How to Weld Without a Welder? Tips, Techniques, and Safety
Published on: March 1, 2025 | Last modified: March 4, 2025
By: Joe Carter
A welder is someone who joins pieces of metal using heat. It’s a skill that’s essential in many industries.
One thing people often ask me about is how to weld without a welder. It’s crucial to know because sometimes you may be in a pinch. I remember a time when I needed to fix something quickly, and having alternatives made all the difference in the world. Understanding the basics of welding fundamentals can also help in these situations.
In this guide, you’ll learn about the basics of welding without a welder, key types of methods, safety tips, steps to take, and unique challenges. We’ll cover factors to consider, useful alternatives, inspection practices, and the advantages of these techniques. If you’ve ever wondered how to weld aluminum without a welder or similar methods, this guide’s for you! Additionally, understanding specific welding guidance can enhance your skills and knowledge in this area.
Contents
- How to Weld Without A Welder?
- What is a Welder?
- Types Of Welders
- Essential Prerequisites to Get Started
- Safety Tips
- Steps for Welding Without a Welder
- Types Of Methods for Welding Without a Welder
- Factors to Consider When Welding Without a Welder
- Unique Issues
- Aftercare, Inspection, and Advanced Tips for Welding Without a Welder
- Why This is Worth It: Advantages
- Use Cases Of Welding Without a Welder
- Other Options for Achieving Welding Results
- Frequently Asked Questions (FAQs)
- Conclusion
- Additional Reading
How to Weld Without A Welder?
A welder is a tool that fuses materials, often metal. To weld without a welder, you can use alternatives like soldering, brazing or using adhesives. This method’s tricky and best for small projects like art or repairs. If you’re exploring the components that make up a GMA welding system, discover more in this comprehensive guide.
What is a Welder?
A welder is a skilled professional who uses high heat to fuse materials, primarily metals. They operate welding machines that can exceed 3,000°C (5,432°F). Types of welders include MIG, TIG, and Stick. According to the Bureau of Labor Statistics, over 370,000 welders were employed in the U.
S. as of 2021.
If you’re wondering how to weld without a welder, it’s tricky. You can use methods like soldering or brazing, which require lower temperatures but still effectively join metals. I’ve tried soldering for minor repairs, and it’s rewarding to get a good bond without heavy welding gear.
I once used an innovative method to repair my bike frame. I needed to fix a crack and used a strong adhesive, which felt like the perfect alternative. While it isn’t traditional welding, sometimes you have to ask, can I weld without a welder? Methods like this are handy when you lack access to welding equipment!
Types Of Welders
-
Stick Welders
Stick welders use a consumable electrode for welding. To join metal without this tool, use the cold welding method. Clean the surfaces thoroughly, press them together with extreme force, and apply heat if needed. If you’re interested in understanding similar welding configurations, explore basic semiautomatic welding systems.
-
MIG Welders
MIG welders continuously feed a wire for a strong bond. To weld metals without a MIG welder, use JB Weld or a bonding adhesive. Mix the adhesive according to package instructions and apply it to the metal surfaces that need joining.
-
TIG Welders
TIG welders utilize a non-consumable tungsten electrode for precise joints. To achieve a similar result without a TIG welder, consider using high-strength epoxy. Clean the metal, apply the epoxy, and allow it to cure following the instructions on the tube.
-
Flux-cored Arc Welders
These welders use hollow wire filled with flux to protect the weld. To connect metal without one, use flux-cored adhesive. Prepare your metals, apply the adhesive generously, and clamp them together until it sets. For effective welding processes, it’s essential to understand what gas is used for welding.
-
Multi-process Welders
Multi-process welders perform various types of welding in one machine. To weld without one, use metal bolts or rivets. Align the pieces, drill holes through both, and secure them using bolts and nuts or rivets for a solid connection. If you encounter issues with your welding machine and need guidance on repairs, check out this welding machine troubleshooting resource.
You should now have a good understanding of various welder types and their applications. In the next part, we’ll discuss necessary prerequisites for getting started.
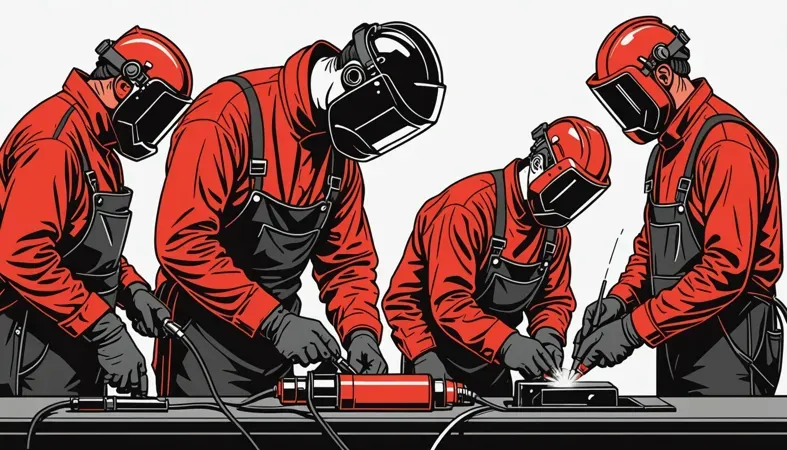
Essential Prerequisites to Get Started
What do you need to start welding without a welder?
- Cold Weld Adhesive: You’ll need a cold weld adhesive like JB Weld. It’s essential for bonding metals without heat.
- Aliens Metallouch: This method requires products that can fuse aluminum, such as Metallouch aluminum rods. It’s designed for strong connections when welding aluminum without a welder.
- Metal Prep Spray: You’ll need a spray like Rust-Oleum Weld-Through Primer. It ensures metal surfaces are clean and ready for bonding by preventing corrosion.
- Basic Clamps: Use clamps, like Irwin Quick-Grip Clamps, to hold your metal securely. This stabilizes the pieces for a better bond during the process.
So far we covered the vital prerequisites for getting started. Next, let’s look at important safety tips.
Safety Tips
Here are essential precautions for DIY welding techniques.
- Protective Gear: Always wear gloves and a welding mask to protect against sparks and eye damage.
- Ventilation: Ensure your workspace is ventilated. Fumes can be harmful, so use fans or work outside when possible.
- Flammable Materials: Keep flammable items away. A small fire can ignite quickly and cause serious damage.
- Sturdy Surface: Use a heavy, stable base. This prevents slipping and keeps your work steady on a sturdy tabletop or the ground.
Always prioritize safety—taking risks isn’t worth it! I’ve lost too much sleep over bad welds.
We covered safety recommendations, precautions, and best practices here. Next, we will cover methods for welding without a welder.
Steps for Welding Without a Welder
Here are the steps to weld metal without a welder. Follow them closely.
-
Choose the Right Method
Select a technique that suits your project. Cold welding is a strong option for clean metal surfaces, creating bonds as strong as traditional methods. This typically works on softer metals, like aluminum, which can be effectively joined using this method. When considering various welding methods, understanding the use of tri-mix gas provides deeper insights into enhancing weld quality for specialized projects.
First, make your metal surfaces spotless. Use a wire brush or sandpaper—aim for a smooth finish. A shiny surface enhances metal-to-metal contact, significantly improving bond strength.
-
Prepare Your Metal Pieces
Trim and shape your metal pieces as needed. Aim for at least a 1 inch (2.54 cm) overlap for stronger joints. Use a hacksaw or metal snips for precise cuts, and clean the edges afterward to ensure a good weld. To achieve a smooth finish, learn about techniques for cutting welds.
Align the pieces tightly and clamp them together. Tight clamping ensures a firm bond and prevents gaps, which can weaken the weld and affect stability.
-
Apply Heat Using a Torch
Use a propane torch to heat the metal. The required temperature varies—heat aluminum to around 2000°F (1093°C) to start melting. Keep the torch moving to avoid burning through the metal, pointing it at the joint between the two pieces.
As you heat, wait for the metal to glow slightly, indicating it’s ready to bond. Once it glows, quickly bring the two pieces together, positioning them tightly for metal fusion.
-
Use Filler Material (if Necessary)
A filler rod can strengthen the joint, especially for thicker materials. Choose a filler compatible with your base metal—aluminum requires an aluminum filler. Heat the filler rod as you apply it to the joint, letting it melt and bond the metals together.
Move quickly and maintain a steady hand. Let the joint cool naturally—don’t rush, as quick cooling can create weak spots. Patience is key!
You should now have a good understanding of techniques, materials, and safety for welding without a welder. In the next part, we’ll discuss various methods for this process.
Types Of Methods for Welding Without a Welder
Let’s explore the methods: Oxy-Acetylene Welding, Brazing Techniques, Adhesive Bonding Methods, and Soldering Techniques.
-
Oxy-acetylene Welding
Oxy-acetylene welding creates a flame by burning acetylene gas in oxygen. This method reaches temperatures up to 3,500 °C (6,332 °F), hot enough to melt metals. It’s effective for welding steel and certain alloys, allowing you to fuse materials without a traditional welder.
-
Brazing Techniques
Brazing joins metals by melting a filler material above 450 °C (842 °F) without melting the base metals. The filler flows into the joint through capillary action, forming a strong bond. It’s ideal for welding aluminum without a welder, as it works with various materials effectively.
If you’re looking to explore more DIY methods, discover how to make a welding machine using a 12V battery.
-
Adhesive Bonding Methods
Strong adhesives can bond metals without heat. Epoxy and polyurethane adhesives provide excellent shear strength, with some achieving over 6,000 psi (Pounds Per Square Inch). Adhesive bonding excels in situations where traditional welding isn’t viable, especially for thin materials.
-
Soldering Techniques
Soldering melts a filler metal, such as tin-lead, at lower temperatures, usually around 180-260 °C (356-500 °F). Common in electronics, it can also join thin metal sheets effectively. Soldering is a reliable method for joining metal without a welder, especially in delicate tasks. In contrast, welding often requires inert gases to shield the weld zone, and one critical component is argon in welding applications.
-
Mechanical Joining Methods
Mechanical joining uses fasteners like bolts, nuts, or screws to secure metal pieces together. This straightforward method requires no heat or special materials. If you’re wondering, “Can I weld without a welder?” mechanical joining offers a strong solution for many projects. However, if you’re interested in exploring more advanced welding techniques, you might want to consider learning about DC inverter welding machines.
Factors to Consider When Welding Without a Welder
What factors affect your ability to fuse metals without a typical welding machine?
-
Material Type
Different metals require various approaches. For instance, aluminum melts at around 660°C (1220°F), while steel melts at about 1370°C (2500°F). Identify the metal and adjust your method accordingly.
-
Joint Design
How pieces fit together matters. A V-joint design increases surface area for better bonding, while a lap joint may reduce strength. Choose designs that provide a good mechanical interlock or increased surface contact.
-
Heat Application
When applying heat, use a suitable source, like a propane torch, and maintain a consistent temperature. Overheating can weaken or warp materials, while insufficient heat prevents joints from fusing.
-
Skill Level
Your experience matters. Novices may struggle with flow and control, while experts understand heat zones and material interactions. Practicing on scrap can build essential skills before tackling real projects.
-
Tools and Equipment
Using the right tools is vital. You can use a propane torch or even J-B Weld in some cases. The method you choose must fit the task, as some alternatives may not provide the needed strength.
Unique Issues
Let’s examine unique technical problems affecting welders.
-
Limited Strength Of Joints
Weak welds may lead to joint failure. Gaps appear when mated parts aren’t flush. Use a gauge; it’s crucial. To fix this, apply adequate filler and ensure proper heat settings—typically in the 25–30 volt range.
-
Increased Risk Of Contamination
Welders face contamination risks from oil, rust, or paint. Visually inspect and clean surfaces. Here’s what to do: grind the area and apply a cleaner. A clean joint ensures a strong joint.
-
Difficulty Achieving Consistent Results
Inconsistency greatly affects weld quality. Variations in amperage or travel speed can create weak spots. Use a digital meter to check settings and follow standard procedures for each weld pass.
-
Potential for Warping
Warping is a serious problem for welders. Excessive heat applied too quickly causes this. To prevent it, use a lower heat setting and maintain a steady, even weld pattern.
-
Air Quality Concerns During Welding
Welding can produce harmful fumes. Check for proper ventilation to protect your lungs. Use a respirator when necessary; it’s essential for avoiding long-term health issues.
Aftercare, Inspection, and Advanced Tips for Welding Without a Welder
Here are essential aftercare, inspection, and expert tips to ensure your connections last.
Aftercare Tips
After you’ve bonded metals without a welder, clean up immediately. Use a wire brush to remove any slag or dirt from the joints. Apply a rust deterrent, like WD-40, to protect against corrosion in humid environments. For those needing to undo metal bonds, understanding how to remove welds can be a critical skill.
Inspection Checks
Start inspection by checking joint strength visually—any gaps over 1 mm (0.04 In) are a concern. Use a magnifying glass to find fine cracks, especially after stress testing. I trust my DAP Premium Construction Adhesive; it holds well and withstands heat fluctuations.
Expert Tips
From one expert to another, consider preheating your metal to about 150°C (300°F). This reduces thermal stress during bonding without a traditional welder. Test your joints by applying torsion; a quarter turn should reveal flaws. When using adhesives, ensure a uniform thickness of 0.5 mm (0.02 In) for maximum strength across the surface area.
Why This is Worth It: Advantages
The biggest perk of knowing how to weld without a welder is flexibility. I used it to help a friend patch his car’s frame, saving us both time and money.
Additionally, this skill opens up new possibilities. You can work in tight spaces, tackle quick repairs, enhance your creativity with alternative materials, and save on equipment costs.
Use Cases Of Welding Without a Welder
I’ve seen people use techniques for metal joining without a welder. These methods have various applications:
- Puddle Welding: Used for small repairs, like fixing thin sheets of metal on appliances. It’s popular because it doesn’t require heavy equipment and can handle minor fixes.
- Brazing: Common for joining copper pipes in HVAC systems, it’s often preferred for creating strong joints without excessive heat. Many contractors appreciate its versatility.
- Soldering: Essential for electrical connections, especially in circuit boards. It’s popular among electronics repair shops because it’s easy to do without a welder.
- Adhesives: In automotive applications, they effectively bond dissimilar materials. Many designers use them to reduce wear on parts, avoiding welding altogether.
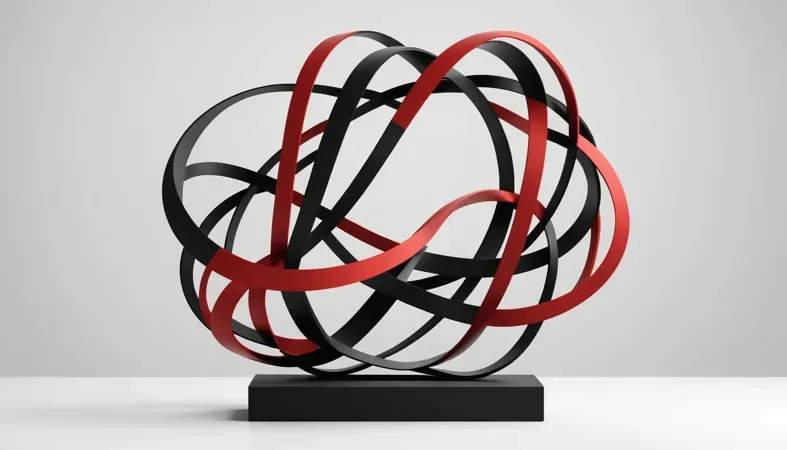
Other Options for Achieving Welding Results
There are several alternatives to achieve similar results as welding. For instance, you might consider using Cold Welding, which bonds two metal surfaces together without heat. Over time, I’ve observed that JB Weld epoxy works wonders, especially for small repairs, providing a strong hold, similar to a weld, without the bulk of a Welding Machine.
If you’re dealing with aluminum, products like 3M’s AFD Tape can create solid joins for light applications without a welder. These options come in handy, particularly when you’re working in tight spaces or need a quick fix. So, can you get the job done without a welder? Absolutely!
Frequently Asked Questions (FAQs)
Now let us look at some common questions I typically get asked.
What Can I Use to Weld Without a Welder?
To bond metal without a welder, you can use metal adhesives or epoxy. Some epoxies can withstand temperatures of up to 150 °C (302 °F) and provide strength comparable to traditional welds, making them suitable for light repairs.
How Do You Bond Metal Without a Welder?
You can bond metal by using adhesives or mechanical fasteners. Adhesives like epoxy can bind metals together effectively, achieving good tension and shear strength, while fasteners like screws can provide a strong hold for heavier applications.
Is Metal Glue As Strong As Welding?
Metal glue can be strong but it usually isn’t as strong as welded joints. Some metal glues can reach bond strengths between 5,000 to 10,000 psi, while welded designs often exceed these, especially under load. It’s suitable for lightweight projects.
What is the Easiest DIY Welding?
The easiest DIY welding is low-temperature metal soldering. This method doesn’t require a welding machine and uses soldering iron, allowing users to join thin metal sheets at temperatures below 400 °C (752 °F). Ideal for hobbies or minor repairs.
Can I Weld Without a Welder?
Yes, you can weld without a welder by using alternative joining methods like soldering or brazing. While not as strong as welding, these methods can create durable connections when done properly, depending on application and load requirements.
How to Weld Aluminium Without a Welder?
You can weld aluminium without a welder using techniques like brazing or using metal adhesives. These methods are simpler and can bond aluminium at lower temperatures, but require proper cleaning to ensure good adhesion or a strong bond.
Conclusion
We’ve reached the end, and I appreciate you sticking around. We covered what a welder is, different types of welders, essential prerequisites to get started, and various methods for welding without a welder. We also touched on safety tips, factors to consider, unique issues, aftercare, and even the advantages of welding without traditional equipment.
So, how do you weld without a welder? You can use metal adhesives, forging methods, or mechanical fastening techniques. With options like these, plus the right tools and safety practices, you can successfully join metal without a welder and achieve solid results in various projects.
If you’re eager to explore more topics related to welding and enhance your knowledge, feel free to visit our homepage at What is Welding for additional expert blogs and valuable advice.
Additional Reading
- ISO. (2017). ISO 3834: Quality Requirements for Fusion Welding of Metallic Materials. Geneva, Switzerland: ISO.
- Kou, S. (2003). Welding Metallurgy (2nd ed.). Hoboken, NJ: Wiley.
Joe Carter is a retired welding professional with over 40 years of hands-on experience in the industry, spanning ship repair, structural welding, and even underwater projects. Joe is a master of MIG, TIG, and Stick welding. Passionate about mentoring the next generation of welders, Joe now shares his decades of expertise and practical insights to help others build rewarding careers in welding.
Adhesive Bonding, DIY Techniques, Metal Bonding, Safety Tips, Soldering, Welding, Welding Alternatives, Welding Applications, Welding Techniques