What Components Make Up a GMA Welding System? – Key Parts Explained
Published on: February 18, 2025 | Last modified: March 4, 2025
By: Joe Carter
The Gas Metal Arc (GMA) welding system is a popular method for joining metals. It uses a continuous electrode and a shielding gas to create strong, clean welds.
So, what components make up a gma welding system? It’s crucial to know each part, as each plays a role in the welding process. In my experience, missing even one component can lead to poor welds or equipment failure.
In this article, I’ll cover how a GMA welding system operates, its various types, steps for setup, factors that influence the components, common problems, inspection tips, applications, and alternatives. You’ll even learn about terms like what is globular transfer welding. Stick around for all the details!
Contents
- What Components Make Up a GMA Welding System?
- How Does a GMA Welding System Work?
- Types Of GMA Welding Systems
- Steps for Setting Up a GMA Welding System
- Key Accessories for an Effective GMA Welding System
- Factors Influencing GMA Welding System Components
- How to Address Frequently Encountered Problems
- Applications You Should Know About
- What Are the Alternatives to GMA Welding Systems?
- Frequently Asked Questions (FAQs)
- Conclusion
- Additional Reading
What Components Make Up a GMA Welding System?
A GMA welding system includes a power source, a welding gun, and filler metal. This setup efficiently joins metals using an arc between the electrode and workpiece. For those looking to understand more about the essential components of welding equipment, it’s often used in automotive and construction due to its speed and versatility.
Welding can have unexpected health effects, and one concern is whether it can cause skin damage similar to sunburn. For detailed information, explore the sunburn risks associated with welding.
How Does a GMA Welding System Work?
A GMA (Gas Metal Arc) welding system consists of key components: a power source, welding wire, shielding gas, and a welding gun. The power source, adjustable between 250-500 Amps, supplies electricity to melt the wire. The welding wire feeds through the gun and fuses with the workpiece. Shielding gas, usually argon or a mix of argon and CO2, protects the weld from atmospheric contamination.
.
With these components and proper settings, you can achieve strong, clean welds under various conditions. Data shows that GMA welding improves travel speed by 25-50% compared to traditional methods.
.
I’ve been down this road before, and managing the components of a GMA welding system is crucial for successful outcomes. Understanding each part, such as the role of shielding gas, can help you avoid defects. You don’t want to end up with a bad weld, especially on projects like a Can-Am X3 weld-in gusset kit!
Types Of GMA Welding Systems
MIG Welding Systems
MIG welding, or Metal Inert Gas welding, uses a continuous wire feed. For a GMA MIG setup, you’ll need a wire feeder, MIG gun, shielding gas supply, grounding clamp, and power source; they’re crucial for completing the circuit.
TIG Welding Systems
TIG welding, or Tungsten Inert Gas welding, employs a non-consumable tungsten electrode. To set up a GMA system for TIG, start with a TIG torch, tungsten electrode, and shielding gas system. The power source should be adjustable for different materials and thicknesses.
Pulsed MIG Welding Systems
Pulsed MIG combines MIG with on-and-off pulses of current. For a GMA pulsed MIG system, you’ll need a standard MIG setup plus a pulsing control feature integrated into the power source. Ensure the wire feed speed and pulse settings are fine-tuned for optimal results.
Short Circuit MIG Welding Systems
This type uses a short-circuiting transfer method for welding. In a GMA setup for short circuit MIG, you’ll need a specific short-circuiting MIG gun and a power source that supports low voltage and high current. This ensures a stable arc and better control over weld penetration. When engaging in these methods, it’s crucial to consider the hazards involved in welding.
Multi-process Welding Systems
Multi-process welding systems can perform several welding types. To configure a GMA system for multi-process welding, you’ll need a versatile power source along with interchangeable welding torches and wires to switch between MIG, TIG, or stick welding. This provides flexibility across different projects.
We’ve wrapped up the various types of GMA welding systems here. Next up, we’ll look at the steps for setting up a GMA welding system.
Steps for Setting Up a GMA Welding System
Now, we’ll cover the steps detailing the components of a GMA welding system. These steps are crucial for setting everything up correctly.
Select Your Welding Voltage
Start by choosing the right welding voltage. For GMA welding, you’ll typically adjust between 18 and 35 volts. The ideal voltage depends on the thickness of your material; thinner materials often require lower settings. Using improper voltage can lead to issues like undercutting or poor penetration.
When welding galvanized steel, it’s crucial to understand the potential health risks involved as improper handling can be dangerous, and you can learn more about the hazards associated with welding galvanized steel.
Increasing the voltage also affects the arc length. Many beginners struggle with maintaining consistent voltage while welding. Set it and check it often.
Choose Wire Feed Speed
Adjust your wire feed speed to ensure a stable arc. Speeds usually range from 300 inches per minute (Ipm) to 700 ipm (About 7620 Cm/min to 1780 Cm/min). Higher speeds can lead to burn-through on thinner metals, while slower speeds may cause a lack of penetration. It’s a balance, and you’ll find it with practice.
A suitable speed for mild steel is around 400 ipm (1016 Cm/min). If you get it wrong, you’ll waste wire or damage your workpiece. Keep that setting dialed in!
Set Up the Shielding Gas
Determine your shielding gas mix. For carbon steel, a mixture of 75% argon and 25% CO2 usually works well. If you stray too far from these ratios, you can get poor bead shape. Don’t overlook the gas flow rate, which should be set between 15 and 25 cubic feet per hour (Cfh), depending on your setup.
Excessive flow can create turbulence, while inadequate flow won’t protect the weld pool effectively. Check this before starting to weld.
Connect the Ground Cable
Next, connect the ground clamp securely to your workpiece. This helps establish a clean electrical circuit for effective welding. A loose ground can lead to poor arc starts and spatter. Always use a solid connection; clean any rust and paint from the attachment spot.
To ensure proper safety protocols, explore what happens when observing welding from afar.
A good practice is to clamp it to the same side you’re welding. This reduces issues with arc stability on larger projects. Don’t skip this—it’s critical!
Adjust Your Travel Speed
Finally, set your travel speed. Typically, a speed of 5 to 15 inches per minute (Ipm) works for most applications, but it varies with material and weld joint. Travel too fast, and the weld becomes weak with incomplete fusion; too slow, and you risk burn-through.
Experiment with your torch angle and travel speed, adjusting until you find the sweet spot for your setup. Getting this right makes all the difference in bead quality.
We’ve wrapped up the steps for establishing a GMA welding system here. Next up, we’ll look at essential accessories for an effective GMA welding system.
Key Accessories for an Effective GMA Welding System
Beyond the main components, several key accessories enhance a GMA welding system’s performance.
Accessory | Purpose | Specifications |
---|---|---|
Welding Nozzles | Directs shielding gas and protects the welding tip. | Sizes: 0.8 mm (0.03 inch) to 2.0 mm (0.08 inch) |
Contact Tips | Conducts electrical current to the welding wire. | Material: Copper Alloy; Diameters: 0.6 mm (0.023 inch) to 1.6 mm (0.062 inch) |
Gas Regulators | Controls the flow of shielding gas. | Pressure Range: 0-30 psi (0-207 kPa) |
Wire Feed Rollers | Controls the feeding of the welding wire into the nozzle. | Sizes: 0.8 mm (0.030 inch) and 1.0 mm (0.035 inch) roller grooves |
Ground Clip | Connects the workpiece to the power source to complete the circuit. | Clamp Type: Heavy-duty, at least 8 AWG (American Wire Gauge) |
Each accessory plays a crucial role. For instance, if your nozzle isn’t properly sized, you might get gas turbulence, which can ruin your weld. So, always match your accessories to your specific application for the best results!
That covers essential accessories for a successful GMA welding setup. Let’s now take a look at the factors affecting GMA welding components.
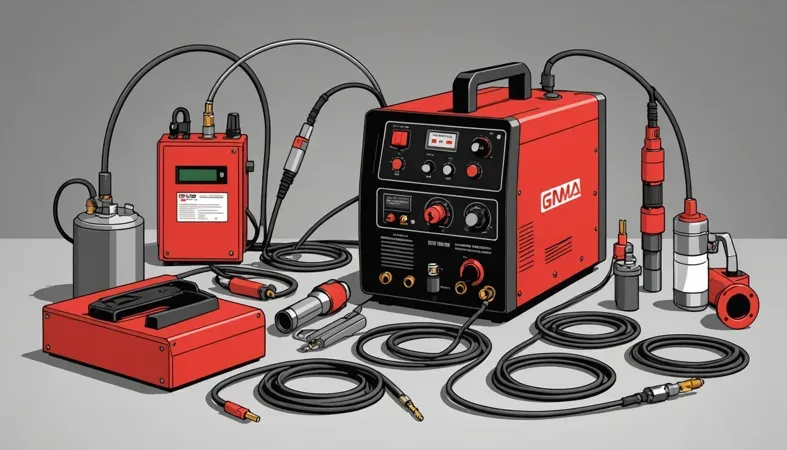
Factors Influencing GMA Welding System Components
What factors affect the components of a GMA welding system?
Welding Material Types
Different materials require specific welding approaches. For instance, steel needs different settings than aluminum.
Welding Power Supply Rating
The power rating affects arc stability and penetration. A 300 amp (A) power supply suits thick materials, while a 150 A works for thinner ones.
Gas Mixture Composition
The gas mixture can significantly change weld quality. A mix of argon and CO2 is common; 75% argon and 25% CO2 yields good results.
Nozzle Design
A well-designed nozzle ensures proper gas flow. Choosing the right size—like 15 mm (0.6 Inch) vs. 25 mm (1 Inch)—affects heat distribution and bead appearance.
Current Settings
The amperage setting directly impacts heat input. Typically, a 1 A increase raises temperature by about 10°F (5.5°C) per inch of material thickness.
That covers the elements affecting GMA welding system components. Let’s now take a look at solving common issues encountered.
How to Address Frequently Encountered Problems
Let’s look at some common issues with the GMA welding system.
Contact Tip Burnback
The GMA welding system may experience contact tip burnback. Look for burnt electrodes or inconsistent wire feed. If this occurs, clean the contact tip and adjust the distance to prevent the issue.
Insufficient Penetration
Insufficient penetration can happen with the GMA welding system. It’s often due to low heat or travel speed. Increase your amperage (Around 50-70 A for Steel) and ensure a proper travel speed.
Welding Spatter Issues
You might notice excess spatter when using the GMA welding system. Look for pockmarks on your work. Adjust your voltage settings and ensure the shielding gas flow is set properly at about 15-20 CFH (Cubic Feet Per Hour).
Poor Gas Coverage
Poor gas coverage can affect the GMA welding system. If you see oxidation on the weld, your gas settings may be off. Increase flow rates and check for leaks to improve coverage.
Weld Contamination
Weld contamination is a challenge with the GMA welding system. Ensure no oils or rust are present on the surface. Clean thoroughly before welding to avoid this issue.
Applications You Should Know About
People commonly use GMA welding systems in automotive manufacturing, but they also have many practical applications, including:
- Robot Welding: Used on assembly lines for high-precision tasks. This application is popular for its speed and accuracy.
- Pipe Fabrication: Ideal for welding pipes in construction. GMA systems deliver clean welds, minimizing rework—often essential for compliance.
- Thin Sheet Metal Welding: Perfect for HVAC systems. It offers excellent control over thin materials, ensuring integrity and aesthetics.
- Automotive Repairs: Great for restoring frames and body panels. Many prefer GMA for its versatility and consistent results on various metals.
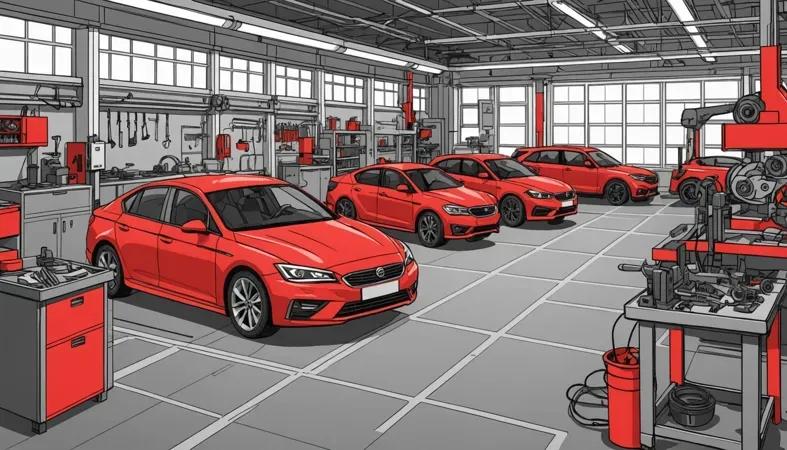
What Are the Alternatives to GMA Welding Systems?
There are viable alternatives to achieve similar results as the GMA welding setup. For example, using TIG welding is one option, particularly for thinner materials where precision is key. In heavy-duty applications, stick welding, like the Lincoln Electric 225, may excel due to its durability and ease of use in outdoor settings. When selecting suitable materials for these welding techniques, it’s crucial to know where to purchase metal that meets the specific project requirements.
If there’s one thing I’ve gained from my journey, it’s that selecting the right welding method can depend on your project’s specifics. Another choice, MIG welding with a Hobart Handler, offers a great balance of convenience and performance for general metalworking tasks. Weigh the pros and cons to find what suits you best! For projects involving both creating and dismantling metal joints, understanding how to cut welds efficiently is crucial to maintaining high-quality standards.
Frequently Asked Questions (FAQs)
Now let us look at some questions I typically get asked regarding GMA welding systems.
What Does ‘G’ Mean in a Welding Symbol?
The letter ‘G’ in a welding symbol stands for groove. Groove welds are joint designs requiring a specific shape to hold two pieces together. Understanding these symbols helps ensure accurate welds and adherence to specifications in projects.
What is Globular Transfer Welding?
Globular transfer welding is a welding process involving the transfer of molten metal droplets from the electrode to the workpiece. This method is typically used in carbon dioxide (CO2) welding and becomes effective at currents between 150 A to 250 A. Globular transfer aids in creating deeper weld penetration.
What is a Girth Weld?
A girth weld is a type of butt weld used primarily in joining two pipes end-to-end. It typically appears in pipeline applications, especially for accommodating stresses due to movement. Girth welds are crucial for ensuring pipeline integrity and preventing leaks.
What is a Gusset in Welding?
A gusset in welding refers to a triangular plate that strengthens a joint, often used in structural applications to provide additional support. Gussets help distribute loads, and their use can significantly improve structural integrity in frames and bridges.
What is the Process Of GMA Welding?
The GMA welding process, or Gas Metal Arc welding, involves creating an arc between a continuously fed consumable electrode and the workpiece. This process is known for its speed and versatility and is widely used in automotive and manufacturing industries for efficiency. Selecting the appropriate welding rod to use enhances the overall effectiveness of the welding technique.
What Parts Of a Typical GMA Welding Gun Can Be Replaced?
In a typical GMA welding gun, parts like nozzles, body, liners, and contact tips can be replaced easily. Maintaining these components optimizes performance and ensures quality welds, which is vital for successful long-term operations.
Conclusion
We covered several components that make up a GMA welding system, including the power source, wire feeder, welding gun, shielding gas, and various accessories. Additionally, we discussed how GMA welding works, different system types, setup steps, and factors influencing these components. Don’t forget the importance of aftercare and common troubleshooting techniques, as well as knowing alternative welding systems.
So, what components make up a GMA welding system? In summary, it includes a power source to generate the necessary voltage, a wire feeder to supply the welding wire, and a welding gun for directing heat and filler material. Plus, shielding gas is vital for protecting the weld area. If you have more questions about GMA welding or need help on related topics, don’t hesitate to get in touch for further assistance.
For additional expert insights into welding techniques and systems, be sure to visit What is Welding.
Additional Reading
- ISO. (2017). ISO 3834: Quality Requirements for Fusion Welding of Metallic Materials. Geneva, Switzerland: ISO.
- Richardson, R. (2010). MIG Welding Guide. Cambridge, UK: Woodhead Publishing.
- American Welding Society. (2021). AWS B2.1: Standard for Welding Procedure and Performance Qualification. Miami, FL: AWS.
- Smith, D. L. (2010). Welding: A Journey to Explore Its History. Dubuque, IA: Kendall Hunt Publishing Company.
Joe Carter is a retired welding professional with over 40 years of hands-on experience in the industry, spanning ship repair, structural welding, and even underwater projects. Joe is a master of MIG, TIG, and Stick welding. Passionate about mentoring the next generation of welders, Joe now shares his decades of expertise and practical insights to help others build rewarding careers in welding.
American Welding Society, Gas Metal Arc Welding, GMA Welding, MIG Welding, Welding, Welding Equipment, Welding Setup, Welding System Components, Welding Techniques, Wire Gauge