What is TIG Welding? Overview, Process, Uses, and Tips
Published on: November 21, 2024 | Last modified: March 4, 2025
By: Joe Carter
TIG stands for Tungsten Inert Gas. It’s a type of welding that uses a non-consumable tungsten electrode to create a weld.
A frequent question I encounter is what is tig welding? Understanding this process is crucial, especially if you’re looking to create clean, high-quality welds. Personally, I’ve found precise control is key to achieving the best results when using a TIG welder.
In this guide, I’ll cover what TIG welding is, how it works, different types of TIG welding, steps to perform it, factors that affect efficiency, common issues, aftercare and inspections, where it’s used, and when to consider other methods. You’ll gain clear insights into what does TIG stand for in welding and how TIG welding works in practical terms.
Contents
- What is TIG Welding?
- How Does TIG Welding Work?
- Types Of TIG Welding
- Steps to Perform TIG Welding
- What Could Go Wrong: Common Issues
- Factors Affecting TIG Welding Efficiency
- Aftercare, Inspection, and Advanced Tips for TIG Welding
- TIG Welding Techniques and Best Practices
- Where is TIG Welding Used?
- When to Try a Different Approach
- Frequently Asked Questions (FAQs)
- Conclusion
- References
What is TIG Welding?
TIG welding, or Tungsten Inert Gas welding, uses a non-consumable tungsten electrode. It creates precise, clean welds and excels in thin materials. Industries rely on it for its versatility in aerospace, automotive, and art projects.
How Does TIG Welding Work?
Gas Tungsten Arc Welding (GTAW) uses a non-consumable tungsten electrode to create an arc. This arc melts the base metal and the filler rod, which you manually feed into the weld area. The process operates at around 100 A (Amperes) for light materials, while heavier metals can require over 300 A. TIG welding provides high precision and cleaner results, making it ideal for critical applications.
This method requires skill and control. With TIG welding, you can work with stainless steel, aluminum, and even exotic materials like titanium. It’s all about technique and knowing how to manipulate the arc effectively.
Here’s what you need to do: First, adjust your settings based on your base material thickness. Second, practice combining the right travel speed and feed rate to produce a solid weld. This way, you’ll fully grasp what TIG welding is all about and see why it’s favored in industries from automotive to aerospace.
Types Of TIG Welding
What are the types of TIG welding?
-
AC TIG Welding
AC TIG welding uses alternating current. It’s ideal for welding aluminum and magnesium. To perform this type, set your welder to AC, strike the arc, and control heat input for a clean weld.
-
DC TIG Welding
DC TIG welding operates on direct current. It’s perfect for stainless steel and carbon steel. To start, set your machine to DC, prepare your material, and establish your arc for a strong, precise weld. If you need to dismantle any connections made during your work, consider exploring effective techniques on how to remove welds.
-
Pulsed TIG Welding
Pulsed TIG welding alternates between high and low current. This method minimizes heat and reduces warping. To use it, adjust your machine to pulse settings, select your peak and base currents, and start for better control over your welds.
-
Orbital TIG Welding
Orbital TIG welding is a specialized technique for tube and pipe welding. It creates consistent and precise welds in a circular path. To perform it, set up your machine for orbital motion, align the workpieces, and let the welder do the work.
-
Automated TIG Welding
Automated TIG welding uses machines to perform the welds. This boosts efficiency and precision. To implement it, program your welder for specific tasks, ensure the material is set up correctly, and watch as the machine carries out the process. Understanding how to efficiently set up a welder facilitates effective automation and ensures quality results. For detailed guidance on how to use a welder, learning the technical aspects is crucial for success.
We’ve wrapped up the different types of TIG welding here. Let us turn our attention to the steps for performing TIG welding.
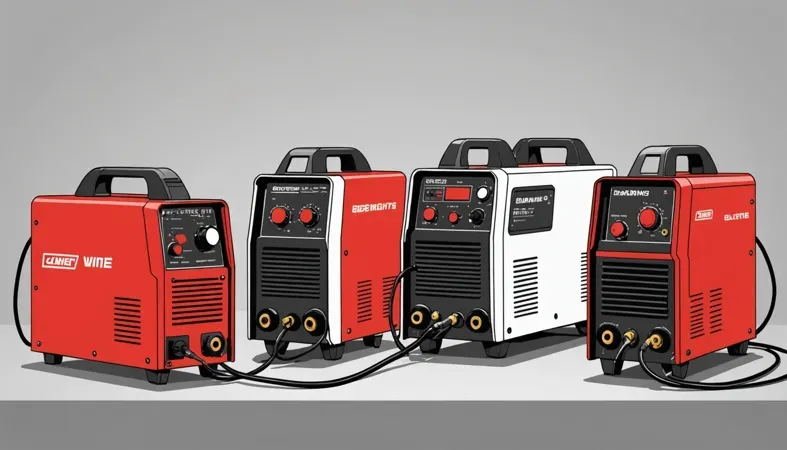
Steps to Perform TIG Welding
Now, we’ll cover the steps to get you started with TIG welding.
-
Set Up Your Equipment
Start by setting up your TIG welder. Adjust the amp setting based on the material thickness; a common setting is about 1 amp for every 0.025 inches (0.64 Mm) of thickness. A high amp setting can burn through your material, so start low and adjust as needed.
Select the right tungsten electrode. For aluminum, use pure tungsten or a tungsten-argon mix. Keep the tungsten sharpened to a fine point, about 1/8 inch (3.17 Mm) long, to ensure a stable arc and precise welding.
-
Prepare the Workpiece
Clean the metal surfaces before welding. Remove any oxides, grease, or paint for a clean weld. Use a wire brush or solvent to thoroughly clean metals such as aluminum, as a clean joint is vital for a strong bond. You may need to texture the edges depending on the joint type.
Consider beveling your edges for joint preparation. A 30° to 45° bevel is effective for thick materials, creating a stronger joint by allowing better weld penetration, which is especially critical for important structures.
-
Strike the Arc
Once everything’s set, position your welding torch above the workpiece and strike the arc by quickly dragging the torch, just like striking a match. Aim for a stable arc; you must maintain a steady hand to achieve an even bead. Discover the process of creating an arc welder using a microwave transformer to explore innovative welding techniques.
Slowly move the torch while feeding the filler rod into the molten pool. Typically, an arc length of about 1/8 inch (3.17 Mm) works best for most metals. If you get too close or too far away, you’ll disrupt the arc and may not achieve a solid weld.
-
Control Travel Speed
The speed at which you move your torch is crucial. Moving too fast can lead to weak welds, while going too slow might burn through. Aim for a steady pace to ensure consistent bead size and penetration. A typical travel speed is about 5 to 7 inches per minute (12.7 To 17.8 Cm/min).
Watch the puddle closely; it should appear fluid and shiny, not dry or bubbling. Practicing with different speeds helps you find the best pace based on material thickness and type.
-
Finish the Weld
After completing your weld bead, slowly pull the torch away to avoid creating a crater in the weld. Allow the weld to cool naturally instead of using a cooler, as rapid cooling can lead to cracking or warping.
Once cooled, clean the weld area to remove any slag or residue for a smooth finish and to prepare for any additional mechanical processes or inspections, if needed. Always assess your work to learn what was effective and what you can improve next time.
That covers the steps to perform TIG welding. Let’s now take a look at potential problems and common issues.
What Could Go Wrong: Common Issues
Let’s look at some unique problems you might face with TIG welding.
-
Poor Arc Stability
TIG welding needs a consistent arc. If you notice erratic welds, that’s poor arc stability. Fix it by adjusting your electrode closer to the workpiece or checking the gas flow rates, usually 15-25 cubic feet per hour (CFH). Mastering the techniques of forge welding can further enhance your skill set, helping you to learn how to forge weld effectively.
-
Inadequate Penetration
TIG welding often struggles with penetration on thick materials, resulting in little to no fusion. To improve this, increase your amperage, typically 1 amp per 0.001 inch (0.025 Mm) of material thickness.
-
Contaminated Weld Pools
TIG welding can suffer from contamination in the weld pool. If your welds look dull or have craters, contamination is likely. Clean the base metal thoroughly; oil or oxidation can affect the weld.
-
Weld Cracking
In TIG welding, weld cracking often occurs in carbon steel. If cracks appear after welding, it may be due to stress or insufficient heat input. Post-weld heat treatment is effective between 300°F and 500°F (149°C and 260°C).
-
Excessive Heat Input
TIG welding can also experience excessive heat input, leading to warped metal. If you see distortion, your amps are too high. Aim for about 20% less than what seems excessive. Controlling your travel speed can help too!
That covers potential pitfalls in TIG welding. Let’s now take a look at elements influencing welding efficiency.
Factors Affecting TIG Welding Efficiency
What factors influence the effectiveness and outcomes of gas tungsten arc welding?
-
Material Type
The base material significantly impacts the TIG welding process. Metals like aluminum and stainless steel require different heat settings due to their thermal conductivity—aluminum has higher conductivity and needs more power (200 to 300 A) for effective penetration.
-
Welding Current
The current must match the material’s thickness and type. Generally, thin materials use lower currents (50 to 100 A), while thicker materials need higher currents (Up to 250 A) for a strong weld. Incorrect settings lead to poor fusion or burn-through.
-
Tungsten Electrode Type
Select the right tungsten electrode. For instance, pure tungsten is ideal for DC welding on steel, while thoriated tungsten is better for aluminum. The tip shape affects arc stability—pointed tips create a focused arc, enhancing precision.
-
Shielding Gas Selection
Choosing the right gas protects the weld from contamination. Argon is commonly used for its good coverage and inert properties. Adding helium increases heat input for faster welds, particularly useful for thicker materials (2.5 Mm or More).
-
Travel Speed
Your travel speed can affect weld quality. Faster speeds can weaken welds, while too slow can cause burn-through. Aim for speeds around 10 to 20 inches per minute (25 to 50 Cm/min), depending on thickness.
We have now covered the elements influencing TIG welding efficiency. The next section will focus on aftercare, inspection, and advanced tips.
Aftercare, Inspection, and Advanced Tips for TIG Welding
Here’s key info on what to do once you’ve finished welding to keep your work top-notch.
Aftercare Strategies
After your TIG project, clean the arc zone immediately. Use a wire brush to remove impurities from the weld, plus a chemical cleaner designed for aluminum or stainless steel. Always inspect the tungsten electrode’s tip; shorten it by 3 mm if it’s worn or contaminated to maintain a stable arc.
Inspection Essentials
Inspect your weld with a weld gauge; for a 3 mm (1/8 Inch) weld, ensure the toe angle is within 70 degrees. Check for undercuts with a magnifying glass; a gap near the edge shouldn’t exceed 0.5 mm (0.02 Inches). For added assurance, use a visual inspection light like Greenlee’s Compact, which provides clear visibility of defects.
Expert Insights
If you’re experienced, like I am, fine-tuning your filler rod feed speed is crucial. Keep it 1 to 2 inches (2 to 5 Cm) away from the workpiece for optimal penetration. Always adjust argon gas flow; maintain it between 10-15 CFH (Cubic Feet Per Hour) for a precise, clean weld, especially with thin materials.
TIG Welding Techniques and Best Practices
Now that you know what TIG welding is, let’s dive into some advanced techniques and best practices you can use for better results.
Techniques to Master TIG Welding
-
Weaving Technique
The weaving technique involves moving the torch side to side while maintaining a steady travel speed. This helps fill wider joints and improves overall penetration, especially on thicker materials.
-
Manipulation of the Filler Rod
Controlling the filler rod’s angle is vital. Hold it at a 15° angle to the travel direction to guide the metal into the molten puddle, promoting better fusion.
-
Walking the Cup
This technique moves the torch in a circular motion. It’s effective for filling gaps and creating smooth welds. Perfect for pipework or wider seams!
Best Practices for Effective TIG Welding
Practice | Description | Why It Matters |
---|---|---|
Consistent Torch Position | Keep the torch at a 15° angle to maintain a stable arc. | This helps with arc stability and mitigates contamination risks. |
Regular Equipment Maintenance | Check and replace worn parts regularly, including nozzles and electrodes. | Well-maintained equipment ensures cleaner, more reliable welds. |
Practice Paddle Technique | Use a back and forth motion to enhance weld quality. | It ensures better heat distribution and material fusion. |
Where is TIG Welding Used?
TIG welding suits intricate projects and has unique applications, such as:
- Aerospace Components: TIG is essential for manufacturing aircraft parts. Its precision leaves no room for errors, critical for safety.
- Artistic Metal Sculptures: Artists prefer TIG for its versatility. It produces clean welds on materials like aluminum or stainless steel, achieving fine details.
- High-End Automotive: Custom car builders use TIG for performance. Strong, aesthetically pleasing welds keep vehicles looking sharp on the road.
- Medical Equipment: TIG welding excels in creating sterile tools. Precision is vital in healthcare, ensuring reliability and safety in surgical procedures.
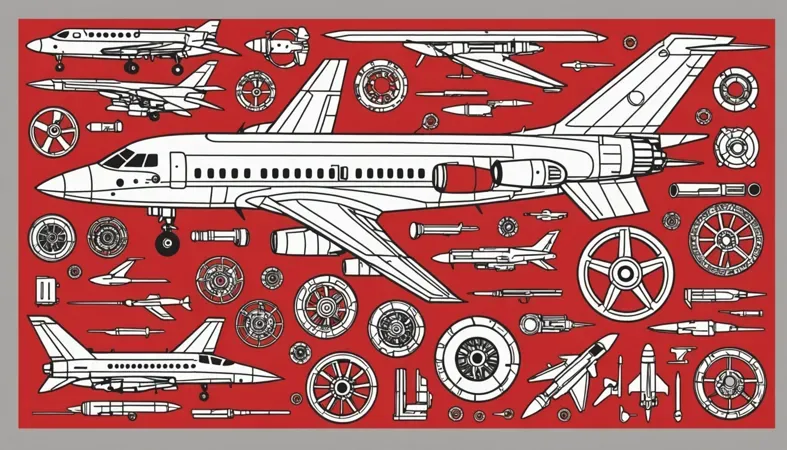
When to Try a Different Approach
Sometimes, you might want to explore alternatives to get similar results to TIG welding. Options like MIG welding or gas tungsten arc welding can be more efficient and economical in specific situations. For example, a Hobart Handler 210 MVP for MIG welding is great for speed, especially on thicker materials.
From my unique perspective, I’ve noticed that submerged arc welding is perfect for heavy-duty projects where depth of penetration is key. It also delivers faster production rates, which can save you time and money. When precision isn’t as critical, these options can really shine.
Frequently Asked Questions (FAQs)
Now let us look at some common questions I typically get asked.
What is TIG Welding Used for?
TIG welding is often used for applications requiring high precision and quality. This method works well for metals like aluminum, stainless steel, and copper. It’s ideal for aerospace and automotive industries where small tolerances matter, usually within 0.25 mm (0.01 In).
What is the Difference Between TIG and MIG Welding?
The key difference between TIG and MIG welding lies in the process. TIG welding uses a non-consumable tungsten electrode to produce the weld, while MIG employs a continuous wire feed. TIG is slower but offers more control, perfect for thinner materials. For those exploring combined roles and skills in welding, understanding what a combo welder does provides significant professional insights.
Does TIG Welding Require Gas?
Yes, TIG welding requires shielding gas for protection. Most commonly, argon gas is used, with a flow rate around 12-15 liters per minute (L/min). This gas shields the weld area from contaminants, ensuring a clean weld. Ensuring adequate amperage for specific rod sizes is critical in welding performance, and you can explore more about the required amps for a 3/32 welding rod.
What Does TIG Stand for in Welding?
TIG stands for Tungsten Inert Gas. This name highlights the use of tungsten electrodes and inert gas like argon for shielding. It reflects the technique’s reliance on these components for creating high-quality welds.
How Does TIG Welding Work?
TIG welding works by generating an electric arc between the tungsten electrode and the workpiece. This arc melts the base metal and a filler rod if used. The process offers excellent precision, suitable for intricate designs and applications.
Conclusion
We covered what TIG welding is, how it works, different types, the steps to perform it, factors affecting efficiency, common issues, inspection, advanced tips, and its applications. You learned about important elements like electrode types, filler material, and common challenges. We also touched on when to consider alternatives to TIG welding and answered frequently asked questions.
TIG welding, or Tungsten Inert Gas welding, is a precise technique that uses a non-consumable tungsten electrode to create a strong joint in metals like aluminum and stainless steel. It’s popular for its clean welds and versatility, which includes various applications across industries. Feel free to reach out if you have further questions about TIG welding or any related topics.
For additional insights and resources related to welding, consider visiting What is Welding.
References
- American Welding Society. (2020). AWS Welding Handbook: Welding Science and Technology (Vol. 1). Miami, FL: AWS.
- Canadian Welding Bureau (CWB): https://www.cwbgroup.org
- American Society of Mechanical Engineers. (2019). ASME Section IX: Welding and Brazing Qualifications. New York, NY: ASME.
Joe Carter is a retired welding professional with over 40 years of hands-on experience in the industry, spanning ship repair, structural welding, and even underwater projects. Joe is a master of MIG, TIG, and Stick welding. Passionate about mentoring the next generation of welders, Joe now shares his decades of expertise and practical insights to help others build rewarding careers in welding.
American Welding Society, Arc Welding, MIG Welding, Pipe Welding, TIG Welding, Tungsten Inert Gas, Welding, Welding Applications, Welding Technique, Welding Techniques, Welding Tips