How to MIG Weld? A Guide on Basics, Steps, and Safety
Published on: November 20, 2024 | Last modified: March 4, 2025
By: Tyler James
MIG stands for Metal Inert Gas welding. It’s a popular method that uses a continuous wire feed to create strong welds.
I get asked quite often how to how to mig weld. This question’s crucial because following proper techniques can make all the difference in your project’s quality. From my experience, a well-done MIG weld can save time and material, ensuring your work looks professional and holds up well.
In this guide, you’ll learn about MIG welding basics, the necessary equipment, safety tips, various MIG processes, factors that affect welding, unique issues you may face, and aftercare. We’ll dive into applications, benefits, and even how not to mig weld. Let’s explore how to weld mig like a pro in no time!
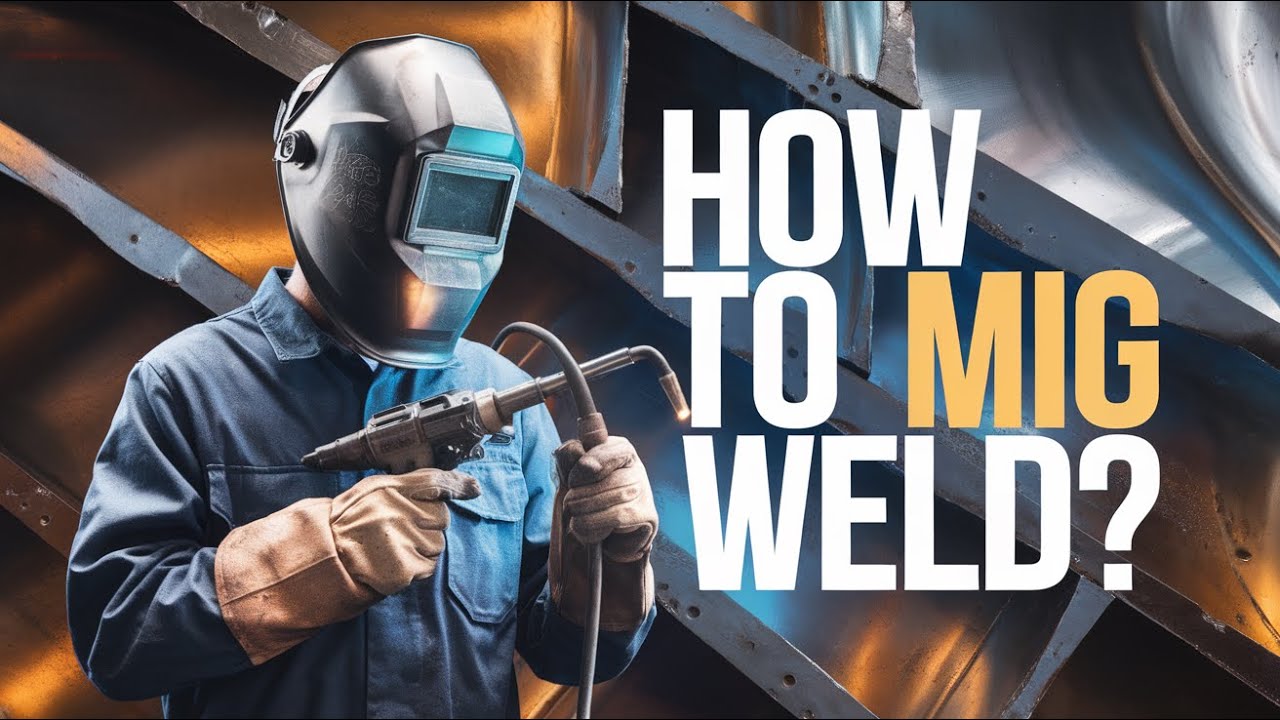
Contents
- How to MIG Weld?
- What is MIG (Metal Inert Gas Welding)?
- Types Of MIG in Context Of How to MIG Weld
- Prerequisites: What Do You Need
- Steps for How to MIG Weld
- Safety Tips
- Types Of MIG Welding Processes
- Factors Affecting MIG Welding
- Common Problems in MIG Welding
- Aftercare, Inspection, and Advanced Tips for MIG Welding
- Top Benefits You Can Expect From MIG Welding
- Applications Of MIG Welding
- Other Options for Achieving Similar Results to MIG Welding
- Frequently Asked Questions (FAQs)
- Conclusion
- References
How to MIG Weld?
MIG, or Metal Inert Gas, uses a wire electrode for welding. To MIG weld, set your voltage between 18-30 volts, adjust the wire feed to 3-12 meters per minute, and practice on steel. It’s beginner-friendly, ideal for automotive and fabrication work.
What is MIG (Metal Inert Gas Welding)?
MIG, or Metal Inert Gas Welding, is an electric arc welding process that uses a continuous wire feed as an electrode, melting it into the workpiece. It requires an inert gas, usually argon or helium, to shield the weld area from contaminants. MIG welding operates at amperages between 30 to 300 A (Amps), producing high-quality welds on metals like steel and aluminum.
To start, you need a MIG welder, a wire spool, and shielding gas. It’s crucial to adjust settings based on material thickness and type. When I started MIG welding, I spent time fine-tuning the wire speed and voltage; it made a significant difference in my projects. Remember, practice makes perfect when learning to MIG weld!
A colleague found MIG welding useful for tackling challenging tasks. He noted it’s effective for beginners, especially when learning to weld steel. In his words, mastering the basics of MIG welding can open doors to various projects, including welding pipes with MIG. Investing time in resources like MIG welding videos can accelerate your understanding and skills.
Types Of MIG in Context Of How to MIG Weld
What are the types of MIG welding techniques?
-
Gas Metal Arc Welding (GMAW)
GMAW is a popular MIG welding method. Set your welder to a constant voltage, typically between 18-28 volts. Then, connect a shielding gas (Usually Argon or a Mix) to protect the weld from contamination. If you’re aiming to understand the skills needed for sophisticated welding, you might explore what defines a combo welder.
-
Short-circuit MIG Welding
This technique is ideal for thinner metals. Lower the voltage to around 15-20 volts and keep the contact tip close to the base material, almost touching it.
-
Pulsed MIG Welding
Pulsed MIG alternates between high and low current. Set the welder to pulse mode, releasing current in short bursts for better penetration.
-
Flux-cored Arc Welding (FCAW)
FCAW uses a tubular wire filled with flux. You can choose between self-shielding (No Gas) or gas-shielded. Adjust your welder settings accordingly, usually between 18-26 volts.
-
Spray Transfer MIG Welding
This advanced technique is effective for thick materials. Use higher voltage (Around 26-30 Volts) and a shielding gas for a smooth, high-quality weld.
So far we covered the various types of MIG welding. Next, let’s look at the necessary prerequisites for MIG welding.
Prerequisites: What Do You Need
What do you need to start MIG welding?
- MIG Welder: You’ll need a MIG welder, like the Hobart Handler 140. It’s essential for high-quality welds.
- MIG Wire: Get solid MIG wire such as ER70S-6 in 0.030 inches (0.762 Mm). This gauge is crucial for strong welds on steel.
- Shielding Gas: Use a mix of 75% argon and 25% CO2 gas, typically sold in 20 lb (9 Kg) tanks. This mix protects your weld from contamination.
- Gas Regulator: You’ll need a regulator, such as the Smith Equipment 301, on your tank. It controls gas flow and is critical for safety.
- Welding Cart: A sturdy cart like the Pro-HD model helps you maneuver your gear easily. It keeps everything organized and ensures safety.
We covered the necessary requirements for MIG welding here. Next, we will cover the steps for MIG welding.
Steps for How to MIG Weld
Here are steps for MIG welding to help you succeed.
-
Gather Necessary Equipment
Get your MIG welder ready. Ensure you have a power source, gas supply, and suitable filler wire. Check the spool size; 0.030 in (0.76 Mm) wire is great for general welding. Don’t forget your personal protective equipment (PPE), like gloves and a welding helmet! A clear understanding of welding equipment can be vital, especially when exploring options like inverter welders and their benefits.
Work with a clean setup. A good connection can make or break your welds. Ensure your welder is well-maintained; a dirty tip can lead to poor results. You’ll thank yourself later for any prep work you do now!
-
Prepare Your Workspace
Clear a flat, secure area to work. Ensure good ventilation, especially if you’re welding coated metals. Use a fire-retardant surface for safety. Setting up a workbench to hold your project materials is also helpful!
Keeping my workspace tidy taught me valuable lessons. Clutter can lead to accidents. Ensure tools and materials are within arm’s reach to avoid unnecessary movement while welding. It’ll help you stay focused and efficient!
-
Select the Right Material
Choose the right metals to weld. Most beginners start with mild steel; it’s forgiving and popular. Ensure your materials are clean and free of rust or dirt, as this affects bonding. Remember, thicker metal requires more power!
Practicing with mild steel was a game changer for me. For thin materials, reduce the amperage to prevent burn-through. By understanding material thickness, you’ll have much better control over the weld pool!
-
Set Up Your MIG Welder
Connect the gun to the welder and set your spool correctly based on wire size. Input your wire diameter and project thickness to adjust the power settings. Typically, use 18-24 volts, depending on your metal’s gauge.
Double-check connections; loose wires can cause inconsistent welds. Perform a quick test run on scrap material before starting. It really helped me find a good rhythm!
-
Adjust the Welding Parameters
Set the wire feed speed to around 200-350 inches per minute for mild steel. Increasing voltage provides deeper penetration. Adjust the gas flow rate to about 20-25 cubic feet per hour (CFH)—too much can cause turbulence!
Every setup is unique, so experiment to find what works best. I kept a notebook of my settings when starting out, so I knew what worked well for future projects, saving time and material!
-
Begin Welding Process
Hold the torch at a 15-20 degree angle before pulling the trigger. Move steadily along the joint—a consistent pace creates even welds. Maintain a distance of around 3/8 inch (9.5 Mm) between the nozzle and workpiece for best results.
Start and stop smoothly; abrupt movements can create defects. A steady hand made a significant difference in my weld quality. Don’t hesitate to take breaks to reset and reassess if needed; practice makes perfect!
We have now covered the steps for MIG welding. Next, we will examine important safety tips.
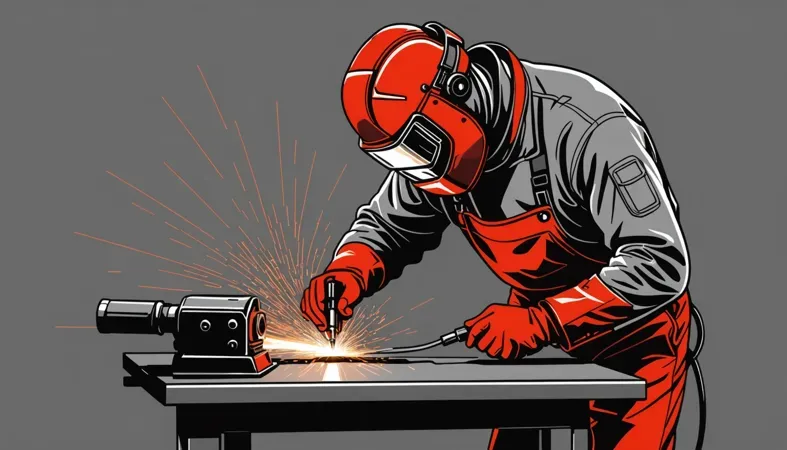
Safety Tips
Let’s explore important safety precautions for MIG welding.
- Welding Helmet: Always wear a helmet to protect your eyes. Consider options like the Lincoln Viking 3350, which has a 1/1/1/1 optical clarity rating. Eye injuries can happen instantly.
- Fire Extinguisher: Keep a Class C fire extinguisher nearby to stop electrical fires before they spread. Fires are unpredictable; be prepared.
- Gloves: Use leather welding gloves. Products like the Miller Electric 907476 are durable and protect against heat. Protecting your skin is crucial to avoid severe burns.
- Ventilation: Ensure good airflow; a fan or open windows reduce harmful fumes. Poor ventilation can lead to serious respiratory issues.
Always prioritize safety, because every precaution counts!
You should now have a good understanding of safety precautions, best practices, and essential equipment. In the next part, we’ll discuss types of MIG welding methods.
Types Of MIG Welding Processes
Let’s look at the types of MIG welding: Gas Shielded MIG, Self-Shielded Flux-Cored, Metal Core MIG, Dual Shielded, and Submerged Arc Welding (SAW).
-
Gas Shielded MIG Welding
This type uses an external gas, usually argon or CO2, to protect the weld from contaminants. It’s ideal for clean, precise welds. It works best on mild steel and aluminum, with a typical wire diameter of 0.025-0.035 inches (0.635-0.889 Mm).
-
Self-shielded Flux-cored Welding
In self-shielded flux-cored MIG, the flux inside the wire generates its own shielding gas when melted. This allows outdoor welding without wind interference. This process is great for quick repairs, especially in construction. To further enhance your welding projects, you might want to explore how to build a bridge rectifier for an AC welder.
-
Metal Core MIG Welding
This method uses a hollow wire filled with metal powder, providing arc stability and low spatter. It’s efficient for high-speed operations. Typically, you’ll use wire diameters of 0.045-0.062 inches (1.14-1.57 Mm) for thicker metals.
-
Dual Shielded MIG Welding
Dual shielded welding combines gas and self-shielding for a strong, stable arc. It’s often used in heavy industries like shipbuilding. This combination improves bead appearance and penetration.
-
Submerged Arc Welding (SAW)
SAW employs a granular flux that covers the arc, preventing contamination. This results in deep penetration and high productivity. It’s commonly used for thick plates, with average welding speeds of 24 inches per minute (610 Mm/min).
Factors Affecting MIG Welding
What factors influence your MIG welding experience?
-
Material Thickness
Thickness ranges from 1/16 inch (1.6 Mm) to over 1 inch (25.4 Mm). Thicker materials require higher heat settings and slower travel speeds for good penetration.
-
Welding Position
Welding can be flat, horizontal, vertical, or overhead. Each position affects control and weld quality, so it’s crucial to practice in various setups.
-
Electrode Diameter
Choosing the right electrode size is vital. Typically, a 0.030 inch (0.8 Mm) diameter electrode works well for thin metals, while 0.045 inch (1.2 Mm) suits thicker materials.
-
Travel Speed
Travel speed determines how fast you move the gun. A speed of 10 to 20 inches per minute (25 to 51 Cm/min) usually yields strong, clean welds. Moving too slowly creates buildup, while moving too quickly results in weak joints.
-
Gas Flow Rate
Use a gas flow rate of 15 to 25 cubic feet per hour (CFH). Proper shielding gas flow protects the weld from contamination. A low flow increases defects, while a high flow causes turbulence.
Common Problems in MIG Welding
When learning how to MIG weld, you might encounter a few common issues that can affect your results.
Problem | Cause | Solution |
---|---|---|
Porosity | Contaminated surface or incorrect gas mix. | Ensure surfaces are clean and use a 75/25 Argon/CO2 mix. |
Burn-Through | Too much heat for thin materials. | Lower voltage and wire speed; use a faster travel speed. |
Inconsistent Bead Appearance | Improper settings or inconsistent travel speed. | Adjust voltage and ensure a steady hand while moving. |
Spatter | Incorrect settings or wire type. | Reduce voltage and use the right diameter wire. |
Undercut | Too fast travel speed or poor technique. | Adjust speed; maintain a correct angle and distance. |
By understanding these common problems and their solutions, you can enhance your MIG welding skills significantly.
Aftercare, Inspection, and Advanced Tips for MIG Welding
Here’s expert advice on aftercare, inspection, and advanced techniques to elevate your MIG welding skills.
Aftercare Tips
After each session, clean your welding gun nozzle to prevent spatter build-up. Use a nozzle cleaner with a diameter of 0.8 mm to remove residue. Store your MIG machine in a cool, dry place, ideally under 30°C (86°F), to protect essential components from overheating.
Inspection
Inspect the gas diffusion cone for signs of abnormal wear every five sessions. Ensure you’re using an argon/CO2 mix at a flow rate of 18-25 cubic feet per hour (Cfh). In my experience, mild steel wire like ER70S-6 consistently provides excellent arc stability.
Expert Tips
I recommend fine-tuning the wire speed and voltage settings for different materials like stainless steel or aluminum. Aim for a voltage range of 17 to 20 volts when welding aluminum less than 3 mm thick. Use specialized push-pull feeding systems for smoother feeding and stronger welds on challenging materials. These adjustments can make a significant difference.
Top Benefits You Can Expect From MIG Welding
The main benefit of MIG welding is its speed. A colleague found it useful for completing projects quickly, saving time and money.
MIG welding also offers several additional benefits. It’s easy to learn, making it ideal for beginners. Its versatility is impressive; you can weld various materials like steel, aluminum, and stainless steel. Plus, you get clean welds with minimal spatter, which means less cleanup. Lastly, it works well in different positions—flat, horizontal, vertical, and overhead—making it a flexible choice for various projects.
Applications Of MIG Welding
I’ve used MIG welding for automotive repairs, but it has many applications, such as:
- Construction: MIG welding joins steel beams for structures. It’s favored for its speed and strength, making it a go-to for builders.
- Aerospace: In this industry, MIG welding fabricates lightweight fuselage components. Precision is crucial, so this method meets high safety standards.
- Robotics: Here, MIG welding assembles frames for robotic arms. The speed and neatness of the welds maintain quality during production.
- Shipbuilding: MIG welding constructs hulls and decks. Its ability to handle thick metals ensures that ships remain sturdy and seaworthy.
Other Options for Achieving Similar Results to MIG Welding
There are several excellent alternatives to achieve results similar to MIG welding. For instance, Gas Tungsten Arc Welding (TIG) allows for precision in thin metals, making it a great choice when quality matters. I’ve often found myself thinking that Submerged Arc Welding provides a high deposition rate, ideal for thick materials.
Then there’s electric Stick Welding, which is versatile and works well outdoors. If you’re looking for a MIG weld without gas, consider using flux-cored wire—it’s great in windy environments. Each method has its strengths, so choose based on your project needs and materials!
Frequently Asked Questions (FAQs)
Now let us look at some common questions I typically get asked about MIG welding.
What Are the Steps to MIG Welding?
The steps to MIG welding include preparing the materials, setting up the welder, and making the weld. Preparation ensures good penetration and a strong joint, while correct settings reduce errors. Each step’s importance can vary by metal type. For instance, you may need to clean steel surfaces to remove contaminants.
Can I Teach Myself to MIG Weld?
Yes, you can teach yourself to MIG weld! Many people start with online tutorials and practice. Warping the metal often occurs during learning, which can be easily fixed by adjusting heat settings or travel speed. You’ll find that practice greatly improves your welding quality.
Do You Push or Drag When MIG Welding?
You generally push the MIG torch while welding, but it can vary with applications. Pushing helps reduce spatter and creates a cleaner bead, while dragging might increase penetration in thicker materials. Knowing when to use each technique is key for a strong, reliable weld.
How Easy is It to Use a MIG Welder for Beginners?
Using a MIG welder is relatively easy for beginners! The machine’s setup and controls are straightforward, making it user-friendly. Studies show beginners can become proficient within a few hours of practice, often producing acceptable welds much quicker than with other welding processes.
How Do You Choose the Right Wire for MIG Welding?
Choosing the right wire for MIG welding depends on the material and joint type. Common wire sizes range from 0.8 mm (0.030 In) to 1.0 mm (0.040 In) for typical applications. For instance, aluminum wire is best for aluminum; carbon steel wire is preferred for steel welding.
What Safety Gear Do I Need for MIG Welding?
You need specific safety gear for MIG welding to protect yourself. At minimum, a welding helmet, gloves, and protective clothing are essential. The helmet should have a shade of at least 10, which helps block harmful UV rays and keeps your eyes safe.
Conclusion
I hope this gave you what you needed on how to MIG weld. We covered MIG welding basics, types of MIG processes, prerequisites for setup, necessary equipment, safety tips, steps to follow, influencing factors, common issues, aftercare, and benefits. We also discussed various applications and other welding options to achieve similar results.
To wrap it up, learning how to MIG weld means knowing how to set up your machine, choose the right wire, and follow safety rules. Remember, practice makes perfect, so start with scrap metal before moving to your project. Happy welding!
If you’re eager to explore more resources, check out what What is Welding has to offer you.
References
- American Welding Society. (2020). AWS Welding Handbook: Welding Science and Technology (Vol. 1). Miami, FL: AWS.
- Howard B. Cary. (1997). Welding Manual. Upper Saddle River, NJ: Prentice Hall.
Tyler is a passionate DIY welder and self-taught metal artist with years of hands-on experience transforming raw materials into functional and artistic creations. Specializing in MIG welding, Tyler crafts everything from custom furniture to outdoor sculptures, blending creativity with technical skill. Committed to making welding accessible, Tyler shares practical insights and project inspiration to help beginners and hobbyists confidently explore the world of metalworking.
American Welding Society, Beginner Welding, MIG Welding, Safety Tips, Welding, Welding Equipment, Welding Process, Welding Techniques