How Much is a Laser Welder? Cost, Types, and Benefits Explained
Published on: March 8, 2025 | Last modified: March 4, 2025
By: Joe Carter
A laser welder is a machine that uses a focused beam of light to join materials together. It creates precise welds with minimal heat, perfect for delicate jobs.
You may be wondering how much is a laser welder. It’s important to know this because the right welder at the right price can make or break your projects. I’ve seen it firsthand; investing wisely saves time and money down the road.
In this article, we’ll cover what a laser welder is, different types of laser welders, steps to evaluate costs, safety tips, pricing factors, benefits of laser welders, and real-world applications. We’ll also touch on related topics like how much does a laser welding machine cost and where can I buy a laser welder.
Contents
- How Much is A Laser Welder?
- What is a Laser Welder?
- Types Of Laser Welders
- Prerequisites: Things You Should Prepare in Advance
- Safety Tips
- Steps to Determine the Cost Of a Laser Welder
- Types Of Costs Associated With Laser Welders
- Factors Influencing Laser Welder Pricing
- How to Calculate the Total Cost of Ownership (TCO) for a Laser Welder
- Unique Issues Related to Laser Welder Costs
- Benefits Of Using Laser Welders
- Real-world Uses for Laser Welders
- Other Options You Can Consider
- Frequently Asked Questions (FAQs)
- Conclusion
- References
How Much is A Laser Welder?
A laser welder uses focused light to join metals. So, how much is a laser welder? Prices range from $5,000 to $25,000, depending on features. They’re used in industries like automotive and aerospace, great for precision work.
Welding in challenging positions also necessitates specific skills and tools; learn techniques for welding upside down to enhance your welding capabilities.
What is a Laser Welder?
A laser welder uses focused laser beams to join materials. The intense energy from the laser allows precise welding, often at temperatures exceeding 1,000°C (1,832°F). Common laser types include Nd:YAG (Neodymium-doped Yttrium Aluminum Garnet) and fiber lasers. These machines can achieve welds with widths as small as 0.5 mm (0.02 Inches), making them suitable for intricate projects.
Now, let’s talk about the cost of a laser welder. Prices vary widely based on the machine’s power and features. When I first looked into buying a laser welding machine, I was amazed by the options and their costs.
While working on a custom project, I used a handheld laser welder for delicate tasks. It was easy to maneuver and offered remarkable precision. This experience taught me that understanding the cost of a laser welder is crucial before making a purchase. Finding the right balance between cost and capability is essential, whether you’re considering a small laser welding machine or a powerful model.
Types Of Laser Welders
What are the types of laser welders and their costs?
-
Fiber Laser Welders
Fiber lasers use a fiber optic cable to generate a beam. Expect to pay around $5,000 to $30,000. Consider features, power output (E.g., 500W to 3000W), and brands like Raycus when selecting a model.
-
CO2 Laser Welders
CO2 lasers use a gas mixture to create a powerful beam. Prices range from $3,500 to $20,000. Factor in your required wattage (E.g., 100W to 500W) and check quality brands like Synrad.
-
Diode Laser Welders
Diode welders use semiconductor technology for beam generation. They typically cost between $2,000 and $15,000. Consider wattage ratings (E.g., 20W to 300W) and look for reputable models like LQS. When managing tasks that involve joining and separating metal pieces, it can be beneficial to know how to cut welds effectively.
-
YAG Laser Welders
YAG (Yttrium Aluminum Garnet) lasers are solid-state, making them highly reliable. Their prices range from $4,000 to $25,000. Check for beam quality, power (E.g., 100W to 2000W), and well-known brands like Newport.
-
Nd:yag Laser Welders
Nd:YAG lasers offer high precision and versatility for various materials. Expect to pay between $5,000 and $30,000. Examine power options (E.g., 50W to 1000W) and trusted brands like TRUMPF when choosing an Nd:YAG welder.
We covered different types of laser welders here. Next, we will cover essential preparations you should make in advance.
Prerequisites: Things You Should Prepare in Advance
What do you need to prepare for?
- Laser Welder: You’ll need a specific model, like the 1500W Laser Welding Machine. It helps you know your exact costs.
- Welding Lens: Get a high-quality 2.5 shade lens. It protects your eyes while working with high precision.
- Fume Extractor: A good extractor, such as the BOFA AD 150, keeps your workspace safe and clean from harmful fumes during welding.
- Work Surface: Prepare a sturdy metal table. A flat, non-combustible surface, like steel, is essential for stability.
- Welding Wire: Stock up on specific wire, like ER308L, to ensure strong and consistent welds.
That covers essential preparations to have in place. Let’s now take a look at safety precautions to keep in mind.
Safety Tips
Let’s cover safety measures for using a laser welder.
- Protective Eyewear: Always wear laser safety goggles. They block harmful rays, such as the N95-2913 glasses for laser use.
- Ventilation: Ensure adequate airflow during operation. Use an exhaust fan or fume extractor, like the 3M 6500 Series, to avoid inhaling fumes.
- Fire Extinguisher: Keep a fire extinguisher nearby. A Class B-C extinguisher can help manage sparks and minimize fire risks during welding.
- Clothing: Wear flame-resistant clothing. Fabrics designed for arc welding, like the Revco/Coleman fire-resistant jacket, can help prevent burns from heat and sparks.
Remember, staying safe is as important as getting the job done.
We covered safety precautions, best practices, and necessary equipment here. Next, we will look at how to assess laser welder costs.
Steps to Determine the Cost Of a Laser Welder
Now, we’ll cover the steps to help you find the costs associated with a laser welder.
-
Identify Your Needs
Start by analyzing your welding requirements. Consider the materials you’ll work with and their thickness. A laser welder can handle materials like steel, aluminum, or plastic, with thicknesses from 0.5 mm to 5 mm (0.02 In to 0.2 In). Understanding the capabilities of different welding machines affects costs because some machines are better suited for specific jobs.
It is crucial to adopt practices that help prevent cancer from welding exposure when working with these materials.
If it’s for a DIY project or small tasks, look for handheld models, which usually range from $1,200 to $3,000. I once overlooked this step and ended up with a laser welder that’s too powerful—and costly—for my needs.
Proper technique can greatly enhance the quality of your welds and minimize issues like spatter. Explore how to avoid spatter in welding to achieve cleaner results with every project.
-
Research Laser Welder Types
Explore the different types of laser welders available. There are desktop units for precise jobs and larger machines for heavy-duty tasks. Desktop models can cost about $3,000 to $10,000, while industrial models can exceed $20,000. Each type serves distinct purposes.
Brands like Miller receive excellent reviews for reliability. Investing in quality models can significantly lower long-term operational costs. Don’t rush; I wish I’d researched brands more carefully before deciding.
-
Compare Prices and Vendors
Request quotes from several vendors to find the best price range. Websites like Amazon often offer competitive prices and sales on laser welding machines. For example, I found a 1500W laser welding machine priced at around $5,500 online, which was lower than local suppliers.
Also, watch for seasonal sales or discounts on new arrivals. You might land a great deal on a laser welding machine. I once saved nearly $1,000 by waiting for a holiday sale!
-
Check After-sales Support
Evaluate the after-sales support provided by the vendor. Good customer service can save you time and money in case of issues. Ensure the vendor offers training, a warranty, and easy access to replacement parts. Some lines, like handheld models, may come with limited service warranties.
I’ve worked with companies that quickly helped resolve problems, which made a significant difference in my projects. Don’t overlook this—consider it part of your investment. What’s the benefit of a great price if you can’t get help when needed?
We covered how to assess costs for a laser welder. Next, we will explore the various cost types related to laser welders.
Types Of Costs Associated With Laser Welders
Now, let’s discuss the types of costs: purchase price, maintenance, operational costs, training, and part replacement.
-
Purchase Price
The purchase price of a laser welder typically ranges from $3,000 to $50,000, depending on the model and features. High-end machines with advanced capabilities can exceed $100,000. If you’re wondering, “How much is a laser welding machine?” consider your project needs.
-
Maintenance Costs
Maintenance costs average around $500 to $2,000 annually. Regular upkeep is essential for maintaining peak performance. Neglecting this can lead to costly repairs!
-
Operational Costs
Operational costs, including energy, consumables, and labor, can be significant. Expect to spend about $2 to $5 per operating hour, depending on power usage and materials. Monitoring these costs can help you stay within budget!
-
Training Expenses
Training can cost about $1,000 to $3,000 per employee, depending on the training depth. Highly skilled operators reduce errors and increase efficiency, yielding returns on investment. In my experience, solid training maximizes your machine’s potential.
-
Part Replacement Costs
Part replacement costs vary but generally range from $200 to $1,500, depending on the part. Common replacements include lenses, nozzles, and cables. From hands-on experience, budgeting for these costs can prevent future headaches!
Factors Influencing Laser Welder Pricing
What factors affect the cost of a laser welder?
-
Brand Reputation
Brands like Miller and IPG Photonics often command higher prices. Prestigious brands can cost 30% more than lesser-known ones, mainly due to reliability and support.
-
Machine Features
Advanced features like adjustable power settings or integrated cooling systems can raise the price. Feature-rich machines typically range from $5,000 to $20,000 or more, depending on technology.
-
Welding Thickness Capability
Welders that handle thicker materials require more power, increasing costs. Check the machine’s specs; machines for thicker materials usually cost 20% to 50% more.
-
Control Software
High-end control software can enhance precision and add to the machine’s cost. Expect software tools to increase the price by an additional $1,000 to $5,000, depending on features and updates.
-
Market Demand
Prices fluctuate based on demand. When new techniques emerge, prices can rise by up to 40% due to increased interest, impacting overall costs.
How to Calculate the Total Cost of Ownership (TCO) for a Laser Welder
Understanding the total cost of ownership (TCO) is crucial when considering a laser welder.
Cost Category | Details | Estimated Cost (USD) |
---|---|---|
Initial Purchase Price | Base price of the machine. | $5,000 – $50,000 |
Maintenance | Annual upkeep for optimal performance. | $500 – $2,000 |
Operational Costs | Energy and materials used. | $2 – $5 per hour |
Training | Cost to train operators for proper usage. | $1,000 – $3,000 per employee |
Part Replacements | Regular part replacements like lenses. | $200 – $1,500 |
Additional Considerations
- Downtime Costs: Account for potential losses during repairs or maintenance.
- Increased Production Costs: Higher efficiencies can reduce costs over time.
- Insurance Premiums: Ensure to factor in the insurance costs associated with ownership.
Calculating TCO helps in making informed purchasing decisions. It’s not just about the upfront cost; consider how much you’ll spend over the laser welder’s lifespan.
Unique Issues Related to Laser Welder Costs
Let’s examine unique technical issues with laser welders.
-
Technology Advancements
Laser welders face challenges adapting to new technology. Upgrading can increase costs and cause downtime. Regularly assess your system’s compatibility with innovations.
-
Availability Of Spare Parts
Laser welders may need specific parts quickly. Stocking critical components can save time. I recommend keeping a list of essential parts and their suppliers.
-
Calibration and Setup Requirements
Laser welders require precise calibration for proper welding. Incorrect settings can result in poor weld quality. Always check the focal length and laser intensity before starting.
-
Insurance Costs
Your laser welder may have higher insurance premiums due to fire risks. Review insurance options to find the most cost-effective coverage for your operations.
-
Specialized Training Needs
Employees need specialized training to use a laser welder safely. Lack of training can lead to accidents or improper use. Invest in training programs to minimize risks.
Benefits Of Using Laser Welders
The main benefit of laser welders is precision. While I was working on a delicate metal project, I used it for its ability to create fine, consistent welds.
Additionally, laser welders provide speed, reduced heat input, cleaner welds, and versatility. You can weld thin materials without warping, work on various metals, and even automate the process for efficiency. It is crucial to protect your eyes when welding to avoid injury such as flash burn which requires specific treatment, as detailed in the flash burn treatment guide.
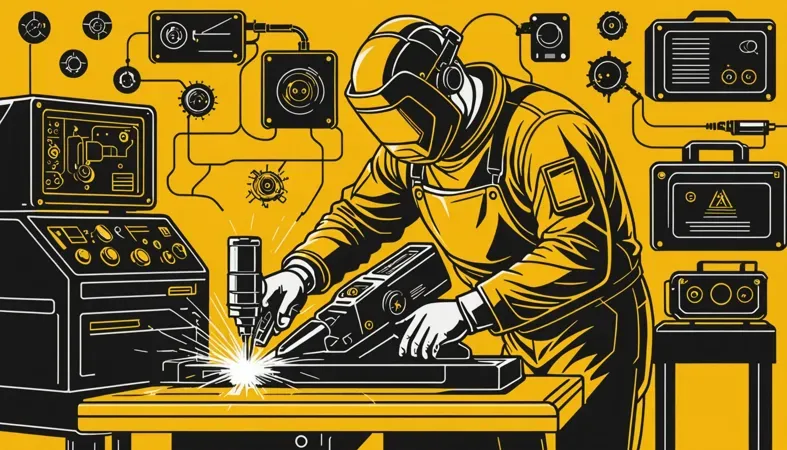
Real-world Uses for Laser Welders
I’ve seen people use laser welders to craft precision parts, but they have many applications, such as:
- Aerospace Components: Laser welders join lightweight metals precisely, reducing weight and increasing fuel efficiency. They’re crucial in aircraft manufacturing.
- Jewelry Production: Jewelers use laser welders for delicate repairs and assembling intricate designs. The heat-affected zone is minimal, ensuring the integrity of the piece.
- Medical Devices: Medical device manufacturers use laser welders to create sterile and precise components, like surgical instruments and implants. Integration is key for safety.
- Automotive Industry: In car manufacturing, laser welding provides strong joints for vehicle frames, allowing for lightweight structures and improved crash safety ratings.
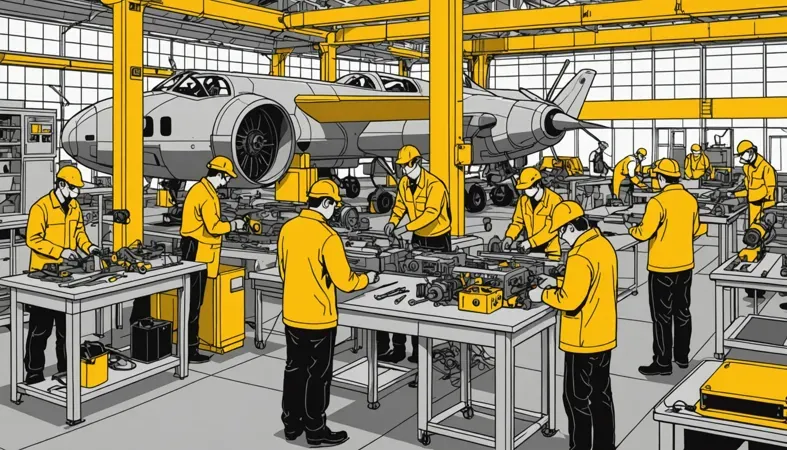
Other Options You Can Consider
There are alternative welding methods that might fit your budget and needs. For example, MIG welders, like the Miller Multimatic 215, offer great versatility for metal work. You could also explore TIG welding, which is precise and great for thin materials.
I’ve learned through hands-on experience that each method has its pros and cons. Flux-cored wire welders are also cheaper and easier to use for DIY projects. At the end of the day, it depends on your project requirements and skills! Techniques like seam welding play a crucial role in projects that require continuous welds for joining metal sheets, which you can explore further through this comprehensive guide on what is seam welding.
Frequently Asked Questions (FAQs)
Now let us look at some burning questions I typically get asked about laser welders.
How Expensive is Laser Welding?
Laser welding can be expensive, but it’s efficient. On average, it costs about $75 to $200 per hour of labor, depending on the complexity of the work. Investing in high-quality equipment can save you money long-term by reducing material waste and improving speed.
Is Laser Welding Stronger Than MIG?
Yes, laser welding is often stronger than MIG welding. Laser welds generally create deeper and narrower seams, leading to less distortion and stronger joints. Reports show that laser welds can achieve tensile strengths over 600 megapascals (Mpa) compared to 450 MPa for typical MIG welds.
How Thick Will a Laser Welder Weld?
A laser welder can effectively weld materials up to 25 mm (1 Inch) thick. However, the actual thickness depends on the specific machine and settings you’re using. Generally, machines designed for industrial use handle thicker sections better. The height of your welding table can impact the ease and precision of your work, so it’s crucial to know how high should a welding table be.
How Good Are Laser Welders?
Laser welders are incredibly good at precision tasks. They provide consistent, high-quality welds with minimal heat input. This results in lower distortion, making them a popular choice in industries like automotive and aerospace. For those looking to understand more about different types of welding equipment, welding equipment encompasses a variety of technologies that enhance efficiency and quality.
It’s essential to explore the potential health impacts associated with welding processes, especially to understand how welding can cause cancer, to ensure safety measures are appropriately implemented.
Where Can I Buy a Laser Welder?
You can buy a laser welder online or from specialty welding equipment dealers. Websites like Amazon and manufacturer’s sites offer a variety of models. Check reviews to find the best one for your needs and budget.
How Much Does a Handheld Laser Welder Cost?
A handheld laser welder typically costs between $5,000 and $15,000. The price varies based on power output and features. While it’s a higher upfront cost, it can provide a significant return on investment for mobile and custom jobs.
What is the Best Laser Welder?
The best laser welder depends on your specific needs. However, models from brands like Trumpf and IPG Photonics stand out for their reliability and performance. They offer various options suitable for different applications, from heavy industrial use to fine aerospace tasks.
Conclusion
We covered a variety of topics, including what a laser welder is, the types of laser welders, prerequisites for use, steps to determine costs, and safety tips. We also looked at the factors influencing pricing, costs associated with laser welders, unique issues related to these costs, aftercare, inspection tips, and real-world applications. Lastly, we explored alternative options and answered frequently asked questions about how much is a laser welder.
So, how much is a laser welder? Prices typically range from $5,000 to $25,000 USD, depending on the type and features you need. If you’re curious or have more questions on this, contact me if you’d like more guidance on how much does a laser welder cost or finding the best options for you.
For further information and insights into the world of welding, visit What is Welding.
References
- Howard B. Cary. (1997). Welding Manual. Upper Saddle River, NJ: Prentice Hall.
- Blodgett, O. W. (1995). Design of Weldments. Cleveland, OH: James F. Lincoln Arc Welding Foundation.
Joe Carter is a retired welding professional with over 40 years of hands-on experience in the industry, spanning ship repair, structural welding, and even underwater projects. Joe is a master of MIG, TIG, and Stick welding. Passionate about mentoring the next generation of welders, Joe now shares his decades of expertise and practical insights to help others build rewarding careers in welding.
Benefits Of Laser Welding, Laser Welder, Laser Welding Costs, Safety Tips, Types Of Laser Welders, Welding, Welding Equipment, Welding Safety, Welding Table, Welding Technology, Welding Wire