What is Weld Flash? | Causes, Effects, and Prevention
Published on: April 8, 2025 | Last modified: March 4, 2025
By: Tyler James
Weld flash is bright light caused by intense heat during welding. It can harm your eyes and skin if you’re not careful.
I often hear people ask what is weld flash? It’s crucial to understand this, as not knowing can lead to serious injuries. From my experience, even a moment of exposure can leave you hurting, so protective gear is a must.
In this guide, we’ll discuss how weld flash works, different types of weld flash, steps to minimize its effects, factors influencing it, common issues, aftercare, and advanced tips. We’ll also cover use cases and explore alternatives to achieve results similar to weld flash, including topics like what is flash burn in welding.
Contents
- What is Weld Flash?
- How Does Weld Flash Work?
- Types Of Weld Flash
- Steps for Minimizing Weld Flash
- Factors Influencing Weld Flash
- Typical Issues With Weld Flash
- Effects of Weld Flash
- Aftercare, Inspection, and Advanced Tips for Weld Flash
- Use Cases Of Weld Flash
- Alternatives for Achieving Results Similar to Weld Flash
- Frequently Asked Questions (FAQs)
- Conclusion
- References
What is Weld Flash?
Weld flash is an eye injury caused by exposure to intense welding light. It produces UV radiation that can burn the cornea, leading to pain and sensitivity. Welders often face this risk during metal joining and fabrication processes.
How Does Weld Flash Work?
Welder’s flash occurs when the bright light and harmful ultraviolet (UV) rays from welding irritate the eyes. It’s caused by strong radiation, often exceeding 6,000 °F (3,316 °C). The human eye can’t handle this intense light, leading to corneal damage. About 90% of welders report experiencing this condition at some point in their careers.
This flash burn results from UV rays, which can damage the eye’s tissue and cause intense discomfort. Symptoms include redness, tearing, and pain, lasting from a few hours to several days. Without protective gear, these effects can worsen significantly.
I recommend always wearing a proper welding helmet with UV protection. In my experience, a good-quality lens can prevent flash burn. Simple safety measures can save you from serious pain later!
Types Of Weld Flash
What types of flash do welders encounter?
-
Arc Weld Flash
Arc weld flash results from the intense light of an electric arc. It can cause eye discomfort, similar to sunburn. To prevent it, wear a welding helmet with the correct shade to protect your vision. Understanding the potential risks associated with welding can provide vital knowledge about how dangerous welding can be.
-
Micro Weld Flash
Micro weld flash is a smaller-scale flash from high-frequency welding processes. It can lead to temporary eye pain. To protect yourself, use proper eye protection and limit exposure to sparks and intense light.
-
Laser Weld Flash
Laser weld flash is intense and may occur during laser welding. It generates a bright beam that can damage your eyes. To reduce this risk, use appropriate filters and protective gear while working. Exploring the assembly of a simple welding system from a 12v battery-powered setup can help understand basic welding principles and safety measures.
-
TIG Weld Flash
TIG weld flash comes from the tungsten inert gas process, producing concentrated light. It’s very bright and can harm your retinas over time. To protect against it, use a well-fitted helmet with the proper lens shade.
-
MIG Weld Flash
MIG weld flash occurs during metal inert gas welding. The rapid arcs can emit bright light, temporarily blinding a welder. To combat this, always wear a quality welding mask designed for MIG use.
That covers the different types of weld flash. Let’s now take a look at steps for minimizing weld flash.
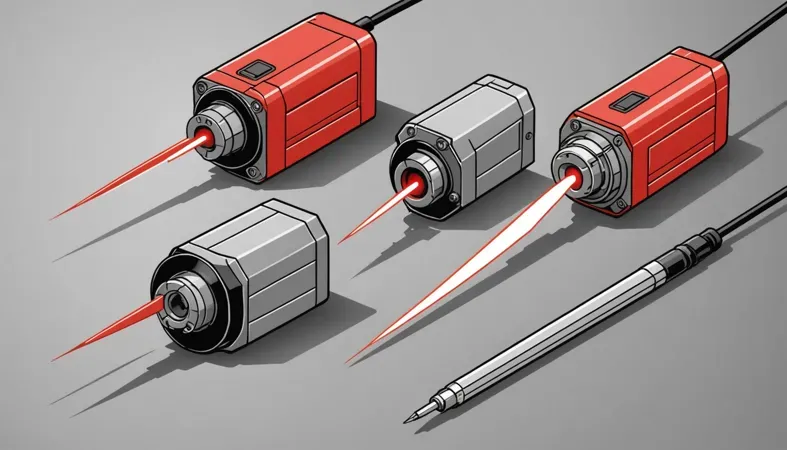
Steps for Minimizing Weld Flash
Here are steps to effectively reduce weld flash.
-
Prepare Your Workspace
Keep your workspace clean and organized. Remove flammable materials and ensure proper ventilation. A well-lit area helps spot potential flash risks. Don’t underestimate the importance of a tidy work surface; it makes a significant difference!
-
Select Appropriate Equipment
Use high-quality protective gear, especially welding helmets with UV/IR protection. I recommend a shade 10 lens to shield your eyes from harmful radiation. Plenty of options are available, so research brands like 3M or Jackson Safety. Remember, protecting your vision is priority number one!
-
Ensure Proper Settings
Check your welding machine settings before starting. Adjust the voltage and amperage according to the material’s thickness; for example, 3 mm requires about 115-130 Amps. Keep a log of tested settings to find the ideal match quickly. This minimizes unwanted flash while ensuring a strong weld.
-
Utilize Correct Techniques
Use steady, fluid motions while welding to reduce flashes. Maintain a consistent arc length; a longer arc can increase the chance of flash burns. Aim for an arc distance of about 3-5 mm (1/8 – 3/16 inches) for optimal results. For more insights on best practices, consider following some welding guidance to enhance your skills. A stable hand prevents mistakes and enhances your craftsmanship!
If spatter affects nearby surfaces understanding how to fix welding spatter on glass can be crucial.
-
Implement Protective Measures
Always wear appropriate face shields and gloves when welding. Consider using anti-flash screens or protective barriers around your workspace for larger projects. Cover exposed skin to prevent welding flash burns, even in areas not typically exposed to sparks. For more effective practices, look into welding safety precautions as safeguarding your skin is as important as protecting your eyes!
Learning about how you can safely view an eclipse with a welding mask could enhance your understanding of eye protection in different contexts, and for more information, check out viewing an eclipse through a welding mask.
We’ve wrapped up steps for minimizing weld flash here. Next up, we’ll look at factors influencing weld flash.
Factors Influencing Weld Flash
What factors can affect weld flash severity?
-
Welding Technique
Your welding technique matters. Techniques like arc welding generate a lot of UV (Ultraviolet) and IR (Infrared) radiation, increasing the risk of weld flash.
-
Material Type
The materials you’re using can make a difference. Metals like aluminum produce more intense flashes due to their reflective properties and high heat conductivity.
-
Environmental Conditions
It’s best to work in controlled environments whenever possible. Windy or bright conditions can increase flash intensity, causing more eye strain.
-
Equipment Calibration
Calibrating your equipment ensures you’re using the correct power settings. Mismatched settings can raise the chance of flash burns by allowing excessive light exposure.
-
Operator Skill Level
An experienced welder can minimize risks. They’re less likely to face severe flashes because they know how to shield their eyes and have refined their techniques.
So far we covered the factors that influence weld flash. Next, let’s look at common problems associated with weld flash.
Typical Issues With Weld Flash
Let’s look at unique issues related to weld flash.
-
Excessive Heat Generation
Weld flash can generate excessive heat. You can identify it by warped materials or discoloration. Cool the weld area with water or apply a thermal barrier. Adjust your settings—lowering amperage often helps. Understanding the factors that lead to spatter can further enhance your welding techniques. For more information on this, explore more about what causes weld spatter.
-
Inconsistent Quality
Weld flash may cause inconsistent quality in seams. Spot testing reveals weak points. I recommend using a calibration process before starting to maintain balance in your technique.
-
Visibility Problems
Weld flash can create visibility problems due to smoke or sparks. Ensure strong lighting in your workspace. Use clear perspex (Acrylic) barriers to protect visibility without compromising safety.
-
Health Risks
Weld flash poses health risks like flash burns. Symptoms include redness and irritation. Always wear appropriate protective gear, like a welding helmet with UV filters, and take breaks to prevent strain. For those involved in aquatic environments, it is crucial to be aware of the hazards of underwater welding.
-
Compliance Issues
Weld flash can lead to compliance issues, particularly with safety regulations. Check local standards regularly to ensure adherence and keep documentation of safety equipment used on-site.
Effects of Weld Flash
Weld flash can have various effects, both short and long-term. Let’s break them down:
Short-Term Effects
- Eye Irritation: Bright flashes can strain your eyes. You might feel discomfort.
- Heat Sensation: The intense heat from the flash can cause burns.
- Noise Exposure: The welding noise can damage your hearing over time.
Long-Term Effects
- Vision Problems: Prolonged exposure may lead to permanent vision loss.
- Skin Damage: Skin can suffer from repeated exposure to UV radiation.
- Hearing Loss: Chronic exposure to loud welding sounds can cause hearing issues.
Understanding these effects can help you take better care of your health while welding.
Aftercare, Inspection, and Advanced Tips for Weld Flash
Here’s essential guidance to help you manage and tackle weld flash effectively.
Aftercare Tips
After you notice weld flash effects, avoid rubbing your eyes. Use a saline solution (Salt Water) to rinse them gently. Stay hydrated; drink at least 2 liters (0.53 Gallons) of water daily to aid in healing.
Inspection
Inspect your eyes under good lighting after experiencing weld flash. Check for swelling or redness using a mirror. I use ‘Refresh Plus’ eye drops to soothe irritation before getting a full check-up with a specialist.
Expert Tips
Wear UV protection goggles (Minimum UV400 Rating) during welding tasks. Use specific products like ‘3M Peltor’ if you notice persistent side effects. Keep your workstation well-ventilated, aiming for less than 100 ppm (Parts Per Million) of harmful fumes to avoid further complications. Consistency in protective measures is essential!
Use Cases Of Weld Flash
I’ve known people who use weld flash for various tasks. It has many applications, such as:
- Pipeline Construction: In pipeline welding, weld flash ensures joint quality and prevents failures. It’s crucial for transporting gas and oil, making it popular in the energy sector.
- Automotive Assembly: Weld flash plays a key role in producing strong, heat-treated parts. It’s often used in frames and chassis, making it common in the automotive industry.
- Aerospace Manufacturing: Aerospace applications require precise weld flash to avoid structural failures. It’s used for fuselage and engine components, making it vital for safety.
- Shipbuilding: Weld flash is essential for constructing hulls and superstructures. It ensures resilience against harsh marine environments and is extensively used in naval engineering.
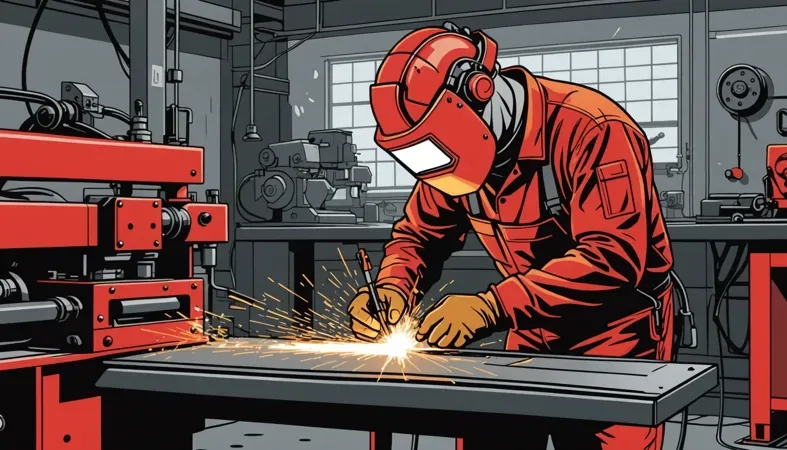
Alternatives for Achieving Results Similar to Weld Flash
There are several methods that can yield similar results when managing risks associated with weld flash. For instance, using auto-darkening helmets, such as Speedglas 3M, helps protect your eyes effectively. Based on my observations and experiences, these helmets adjust to light properly and can greatly reduce the chance of flash burn.
Another option is employing safety goggles, like Pyramex V2G, designed specifically for welding tasks. These goggles give you solid protection against harmful UV rays while enhancing visibility. In some cases, people might prefer these alternatives for better comfort and a wider field of view during the welding process.
Frequently Asked Questions (FAQs)
Here are some questions I typically get asked about weld flash.
What is Welder’s Flash?
Wil der’s flash is a condition caused by exposure to intense light during welding. It’s due to ultraviolet (UV) light that can burn the cornea, leading to painful symptoms. More than 80% of flash burns are preventable with proper eye protection.
How to Get Rid Of Welders Flash?
To get rid of welder’s flash, it’s best to rest your eyes in a dark room. Place a cold compress on your eyes to reduce discomfort. Many find soothing eye drops helpful. If symptoms persist for more than 24 hours, seek medical attention.
How Long Does It Take to Get Welders Flashed?
You can get welder’s flash instantly or within a few hours after exposure. Symptoms usually appear 6-12 hours post-exposure, peaking around 24 hours. Prompt treatment can shorten discomfort duration.
What Causes Flashback in Welding?
Flashback in welding occurs when flames travel back into the welding equipment. This danger can arise from improper gas pressures or mixed gases. Maintaining proper equipment and checks is crucial; it can save lives.
What Does Welding Flash Feel Like?
Welding flash feels like a gritty sensation in your eyes, resembling sand. You might experience redness and tears. Since it’s caused by UV rays, it leads to burning and discomfort, requiring urgent attention when it happens.
What is Flash Welding?
Flash welding is a process that joins two pieces of metal using high current and heat. The two pieces’ surfaces are joined without filler metal. This method is fast and provides strong weld joints, typically seen in large-scale manufacturing.
When considering the costs involved in welding, understanding the expenses associated with different types of welding gases can be beneficial. For more details on this, you can explore how much MIG welding gas costs through this resource.
Conclusion
I hope this gave you what you needed about weld flash. We covered what weld flash is, its function, types of weld flash, and steps to minimize it. We also discussed factors influencing weld flash, typical issues, aftercare, use cases, and some alternatives. Many welders also need to understand the difference between 6010 and 6011 rods for effective welding.
So, what is weld flash? Simply put, it’s the discomfort and irritation caused by bright welding light on unprotected skin and eyes. We looked at how exposure can lead to issues like flash burns and the importance of proper gear. If you need additional advice, I’m here to help you understand and prevent these effects safely.
For further insights and resources on welding techniques, feel free to explore What is Welding.
References
- British Standards Institution. (2018). BS EN ISO 9606-1: Qualification Testing of Welders. London, UK: BSI.
Tyler is a passionate DIY welder and self-taught metal artist with years of hands-on experience transforming raw materials into functional and artistic creations. Specializing in MIG welding, Tyler crafts everything from custom furniture to outdoor sculptures, blending creativity with technical skill. Committed to making welding accessible, Tyler shares practical insights and project inspiration to help beginners and hobbyists confidently explore the world of metalworking.
12V Battery, Eye Protection, Filler Metal, Flash Burn, MIG Welding, UV Radiation, Weld Flash, Welding, Welding Hazards, Welding Safety, Welding Techniques