What Items Make Up a Basic Semiautomatic Welding System?
Published on: January 30, 2025 | Last modified: March 4, 2025
By: Joe Carter
Welding tools, equipment setup, essential components
A semiautomatic welding system helps you weld materials with some automated assistance. This means you control the welding process while the system manages certain tasks like feeding the wire.
A frequent question I encounter is what items make up a basic semiautomatic welding system? It’s crucial to know these components for effective and safe welding. From experience, missing just one part can lead to frustrating results, and I’ve seen it happen too many times.
In this guide, I’ll cover important elements like the main components, types of semiautomatic welding systems, setup steps, factors affecting performance, common issues, and aftercare tips. I’ll also share different industry applications for semiautomatic welding systems. If you’re keen to learn what are the tools used for welding or what equipment is used in welding, you’re in the right place!
Contents
- What’s in a Basic Semiautomatic Welding System?
- What Items Make Up a Basic Semiautomatic Welding System?
- Types Of Semiautomatic Welding Systems
- Steps to Set Up a Semiautomatic Welding System
- Factors Affecting Semiautomatic Welding Systems
- Typical Issues for Semiautomatic Welding Systems
- Industry Applications for Semiautomatic Welding Systems
- Essential Accessories for Semiautomatic Welding Systems
- Are There Any Alternatives to Semiautomatic Welding Systems?
- Frequently Asked Questions (FAQs)
- Conclusion
- Additional Reading
What’s in a Basic Semiautomatic Welding System?
A basic semiautomatic welding system includes a welding machine, wire feeder, and protective gear. It’s often used in auto shops, construction sites, and metal fabrications for its efficiency and ease. They enable quick, quality welds with minimal effort. To explore specific practices and considerations, you might be interested in how to weld zinc plated steel.
What Items Make Up a Basic Semiautomatic Welding System?
A basic semiautomatic welding system consists of several key components. There’s the welding power source, welding gun, and wire feed system. The power source provides the necessary voltage and current, usually ranging from 150 to 350 amps for most projects. The wire feed system automatically feeds welding wire at a controlled speed of around 2 to 21 inches per minute (50 to 500 Mm/min).
A shielding gas tank is crucial as it protects the weld from oxidation. This gas is usually argon or a mix, ensuring a clean and strong weld joint. Understanding these components is essential for efficient work.
I recommend investing in a quality welding helmet with a high protection rating. Don’t skip a good pair of leather gloves; they’re lifesavers. A decent modulator can greatly enhance consistent feed and make your welds more reliable.
Types Of Semiautomatic Welding Systems
-
MIG Welding Systems
MIG welding (Metal Inert Gas) is popular for beginners. You’ll need a MIG welder, welding wire (Typically ER70S-6), a shielding gas cylinder (Like Argon), and a ground clamp. These components ensure a smooth welding process and high-quality welds.
-
Flux-cored Arc Welding Systems
Flux-cored arc welding (FCAW) uses tubular wire filled with flux. Your setup includes an FCAW welder, flux-cored wire (Like E71T-1), and a ground clamp. This equipment enables welding in windy conditions as the flux generates a protective gas. The numbers on a welding rod indicate its properties and capabilities, offering crucial information for different welding projects. For more details, explore what the numbers on a welding rod mean.
-
TIG Welding Systems
TIG welding (Tungsten Inert Gas) is known for precision and high-quality welds. You’ll need a TIG welder, tungsten electrodes (Such As E3), filler rods, and Argon gas for shielding. These items allow for intricate work and welding of thin metals.
-
Submerged Arc Welding Systems
Submerged arc welding (SAW) is ideal for thick materials and high productivity. You’ll require a heavy-duty SAW machine, continuous wire feed, flux, and a ground clamp. This setup creates clean, large welds without spatter.
However, while submerged arc welding minimizes direct exposure to the arc, understanding how to treat flash burn in your eyes from welding is crucial for safety.
-
Plasma Arc Welding Systems
Plasma arc welding (PAW) uses a plasma torch for superheated welding. To start, you’ll need a plasma welder, tungsten electrodes, and Argon gas. These components work together for precise and efficient welding, especially in thin sheet metals.
We’ve wrapped up the types of semiautomatic welding systems here. Next up, we’ll look at the setup steps for these systems.
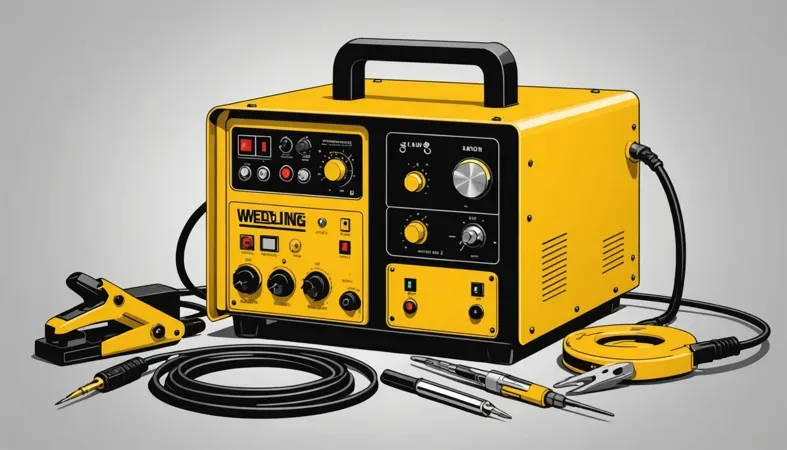
Steps to Set Up a Semiautomatic Welding System
Here are the steps to understand the components of a semiautomatic welding system.
-
Connect the Water Cooler
Start by connecting the water cooler to the welding machine. Most semiautomatic systems require cooling to prevent overheating, especially during prolonged welding. Use clean water—ideally distilled—to prolong your torch’s life. A flow rate of about 1.0 liter per minute is recommended to maintain a cool temperature.
Check the connections regularly. Leaks can reduce efficiency and damage your equipment. Use reinforced tubing for durability. Ensure you have a reliable pump to maintain smooth coolant flow; the setup should take no longer than 15 minutes.
-
Set Up the Welding Gas Supply
Next, connect the gas cylinder. Use shielding gas—usually argon or a mix with carbon dioxide. Secure the cylinder to prevent tipping. Open the cylinder valve slowly and adjust the regulator to between 10-20 psi for optimal flow during operation.
Ensure you have the correct fittings during setup. Poor connections can cause leaks, wasting gas and creating unsafe conditions. A good practice is to apply a soapy water solution to the connections after setup; bubbles indicate a leak.
-
Install the Torch and Electrode
Attach the welding torch to the cable assembly. This setup typically uses a MIG or TIG torch in semiautomatic systems—fit the proper contact tip for the wire diameter, usually around 0.8 to 1.2 mm (0.030 To 0.047 In). Ensure the electrical connection is tight to prevent misfires and ensure smooth wire feeding.
Before undergoing medical procedures like MRI, welders need to consider certain precautions related to metallic interference. Discover if a welder can get an MRI safely and what steps to take beforehand to ensure compatibility with diagnostic machines.
Adjust the spool tension before starting. Too much tension can create friction, leading to wire feed issues. It’s crucial to use the correct size and type of electrode for your welding job. Don’t overlook this step!
-
Position the Ground Clamp
Next, securely attach the ground clamp to the workpiece. This ensures an uninterrupted path for electrical current and prevents erratic starts. Find a clean, rust-free area for reliable conductivity, aiming for a ground clamp rating of at least 150A for better performance during lengthy jobs.
Ensure the clamp is firm to prevent resistance in the circuit. I once overlooked this and experienced poor weld quality due to voltage drops. A solid connection withstands vibrations and movement. Do a quick tug test to ensure it’s tight and secure.
-
Feed the Filler Wire
Finally, feed the filler wire into the torch. Measure about 1.5 meters (4.9 Ft) of wire to feed into the machine. Run the wire through the drive rolls, ensuring it fits snugly into the grooves. Adjust the tension in the rollers for smooth feeding without excessive pressure.
Be careful of debris or mishandling while feeding the wire. This can lead to issues later in your project. While it may seem tedious, ensuring even threading will save time and frustration during welding. A smooth wire feed significantly improves your welding quality.
That covers the steps to establish a semiautomatic welding system. Let’s now take a look at factors influencing semiautomatic welding systems.
Factors Affecting Semiautomatic Welding Systems
What factors influence the components needed for a semiautomatic welding setup?
-
Type Of Materials Being Welded
The material significantly impacts your welding setup. For example, mild steel requires different settings than aluminum, including lower voltage and faster travel speed.
-
Environmental Conditions
Welding outdoors? Wind can disrupt your shielding gas, leading to poor welds. A 5 mph (8 Km/h) wind can blow away shielding gas!
-
Operator Skill Level
I recommend investing in training for your welders. Skilled operators produce cleaner welds, reducing the need for rework and improving productivity.
-
Welding Techniques Used
Different techniques, such as stringer beads versus weave patterns, affect weld quality and penetration depth. Techniques also vary based on the semiautomatic welding system you use.
-
Quality Of Equipment
High-quality welding machines and tools increase efficiency and reduce defects. Investing in a good MIG (Metal Inert Gas) or TIG (Tungsten Inert Gas) machine often pays off in durability and reliability.
We have now covered elements influencing semiautomatic welding systems. Next, we will examine common challenges encountered with these systems.
Typical Issues for Semiautomatic Welding Systems
Let’s look at the unique challenges you might face with a semiautomatic welding system.
-
Inconsistent Welding Quality
Semiautomatic welding systems can lead to irregular quality. Check the feeder speed and wire diameter. Use a caliper to measure the wire within ±0.1 mm. Adjustments should be made based on the material type and thickness for consistency.
-
Equipment Malfunctions
Semiautomatic welding systems may have issues like wire feed jams. Regular maintenance every 50 hours is recommended. Use a suitable lubricant for welding machinery and clean the roller guide to avoid clogs.
-
Improper Settings Adjustments
In a semiautomatic welding system, incorrect voltage or amperage settings can cause defects. Always refer to material specifications and set the voltage between 18-26 V, depending on the wire type. Use a multimeter for accurate readings.
-
Welding Defects Such As Porosity
Semiautomatic welding systems can suffer from porosity due to trapped gases. Inspect for adequate shielding gas flow rates, ideally 20-25 CFH. Increase flow to prevent gas entrapment.
-
Contamination Of the Weld Area
In a semiautomatic welding system, contamination often results from dirty work surfaces. Clean your base metals with a wire brush and acetone. Aim for a surface cleanliness grade of at least ISO 8501-1.
We covered common challenges in semiautomatic welding systems. Next, we will explore their applications across various industries.
Industry Applications for Semiautomatic Welding Systems
I’ve seen people use semiautomatic welding systems for car repairs. However, they have many other applications, such as:
- Pipe Fabrication: Joins metal pipes in construction. It’s popular for its efficiency in high-volume projects.
- Automotive Manufacturing: Commonly used to assemble vehicle frames. This method offers durability and precision.
- Aerospace Components: Ideal for welding lightweight structures. Semiautomatic systems help meet strict safety standards.
- Shipbuilding: Used to fabricate hulls. It’s favored for its speed and capability to handle thick materials.
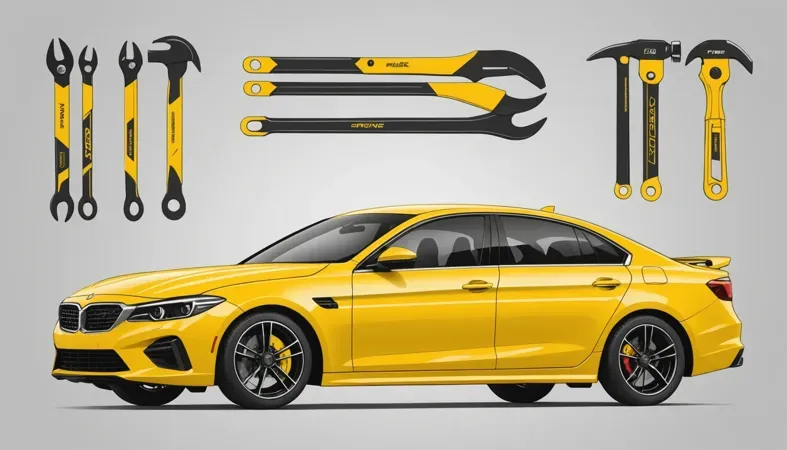
Essential Accessories for Semiautomatic Welding Systems
Besides the main components, various accessories can enhance your semiautomatic welding system.
Accessory | Description | Benefits | Typical Cost (USD) |
---|---|---|---|
Spool Gun | A tool for feeding welding wire, especially for aluminum. | Improves feed accuracy and reduces birdnesting issues. | 150 – 300 |
Welding Cart | A mobile cart to hold the welding machine and supplies. | Makes it easier to transport your setup around the workspace. | 100 – 250 |
Welding Lagging | Insulative cover for hot surfaces of the welder. | Promotes safety by reducing burn risk and heat loss. | 30 – 100 |
Fume Extractor | Device to filter harmful welding fumes. | Ensures a healthier working environment. | 200 – 1,000 |
Cuprum Cleaning Brushes | Brushes specifically designed for cleaning the welding nozzle. | Removes spatter and builds up for smoother operation. | 10 – 30 |
Investing in these accessories can save you time and enhance the quality of your welds. What’s your favorite accessory for welding?
Are There Any Alternatives to Semiautomatic Welding Systems?
Sure, there are other ways to achieve solid welds. Stick welding, also known as Shielded Metal Arc Welding (SMAW), is a popular alternative. You might prefer it for its simplicity and low cost, using equipment like the Lincoln Electric Stick Welder for versatile applications.
Gas Metal Arc Welding (GMAW), with products like the Miller Multimatic 215, is another option. It’s great for beginners and helps produce clean welds. Each method has unique advantages, so consider your project needs and budget before diving in! Identifying the root of issues such as what causes porosity in welding can also improve your welding outcome.
Frequently Asked Questions (FAQs)
Now let us look at some common questions I typically get asked.
What is a Semi-automatic Welder?
A semi-automatic welder is a type of welding machine that requires some manual operation but manages most tasks automatically. This setup typically uses Gas Metal Arc Welding (GMAW) technology for efficiency, allowing for extended operation times and a higher quality finish.
While welding technology continues to evolve, pushing the boundaries of what’s possible in construction and repair, it’s crucial to understand the specific hazards associated with specialized practices like underwater welding. Discover more about how dangerous is underwater welding.
What Components Make Up a GMA Welding System?
The components that make up a GMA welding system include a power source, a wire feeder, and the welding torch. These parts work together to provide steady power, deliver the filler wire, and control the welding arc. In specialized fields such as pipeline construction, welders often need to possess specific certifications and skills. For instance, B-pressure welding certification is essential for those working on high-pressure systems, ensuring weld quality and safety.
.
What Are the Basic Equipment Used in the Welding Process?
The basic equipment used in the welding process includes a welding machine, welding electrode or filler material, protective gear, and clamps. Each piece plays a vital role in ensuring safety and quality during welding operations, especially the welding machine, which is central to the entire process.
It’s crucial to know how to address welding burns for effective first aid response.
What Tools Does a Welder Need?
A welder needs tools such as a welding helmet, gloves, and a chipping hammer. These tools protect the welder and help maintain workspace safety while removing slag after welding.
What Tools Are Used for Welding?
The tools used for welding can include torches, welding machines, and grinders. Each tool helps achieve specific tasks, from creating precise welds to cleaning welded joints for the best finish.
Which Of These is an Example Of Semiautomatic Welding?
An example of semiautomatic welding is the Gas Metal Arc Welding (GMAW) process. GMAW allows for a continuous feed of filler material while letting the welder control the movement and placement for optimal results.
Conclusion
We’ve covered a lot in this article. We discussed essential items like the welding machine, wire feeder, welding gun, shielding gas, and safety gear, among others. Each of these tools plays a critical role in setting up welding equipment for a semiautomatic welding system.
So, what items make up a basic semiautomatic welding system? Simply put, you need a welding machine, a wire feeder to supply the welding wire, a welding gun to direct the heat, shielding gas to protect the weld, and proper safety equipment like gloves and helmets. Feel free to reach out if you have further questions about welding and the gear used in the process.
To explore more insights and advice on welding, visit What is Welding.
Additional Reading
- Lincoln Electric. (2020). The Procedure Handbook of Arc Welding (15th ed.). Cleveland, OH: Lincoln Electric Company.
- American Petroleum Institute. (2018). API 1104: Welding of Pipelines and Related Facilities. Washington, DC: API.
- American Welding Society. (2018). AWS D14.3: Specification for Welding Earthmoving and Construction Equipment. Miami, FL: AWS.
Joe Carter is a retired welding professional with over 40 years of hands-on experience in the industry, spanning ship repair, structural welding, and even underwater projects. Joe is a master of MIG, TIG, and Stick welding. Passionate about mentoring the next generation of welders, Joe now shares his decades of expertise and practical insights to help others build rewarding careers in welding.
American Welding Society, MIG Welding, Semiautomatic Welding System, Voltage Drop, Welding, Welding Equipment, Welding Safety, Welding Tools, Welding Wire