What is Metal Fabrication and Welding? Discover Processes, Techniques, and Applications
Published on: February 4, 2025 | Last modified: March 4, 2025
By: Joe Carter
Metal fabrication is the process of shaping and assembling metal parts. It includes cutting, bending, and joining metals to create structures or products.
If you’re curious about what is metal fabrication and welding, you’re in the right place. It’s crucial to understand these processes because they form the backbone of many structures we rely on, from bridges to machinery. In my experience, following the right techniques can make all the difference in safety and durability.
In this guide, you’ll learn about what metal fabrication and welding involves, how it works, the various types, essential steps in the process, factors influencing success, unique challenges, aftercare, inspection tips, and its applications in everyday life. You’ll also discover the difference between welding and metal fabrication, helping you grasp the full picture.
Contents
- What is Metal Fabrication and Welding?
- How Does Metal Fabrication and Welding Work?
- Types Of Metal Fabrication
- Techniques in Metal Fabrication and Welding
- Steps to Perform Metal Fabrication and Welding
- Factors Influencing Metal Fabrication and Welding
- Unique Issues in Metal Fabrication and Welding
- Aftercare, Inspection, and Advanced Tips for Metal Fabrication and Welding
- Applications Of Metal Fabrication and Welding
- When to Try A Different Approach
- Frequently Asked Questions (FAQs)
- Conclusion
- References
What is Metal Fabrication and Welding?
Metal fabrication combines processes like cutting, bending, and assembling to create metal structures. Welding joins pieces of metal using heat or pressure. You’ll see this in cars, buildings, and various machinery due to its strength and versatility. When considering the cost-effectiveness of different welding projects, it’s essential to understand how much welding rods cost.
How Does Metal Fabrication and Welding Work?
Metal fabrication and welding create structures from metal parts. Fabrication includes cutting, shaping, and assembling metal, often with tools like lasers and shears. Welding joins metal pieces by melting them together, commonly using methods like MIG (Metal Inert Gas) or TIG (Gas Tungsten Arc Welding). Did you know the welding industry contributes nearly $50 billion annually to the U.
S. economy?
To succeed in this field, you need specialized skills and knowledge of materials. Parts must fit perfectly; for example, a fabricator-welder may work with steel, aluminum, or titanium. Each material has unique properties, and understanding these significantly impacts quality.
If I were you, I’d invest time in learning welding techniques. Knowing what a fabricator-welder does will strengthen your skills in metalwork. Understanding the difference between welding and metal fabrication can also give you a competitive edge in the industry.
Types Of Metal Fabrication
What are the types of metal fabrication?
-
Laser Cutting
Laser cutting uses focused laser beams to slice through metal. It’s essential for metalwork because it offers precision and detail. To perform laser cutting, you’ll need a laser cutter, set the material thickness, and select the right power level for clean edges.
-
Press Brake Forming
Press brake forming shapes metal sheets by bending them. This process is vital for creating angles and complex parts. To bend metal, align your sheet, select the right die, and apply controlled pressure until you achieve the desired angle.
-
Sheet Metal Fabrication
Sheet metal fabrication involves cutting, bending, and assembling metal sheets. It’s crucial for making ducts, enclosures, and chassis. To fabricate sheet metal, start by cutting it to size, then bending at precise angles, and finally welding or assembling the parts.
-
TIG Welding
TIG welding uses a non-consumable tungsten electrode to join metals. This technique is essential for high-quality welds on thin materials. To perform TIG welding, adjust your current settings, clean the parts, and maintain a steady hand while moving the electrode along the joint.
-
MIG Welding
MIG welding uses a continuously fed wire electrode and gas to join metals. It’s popular for its speed and versatility. To start MIG welding, set up your machine, select the wire type, and control your feed and speed settings for clean welds.
You should now have a good understanding of various metal fabrication methods. In the next part, we’ll discuss techniques in metal fabrication and welding.
Techniques in Metal Fabrication and Welding
Let’s dive into specific techniques that enhance fabrication and welding processes.
Technique | Description | Applications | Advantages |
---|---|---|---|
Plasma Cutting | Uses a high-velocity jet of ionized gas to cut through metal. | Industrial parts cutting, art pieces. | Fast and precise, works on thick materials. |
Laser Cutting | Employs a focused laser beam to slice metal with extreme precision. | Signage, automotive components. | High precision, minimal waste. |
Spot Welding | Joins metals by applying heat and pressure to localized areas. | Automotive assembly, appliances. | Fast, efficient for thin sheets. |
Oxy-Acetylene Welding | Uses a flame produced by burning acetylene and oxygen to melt metals. | Metal art, plumbing, and repairs. | Versatile, can weld various metals. |
Filler Metal Techniques | Involves adding filler metal during welding processes to strengthen joints. | Pipe welding, structural supports. | Improves joint strength and stability. |
You should now have a good understanding of methods in metal fabrication and welding. In the next part, we’ll discuss procedures to perform these techniques.
Steps to Perform Metal Fabrication and Welding
Here are the steps for metal fabrication and welding to guide your project.
-
Identify Project Requirements
Start by understanding your goals. Gather specifications like dimensions, weight, and intended use. You might need to consult an engineer based on the project. Clearly defining these requirements can save hours of work later.
Consider any limitations or challenges you might face. Is your project for indoor or outdoor use? This choice affects material selection, as weathering can impact structural integrity. For outdoor projects, opt for corrosion-resistant metals like stainless steel.
-
Select Appropriate Materials
Choosing the right materials is crucial. Common options include aluminum, carbon steel, and stainless steel. Aluminum weighs about 2.7 g/cm³ (0.0975 Lb/in³), while carbon steel is about 7.85 g/cm³ (0.284 Lb/in³). Your material should align with your project requirements.
Consider factors like strength, weight, and cost. Also, think about how easy it is to weld the material; for example, stainless steel requires a different approach than aluminum. Make sure you’re comfortable with the welding guidance for your chosen material.
Knowing the specifics such as how many 1/8 7018 rods are needed can also assist in planning your project efficiently.
-
Prepare Materials for Fabrication
After selecting your materials, prepare them for fabrication by cutting and shaping the metal parts accurately. Use the appropriate cutting tool: plasma cutters for metal over 1/16 inches (1.6 Mm) thick or a band saw for thinner materials. Achieving precision in shaping is crucial for projects involving thin metals, which require specific techniques to ensure strength and stability; you can find details by exploring welding thin metal.
Clean your materials to remove contaminants. Rust or grease can affect weld quality; a clean surface ensures a strong bond. Use a grinding wheel or sandpaper to achieve a smooth surface.
-
Execute Fabrication Processes
Now, bring everything together through fabrication. This involves bending and assembling metal parts using welding methods like MIG (Metal Inert Gas) or TIG (Tungsten Inert Gas). MIG is quicker for large surfaces, while TIG offers more precision for detailed work.
Follow the correct temperature settings. For mild steel, maintain a range of about 1400°F to 1600°F (760°C to 870°C) for optimal fusion. Pay attention to how parts fit together; gaps can create weak joints that compromise your project’s integrity.
We covered steps for metal fabrication and welding here. Next, we will cover factors that influence these processes.
Factors Influencing Metal Fabrication and Welding
What factors affect metalwork and joining techniques? Here are some key variables.
-
Material Thickness
Materials range from 0.5 mm (0.02 In) to over 25 mm (1 in). Thicker metal requires more heat and time, impacting the weld’s quality and integrity.
-
Welding Method
Techniques such as MIG, TIG, and SMAW offer unique benefits. Each method suits specific metal types and thicknesses, significantly influencing performance.
-
Heat Input
Monitor the heat closely. Excessive heat can warp the material, while insufficient heat can create weak bonds, affecting durability.
-
Joint Design
Effective joint design affects stress distribution. For instance, a butt joint requires precise alignment, which is critical for maximizing strength in fabrication.
-
Environmental Conditions
Conditions like temperature and humidity directly impact the welding process. For example, welding in cold temperatures can cause brittleness in certain metals, leading to failures.
You should now have a good understanding of the elements affecting metal fabrication and welding. In the next part, we’ll discuss distinctive challenges in these processes.
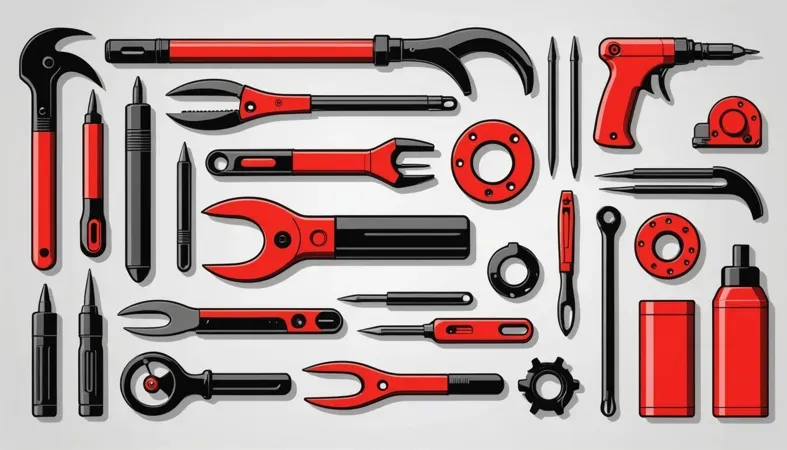
Unique Issues in Metal Fabrication and Welding
Let’s look at unique challenges in metal fabrication.
-
Weld Cracking Challenges
Weld cracking often occurs due to excessive stress or rapid cooling. You can identify it by visible cracks after welding. To resolve this, use preheating and ensure proper cooling rates—aim for temperatures around 21°C (70°F) before welding. Understanding the underlying issues such as what causes crater cracks in welding can help improve your approach to mitigating weld defects.
-
Heat Affected Zone Changes
The heat affected zone (HAZ) can weaken metal joints. Check the metallurgical properties affected by heat. Use localized cooling techniques, like water quenching, to minimize HAZ damage.
-
Distortion During Welding
Distortion during metal fabrication can warp or misalign parts. Visually inspect for misalignment after welding. To fix it, adjust joint designs and use proper fixturing to maintain alignment.
-
Material Compatibility Concerns
Ensure materials are compatible in metal fabrication. Dissimilar metals can cause weak bonds. Test coatings and filler materials suited to the metals involved. Check material data sheets before starting.
-
Surface Contamination Effects
Surface contamination can affect weld quality. Look for oil, rust, or dirt. Always clean surfaces before welding—methods include grinding or chemical cleanup.
Aftercare, Inspection, and Advanced Tips for Metal Fabrication and Welding
Here’s essential guidance on aftercare, inspection, and expert tips for metal fabrication processes.
Aftercare Tips
After installing fabricated components, let them cool naturally, aiming for no more than 50 °C (122 °F) per hour. Apply a corrosion inhibitor, like Rust-Oleum 773, for moisture resistance to extend the item’s life. Regularly inspect weld seams and transitions; cleanliness is key, so wipe surfaces with isopropyl alcohol to keep them free from contaminants.
Inspection
Inspecting weld penetration depth is critical. Use a caliper for millimeter (Mm) measurements to check depths for compliance (E.g., 1.2-2.4 Mm for Structural Integrity). Non-destructive tests (NDT), like ultrasonic testing, reveal defects without causing damage. I’ve successfully used a Sono Ace 800 for precise evaluations in past projects. Additionally, selecting the appropriate welding equipment can significantly affect efficiency and performance, particularly when considering the concept of duty cycle.
Expert Tips
Your routing of different materials directly affects final outcomes, so monitor thermal expansion; metals expand at different rates (E.g., Steel: 11.5 X 10⁻⁶/°C). Precision matters! Invest in a variable-speed rotary tool, like the Dremel 4000, for high-detail finishes. Always plan your heat sinks effectively to draw excessive heat away during fabrication, preventing warping of completed shapes.
Applications Of Metal Fabrication and Welding
I’ve seen metal fabrication and welding used in amazing projects. They have numerous applications, including:
- Aerospace Structures: Metal fabrication creates lightweight, strong parts for aircraft, ensuring safety and improving fuel efficiency.
- Custom Automotive Parts: Welders fabricate unique components for cars, like exhaust systems. This is popular for performance enhancements or restorations.
- Industrial Machinery: Metal fabrication strengthens manufacturing equipment, enhancing durability and keeping production lines running smoothly.
- Architectural Features: Welders create intricate metal railings and staircases, adding beauty and strength to buildings while ensuring safety.
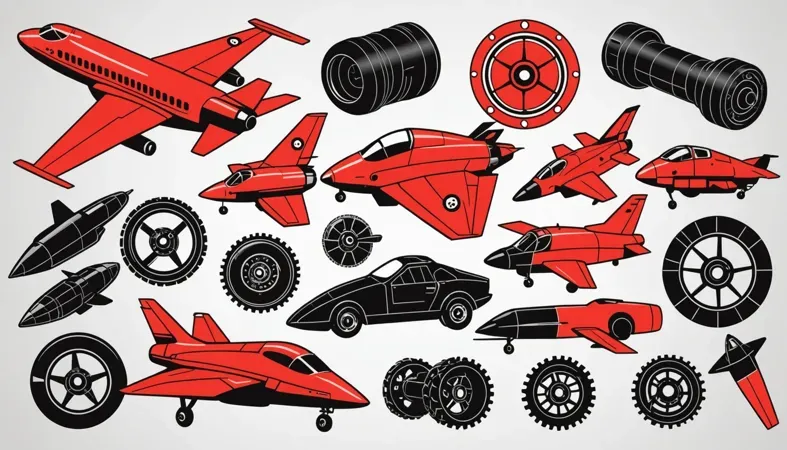
When to Try A Different Approach
Sometimes, you might consider alternatives to achieve similar results in metal shaping. Methods like laser cutting and plasma cutting offer precision without traditional welding. I’ve often found myself thinking that using products such as Omax Waterjets or Miller welders can be more efficient and cleaner in certain scenarios. Selecting the right tool for household projects can be crucial for achieving high-quality results and you might want to explore the best welding machine for home use.
In instances where heat distortion is a concern, adhesive bonding could be a worthwhile route. This approach is popular in the automotive industry, using products such as Loctite Epoxy. Choosing the right method can save time and costs while still delivering strong results.
Frequently Asked Questions (FAQs)
Here are some questions I typically get asked about metal fabrication and welding.
What is the Difference Between Metal Fabrication and Welding?
The difference between metal fabrication and welding is that metal fabrication involves creating structures from raw materials, while welding is a process used to join those materials. Metal fabrication can include tasks like cutting, bending, and assembling, whereas welding focuses solely on joining pieces, often using heat to melt metal together. An understanding of different welding gases like the common 75/25 mixture can enhance welding accuracy and efficiency in various applications.
What Are the Three Types Of Metal Fabrication?
The three types of metal fabrication are cutting, bending, and assembling. Cutting shapes the metal using methods like laser or plasma cutters; bending forms metal into shapes; and assembling involves joining pieces, often through welding or mechanical fasteners. These processes work together to create finished products.
Is Metal Fabrication a Good Career?
Yes, metal fabrication is a good career choice due to high demand and competitive salaries. According to the Bureau of Labor Statistics, welders and metal fabricators earn about $42,000 per year on average, depending on skills and location. Skilled workers are needed in construction, manufacturing, and repair. For those getting started or expanding their work, knowing where to purchase welding metal is crucial for successful projects.
What is Meant by Metal Fabrication?
Metal fabrication refers to the process of creating metal structures and components. This includes cutting, shaping, and joining metal pieces into usable products. It’s essential in industries like automotive and construction, which rely on custom metal solutions for functionality and aesthetics.
What is a Welder Fabricator?
A welder fabricator is a professional who specializes in both welding and fabricating metal parts. They possess skills to read blueprints, cut, shape metal, and then weld components together. This dual ability makes them valuable in various sectors, from manufacturing to construction.
Conclusion
I hope this gave you what you needed. We covered what metal fabrication and welding are, how the process works, various types, essential steps involved, influencing factors, unique challenges, aftercare tips, and practical applications. We also explored welding fundamentals to help you understand when to try a different approach and answered frequently asked questions.
So, what is metal fabrication and welding? It’s the art of shaping metal through processes like cutting, bending, and assembling, along with joining metals with heat and pressure. With this knowledge, you can better understand how fabrication and welding play key roles in creating everything from simple tools to complex structures using various methods and equipment.
If you’re eager to expand your knowledge further, I invite you to revisit What is Welding for additional insights and resources.
References
- American Welding Society. (2020). AWS C5.6: Recommended Practices for Gas Metal Arc Welding. Miami, FL: AWS.
Joe Carter is a retired welding professional with over 40 years of hands-on experience in the industry, spanning ship repair, structural welding, and even underwater projects. Joe is a master of MIG, TIG, and Stick welding. Passionate about mentoring the next generation of welders, Joe now shares his decades of expertise and practical insights to help others build rewarding careers in welding.
American Welding Society, Fabrication Processes, Industrial Applications, Metal Fabrication, Metalworking, MIG Welding, Pipe Welding, Welding, Welding Equipment, Welding Methods, Welding Techniques