How to Weld With a MIG Welder? Steps, Benefits, and Tips
Published on: November 27, 2024 | Last modified: March 4, 2025
By: Joe Carter
I get asked quite often about how to weld with a mig welder. Knowing the right techniques is key to getting solid welds. In my experience, following proper steps minimizes mistakes and creates better results.
In this guide, you’ll learn about the MIG welder, the different types of MIG welders, necessary prerequisites, steps for welding, safety precautions, common issues you might face, aftercare tips, and industry uses. Plus, we’ll touch on advantages and alternatives, so you’ll have a complete overview of how to use a mig welder.
Contents
- How to Weld With A Mig Welder?
- What is a MIG Welder?
- Types Of MIG Welders
- Prerequisites
- Steps for Welding With a MIG Welder
- Precautions
- Types Of MIG Welding Processes
- Factors Affecting MIG Welding
- Common Issues You Might Encounter
- Aftercare, Inspection, and Advanced Tips for MIG Welding
- Key Benefits Of MIG Welding
- Industry Uses Of MIG Welding
- Alternatives for Welding With a MIG Welder
- Frequently Asked Questions (FAQs)
- Conclusion
- References
How to Weld With A Mig Welder?
A MIG welder, short for Metal Inert Gas welder, provides a strong, easy way to fuse metals. To weld, set your machine to the material’s gauge, feed the wire automatically, and maintain a steady arc. It’s beginner-friendly, ideal for craft projects or automotive repairs.
What is a MIG Welder?
A MIG welder, short for Metal Inert Gas welder, is a welding machine that uses a continuous wire feed. The wire, typically made from solid metal, melts when an electrical arc is created. It can weld materials like steel, aluminum, and copper alloys, with thicknesses ranging from 0.6 mm (0.024 In) to over 12.7 mm (0.500 In).
When you’re ready to weld with a MIG welder, the process is straightforward. Feed the wire into the welder, set your power level, and start the arc. In my experience, adjusting the wire speed to match the thickness of the metal significantly improves weld quality.
A friend of mine used it to craft custom metal sculptures. He believes that learning to use a MIG welder enhanced his skills. By watching welding videos, he picked up essential techniques to tackle any project, including how to weld effectively with a MIG welder.
Types Of MIG Welders
-
Gas Metal Arc Welders
Gas metal arc welders use a continuous wire feed to join metals. Set your voltage and wire speed based on the material’s thickness. To achieve a solid weld, start the arc and move steadily, adjusting your speed according to the weld puddle’s appearance.
-
Inverter MIG Welders
Inverter MIG welders are lightweight and efficient, utilizing advanced technology to optimize power. Adjust the settings for your material and wire size. Maintain an optimal distance (About 1/4 Inch or 6 Mm) between the tip and workpiece while moving at a consistent pace. A basic understanding of the components required for a semiautomatic welding system can enhance overall welding performance. For more information, explore what items make up a basic semiautomatic welding system.
-
Multi-process Welders
Multi-process welders handle MIG, TIG, and stick welding, offering versatility for various projects. Select MIG mode on your welder. Follow the specific gas and wire recommendations based on your material, ensuring you set the right amperage and voltage.
-
Industrial MIG Welders
Industrial MIG welders are designed for heavy-duty projects, providing robust performance and high duty cycles. Set the machine’s power levels to match the material’s requirements. Maintain a steady hand and ensure a clean work area to avoid joint contamination.
-
Portable MIG Welders
Portable MIG welders are compact, ideal for light to moderate tasks, and perfect for DIY and on-site work. Check the gas supply and set your welding parameters. Keep your machine stable while moving the nozzle smoothly along the joint for an even bead.
So far we covered the different types of MIG welders. Next, let’s look at what you need before starting.
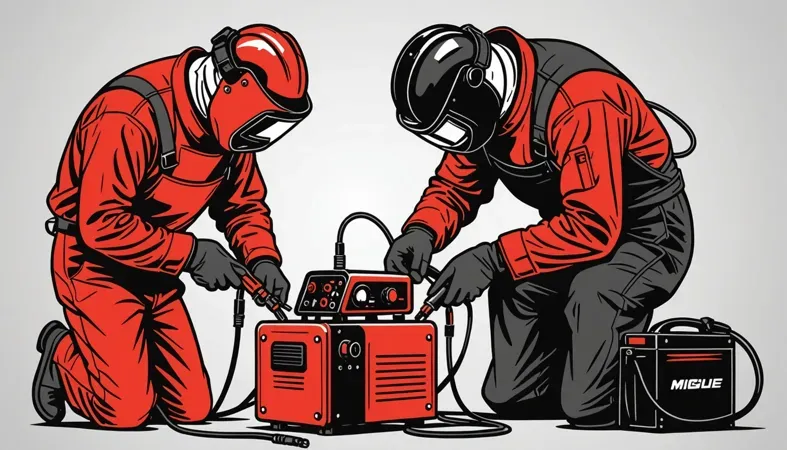
Prerequisites
What do you need to get started?
- MIG Welder: You’ll need a MIG welder, like the Lincoln Electric Easy MIG 180. It’s essential for providing the right power and efficiency for various materials.
- Welding Wire: You’ll need .030 inch (0.76 Mm) diameter ER70S-6 welding wire for mild steel. It ensures a strong weld joint.
- Shielding Gas: A gas cylinder with an Argon mix, e.g., 75% Argon and 25% CO2, is vital for protecting the weld and preventing oxidation.
- Welding Cart: An adjustable welding cart, like the Harbor Freight Welding Cart, provides a sturdy place for your welder and supplies, keeping everything organized and accessible.
- Chipping Hammer: You’ll need a chipping hammer, such as the Forney 70356, to remove slag. It’s crucial for achieving a clean, polished finish on your welds.
So far we covered the requirements for welding. Next, let’s look at the process for using a MIG welder.
Steps for Welding With a MIG Welder
Here are the essential steps to effectively use a MIG welder.
-
Adjust the Welder Settings
Start by setting the voltage and wire feed speed on your MIG welder. Refer to the material thickness; for example, for 18-gauge steel (1.2 Mm), set the voltage to 18-20 volts and the wire feed speed to about 4-6 inches per minute (100-150 Mm/min). Each material type may require slight adjustments, so experiment as needed. The right settings can make the difference between a clean weld and a messy one! From experience, fine-tuning these settings first saves time later. Always check the manufacturer’s guide for recommended settings; it speeds things up significantly. For aluminum, increase the feed speed and lower the voltage for a clean weld. Ensuring you know how to properly hook up a Miller suitcase welder can enhance your welding technique by providing consistent settings.
-
Set Up the Workpiece
Position your workpiece securely on a flat surface. Use clamps to hold everything tight to prevent movement during welding. For thicker metals, maintain at least a 1/4 inch (6 Mm) gap for proper penetration. A solid hold makes a difference in tight welds and avoids messy, uneven spots.
You might not realize how crucial a good setup is until you see a clean bead versus a poor one! Think of it as building a strong foundation—your welds are only as good as how you secure the piece. To reduce aggressive movements, use a table or vise to stabilize your material.
-
Initiate the Welding Process
Pull the trigger to start the arc, keeping the nozzle about 1/4 inch (6 mm) above the workpiece. Move steadily and smoothly in the desired direction. Maintain a consistent speed; starting too quickly or slowing down mid-pass can ruin your weld. A steady pace is key; the best results come from planning your movements. Start with a short test weld to fine-tune your technique. Remember, it’s like learning to ride a bike; it takes practice! Always travel in a straight line, whether moving left to right or vice versa. Circular movements can make it hard to maintain a uniform weld with good penetration. When welding, understanding how to handle weld flash issues is vital for safety and success.
-
Complete the Weld and Inspect
Once you’re done, release the trigger and let the weld cool. Examine the bead; a good weld should look consistent, smooth, and free of cracks. If you see spatter or gaps, adjust your technique or welder settings. You want a strong connection with an elegant finish!Inspect your work closely for any issues. Small flaws can turn into big repairs later. I often flip the piece to assess the underside—as that’s where weaknesses often hide! The goal is a clean bead that’s both aesthetically pleasing and structurally sound.
We covered steps for using a MIG welder. Next, we will discuss important safety precautions.
Precautions
Let’s review essential safety tips critical for your success.
- Wear Appropriate Gear: Use protective gloves and a welding helmet to shield against sparks. Brands like Lincoln or Miller offer quality options that protect you from burns and eye damage.
- Ensure Proper Ventilation: Welding fumes can be harmful. Always work in open spaces or use exhaust fans, maintaining at least 1.5 meters (5 Feet) of clearance.
- Check Equipment Regularly: Inspect hoses and connections for wear to prevent leaks. A Weld-Spider (Tool for Pressure Testing) can help identify issues.
- Be Mindful of Fire Hazards: Remove flammable materials at least 3 meters (10 Feet) away. Items like paper or acetylene tanks are highly risky and can ignite.
Safety precautions are crucial—I learned that the hard way! Don’t skip them.
That covers precautions for MIG welding. Let’s now take a look at the various types of MIG welding processes.
Types Of MIG Welding Processes
Let’s look at different types of MIG welding: Short-Circuiting, Spray Transfer, Pulsed, Flux-Cored, and Dual-Shielded.
-
Short-circuiting MIG Welding
Short-circuiting, or ‘dip transfer,’ uses low amperage (50 to 150 A) to create a molten puddle. The wire electrode touches the puddle, forming a short circuit. It’s ideal for thin materials like sheet metal and allows for welding in all positions!
-
Spray Transfer MIG Welding
This technique needs higher amperage (180 to 250 A) and employs a fine, stable arc to spray molten metal droplets. It’s suitable for thicker materials (Over 3.2 Mm or 1/8 Inch). Spray transfer results in a smoother finish but is less effective in windy conditions. Ensure good gas shielding while using it!
-
Pulsed MIG Welding
Pulsed MIG welding alternates between high and low current to control heat and manage weld penetration. It’s often used on thicker materials or in positions that require better control. It produces less spatter and improves overall appearance! For those exploring advanced welding equipment, understanding how much a laser welder costs can be quite beneficial.
-
Flux-cored MIG Welding
This type uses tubular wire filled with flux, allowing for outdoor welding without much wind interference. The process can be self-shielded or gas-shielded, increasing its versatility, especially for thick sections.
-
Dual-shielded MIG Welding
In this method, both flux-cored wire and a shielding gas are used. It’s a hybrid approach that enhances weld quality, resulting in better penetration and a smooth finish, making it perfect for thick materials.
Factors Affecting MIG Welding
What factors determine your success with a MIG welder?
-
Wire Diameter
The wire diameter affects the thickness of the material you can weld. A common choice is 0.030 inches (0.76 Mm) for materials up to 1/4 inch (6.35 Mm) thick.
-
Gas Flow Rate
Setting the correct gas flow rate is crucial to prevent contamination. A flow rate of 20-25 cubic feet per hour (Cfh) works well for most applications.
-
Amperage Settings
Amperage affects the heat of your weld. A good guideline is about 1 amp for every 1 thousandth of an inch of material thickness. For 1/8 inch (3.18 Mm) metal, set it to around 80 amps.
-
Travel Speed
Your travel speed should match your amperage setting and material. Moving too fast creates weak welds; moving too slow can burn through. A good speed is about 10-15 inches per minute (25-38 Cm/min).
-
Joint Design
The joint type also affects how well your weld holds. For example, a groove joint may need more penetration than a lap joint, impacting your technique and settings.
Common Issues You Might Encounter
Let’s look at some common issues with a MIG welder.
-
Poor Penetration
Poor penetration occurs when the weld doesn’t soak into the base metal. Check your settings. Increase the voltage if necessary, aiming for an arc length of about 3/8 in (9-10 Mm).
-
Excessive Spatter
Excessive spatter might occur when using a MIG welder. If so, consider adjusting the wire feed speed to lower levels without sacrificing your travel speed.
-
Burn-through
Burn-through can create weak joints. Identify thin materials and reduce the heat or move faster to avoid damage.
-
Wire Feeding Problems
Your MIG welder may face feeding issues due to tangling or kinked wire. Inspect the spool, straighten the wire, and ensure proper tension on the drive roll.
-
Inconsistent Weld Bead
Inconsistency in the weld bead often results from user technique. Maintain a steady travel speed of 10-12 inches per minute (25-30 Cm/min) for even distribution.
Aftercare, Inspection, and Advanced Tips for MIG Welding
Here’s some great advice to keep your MIG welder and projects in top shape!
Aftercare Steps
After welding, clean your MIG welder regularly. Use a soft cloth with mild cleaners to remove dust and debris. For the nozzle, dip a wire brush in your cleaning solution and clean it every 15 welding hours for optimal performance. Combo welders perform multiple welding techniques, making them versatile for many applications, so ensure proper maintenance for reliable service over time by understanding what is a combo welder.
Inspection Items
Inspect your MIG machine regularly. Check the gas lines for leaks with a bubble solution monthly. I use a tool like the Miller M-25 series, which provides thorough inspection and operates under high heat with up to 30 g/min of gas flow. Ensure your wire feeder is aligned correctly to avoid jams.
Expert Tips
Maximize efficiency by setting your voltage no higher than 3.5 V for 0.030-inch (0.76-mm) wire. Preheat thicker metals over 1/4 inch (6.35 Mm) to around 150°F (65°C) to reduce warping. Adjust your travel speed; for solid wire, aim for 15-20 inches/min (38-51 Cm/min) for well-penetrated welds.
Key Benefits Of MIG Welding
The MIG welder stands out for its speed and ease of use. A friend used it for a car repair and finished in half the time compared to stick welding.
Moreover, MIG welding offers versatility, allowing you to weld various materials, including aluminum and steel. It produces clean welds with minimal spatter, reduces cleanup, and is less tiring for long projects. Plus, it’s great for both beginners and experienced welders!
Industry Uses Of MIG Welding
I’ve seen people use MIG welders for everything from car repair to heavy machinery. However, it has unique applications such as:
- Automotive Repair: MIG welding is ideal for bodywork and frame repairs. It’s quickly becoming the preferred method for its speed and strength, popular among mechanics.
- Furniture Manufacturing: Many artists and manufacturers use MIG welders to create metal furniture. It allows for clean welds on intricate designs, making it a favored choice in the industry.
- Pipelines: MIG welding is essential for oil and gas pipelines due to its ability to handle thick metal. Its efficiency and durability make it widely used in such projects.
- Construction: Steel structures often benefit from MIG welding. Its ability to weld quickly makes it the preferred method during new builds, ensuring strong connections.
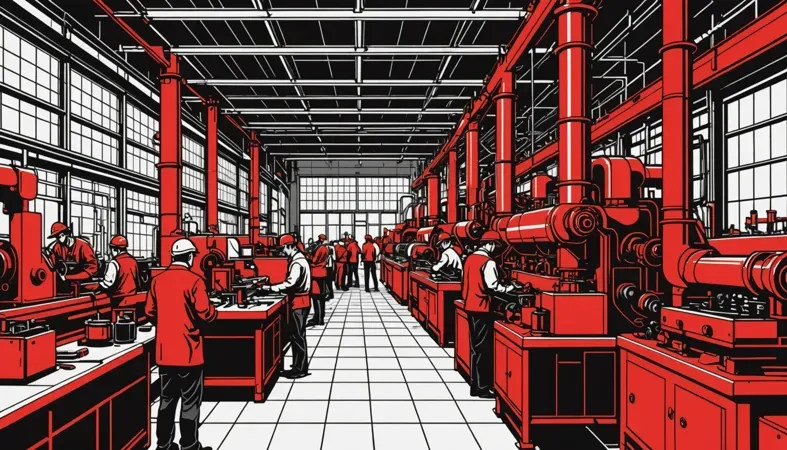
Alternatives for Welding With a MIG Welder
There are several alternatives that can achieve similar results to using a MIG welder. For example, Gas Tungsten Arc Welding (TIG) is excellent for thin metals, offering more precision. You might prefer it when working on projects requiring clean, quality welds, such as art pieces or bicycle frames. Over time, I’ve observed that many hobbyists often turn to TIG for its control, especially in sensitive settings.
Another option is Submerged Arc Welding (SAW), which excels in heavy-duty applications. This technique’s great for large metal sheets and thick materials. While MIG is versatile, SAW’s ability to produce deep, consistent welds makes it a perfect choice for industrial environments. It’s all about the tool that best fits your project’s needs!
Frequently Asked Questions (FAQs)
Now let us look at some common questions I typically get asked.
What is the Most Common Mistake When MIG Welding?
The most common mistake when MIG welding is using the wrong wire feed speed. This error leads to poor penetration and weak welds. Typically, ideal wire feed speeds range from 2.5 to 15 meters per minute (8.2 To 49 Feet Per Minute), depending on the material thickness.
Can You Teach Yourself to MIG Weld?
Yes, you can teach yourself to MIG weld. Many hobbyists and professionals have successfully learned the process through online tutorials and practice. Making use of abundant resources like YouTube can greatly speed up your learning curve while saving you up to 80% on formal training costs.
How Do You Use a MIG Welder Step by Step?
To use a MIG welder, start by setting the voltage and wire feed speed based on your material. Next, place the welder gun at a 15-degree angle. Maintain a movement speed of about 5 centimeters per second (2 Inches Per Second) for good bead appearance. Each step can significantly impact the weld’s quality.
What Does MIG Stand for?
MIG stands for Metal Inert Gas. This welding method uses an inert gas, like argon, to protect the weld pool from contamination. The process helps achieve cleaner welds, and studies show it provides 30% less spatter compared to other welding techniques.
How Thick Can You Weld With a MIG Welder?
With a MIG welder, you can weld materials up to 12.7 millimeters (0.5 Inches) thick effectively. But remember, the specific capabilities depend on the welder’s amperage and the selected wire type. Adjusting settings for different materials ensures quality welds.
Conclusion
We are almost done. We covered what a MIG welder is, different types of MIG welders, prerequisites for welding, steps for proper welding, precautions to keep in mind, various MIG welding processes, factors that affect the weld, and common issues you might encounter. We also discussed aftercare, inspection, advanced tips, key benefits, industry uses, and alternatives for welding.
To sum it up, knowing how to weld with a MIG welder involves understanding its functions and methods. You need to set it up right, choose the correct settings, and follow the step-by-step processes we talked about. I hope these welding tips prove valuable to you in mastering how to use a MIG welder effectively and safely.
If you’re eager to further expand your knowledge on welding, feel free to check out more resources at What is Welding.
References
- Little, R. L. (1999). Welding and Welding Technology. New York, NY: McGraw-Hill Education.
Joe Carter is a retired welding professional with over 40 years of hands-on experience in the industry, spanning ship repair, structural welding, and even underwater projects. Joe is a master of MIG, TIG, and Stick welding. Passionate about mentoring the next generation of welders, Joe now shares his decades of expertise and practical insights to help others build rewarding careers in welding.
DIY Welding, Metalworking, MIG Welder Guide, MIG Welding, Safety Tips, Welding, Welding Equipment, Welding Safety, Welding Techniques, Welding Wire