What is Tri-mix Welding Gas Used for? – Applications, Types, and Usage
Published on: February 24, 2025 | Last modified: March 4, 2025
By: Mark Carter
Tri-mix welding gas is a combination of three gases: argon, helium, and carbon dioxide. This blend enhances welding performance and produces better-looking welds.
I often hear people ask what is tri-mix welding gas used for? It’s crucial to understand its applications. In my experience, using tri-mix can significantly improve the quality of welds, especially in stainless steel and other exotic metals.
In this guide, we’ll dive into how tri-mix welding gas works, different types of tri-mix gases, steps for using it effectively, factors that affect its usage, common issues you might encounter, and tips for aftercare. We’ll also explore its applications and when you might need to consider alternative options. If you’ve ever wondered what is welding gas, you’re in the right place.
Contents
- What is Tri-mix Welding Gas Used for?
- How Does Tri-mix Welding Gas Work?
- Types Of Tri-mix Welding Gases
- Steps for Using Tri-mix Welding Gas
- Factors Affecting Tri-mix Welding Gas Usage
- Common Issues You Might Encounter
- Benefits of Using Tri-mix Welding Gas
- Applications Of Tri-mix Welding Gas
- When to Try a Different Approach
- Frequently Asked Questions (FAQs)
- Conclusion
- References
What is Tri-mix Welding Gas Used for?
Tri-mix welding gas primarily combines argon, helium, and carbon dioxide. It’s ideal for welding stainless steel and non-ferrous metals, improving arc stability and reducing spatter. Many welders prefer it for its versatility in various applications.
How Does Tri-mix Welding Gas Work?
Tri-mix welding gas is a mixture commonly used in MIG (Metal Inert Gas) welding. It typically contains three gases: Argon, Carbon Dioxide (CO₂), and Helium, in the ratio of 90% Argon, 7.5% CO₂, and 2.5% Helium. This combination improves arc stability and penetration, resulting in high-quality welds on stainless and mild steel.
Using tri-mix produces cleaner welds with less spatter. The inert gases shield the weld area from contamination, which is critical when working with reactive materials.
If I were you, I’d choose tri-mix for precise, strong welds on stainless steel. I’ve used it in my projects, and the quality speaks for itself. Understanding tri-mix welding gas can save you time and money in welding operations.
Types Of Tri-mix Welding Gases
What are the types of tri-mix welding gases and how are they used?
Helium-based Tri-mix
Helium-based tri-mix contains argon, helium, and carbon dioxide. This blend produces a cleaner weld with less oxidation. Use it for aluminum and stainless steel to achieve better heat distribution and smooth arcs in high-precision applications. For welders working on specific steel types it is crucial to understand E316-16 electrode classification.
Argon-based Tri-mix
Argon-based tri-mix typically features argon, carbon dioxide, and sometimes oxygen. This mix enhances penetration and bead shape while reducing spatter. Optimize this gas for mild steel by aiming for a faster travel speed and maintaining a steady arc for consistent results.
Carbon Dioxide Inclusion
This type includes carbon dioxide. It improves arc stability and can be cost-effective. For effective MIG welding, keep your torch angle between 10-15 degrees and maintain a solid wire feed speed to control weld quality.
Oxygen Addition
Oxygen addition enhances arc stability and tightens the focus of the weld. It’s mainly used for specific applications, like joining thin materials. To leverage this effect, add a minimal amount of oxygen to maintain control and avoid excessive oxidation.
Other Gas Mixtures
Other gas mixtures may include various gases for different purposes. These can vary based on metal type and project. To customize your blend, analyze the metal’s properties and desired weld characteristics for optimal performance.
We have now covered the different types of tri-mix welding gases. Next, we will examine the steps for using tri-mix welding gas.
Steps for Using Tri-mix Welding Gas
Here are the steps for effectively using tri-mix welding gas.
Prepare the Welding Area
Clear the workspace of flammable materials. Ensure good ventilation; airflow helps remove fumes. Aim for a minimum airflow of 25 cubic feet per minute (Cfm) or 0.012 m³/s to keep the area safe.
Set up a sturdy table to stabilize your workpiece. If you’re working with stainless steel or aluminum, avoid mixing materials to prevent contamination. Ensure proper grounding with a 2 AWG copper wire for optimal conductivity. Different types of welding rods are essential to achieve successful welds and enhance metallurgical properties, and you can explore what welding rods are made of for more technical insights.
Mix the Gases Appropriately
For tri-mix welding gas, combine argon, helium, and carbon dioxide in specific ratios. A common mix is 90% argon, 7.5% helium, and 2.5% CO₂, which delivers smooth arc stability and minimizes spatter.
If you’re welding mild steel, you can increase the CO₂ ratio slightly for improved penetration. Getting these ratios right significantly affects your weld quality and strength.
Set Up the Welding Machine
Adjust your MIG welding machine settings based on the tri-mix gas you’ve prepared. For a standard 1/8 inch (3.2 Mm) steel plate, set the voltage to 20-22 volts and the wire feed speed to 260-300 inches per minute (Ipm) or 6.6-7.6 meters per minute (Mpm) for optimal fusion. For more precise welding tasks, understanding the cost of welding rods can be beneficial.
Double-check connections and flow gauges for leaks before starting. I’ve encountered weak welds due to slight leaks, so checking helps avoid complications. After setup, monitor the flow rate, aiming for 25-30 cubic feet per hour (Cfh) or 0.012-0.014 m³/h.
Start the Welding Process
Begin by striking an arc on the workpiece. Use steady motion when feeding the filler metal along the seam. Maintain a travel speed of about 6-12 inches per minute (Ipm) or 15.2-30.5 cm/min for a smooth bead.
Pace yourself; overheating can occur quickly. If the metal starts to sag, slow down! Keep a consistent distance from the nozzle to the workpiece, about 8-10 millimeters, to maintain bead shape and prevent issues.
That covers the steps for using tri-mix welding gas. Let’s now take a look at the factors affecting tri-mix welding gas usage.
Factors Affecting Tri-mix Welding Gas Usage
What factors influence the use of tri-mix welding gas in projects?
Welding Material Types
Different materials require specific welding gases. For example, stainless steel often needs a tri-mix of argon, helium, and carbon dioxide for optimal results.
Weld Joint Configuration
The design of the weld joint impacts the gas choice. A narrow gap requires effective shielding gas to prevent oxidation and ensure a strong bond.
Environmental Conditions
Consider how environmental factors, like wind or humidity, affect the effectiveness of tri-mix welding gas. High winds can blow away the shielding gas, compromising weld quality.
Operator Skill Level
The welder’s experience matters. A skilled operator can efficiently adjust parameters, achieving better results with tri-mix gas than a novice.
Gas Flow Rates
Gas flow rates must match the welding process. Standard flow rates range from 15 to 25 cubic feet per hour (425 to 708 Liters/hour), ensuring proper shielding without wasting gas.
We covered the factors influencing tri-mix welding gas usage. Next, we will cover common issues you might encounter.
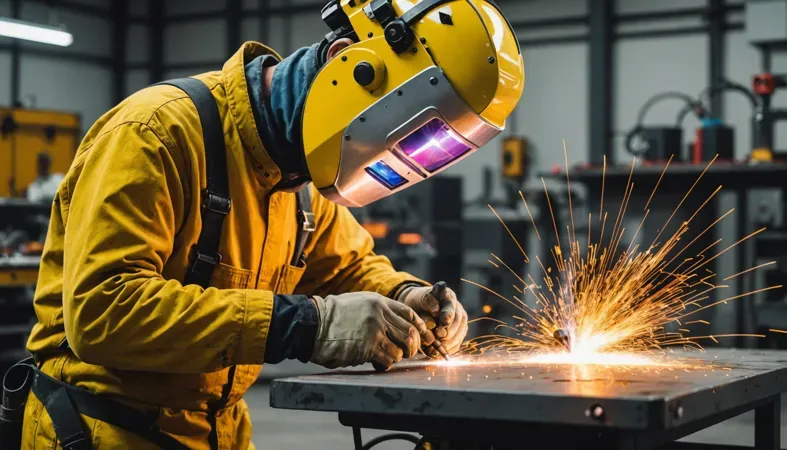
Common Issues You Might Encounter
Let’s look at unique problems with tri-mix welding gas.
Gas Mixture Imbalance
Tri-mix welding gas can have an improper mixture of argon, helium, and carbon dioxide. Watch for changes in arc brightness or weld puddle visibility. If it’s off, check the gas flow rates and adjust them to 90/10 (Ar/co₂) or as specified for your task. For those curious about arc intensity, explore how bright a welding arc.
Inconsistent Arc Stability
Tri-mix welding gas may cause unstable arcs. Focus on the gas flow and check for blockages in the nozzle. A consistent flow leads to a stable arc, resulting in cleaner welds.
Excessive Spatter Production
Tri-mix welding gas can lead to increased spatter. Look for solder balls on the workspace; they signify excessive spatter. Adjust your contact tip-to-work distance, keeping it about 1/4 in (6 Mm) above the workpiece.
Difficulties in Cleanup
Using tri-mix welding gas might leave more residue. If you notice residue, plan to use cleaning tools after each session to avoid buildup. Conventional brushes usually suffice.
Welding Porosity Problems
Tri-mix welding gas can introduce porosity in your welds. Pinholes or bubbles indicate moisture or contamination. Keep the welding area clean and dry, and store your gas properly!
Benefits of Using Tri-mix Welding Gas
Tri-mix welding gas isn’t just a blend; it offers several advantages.
Improved Arc Stability
You’ll notice better arc stability with tri-mix gas. This means smoother welding and fewer defects.
Enhanced Penetration
Tri-mix provides deeper penetration. It’s great for thicker materials, ensuring strong welds.
Minimized Spatter
Using tri-mix reduces spatter. Less cleanup saves you time, letting you focus on your work.
Versatility in Applications
This gas blend works well for different materials—stainless steel, aluminum, and more. It fits various jobs easily.
Cost-Effectiveness
Though it might seem pricier upfront, the quality and efficiency can save you money in the long run. Think about the savings in materials and labor!
Applications Of Tri-mix Welding Gas
I’ve seen people use tri-mix welding gas for precision welding projects. It has several applications, such as:
- Aerospace Manufacturing: It’s used to weld critical aircraft components. The mix minimizes oxidation, ensuring a clean weld crucial for high-stress environments.
- Marine Fabrication: Tri-mix gas is popular for underwater welding. It provides strong, corrosion-resistant joints on ships and offshore structures.
- Cryogenic Applications: It’s ideal for welding cryogenic tanks and pipes. The gas settings address the unique challenges of these materials.
- High-End Automotive Projects: Specialty cars use this gas for aluminum and stainless steel welding, ensuring aesthetic quality and long-lasting durability.
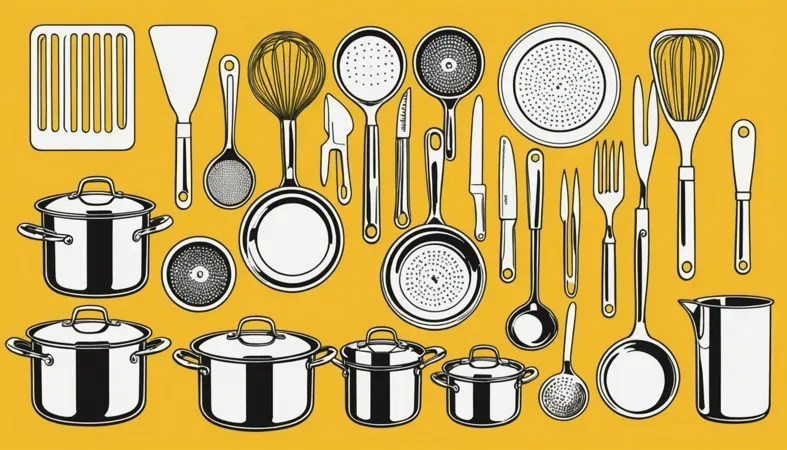
When to Try a Different Approach
If you’re looking for alternatives to tri-mix welding gas, consider using pure argon or a helium-argon blend. These options might be preferred for specific materials, such as aluminum or thin stainless steel, where you want to minimize heat input. After countless attempts and adjustments, I’ve figured out that a 90/10 argon/CO2 mix works well for general steel applications. To achieve the best welding results, it is essential to source high-quality metal and you can explore different options on where to buy metal for welding.
You could also explore options like C10 or A1025 welding gases, especially when tackling diverse projects. Each gas can have its pros and cons, often dependent on the metals and thickness involved. To ensure optimal performance, consider the right welding equipment for your specific welding needs!
Choosing the right method for your projects can be vital, and understanding different techniques can help enhance your outcomes. Discover more about seam welding processes to optimize your welds.
Frequently Asked Questions (FAQs)
Now let us look at some common questions I typically get asked.
What is the Alternative to Tri-mix Welding Gas?
Yes, the alternative to tri-mix welding gas includes gases like 100% argon or argon-CO2 mixtures. These alternatives offer varying arc stability and penetration depth, depending on the material. For example, 75% argon and 25% CO2 is popular for steel welding.
What is the Best Gas Mix for MIG Welding?
The best gas mix for MIG welding is typically 75% argon and 25% CO2. This mix enhances arc stability and minimizes spatter. It’s a great choice for welding thick steel sections, providing excellent penetration without burning through the material.
When mistakes happen during welding projects, it’s crucial to know how to effectively remove unwanted welds.
Which Gas Mixture is Used for Steel Welding?
For steel welding, a common gas mixture is 90% argon and 10% CO2. This mix improves weld bead appearance and provides good penetration on mild steel. A flow rate of 12-20 L/min (0.4-0.7 Cubic Feet/min) is recommended. Many welders face issues with imperfections such as porosity which can compromise weld integrity. It’s crucial to understand what causes porosity in welding to ensure high-quality results.
What is an Inert Gas in Welding?
An inert gas in welding is a gas that doesn’t react with the molten metal, like argon or helium. This helps prevent oxidation and contamination during the welding process. Using such gases improves weld quality and strength significantly. In specialized fields, understanding the potential dangers of underwater welding can enhance safety protocols.
What is Dry Ice Used for in Welding?
Dry ice, or solid carbon dioxide (−78.5°C), is often used for cooling or reducing heat distortion in welded sections. It serves as a quick way to solidify welds in delicate operations. Applying dry ice can help maintain accuracy in a weld structure.
Conclusion
We’ve covered a lot about tri-mix welding gas in this article. We’ve gone over its applications, how it works, the types of gases involved, and steps for using it. We also looked at factors affecting its usage, common issues you might face, and essential aftercare tips.
I trust these insights have been helpful in answering what is tri-mix welding gas used for. In short, tri-mix welding gas is ideal for MIG welding of stainless steel and other alloys, providing excellent arc stability and reduced spatter. Key mixtures typically include 90% argon, 7.5% helium, and 2.5% CO2, ensuring optimal performance for your welding projects.
For more valuable information and the latest articles on welding techniques and tips, feel free to return to our homepage at What is Welding.
References
- American Welding Society. (2020). AWS C5.6: Recommended Practices for Gas Metal Arc Welding. Miami, FL: AWS.
Mark is a skilled welding engineer specializing in advanced metal joining technologies and process design. With a formal education in welding engineering and a background rooted in practical experience, Mark bridges the gap between theory and application. He is passionate about making technical concepts accessible, empowering welders to embrace innovation while mastering essential skills. Mark combines his scientific expertise with a commitment to supporting the welding community alongside his uncle, Joe.
American Welding Society, Filler Metal, Gas Mixtures, MIG Welding, Stainless Steel Welding, Tri-mix Welding, Welding, Welding Gas Applications, Welding Techniques