How to Use a Welder? Setup, Safety Tips, Techniques
Published on: June 29, 2025 | Last modified: March 4, 2025
By: Mark Carter
A welder is a skilled tradesperson who joins metal parts together using heat. They play a crucial role in manufacturing and construction.
Many people are curious about how to use a welder. It’s important to know the right techniques to avoid accidents and ensure quality work. From my own experience, starting with basic safety procedures made all the difference in my welding projects.
In this guide, you’ll discover the basics of welder types, essential prerequisites, steps to use a welder, safety tips, welding techniques, factors affecting quality, common issues, aftercare, and the benefits of this skill. We’ll also touch on alternatives to conventional welding and answer frequently asked questions. Whether you’re curious about how to set up a welder or looking to improve your skills, this guide has you covered.
Contents
- How to Use A Welder?
- What is a Welder?
- Types Of Welders
- Essential Prerequisites to Get Started
- Safety Tips
- Steps to Use a Welder
- Types Of Welding Techniques
- Factors Affecting Welding Quality
- Common Issues You Might Encounter
- Aftercare, Inspection, and Advanced Tips for Welding
- Advanced Welding Techniques You Should Know
- Top Benefits You Can Expect
- Typical Uses Of Welding
- Exploring Alternatives to Conventional Welding
- Frequently Asked Questions (FAQs)
- Conclusion
- References
How to Use A Welder?
A welder joins metal using heat. To use a welder, set your voltage between 18-30 volts, adjust the feed speed to 2-10 inches per minute, and wear safety gear. It’s tricky for beginners, often used in auto repair and construction.
What is a Welder?
A welder is a skilled tradesperson who uses a welding machine to join materials, often metals. The welder applies heat and pressure to fuse pieces, typically using techniques like MIG (Metal Inert Gas) and TIG (Tungsten Inert Gas) welding. An average MIG welder operates at around 200 amps, producing temperatures over 3,600°C (6,500°F). In the U.
S. alone, about 350,000 welders work in various industries, including construction and automotive.
Using a welder may seem daunting at first. I remember learning to set up a welder for the first time. It took some trial and error to adjust the voltage and wire speed just right for my project, but the satisfaction was worth it!
A friend used it for a custom car project. He had to learn how to use a welder effectively to attach new metal panels. We often discussed how to set up the welder so those panels fit snugly. His tips with the welding pliers made a significant difference. I still remember the sparks flying as he executed perfect joint after joint, turning him into quite the mechanic!
Types Of Welders
-
MIG Welders
MIG welders (Metal Inert Gas Welders) use a continuous wire feed for welding. To operate a MIG welder, first set the right voltage and wire speed based on the metal thickness. Adjust the settings, feed the wire through the gun, and pull the trigger to start welding. Consistency in settings is crucial to avoid common causes of weld spatter.
-
TIG Welders
TIG welders (Tungsten Inert Gas Welders) provide precise control for thin materials. To use a TIG welder, strike an arc between the tungsten electrode and the metal. Keep a steady hand while moving the torch and adding filler material as needed for a clean weld. It is also important to understand the relevance of a hot pass in welding when ensuring durability in weld quality.
-
Stick Welders
Stick welders (Shielded Metal Arc Welders) use an electrode to create an arc. To use a stick welder, choose the correct electrode and set the amperage according to the material. Strike an arc by tapping the electrode on the metal, then move steadily to weld. While mastering the techniques of stick welding is essential, it is equally important to be aware of how dangerous welding can be.
-
Multiprocess Welders
Multiprocess welders can handle MIG, TIG, and Stick welding in one machine. To operate this type, select the necessary welding mode. Follow the specific setup steps for that mode, like adjusting wire feed for MIG or choosing the right electrode for Stick.
-
Plasma Arc Welders
Plasma arc welders use a constricted plasma arc, ideal for precision work. To use a plasma arc welder, set up the machine and adjust the gas flow. Maintain a consistent distance between the electrode and the workpiece as you weld to create a strong joint. The intensity of a welding arc can greatly impact the quality and safety of your work, making it essential to understand just how bright a welding arc can be through a welding arc’s brightness.
We’ve wrapped up different types of welders here. Next up, we’ll look at the essential prerequisites to get started.
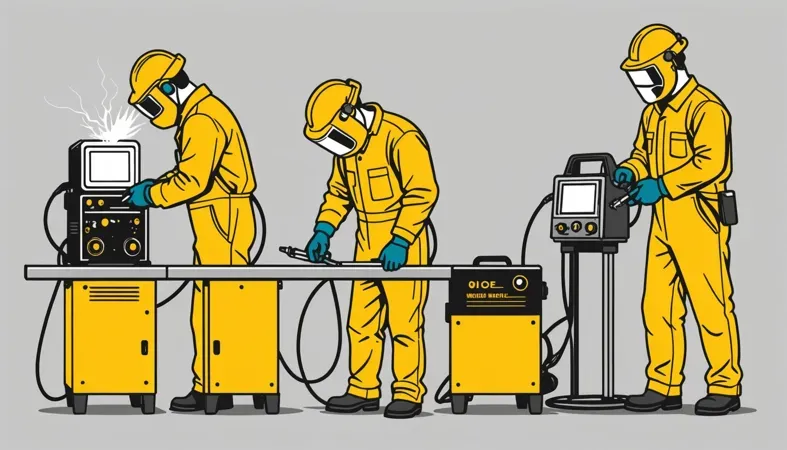
Essential Prerequisites to Get Started
What do you need to prepare for welding?
- MIG Welder: You’ll need a welder, like the Lincoln Electric SP-175, for precise metal joining. It’s vital for maintaining control and quality.
- Welding Wire: High-quality wire, such as ER70S-6, is crucial for a strong bond in MIG welding.
- Gas Cylinder: You’ll need a gas cylinder containing an Argon mix, like 75% Argon and 25% CO2, to produce a stable arc.
- Welding Cart: An ergonomic cart, like those from Chicago Electric, helps organize your tools and keep your workspace clutter-free.
- Workpiece Material: Get materials, like mild steel (A36), to practice welding. You can’t weld without them!
So far we covered the essential requirements to begin. Next, let’s look at important safety guidelines.
Safety Tips
Let’s cover essential precautions for using a welder.
- Wear Protective Gear: Always use a helmet and gloves like those from Lincoln Electric, as they protect against sparks and UV rays.
- Check Ventilation: Proper airflow is vital. Ensure you have at least 12 m³/hour (About 424 Ft³) of fresh air.
- Inspect Equipment: Regularly check cables and connections. I recommend using Miller Electric cables for durability.
- Keep Workspace Clean: Clear clutter to prevent fires and tripping hazards—safety depends on a tidy area.
Remember, safe practices keep you secure and focused while welding.
You should now have a good understanding of welding safety, precautions, and best practices. In the next part, we’ll discuss how to use a welder.
Steps to Use a Welder
Now, we’ll cover the essential steps for using a welder like a pro. Follow these steps and get welding!
-
Set Up Your Workspace
Create a clean, organized workspace. Ensure it’s well-ventilated, especially when using MIG or TIG welding processes. I prefer working on a flat, sturdy surface. A clutter-free area helps you focus on the weld instead of dodging obstacles.
Keep flammable materials at a safe distance of at least 10 feet (3 Meters) from combustible items. Good lighting impacts precision; bright, overhead lights help you see every detail clearly.
-
Prepare the Weld Joint
Clean the surfaces of the materials you’re welding. Rust, oil, or dirt can ruin a good weld. A wire brush or grinder works well. I once skipped this step on a rusty piece of metal, resulting in a weak weld.
Next, align the pieces correctly. Use clamps to hold them in place. You want a tight fit for a strong joint; even a small gap can create problems. For instance, a larger gap reduces penetration, leading to poor fusion.
-
Adjust the Welder Settings
Select the correct amperage based on the material’s thickness. Generally, it’s 1 amp for each 0.001 inch (0.025 Mm) of metal thickness. For a 1/8 inch (3.2 Mm) piece, set your welder to 80 amps. It’s important to be aware of phenomena like weld flash effects when working with welding processes.
If you’re using MIG, also check the wire feed speed. Incorrect settings can lead to birdnesting or poor weld quality. Always do a test weld before starting the actual work; it saves time!
-
Begin Welding
Start welding at the edge of the joint. Move the welder steadily at a moderate pace to create a uniform bead. In MIG welding, aim for the bead width to match the wire for consistent results.
Don’t rush! Moving too fast creates weak spots. If the arc flickers, you’re either too far away or too close. Adjust as needed during the welding process. The more you practice, the better your control will be.
You should now have a good understanding of how to use a welder. In the next part, we’ll discuss various welding techniques.
Types Of Welding Techniques
Let’s explore the different types of welding: Arc Welding, Gas Welding, Resistance Welding, Laser Welding, and Electron Beam Welding.
-
Arc Welding
Arc welding uses an electric arc to melt and join materials. It operates at around 3,600°C (6,500°F). For beginners, you’ll need to set up the welder correctly with the right electrode and voltage settings, which are essential aspects of welding fundamentals.
It’s essential to understand the potential health risks associated with welding practices.
-
Gas Welding
Gas welding uses a flame fueled by oxygen and acetylene. The flame temperature can reach about 3,500°C (6,332°F). It’s ideal for lighter metalwork and repairs.
-
Resistance Welding
This technique uses electric current to create heat in the materials. It’s suitable for thin materials and provides quick results. Just control the pressure and current for a strong joint.
-
Laser Welding
Laser welding employs a high-energy laser beam to melt metals. It’s precise and fast, with laser power ranging from 100 to 10,000 watts. This method is excellent for thin sections and complex shapes.
-
Electron Beam Welding
Electron beam welding uses a focused beam of electrons to weld in a vacuum. The heat can reach up to 3,000°C (10,000°F). It’s ideal for high-precision work and can join dissimilar materials.
Factors Affecting Welding Quality
What factors influence your welding experience and results? Let’s dive in.
-
Material Type
The type of metal significantly alters your welding approach. For example, carbon steel requires different settings than stainless steel, impacting the weld’s appearance and strength.
-
Weld Joint Design
A well-designed joint is crucial for a solid weld. Different designs, like butt or fillet joints, affect penetration and strength. Poor design increases the chance of failure.
-
Welder Settings
Your welder settings must match the job. I once used too high a voltage, causing excessive spatter and weak welds. Each welder requires specific adjustments, like amperage and voltage, for various materials.
-
Environmental Conditions
External factors like wind and temperature can influence weld quality. For instance, welding in high winds can lead to contamination, resulting in weaker seams.
-
Electrode Type
The electrode is your main tool and determines how well you weld. Using the wrong electrode can create defects; for instance, a 6011 electrode works better on dirty metal than a 7018.
Common Issues You Might Encounter
Let’s look at specific problems unique to welders.
-
Inconsistent Weld Beads
Welders might face inconsistent beads due to feed issues. Check cable feeds for clogs, and adjust speed to 1.5 to 2.0 m/min (5 to 6.5 Ft/min). Clean or replace clogged tips, or realign materials.
-
Overheating Of Material
A welder can overheat if settings are too high. Once, I didn’t monitor the amperage, which led to burned edges. Use a lower setting and maintain a consistent speed.
-
Poor Penetration
If your welder struggles with penetration, check for dirty surfaces or insufficient voltage. Use at least 18 volts for strong penetration. Clean the surface before welding.
-
Excessive Spatter
A welder may create too much spatter if the gas mix or stick-out is off. Ensure a gas flow rate of 12-20 L/min (0.4-0.7 Ft³/min) and adjust stick-out to 5 to 10 mm (0.2 To 0.4 In).
-
Cracking in Weld Joints
Cracking might indicate cold welding or rapid cooling, which can trouble any welder. Preheat areas to 100°C (212°F) and cool them slowly to reduce stress.
Aftercare, Inspection, and Advanced Tips for Welding
Here are crucial insights for after welding. This section covers aftercare practices, inspection details, and expert tips.
Aftercare Tips
After you’ve welded, clean the gun nozzle regularly. Use a specialized cleaner like Lincoln Electric C500. Check for dirt or spatter that may affect accuracy. After ten uses, inspect cables and grounded connections for wear. Proper maintenance prolongs equipment life and ensures better results.
Inspection
Inspect your welding helmet for cracks and signs of fatigue at least every six months. Ensure the lens hasn’t degraded; I recommend using auto-darkening lenses like 3M Speedglas for durability. Test your gas flow rate regularly; it should be around 15–20 CFH (Cubic Feet Per Hour). Consistent checks help you avoid uneven welds.
Expert Tips
To enhance weld quality, trial your settings before the actual job. Adjust voltage levels incrementally; a change of just 5 V can significantly alter bead appearance and penetration depth. When welding thin materials, using 0.023 in (0.58 Mm) wire works wonders. Don’t hesitate to experiment with pulsing techniques for better heat control.
Advanced Welding Techniques You Should Know
Once you master the basics, it’s time to elevate your skills. Let’s explore some advanced techniques that can enhance your welding experience.
Pulse Welding
- Pulse welding alternates between high and low heat. This reduces warping and improves penetration in thin materials.
- It’s particularly useful in TIG welding, where controlling heat is critical.
Weaving Technique
- This technique involves moving your welding torch back and forth. It spreads the heat over a wider area, which is great for thicker materials.
- Using the weaving technique can help prevent burn-through in sheets as thin as 1/16 inch (1.6 mm).
Tack Welding
- Tack welding involves making small temporary welds to hold pieces in place before final welding.
- It helps maintain alignment, especially useful in complicated assemblies.
Controlled Heat Input
This technique is all about managing heat during welding. You can adjust travel speed and amperage to control heat input, which can significantly affect the final weld quality.
Technique | What It Does | Benefits |
---|---|---|
Pulse Welding | Alternates heat levels | Reduces distortion and improves penetration |
Weaving Technique | Back and forth motion | Prevents burn-through on thin materials |
Tack Welding | Temporary holds for alignment | Maintains joint stability during final welds |
Controlled Heat Input | Manages heat during welding | Enhances weld quality and prevents defects |
Top Benefits You Can Expect
The main benefit of knowing how to use a welder is the ability to create strong, durable joints. A friend of mine used one to fix his car, and the results were outstanding.
Additionally, you’ll enjoy cost savings, improved safety, better control over your projects, and the satisfaction of creating something unique. With a welder, you can tackle DIY projects, make repairs, and even start a small business!
Typical Uses Of Welding
I’ve used welding for metal repairs in cars, but it has many applications, such as:
- Manufacturing Frameworks: Welders create sturdy frames for buildings. It’s favored for high strength in structures that must support weight.
- Auto Body Repair: Professionals use welding to fix dents or replace damaged sections in vehicles. This method’s effective and fast.
- Pipelines Construction: Welders join pipes for gas and oil transport. This technique’s vital for its leak-proof integrity.
- Art and Sculpture: Artists use welding to craft metal sculptures. It’s highly regarded for creating intricate, durable designs.
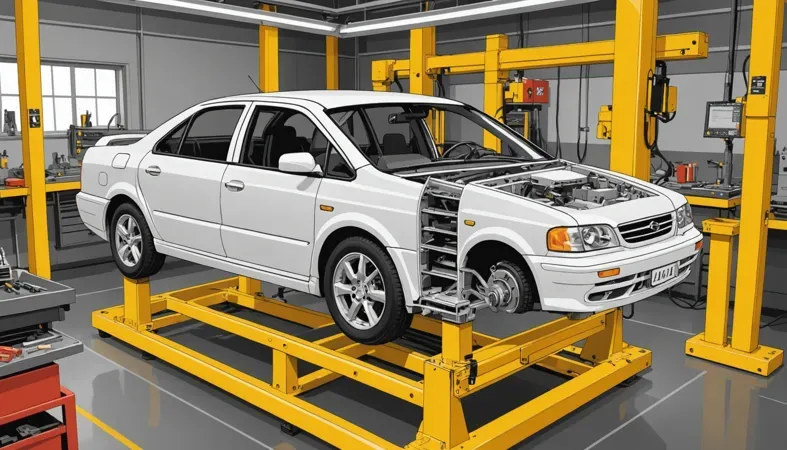
Exploring Alternatives to Conventional Welding
When you’re looking for other ways to join metal, options like gas tungsten arc welding (GTAW) and MIG welding can be great choices. For example, a Miller Multimatic 215 can handle various welding processes, making it incredibly versatile. Sometimes, alternative methods like Soldering are preferred because they require less heat and still achieve solid joints.
If you’re a beginner, using a flux-cored welder, such as the Lincoln Electric K3235-1, simplifies the process. For tasks like repairing thin sheets or doing intricate work, welding machines provide excellent control. Having navigated similar challenges, I’m all about finding the right method that meets your specific needs.
To enhance your welding skills, you might find it valuable to avoid spatter in welding.
Frequently Asked Questions (FAQs)
Now let us look at the questions I typically get asked about welding.
Can You Teach Yourself to Weld?
Yes, you can teach yourself to weld. Many beginners start by watching online tutorials and practicing on scrap metal. A recent survey found that about 70% of amateur welders successfully learn on their own without formal training.
What is the Best Welding Method for Beginners?
The best welding method for beginners is MIG welding. This method is user-friendly, requiring less skill to produce clean welds. In fact, MIG welding can halve the time needed to complete projects compared to other methods like Stick or TIG welding.
How Hard is It to Use a Welder?
Using a welder isn’t very hard, but it does take some practice. Most think it’s similar to using a glue gun, just with more equipment. You’ll get the hang of it with about 8 to 10 hours of hands-on experience.
How Do I Set Up a Welder?
To set up a welder, start by ensuring it’s plugged into a suitable outlet with the right voltage. For instance, many MIG welders operate at 240V (110V in Some Home Setups). Always refer to the user manual for specific setup instructions. If you’re considering welding modifications on a vehicle, it’s crucial to understand the legal aspects of welding car frames.
How Do I Hook Up a Welder?
Hooking up a welder involves connecting the ground clamp to your workpiece and attaching the welding gun to the welder’s output port. For safety, ensure all connections are secure and check for proper flow of electric current.
How to Use Welding Pliers?
You use welding pliers primarily for gripping and cutting. They can cut through wire up to 1/8 inch (3.2 Mm) thick. Their design allows for easy manipulation during welding tasks, helping ensure smooth operation.
Conclusion
We’ve made it to the end, and I hope it was helpful. We covered what a welder is, the types of welders, essential prerequisites, the steps to use a welder, safety tips, welding techniques, factors affecting quality, common issues, inspection, and advanced tips. Also, we talked about the benefits of welding and its typical uses, plus some alternatives to conventional welding.
So, how to use a welder? Start by setting it up properly with the right safety gear. Remember to pay attention to the welding technique and maintain quality; small details count. If you need additional advice, I’m here to help with any tips on how to use weld gear effectively, how to set up a welder accurately, and more.
To explore even more welding insights and resources, feel free to visit What is Welding.
References
- Lincoln Electric. (2020). The Procedure Handbook of Arc Welding (15th ed.). Cleveland, OH: Lincoln Electric Company.
- Norrish, J. (2006). Advanced Welding Processes. Boca Raton, FL: CRC Press.
- American Welding Society (AWS): https://www.aws.org
Mark is a skilled welding engineer specializing in advanced metal joining technologies and process design. With a formal education in welding engineering and a background rooted in practical experience, Mark bridges the gap between theory and application. He is passionate about making technical concepts accessible, empowering welders to embrace innovation while mastering essential skills. Mark combines his scientific expertise with a commitment to supporting the welding community alongside his uncle, Joe.
American Welding Society, How To Use A Welder, Safety Tips, Types Of Welders, Welding, Welding Essentials, Welding Techniques, Welding Wire