What Kind Of Welder Do I Need? Your Guide to Types, Selection, and Applications
Published on: November 19, 2024 | Last modified: March 4, 2025
By: Mark Carter
A welder is a skilled tradesperson who fuses materials, usually metals, using heat. They create strong joints in structures or parts by melting the edges together.
I often hear people ask what kind of welder do I need? This question matters because the right welder can make or break your project. I remember when I started out; picking the wrong welder wasted my time and money.
In this guide, we’ll explore what types of welders are available, how to choose the right one for your needs, factors that affect your choice, and how to tackle common issues. We’ll also cover tips on aftercare and inspection, applications of welders in different industries, and alternatives to traditional welding. Everything you need to know about selecting the welder that fits your project and lifestyle is included, whether you’re wondering what welder should I buy or what to get a welder for Christmas.
Contents
- What Kind Of Welder Do You Need?
- How Does ‘What Kind Of Welder Do I Need?’ Work?
- Types Of Welders
- Steps for Choosing a Welder
- Understanding Welder Specifications
- Factors Affecting Welder Selection
- How to Address Common Problems
- Applications Of Welders in Various Industries
- Are There Any Alternatives to Traditional Welding?
- Frequently Asked Questions (FAQs)
- Conclusion
- Additional Reading
What Kind Of Welder Do You Need?
Choosing a welder depends on your projects. MIG is great for beginners, while TIG offers precision for metal arts. Stick is used in construction due to its versatility.
How Does ‘What Kind Of Welder Do I Need?’ Work?
The phrase ‘what kind of welder do I need?’ refers to understanding the specific equipment for your projects Welding Machines – The Home Depot. First, determine the materials you’ll weld. Do you plan to use steel or aluminum? MIG (Metal Inert Gas) welders are great for beginners and typically run on 230 V (Voltage). MIG welders can handle thicknesses up to about 0.25 inches (6.35 Mm).
Choosing the right welder isn’t just about power; it’s also about aesthetics. Consider if you’re looking for deep penetration, speed, or clean bead appearance. These factors greatly affect your final product.
I can’t stress how crucial it is to pick the right welder. When I was starting, I ignored this and ended up with a machine I barely used! If you’re asking ‘what type of welder do I need?’ make a list of your projects—you might discover you’re ready to tackle DIY furniture or automotive repairs.
Types Of Welders
What types of welders are available?
-
MIG Welders
MIG (Metal Inert Gas) welders use a continuous wire feed. If you want quick, clean welds, this may be your choice. Start with a MIG welder like the Hobart Handler 140, suitable for materials up to 0.25 inches (6.35 Mm) thick. It is crucial to prioritize safety during welding processes to prevent health hazards, especially concerning eye protection. You might wonder about the risks associated with welding without adequate eye protection.
-
TIG Welders
TIG (Tungsten Inert Gas) welders create precise welds with excellent control. If you need high-quality welds on thin metals, consider the Miller Diversion 180. Practice your technique on scrap metal first.
Eye protection is vital during welding to prevent injuries and if accidents happen, it’s crucial to treat flash burns effectively.
-
Stick Welders
Stick welders use a welding rod to join metal parts. They’re perfect for outdoor jobs where wind could be a factor. To start, try the Everlast Power Arc 140, effective on rusted or dirty metals. For those beginning their welding journey, discovering where to find welding metal is essential.
-
Flux-cored Welders
Flux-cored welders are like MIG welders but use a hollow wire filled with flux for self-shielding. They’re ideal for thick materials and outdoor work. For beginners, consider the Lincoln Electric PRO-MIG 140, a reliable option for various tasks.
In welding, mastering different passes like a root or cap pass is essential for a strong joint and completing a proper hot pass can significantly enhance weld penetration and quality. To further explore what is a hot pass in welding, this resource will be useful.
-
Submerged Arc Welders
Submerged arc welders use granular flux to shield the weld, keeping it clean and strong. This type is great for long, straight welds on thick materials. For effective use, invest in a machine like the Miller Matic 350P, known for its productivity. To safely observe welding processes from afar refer to guidance on viewing welding from a distance.
So far we covered the various types of welders. Let’s look at the steps involved in selecting a welder next.
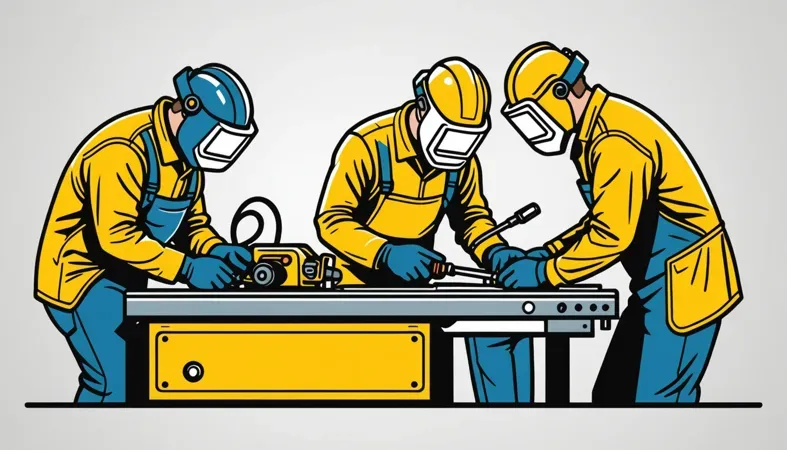
Steps for Choosing a Welder
Here are actionable steps to determine the welder that’s right for you.
-
Identify Your Welding Needs
Start by determining what you need the welder for. Are you fixing a fence, building a car, or something else? Each task may require a different type. For example, a home project might use a MIG welder, while a TIG welder is better for thin materials.
Understanding your project’s requirements is crucial. Consider the materials you’ll work with — mild steel vs. aluminum. Not all welders handle both well, so it’s important to choose the right equipment. Knowing your needs upfront, including the types of welding machines compatible with your materials, saves time and money in the long run.
-
Choose the Welder Type
Next, decide on the type of welder you’ll need: MIG, TIG, or Stick. MIG welders (Metal Inert Gas) are user-friendly and versatile, making them great for beginners. TIG welders excel in precision, while Stick welders are robust for outdoor tasks. Choosing the right technique is crucial for quality work but understanding how to remove welds can be equally important in various projects.
Check your power sources too. Do you have 120V (120 Volts) or 240V (240 Volts) available? This can narrow down your options significantly. If you’re a beginner, I recommend starting with a MIG for its simplicity.
-
Evaluate Your Skill Level
Your experience is important when selecting a welder. If you’re new, a MIG welder is the best choice. Its ease of use helps you learn quickly without frustration.
It’s vital to choose a welder that matches your skill level. Don’t force yourself to use a TIG welder if you’re just starting. Stick welders can also be challenging. Select what feels manageable.
-
Determine Your Budget
Set a budget before purchasing your welder. Prices range from $200 to over $1,500 (USD). High-quality machines often have features that improve welding but can be expensive.
Balance your needs and budget. I’ve seen people overspend on features they never use. Stick to your budget while ensuring quality. It pays off in the long run.
-
Check for Versatility and Future Use
Consider whether you’ll expand into other projects later. Some welders can perform multiple processes. A multi-function welder covers MIG, TIG, and Stick welding, offering flexibility as you learn.
Think about your long-term goals. If you plan to tackle more intense projects, investing in a machine that evolves with you might be wise. Look for units that allow upgrades or additional accessories.
We have now covered the process of selecting a welder. The next section will focus on understanding welder specifications.
Understanding Welder Specifications
Knowing welder specifications is key to making the right choice. Here’s a breakdown of important specs to consider:
Welder Type | Power Input | Welding Process | Max Material Thickness | Best Use Case |
---|---|---|---|---|
MIG Welder | 120/240 V | MIG | 0.25 in (6.35 mm) | General DIY and metal fabrication |
TIG Welder | 120/240 V | TIG | 0.125 in (3.18 mm) | Precision welding for thin metals |
Stick Welder | 120/240 V | Stick | 0.75 in (19.05 mm) | Outdoor construction and repair |
Flux-Cored Welder | 120/240 V | Flux-Cored | 0.5 in (12.7 mm) | Thick materials and outdoor work |
Submerged Arc Welder | 240 V | Submerged Arc | 1 in (25.4 mm) | Heavy industrial applications |
Choosing the right welder starts with understanding these specifications. Remember, each type comes with its strengths tailored for different project needs. So, what will you be welding?
We covered welder specifications, types, and features here. We will now cover factors influencing welder selection.
Factors Affecting Welder Selection
What factors influence your choice of welder? Let’s break it down simply.
-
Project Scope
Your project size matters. For small tasks, a MIG welder is often sufficient, but larger projects may need a stick or TIG welder. Don’t underestimate the scale—getting this right matters.
-
Material Thickness
Material thickness is important. If you’re working with steel thicker than ¼ inch (6.35 Mm), a stick or TIG welder typically provides more power. For thinner materials, a MIG welder usually works well.
-
Welding Position
Welding position affects your choice. Overhead and vertical positions may require more versatile welders like MIG or TIG to maintain quality. Some welders excel in flat positions but struggle elsewhere.
-
Power Supply Availability
Check your power supply. Most MIG welders operate at 120-240 V, while some stick welders can run on 110 V or generators. If you’re in a remote area, choose a welder that accommodates the available power.
-
Portability Needs
Portability matters if you need to move around. For on-site jobs, a lightweight MIG or inverter welder is ideal, while larger units may be best for fixed locations. Always choose one that suits your workspace.
We’ve wrapped up considerations like experience, skill level, and project requirements here. Let us turn our attention to tackling frequent issues.
How to Address Common Problems
Let’s look at issues unique to welders.
-
Inconsistent Arc Quality
Inconsistencies can lead to poor arc stability. You’ll notice if the arc jumps or hisses. Check your settings, adjust the voltage (Usually 18-26 V), and ensure the contact tip is clean. Dirty leads can also worsen the problem.
-
Welding Overheating
Overheating can hamper your work. Keeping your machine within its duty cycle, typically around 60%, is crucial. If it needs frequent breaks, let it cool down.
-
Electrode Sticking
If the electrode sticks, there’s likely not enough voltage. Increase the amperage, inspect the base material, and ensure you’re using the correct electrode type.
-
Poor Penetration
Lack of penetration often leads to weak joints. Check the heat settings; they may need to be 20-30% lower. Consider a slower travel speed as well.
-
Welding Contamination
Contamination can trap impurities and create defects. Look for discoloration in your weld bead and ensure surfaces are clean—free from oils or rust—before starting.
Applications Of Welders in Various Industries
Welders serve a variety of purposes in different jobs, including:
- Automotive Repair: MIG welders are great for car bodywork. Their speed and ease of use make them popular for fixing frames and panels.
- Structural Steel Fabrication: Stick welders excel at joining thick steel plates in construction. They’re sturdy and perform well outdoors.
- Pipeline Welding: TIG welders are the preferred choice for oil and gas pipelines. They create strong, precise welds crucial for safety and efficiency.
- Artistic Metal Sculptures: Oxy-acetylene welders help artists join metals for unique sculptures. Their portability and flame control are ideal for creative projects.
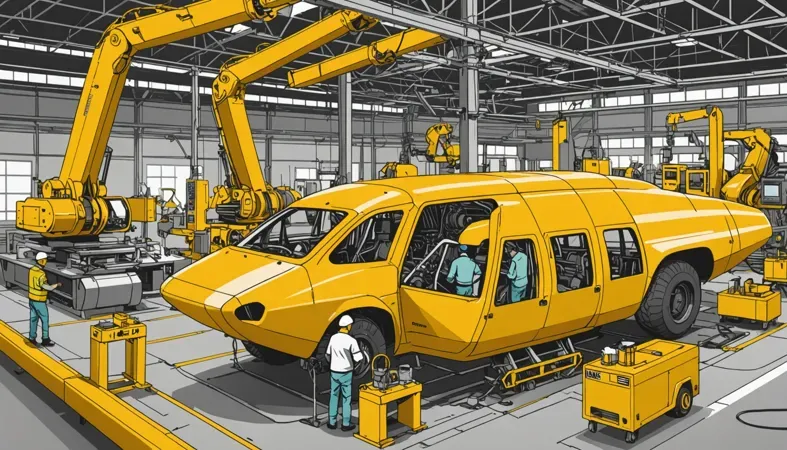
Are There Any Alternatives to Traditional Welding?
Ever thought about alternatives to using a welder? You’ve got options like adhesive bonding or brazing. Products such as Loctite Epoxy can create strong joints, and sometimes, they’re preferred for lighter materials or where you need a smooth finish.
Another route is soldering, especially for electronics. You might use a soldering iron like the Weller WLC100 for small, delicate jobs. I’ve often found that these methods can save time and provide excellent results when traditional welding isn’t suitable.
Frequently Asked Questions (FAQs)
Now let us look at some common questions I typically get asked about welding.
How Do I Know What Welder to Use?
You know what welder you should use by considering your project’s material and thickness. For instance, MIG welders are great for steel up to 5 mm (0.2 In), while TIG works better with thin materials like aluminum.
What Type Of Welder is Best for Home Use?
The best type of welder for home use is usually a MIG welder. It’s easy to use, great for various materials, and works well for hobbyists or DIY projects.
What is the Best Type Of Welding for Beginners?
The best type of welding for beginners is MIG welding. It’s forgiving, simple to learn, and requires less skill than TIG or stick welding, making it great for new welders.
Is a MIG or TIG Welder Better for Beginners?
A MIG welder is better for beginners compared to a TIG welder. MIG welding allows for faster welding speeds and requires less precision, which is less intimidating for someone new to the craft.
How to Choose a Welder for a Specific Project?
You choose a welder for a specific project by assessing the materials you’re working with. Consider factors like material type—whether it’s steel, aluminum, or stainless steel—and thickness to find the optimal welder for your needs.
What Safety Gear Do I Need While Welding?
You need safety gear while welding including a welding helmet, gloves, and protective clothing. Wearing appropriate welding equipment protects you from harmful sparks and ultraviolet radiation during the welding process.
Choosing the right equipment makes a significant impact on your safety and effectiveness, especially when considering what kind of welder suits your needs.
Can I Rent a Welder Instead Of Buying One?
Yes, you can rent a welder instead of buying one. Many hardware stores offer rental services, which can cost around $50 to $100 (USD) per day, making it a budget-friendly option for short-term projects.
How Often Should I Practice Welding?
You should practice welding regularly to improve your skills. Even just a few hours each week can noticeably enhance your techniques, helping you become more confident and efficient over time.
Conclusion
We’ve covered a lot in this article, including the different types of welders, steps for choosing a welder, factors affecting your selection, and common problems you might face. We also looked at aftercare, inspection tips, and applications of welders across various industries. Alternatives to traditional welding and frequently asked questions were part of our journey too.
So, what kind of welder do you need? Essentially, it boils down to your specific projects. If you’re working with thicker metals, you might want a MIG or TIG welder, while for lighter tasks, a stick welder could do the trick. Think about your needs and the material types—steel, aluminum, or something else—years of practice, and thousands of options make your choice easier. When you know your materials and tasks, picking the right welder gets simpler.
For further exploration and deeper insights into the world of welding, visit What is Welding.
Additional Reading
- ISO. (2017). ISO 3834: Quality Requirements for Fusion Welding of Metallic Materials. Geneva, Switzerland: ISO.
- American Welding Society. (2021). AWS B2.1: Standard for Welding Procedure and Performance Qualification. Miami, FL: AWS.
Mark is a skilled welding engineer specializing in advanced metal joining technologies and process design. With a formal education in welding engineering and a background rooted in practical experience, Mark bridges the gap between theory and application. He is passionate about making technical concepts accessible, empowering welders to embrace innovation while mastering essential skills. Mark combines his scientific expertise with a commitment to supporting the welding community alongside his uncle, Joe.
Adhesive Bonding, American Welding Society, MIG Welder, MIG Welding, TIG Welder, Types Of Welders, Welding, Welding Projects, Welding Techniques, Welding Tips