like a digital microscope; ideally, focus at around 40x magnification for clear results. Check the bead shape, measuring the width at 5 mm (0.2 In) for consistency. I often use the Miller Multimatic 215 for detailed inspection because it offers precision welding and clear quality.
Expert Tips
Here’s a pro tip based on my experience: adjust your travel speed to manage slag production effectively; slower speeds create more slag. Experiment with electrode angles—an angle of around 30 degrees can yield cleaner welds. Maintaining optimal heat settings is key; I usually set it to about 250 A (Amps) depending on the thickness being welded. Mastering these techniques becomes even more crucial when tackling challenging positions, such as welding overhead, which requires precise control and adjustments. For further insights on this specialized skill, explore welding in overhead positions.
Exploring Alternatives to Slag in Welding
There are several options available to achieve similar results without slag. Techniques like gas tungsten arc welding (GTAW) with argon shielding gas, for example, eliminate slag formation altogether, offering a cleaner finish. Products such as Lincoln Electric’s TIG welder have consistently worked for me in delivering high-quality welds without the mess of slag. When working with piping systems socket welds ensure a strong and leak-proof joint due to their unique design features, as explored in the socket weld method.
Another alternative is using flux-cored arc welding (FCAW) that typically produces less slag compared to shielded metal arc welding (SMAW). Some core materials specify minimal slag, allowing for easier cleanup. If you’re looking for a smoother finish, using machines like Miller’s Multimatic series can bring precision with less cleanup required.
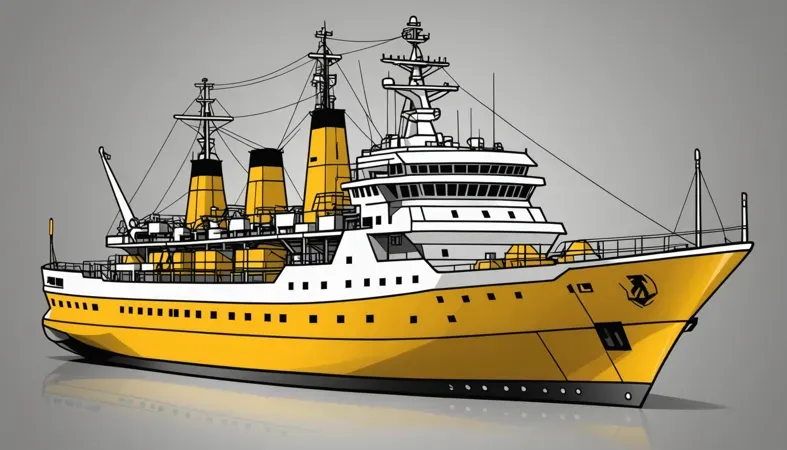
Frequently Asked Questions (FAQs)
Here are some common questions I typically get asked.
What is the Purpose Of Slag in Welding?
The purpose of slag in welding is to protect the weld from contaminants. Slag acts as a barrier between the molten weld and the atmosphere, which prevents oxidation. If the slag isn’t there, impurities can weaken the joint, compromising the overall strength.
Does Slag Need to Be Removed?
Yes, slag needs to be removed after welding. If you leave slag on the weld, it can lead to poor adhesion and potential issues in the future. Depending on the welding method, it’s often recommended to clean the weld with a wire brush or grinder to ensure a strong bond.
What is Mill Scale in Welding?
Mill scale in welding refers to the flaky surface of hot-rolled steel. This scale can negatively affect the weld quality if not removed. It’s crucial to clean the steel using methods like grinding or using solvents to provide a clean surface for effective welding. When dealing with metalwork, it’s also useful to explore using a welder to thaw pipes, which can add versatility to welding skills.
What is Clad Welding?
Clad welding is a process where one material is welded onto another to improve properties. For example, cladding stainless steel on carbon steel enhances corrosion resistance. This method can save costs while maintaining the benefits of both materials, making it an essential technique to understand in the realm of welding fundamentals.
A proper understanding of shielding gases can optimize the welding process, particularly when it comes to using 75/25 welding gas.
How to Remove Slag From Welding?
You can remove slag from welding using a chipping hammer or wire brush. It’s important to do this while the bead is still warm for easier removal. Not cleaning slag effectively can lead to defects and a weaker weld.
What is Electroslag Welding?
Electroslag welding is a specialized welding process, mainly for thick steel sections. It uses a molten slag pool to join materials. This method allows for high deposition rates and lower heat inputs, making it effective for large structures.
What is a Waste Stream in Welding?
A waste stream in welding refers to the waste produced during the welding process, including scraps and materials like flux and slag. Understanding waste streams helps improve efficiency and reduces environmental impact, ultimately saving costs.
Conclusion
We are almost done. We covered what slag is in welding, how it works, different types of slag, steps for welding with slag, and factors affecting slag formation. We also talked about unique issues, aftercare, inspection, applications, and alternatives to slag in welding.
In simple terms, slag in welding is the stony mass made during the weld process. It serves multiple purposes like shielding the weld area and preventing contamination, with specific conditions varying the slag’s properties. Wishing you success in your welding projects, remember that understanding these factors helps create clean, strong welds.
If you’ve made it this far, consider exploring more resources at What is Welding to enhance your knowledge further.
References
- Lincoln Electric. (2020). The Procedure Handbook of Arc Welding (15th ed.). Cleveland, OH: Lincoln Electric Company.
- Norrish, J. (2006). Advanced Welding Processes. Boca Raton, FL: CRC Press.
- Welding Institute (TWI): https://www.twi-global.com
- National Fire Protection Association. (2022). NFPA 51B: Standard for Fire Prevention During Welding, Cutting, and Other Hot Work. Quincy, MA: NFPA.
Joe Carter is a retired welding professional with over 40 years of hands-on experience in the industry, spanning ship repair, structural welding, and even underwater projects. Joe is a master of MIG, TIG, and Stick welding. Passionate about mentoring the next generation of welders, Joe now shares his decades of expertise and practical insights to help others build rewarding careers in welding.
Arc Welding, Art, Slag Removal, Surface Preparation, Types Of Slag, Weld Quality, Welding, Welding Processes, Welding Skills, Welding Techniques