What Causes Weld Spatter? Understanding Spatter Types, Reduction Steps, and Common Issues
Published on: November 16, 2024 | Last modified: March 4, 2025
By: Mark Carter
So, what is spatter? It’s tiny droplets of molten metal that splatter during welding. This phenomenon can make a mess and ruin your work if you’re not careful.
One thing that’s regularly asked of me is what causes weld spatter? It’s crucial to know because spatter can affect the strength and appearance of your welds. I’ve seen beginners struggle with spatter ruining perfectly good projects, so understanding its causes can save you time and frustration.
In this article, we’ll cover what causes weld spatter, how it works, types of spatter, steps for reducing it, factors that affect it, common issues you might encounter, aftercare and inspection, real-world uses for managing spatter, and some options for controlling it. Let’s dive into the nitty-gritty of dealing with what is spatter in welding!
Contents
- What Causes Weld Spatter?
- What is Weld Spatter?
- Types Of Spatter
- Steps for Reducing Weld Spatter
- What Could Go Wrong: Common Issues
- Factors Affecting Weld Spatter
- Weld Spatter and its Influence on Weld Integrity
- Real-world Uses for Weld Spatter Management
- Other Options for Controlling Weld Spatter
- Frequently Asked Questions (FAQs)
- Conclusion
- Additional Reading
What Causes Weld Spatter?
Weld spatter happens due to molten metal droplets flying from the weld pool. It often occurs from improper settings or materials. You’ll see spatter in MIG and TIG welding, and managing it ensures a cleaner finish and better performance.
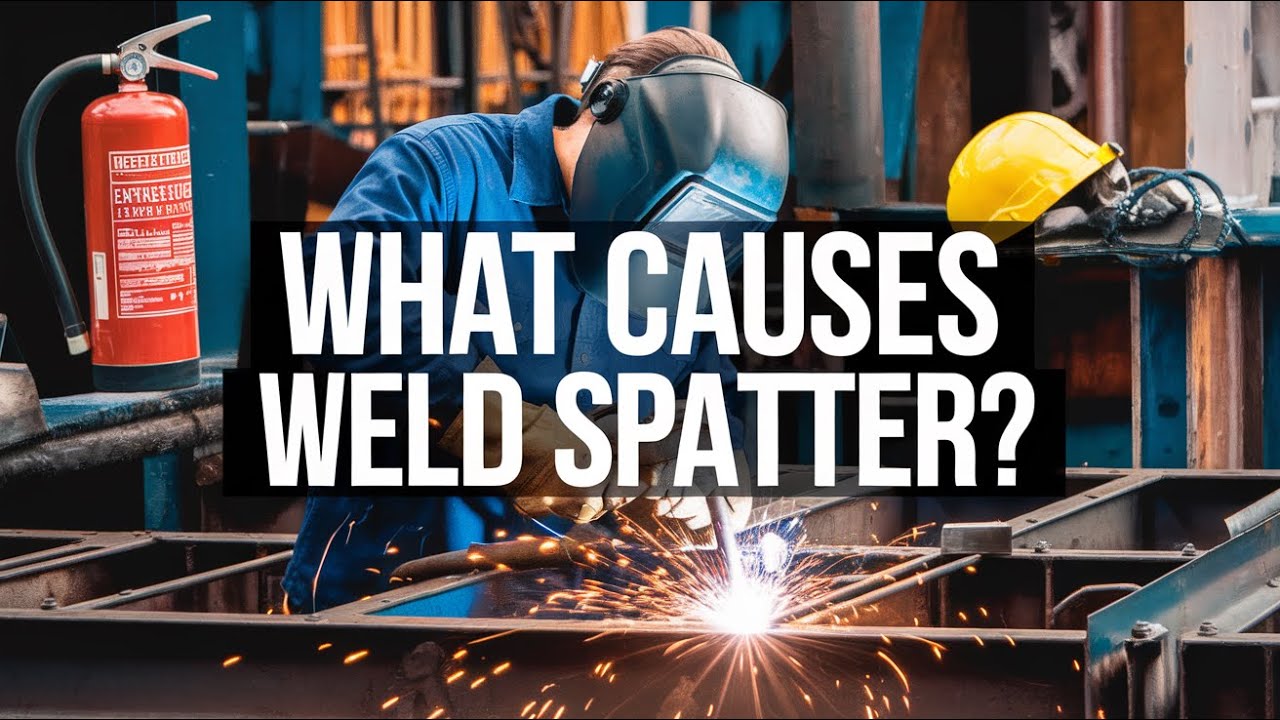
What is Weld Spatter?
Weld spatter refers to small droplets of molten metal ejected from the weld pool during welding. This often occurs due to high arc temperatures, which can exceed 3,500°C (6,332°F). The welding current provides energy to heat the metal. If the current is too high, the arc can’t control the weld pool, resulting in spatter—typically, 2 to 5% of the total filler metal used may turn into spatter.
Spatter isn’t just a minor annoyance; it can affect weld quality. Factors like inconsistent wire feed speed or incorrect inter-electrode distance can worsen the issue. You may experience more spatter when MIG welding compared to TIG welding due to the different arcs involved.
As a welder, I’ve seen plenty of spatter over the years! When I switched to a more consistent wire feed speed, my spatter problems improved dramatically. If you’re wondering what causes weld spatter, remember that an optimal setup can significantly reduce it—ideal for achieving cleaner welds!
Types Of Spatter
What types of spatter might you encounter in welding?
-
Metal Transfer Spatter
This type occurs when molten metal transfers from the electrode to the workpiece. High current settings can increase this spatter. To minimize it, use the correct wire feed speed and maintain a proper arc length.
-
Arc Stability Spatter
This spatter arises from unstable arcs that cause erratic metal transfer. An unstable voltage usually leads to this issue. To achieve a stable arc, keep the ground clean and adjust your welding parameters, like voltage and speed, as needed.
For those interested in detailed applications of welding positions, exploring the intricacies of 3G welding techniques can be useful.
-
Heat Input Spatter
Heat input spatter occurs when excessive heat melts the base material too quickly, creating more molten droplets. To control this, ensure proper travel speed and adjust heat settings on your welder.
-
Shielding Gas Spatter
This spatter happens when shielding gas is insufficient or improperly applied. Incomplete gas coverage can lead to spatter during welding. To prevent this, check your gas flow rate and use the appropriate gas type for your material. Understanding the causes of weld spatter is essential for improving the quality of your welds.
-
Welding Technique Spatter
Your welding technique can also affect spatter. Poor technique, such as incorrect angles, can cause more spatter. To improve, practice the proper torch hold and travel angles for a cleaner weld. If you encounter welding spatter on glass, it’s crucial to know how to fix it effectively.
So far we covered different forms of weld spatter. Next, let’s look at ways to minimize spatter during welding.
Steps for Reducing Weld Spatter
Let’s cover steps to minimize spatter during welding. Each step addresses key factors that cause spattering.
-
Choose the Right Electrode
Select the appropriate electrode for your welding process. For MIG welding, use ER70S-6 for general steel types, and for TIG, use 308L for stainless steel. Using the wrong electrode can reduce arc stability and increase spatter. This simple change can significantly cut down unwanted spatter. Understanding these principles is essential for efficiently handling a multi-process welder.
-
Adjust the Welding Parameters
Set the voltage and wire feed speed correctly. For MIG, aim for 23-26 volts with a feed speed of 300-400 inches per minute (7.62-10.2 M/min). Ensure the amperage ranges between 200 and 250 amps for thicker materials. Tweaking these settings can make the difference between smooth beads and excessive splatter.
-
Maintain a Steady Travel Speed
Move at a consistent speed while welding. Moving too fast results in undercut; moving too slow leads to pooling and spatter. Aim for a travel speed of about 10 to 12 inches per minute (25.4-30.48 Cm/min). For more insights on maintaining proper technique, see our comprehensive welding guidance. Slowing down my speed helped me reduce spatter significantly.
For those exploring advanced welding techniques, understanding what SAW welding involves can be beneficial.
-
Optimize the Work Angle
Adjust your work angle for better control of the puddle. Stick welding benefits from a 15 to 20-degree angle. For MIG, try a 10 to 15-degree push angle to direct heat and minimize spatter. A good angle can help manage the molten metal’s behavior—don’t overlook it!
-
Control the Heat Input
Monitor heat input closely to prevent overheating. Keep heat input below 1.0 kJ/mm. For instance, when welding 3/16 inch (4.76 Mm) steel, too much heat can cause excessive spatter. Finding the right balance takes practice, but controlling heat is key to producing clean welds.
Choosing the right eyewear can enhance precision, and it’s worth knowing if welding with prescription glasses is a viable option for those who wear them.
You should now have a good understanding of methods to minimize weld spatter. In the next part, we’ll discuss potential problems.
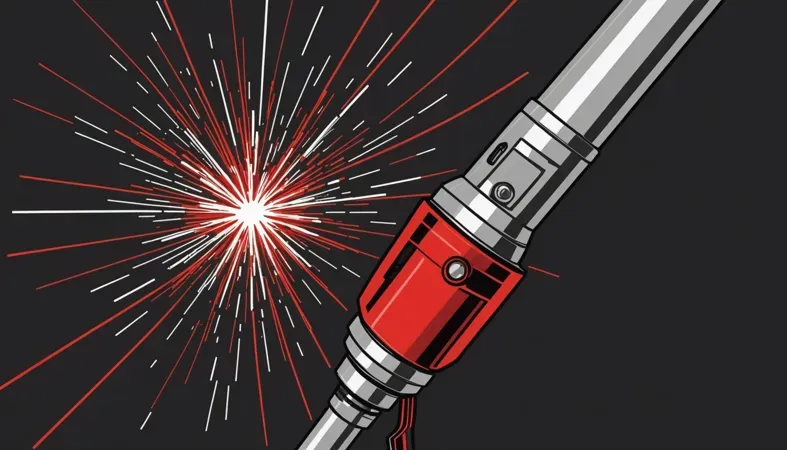
What Could Go Wrong: Common Issues
Let’s examine the unique issues related to spatter in welding.
-
Inconsistent Weld Quality
Spatter can lead to inconsistent weld quality. Look for irregular bead shapes or weak spots. Resolve this by adjusting your arc length and travel speed; aim for an arc length of 1/16 to 1/8 inch (1.5 To 3 Mm). To effectively control these parameters, consider exploring the benefits of a DC inverter welding machine.
-
Excessive Cleanup Requirements
Spatter often creates a messy work area. Cleanup isn’t fun. Use a MIG welder with the proper settings and minimize distance to reduce unwanted spatter.
-
Increased Welding Defects
Spatter often increases welding defects, like lack of fusion. Detect this by visually examining finished welds. To resolve it, adjust the speed and voltage; maintain a voltage of 20-30 volts.
-
Negative Impact on Appearance
Spatter spoils the appearance of your welds. Check for excessive beads. Maintain a steady hand and correct settings—focusing on technique can help a lot.
-
Heat-affected Zone Concerns
Spatter contributes to unwanted overheating in the heat-affected zone (HAZ). Monitor the temperature; keep it below 200 °C (392 °F). To fix this, reduce heat settings and improve cooling methods.
So far we covered potential problems encountered during the process. Next, let’s look at elements influencing weld spatter.
Factors Affecting Weld Spatter
What factors lead to weld spatter issues? Here’s a quick overview.
-
Welding Current Levels
High current levels can increase arc instability, resulting in more weld spatter. For example, using 250 amps tends to create more spatter than 150 amps due to hotter, less controlled arcs.
-
Electrode Type and Diameter
The type and diameter of the electrode significantly impact spatter. A larger 1/8-inch (3.175 Mm) electrode may cause excessive molten material droplets, increasing spatter compared to a smaller 1/16-inch (1.588 Mm) electrode.
-
Base Material Properties
The cleanliness of the base metal matters. Dirty surfaces produce more spatter as impurities melt into the weld pool. Different alloys also react uniquely; for example, aluminum often leads to black soot, affecting overall spatter levels.
-
Welding Speed Variations
Welding speed significantly alters spatter levels. Slow speeds can cause overheating, leading to excess splatter, while speeds that are too fast may starve the weld pool, creating suboptimal conditions. To enhance your understanding of welding techniques, refer to the guidelines on reading welding blueprints.
-
Shielding Gas Composition
The type and mixture of shielding gas play a crucial role in controlling spatter. Using pure argon for TIG welding can reduce spatter compared to a 75/25 argon/CO2 mix in MIG welding, where spatter is more prevalent.
We have now covered the elements influencing weld spatter. Next, we will examine the impact of spatter on weld integrity.
Weld Spatter and its Influence on Weld Integrity
Understanding how weld spatter impacts weld integrity is critical for anyone involved in welding.
How Spatter Affects Strength and Durability
Weld spatter can significantly weaken the final weld. Here’s how:
- Surface Defects: Spatter creates irregularities that can trap impurities. These imperfections lead to weak points in the weld.
- Porosity: Excessive spatter may cause gas pockets. According to studies, 30% of weld defects arise from porosity, affecting the weld’s strength.
- Heat-Affected Zone (HAZ): Spatter can increase the temperature in the heat-affected zone, leading to reduced toughness and brittleness. Maintaining HAZ temperatures under 200 °C (392 °F) helps mitigate this issue.
Impact on Aesthetic Quality
Spatter also affects the visual quality of welds. Aesthetic degradation can lead to rework or rejection from clients, especially in industries demanding high visuals.
Table of Weld Spatter Effects
Effect | Potential Damage | Mitigation Strategy |
---|---|---|
Surface Defects | Weaker welds due to trapped impurities | Regular cleaning, optimal settings |
Porosity | Gas pockets reducing strength | Control arc stability and gas flow |
HAZ Damage | Brittleness and reduced toughness | Monitor heat input and cooling rates |
Real-world Uses for Weld Spatter Management
I’ve seen folks manage weld spatter in many ways, but there are several practical applications:
- Cleaning Automotive Components: In auto repair, minimizing spatter ensures cleaner welds on components like frames and panels, enhancing aesthetics and safety.
- Precision Aerospace Welding: In the aerospace industry, controlling spatter is critical. Clean welds ensure safety, and reducing spatter meets strict weight standards.
- Construction Equipment Manufacturing: For fabricating heavy machinery like bulldozers, managing spatter prevents defects. It’s a common practice to uphold high-quality standards.
- Pipe Welding in Oil Refineries: In oil and gas pipelines, excess spatter can compromise integrity. Using spatter-reduction techniques is vital for structural strength and reliability.
Other Options for Controlling Weld Spatter
When you’re tackling spatter, consider switching to flux-cored wire. Products like Lincoln Electric’s Innershield® wires not only reduce spatter but also enhance penetration. In cases where clean-up is crucial, using anti-spatter spray, such as ABICOR BINZEL’s anti-spatter gel, can also help minimize mess.
Additionally, adjust your settings! Lowering the voltage or increasing travel speed can make a significant difference. Such tweaks may result in less spatter without compromising strength. Having navigated similar challenges myself, I can vouch for these methods in keeping your projects neat and efficient.
Frequently Asked Questions (FAQs)
Now let us look at some common questions I typically get asked.
How Do You Stop Welding Spatter?
To stop welding spatter, you should adjust your welding parameters correctly. Proper voltage, amperage, and travel speed can reduce spatter by up to 50%, improving your weld quality. Regularly cleaning your work area also helps minimize contaminants that can contribute to spatter.
Why Am I Getting So Much Weld Spatter?
You may be getting so much weld spatter due to incorrect settings or poor technique. High voltage or low travel speed often leads to excessive spatter, increasing your cleaning time by as much as 60%. So, keep a close eye on your settings!
What is the Main Cause Of Spatter?
The main cause of spatter is improper arc length. When the arc is too long, it generates more heat and, consequently, more molten metal droplets, increasing spatter. Reducing your arc length by just a few millimeters can significantly diminish the amount of spatter.
Is Weld Spatter a Defect?
Yes, weld spatter is generally considered a defect. While it may not compromise the structural integrity of a weld, spatter can lead to poor aesthetics and require extra cleanup work. In some industries, excessive spatter might even result in rejection of the part.
What Causes Black Soot When TIG Welding Aluminum?
Black soot when TIG welding aluminum is caused by oxidation and contamination. If the surface isn’t cleaned, foreign materials smolder during welding, leading to soot. Always use a proper cleaning method like a wire brush or chemical cleaner to prepare your aluminum before welding.
Conclusion
We are almost done. We covered what causes weld spatter, how it works, types of spatter, steps for reducing spatter, factors affecting spatter, common issues, aftercare tips, real-world uses, and options for controlling it. Lastly, we touched on frequently asked questions about this topic.
In summary, weld spatter occurs from several factors like heat settings, material types, and welding techniques. Basically, the heat causes molten metal to fly off, creating that messy spatter. So, to keep it down, manipulate voltage, wire feed speed, and use proper aftercare techniques.
For more insights and resources on welding, feel free to visit our homepage at What is Welding.
Additional Reading
- American Society of Mechanical Engineers. (2019). ASME Section IX: Welding and Brazing Qualifications. New York, NY: ASME.
- International Institute of Welding (IIW): https://www.iiwelding.org
- Kou, S. (2003). Welding Metallurgy (2nd ed.). Hoboken, NJ: Wiley.
Mark is a skilled welding engineer specializing in advanced metal joining technologies and process design. With a formal education in welding engineering and a background rooted in practical experience, Mark bridges the gap between theory and application. He is passionate about making technical concepts accessible, empowering welders to embrace innovation while mastering essential skills. Mark combines his scientific expertise with a commitment to supporting the welding community alongside his uncle, Joe.
MIG Welding, Pipe Welding, Spatter Reduction, Structural Integrity, Weld Spatter, Welding, Welding Quality, Welding Safety, Welding Techniques