How to Start Oxy Acetylene Welding? Discover Techniques, Safety, and Tips
Published on: November 23, 2024 | Last modified: March 4, 2025
By: Joe Carter
Oxy acetylene welding is a process that joins materials, usually metal, using a flame created by burning oxygen and acetylene gas. It’s widely used due to its effectiveness and versatility.
It’s a question I’ve heard often: how to start oxy acetylene welding? Understanding this is crucial because it sets the foundation for safety and skill. I remember my first attempt; I didn’t follow the steps closely, which led to a disaster. Trust me, starting off with proper instructions makes all the difference.
In this guide, you’ll see how to use an oxy acetylene welding torch, the prerequisites needed, various welding techniques, steps to get started, precautions, and how to tackle common problems. We’ll also discuss the benefits of oxy acetylene welding and its applications in real-world situations. So, let’s dive into mastering how to weld with oxy acetylene!
Contents
- How to Start Oxy Acetylene Welding?
- What is Oxy-acetylene Welding?
- Types Of Oxy-acetylene Welding
- Prerequisites
- Precautions
- Steps to Start Oxy-acetylene Welding
- Essential Oxy Acetylene Welding Techniques
- Factors Influencing Oxy-acetylene Welding
- How to Address Common Problems in Oxy-acetylene Welding
- Top Benefits Of Oxy-acetylene Welding
- Applications Of Oxy-acetylene Welding
- Alternatives for Oxy Acetylene Welding Techniques
- Frequently Asked Questions (FAQs)
- Conclusion
- References
How to Start Oxy Acetylene Welding?
Oxy acetylene welding is a process using fuel gases to weld metals. To start oxy acetylene welding, gather your torch, regulators, and cylinders. Turn on the gas, ignite the torch, and adjust the flame. It’s beginner-friendly for metal fabrications.
What is Oxy-acetylene Welding?
Oxy-acetylene welding (OAW) is a process that uses a flame fueled by oxygen and acetylene gas. The temperature can reach around 3,500°C (6,332°F), making it one of the hottest welding methods available. This intense heat allows you to melt metal quickly and effectively. Typically, the torch system includes gas cylinders, regulators, and hoses to control the mixed gas flow.
When starting oxy-acetylene welding, you need to understand the basics of setting up your equipment. It’s crucial to familiarize yourself with the oxy-acetylene welding tools, like the torch and regulators. In my experience, having the right gear ready saved me time and hassle when I first started. Once you learn how to mix the gases properly and ignite the torch, you’ll be ready to begin!
I used it frequently for my job, especially for repairs on various metal structures. The first time I welded with an oxy-acetylene torch, I realized just how versatile it is, particularly for joining steel. You may want to learn more about using an oxy-acetylene torch as it offers precise control and quick heat-up, making it perfect for small projects or detailed work.
Types Of Oxy-acetylene Welding
What are the types of oxy-acetylene welding?
-
Gas Welding
Gas welding uses a flame from an oxy-acetylene torch to join metals. First, prepare your oxy-acetylene welding kit. Set the acetylene to about 5 PSI and the oxygen to around 10 PSI, then ignite the torch to create the flame.
-
Cutting Welding
This type uses a hot flame to cut through metal. For oxy-acetylene cutting, you need a cutting torch. Set the oxygen to around 30 PSI and ignite it for a focused cutting flame. Adjust until you see a steady cutting stream.
-
Brazing Welding
Brazing uses high heat and a filler metal to bond materials without melting them. To begin brazing, choose a suitable filler rod and set your torch to about 5 PSI of acetylene and 10 PSI of oxygen. Heat the metals until they glow, then feed the rod into the joint.
-
Heating Welding
Heating welding warms metal joints in preparation for welding. Set the oxy-acetylene torch to low settings, around 2-4 PSI of acetylene. Direct the flame onto the metal surface until it reaches the desired temperature. Choosing the correct welding rod is crucial for ensuring a strong weld, and you can learn more about what welding rod to use for different metals and applications.
-
Surfacing Welding
This type adds a layer of metal to protect a surface. For surfacing with oxy-acetylene, you’ll need filler material. Set the torch to medium settings for oxygen and acetylene. Focus the flame on the area to be built-up, then apply the filler as you heat.
You should now have a good understanding of the different types of oxy-acetylene welding. In the next part, we’ll discuss prerequisites.
Prerequisites
What do you need to get started?
- Oxy-Acetylene Torch Kit: You need a kit like the Harris 803 Regulators Oxy-Acetylene Kit. It provides the essentials to control gas flow and ensures a safe, steady flame.
- Fuel Gases: You need oxygen and acetylene, such as Medical Grade Oxygen (O2) and Acetylene Gas in cylinders. These gases work together to create high temperatures (Up to 3,500°C/6,332°F) for effective welding.
- Welding Filler Rods: You need filler rods, such as ER70S-6, that add strength to the joint.
- Weldable Base Materials: You need metals like mild steel (A36) and aluminum (6061). Using the right material is crucial, as each has a distinct melting point that affects weld quality.
We’ve wrapped up necessary prerequisites here. Let us turn our attention to the precautions you should take next.
Precautions
Here are essential safety measures for oxy-acetylene welding.
- Adequate ventilation: Ensure good airflow to avoid harmful gas buildup; use a fan or work in an open space.
- Use personal protective equipment: Always wear welding gloves and goggles, such as 3M Protective Glasses, to shield against sparks and UV light.
- Check equipment regularly: Inspect hoses and connections for leaks; a soapy solution helps identify leaks.
- Be fire-ready: Keep a fire extinguisher nearby; choose one rated 3-A:40-B:C for proper protection.
Safety’s crucial—I learned that the hard way. Stay safe!
You should now have a good understanding of safety measures for oxy-acetylene welding. In the next part, we’ll discuss starting steps.
Steps to Start Oxy-acetylene Welding
Here are the steps to launch your oxy-acetylene welding project successfully.
-
Gather Necessary Equipment
Before you start, make sure you’ve got the right gear. You’ll need an oxy-acetylene torch set, gas cylinders, and protective equipment like gloves and goggles. Don’t forget the welding filler rod, usually made of steel. Each cylinder typically holds oxygen (Around 20 Kg or 44 Lb) or acetylene (About 7 Kg or 15 Lb) to sustain your work.
I once used a subpar regulator, and it was a nightmare! Quality gear is essential for a clean weld. Trust me, invest in proper equipment; it’ll pay off when you see those neat beads forming.
-
Set Up the Workspace
Next, set up a well-ventilated workspace. Clear the area of any flammable materials to reduce risks. Aim for an open area of around 10 cubic meters for safety and efficiency. This not only protects you but also ensures good airflow when cutting or welding.
If possible, use a portable welding table. A sturdy surface makes a difference—I learned that lesson the hard way. A stable platform lowers distractions and mistakes. Keep your tools organized within arm’s reach to avoid scrambling mid-weld.
-
Prepare the Materials
Now it’s time to prepare your materials. Clean the metal pieces you’ll be welding to remove any rust or grease. Ideally, use a wire brush or grinder for this. A clean surface is crucial for strong welds. Contamination can cause weak joints!
Clamp your pieces tightly. I once neglected to secure a piece, resulting in uneven welds. Align everything perfectly for good penetration and to prevent warping from heat. Double-check that you’ve clamped them securely.
-
Adjust the Gas Flow
With your materials prepped, you’ll need to adjust the gas flow. Open the acetylene valve first, setting it to around 5 to 7 psi. Then open the oxygen valve at 20 to 25 psi. This balance creates the ideal flame for your weld—a neutral flame has a 1:1 ratio of oxygen to acetylene.
When you strike the flame, be ready to tweak the knobs slightly afterward; the pressure may fluctuate. I recall being too eager at first, but take your time! Finding the right flame adjusts the heat for optimal welding and reduces blowhole risks.
-
Begin Welding Technique
Now let’s dive into the actual welding. Hold the torch about 1/4 inch (6 Mm) from the metal surface. Move steadily, creating a ‘V’ pattern with the flame. Keep your hands steady to avoid uneven welds, maintaining a constant speed to use your filler material effectively.
Start with small tack welds to secure your pieces before doing long runs. Don’t skip this! I once rushed into a project and ended up with warped metal. Start slow and increase your speed as you gain confidence. Aim for consistency with nice, even beads!
We’ve wrapped up the steps to begin oxy-acetylene welding here. Let us turn our attention to essential welding techniques.
Essential Oxy Acetylene Welding Techniques
Let’s break down specialized techniques to enhance your oxy-acetylene welding skills.
Technique | Description | Ideal For | Speed (Inches Per Minute) |
---|---|---|---|
Weaving | Creates a zigzag pattern with the torch to broaden the weld area. | Wide joints or seams. | 4-6 |
Push and Pull | Push the flame through the joint for a stable weld; pull it back for delicate areas. | Thin metals and delicate work. | 3-5 |
Stringer Beads | Using a steady, straight motion without weaving; ideal for thicker materials. | Thick sections and repairs. | 5-7 |
Circle Motion | Circling the torch tip to melt spots, perfect for filling gaps. | Repairs and joints with misalignment. | 2-4 |
Knowing these techniques will help you apply the right approach for your specific welding tasks. Experiment and find what works best for your projects!
Factors Influencing Oxy-acetylene Welding
What factors determine the effectiveness of oxy-acetylene welding techniques?
-
Gas Pressure Levels
Proper gas pressure is crucial for flame stability. Typically, set acetylene at 5–10 psi (34.5–69 Kpa) and oxygen at 10–15 psi (69–103 Kpa). Too low a pressure can lead to a weak flame, making it hard to achieve the desired weld.
-
Welding Speed
Adjusting your welding speed affects heat input and penetration depth. A slower speed increases heat, resulting in deeper welds, while a fast pace may weaken the bond or cause incomplete fusion. Understanding the specifics of electrode classification can greatly impact the quality of your welds, and details such as the E316-16 electrode guide welders in choosing the right tool for their projects.
-
Material Thickness
Welding thicker materials requires more heat. I once underestimated the time needed to concentrate heat on a thicker steel piece, resulting in a cold joint. For welding processes, thickness of ¼ inch (6 Mm) or greater may require preheating.
-
Welding Position
The position affects weld quality. Overhead or vertical positions are trickier; they require more control to prevent molten metal from dripping. Understanding your body mechanics and torch control is critical in these scenarios.
-
Ambient Temperature
Cold environments can cool your welds quickly, while high temperatures may increase the risk of overheating and warping. Aim for stable conditions to ensure a quality weld.
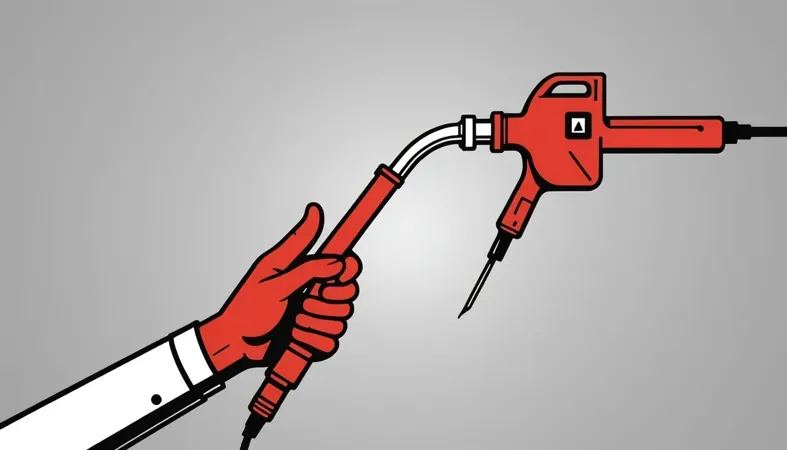
How to Address Common Problems in Oxy-acetylene Welding
Here are some specific issues you might encounter with oxy-acetylene welding.
-
Improper Flame Adjustment
Oxy-acetylene welding requires the right flame for quality work. A neutral flame is best. Check the color: a clear, defined cone indicates success. Too much oxygen or acetylene results in burning. Adjust the needle valves and check the flame again.
-
Inconsistent Welding Bead
During oxy-acetylene welding, I once created a messy bead. Uneven pressure or speed can cause this. Monitor your hand speed and ensure steady pressure. Use the torch at a 45-degree angle to maintain smooth movement.
-
Material Distortion
Excessive heat in oxy-acetylene welding leads to distortion. If you’re melting metal instead of joining it, your flame’s too hot. Maintain control; pause to allow the material to cool.
-
Gas Leaks
Gas leaks in oxy-acetylene welding aren’t just annoying; they’re dangerous. Smelling gas or hearing hissing may indicate a leak. Use soapy water to find bubbles in connections. Tighten or replace fittings as needed.
-
Difficulty Starting the Flame
It’s frustrating when you can’t ignite the flame in oxy-acetylene welding. Check your acetylene to ensure it’s pressurized. Use a flint striker while keeping the torch’s valves slightly open for success.
Top Benefits Of Oxy-acetylene Welding
The main benefit of oxy-acetylene welding is its versatility. I’ve used it extensively for metal fabrication and repair work.
Additionally, you’ll appreciate several advantages, such as precise heat control, the ability to weld various metals, portable equipment, and cost-effective materials.
Applications Of Oxy-acetylene Welding
People often use oxy-acetylene welding to repair metal structures. Its applications include:
- Pipe Fitting: Commonly used for joining pipes in plumbing and construction. It’s popular for handling various diameters and delivering strong joints.
- Automotive Repairs: Ideal for welding panels and exhaust systems. This method is chosen for its speed and versatility, especially in restoring older vehicles.
- Sheet Metal Fabrication: Excellent for creating custom metal products. Many prefer it for providing precise and clean welds on thin materials.
- Artistic Metalwork: Artists use it to create sculptures and decorative items. It allows for creative freedom with a variety of materials.

Alternatives for Oxy Acetylene Welding Techniques
If you’re looking for alternatives to oxy acetylene welding, consider MIG and TIG welding. MIG, or Metal Inert Gas welding, uses a continuously fed wire and is great for beginners due to its ease of use. On the other hand, TIG, or Tungsten Inert Gas welding, offers superior control and is ideal for thin metals. Brands like the Lincoln Electric SP 125 Plus are popular in the MIG world, while the Miller Syncrowave 210 shines in the TIG category. If there’s one thing I’ve gained from my journey, it’s that choosing the right method depends on your project needs.
Another option is plasma cutting, which can deliver clean cuts and precise edges. It’s preferred for thick materials where traditional welding struggles. Equipment like the Hypertherm Powermax is praised for its performance. Additionally, some DIY enthusiasts use soldering tools for small metal parts when high heat isn’t essential. Each method has its strengths, so evaluate your project and budget to find what suits you best. Explore options and ensure you pick the right path for your needs!
Frequently Asked Questions (FAQs)
Now let us look at some common questions I typically get asked about oxy acetylene welding.
Do I Open Oxygen or Acetylene First?
Yes, you should open acetylene first. Opening acetylene first allows you to adjust the flame without risking an explosion. At the torch, you should never open oxygen above 1 PSI (6.9 Kpa) when acetylene is open, as different pressures can lead to an unsafe situation.
How Do You Set Up the Oxy-acetylene Equipment Step by Step?
To set up the oxy-acetylene equipment, start by securing the torch to the hoses. Connect the oxygen and acetylene regulators, and open the cylinder valves to ensure proper gas flow. Always check for leaks with a soap solution; around 10% of welding accidents stem from gas leaks. Many professionals also use inverter welders for their efficiency, and you can explore detailed insights on what an inverter welder is.
Which Valve Do You Open First, on Oxygen or Acetylene?
You always open the acetylene valve first. It’s crucial because if you adjust the pressure on acetylene, you can achieve a more controllable flame. Following this, open the oxygen valve gradually for an optimal and efficient welding flame.
What Are the Common Uses Of Oxy Acetylene Welding?
Oxy acetylene welding is commonly used for metal fabrication, repairs, and cutting. It’s perfect for materials like steel and aluminum, with maximum cutting thickness reaching 300 mm (11.8 In). Often, professionals use it in construction, automotive, and art industries.
What Safety Gear Do I Need for Oxy Acetylene Welding?
For oxy acetylene welding, you’ll need a welding helmet, gloves, and protective clothing. A helmet with a shade of at least 3 is necessary to protect your eyes from harmful UV/IR radiation. You should also wear non-flammable materials to shield yourself from sparks and heat.
Can You Weld Dissimilar Metals With Oxy Acetylene?
Yes, you can weld dissimilar metals using oxy acetylene welding. Adjust the filler rod to match the materials. For instance, welding copper to steel is possible but can be tricky. Careful temperature management is key; too much heat may cause unwanted melting.
Conclusion
I hope this gave you what you needed to kickstart your journey in oxy acetylene welding. We covered essential topics like what oxy acetylene welding is, the types, prerequisites, and the steps to get started. Don’t forget precautions, techniques, factors influencing your weld, and aftercare tips, plus the benefits and applications of this useful method.
To recap on how to start oxy acetylene welding: gather your gear, including the torch, cylinders, and safety equipment. Remember, proper setup and technique are crucial for successful welding, whether you’re practicing or tackling a project. If you need additional advice, I’m here to help with your oxy acetylene welding needs.
For a broader understanding of welding techniques and practices, feel free to return to What is Welding.
References
- American Welding Society. (2015). AWS D1.1/D1.1M: Structural Welding Code – Steel. Miami, FL: AWS.
- European Welding Federation (EWF): https://www.ewf.be
- National Fire Protection Association. (2022). NFPA 51B: Standard for Fire Prevention During Welding, Cutting, and Other Hot Work. Quincy, MA: NFPA.
Joe Carter is a retired welding professional with over 40 years of hands-on experience in the industry, spanning ship repair, structural welding, and even underwater projects. Joe is a master of MIG, TIG, and Stick welding. Passionate about mentoring the next generation of welders, Joe now shares his decades of expertise and practical insights to help others build rewarding careers in welding.
American Welding Society, Beginner Welding, Metal Fabrication, Oxy-acetylene Welding, Personal Protective Equipment, Welding, Welding Safety, Welding Table, Welding Techniques, Welding Tools