What is Duty Cycle in Welding? Understanding Weld Time, Rest Period, and Performance
Published on: January 13, 2025 | Last modified: March 4, 2025
By: Joe Carter
A duty cycle is the amount of time you can use a welder without it overheating. It’s usually given as a percentage, like 60%, in a specific time period, often 10 minutes.
People often ask us, what is duty cycle in welding? It’s crucial to know because it affects your work efficiency and equipment longevity. I’ve experienced downtime due to ignoring the duty cycle, leading to lost productivity and frustration.
In this guide, we’ll dive into what duty cycle is, how it works, the different types, and factors affecting it, plus troubleshooting, inspection tips, and industry applications. You’ll also learn about alternatives to duty cycle in welding and answers to frequently asked questions. Understanding this topic can really enhance your welding skills and equipment knowledge.
Contents
- What is Duty Cycle in Welding?
- How Does Duty Cycle Work in Welding?
- Types Of Duty Cycle in Welding
- Steps for Understanding Duty Cycle in Welding
- Factors Affecting Duty Cycle in Welding
- Understanding Duty Cycle Ratings in Different Welding Processes
- Common Issues and Troubleshooting
- Industry Applications for Duty Cycle in Welding
- Exploring Alternatives to Duty Cycle in Welding
- Frequently Asked Questions (FAQs)
- Conclusion
- References
What is Duty Cycle in Welding?
The duty cycle measures how long you can weld within a specific time, usually 10 minutes. It’s expressed as a percentage. For example, a 60% duty cycle lets you weld for 6 minutes and rest for 4. This helps prevent overheating in various welding applications. Exploring the different types of welding can provide a clearer understanding of how these cycles affect various techniques.
How Does Duty Cycle Work in Welding?
What is duty cycle? in welding indicates how long a welder can operate within a specific time frame, usually expressed as a percentage. For example, a 60% duty cycle means the machine can run for 6 minutes in a 10-minute period. This metric helps prevent overheating and ensures optimal welder performance. It’s crucial for extensive projects, as exceeding the duty cycle can damage your equipment.
Understanding the duty cycle helps you select the right machine for various tasks. A machine with a 100% duty cycle can run continuously without problems, while others may require breaks to cool down. Knowing what a 60% duty cycle means for a welder ensures you don’t overwork it.
I once faced a challenge with a new welding job. I learned the hard way that my 40% duty cycle welder wasn’t sufficient for a large project. If I had understood the duty cycle better, I wouldn’t have had to stop every time my welder overheated.
Types Of Duty Cycle in Welding
What are the types of duty cycles in welding?
Short Duty Cycles
Short duty cycles allow brief bursts of welding. A welder can operate safely for just a few minutes at a time. To work effectively, plan your welding sessions carefully, taking breaks of about 1-2 minutes for every 4-8 minutes of welding.
Medium Duty Cycles
Medium duty cycles balance welding time and cool-down. You usually get around 30% uptime within a 10-minute span. To maximize efficiency, weld for 3 minutes and cool down for about 7 minutes before starting again. Knowing the quantity of welding rods you need can further enhance your workflow, particularly when using specific types like 1/8 7018 rods. For more information on how many 1/8 7018 welding rods are in a pound, check out this resource.
Long Duty Cycles
Long duty cycles allow extended welding periods. This setup permits up to 60% uptime on a welder for every 10-minute period. To maintain quality, weld for 6 minutes, followed by a 4-minute rest; this keeps your machine within safe operating limits.
It is essential to understand the factors that affect welding frequency on different materials, such as the impact on alloy wheels when welding is repeated multiple times. For more detailed technical insights, explore how often you can weld an alloy wheel.
Intermittent Duty Cycles
Intermittent duty cycles involve periods of welding and downtime. A welder rated at a 20% duty cycle can weld for 2 minutes before cooling down for 8 minutes. To practice this well, plan your tasks strategically; spot-welding fits nicely into this type.
Continuous Duty Cycles
Continuous duty cycles allow uninterrupted welding. Machines rated for a 100% duty cycle can weld nonstop without cooling issues. To achieve continuous operation, ensure your machine’s cooling system is efficient—this is key for longer jobs.
That covers the different types of duty cycle in welding. Let’s now take a look at the steps to understand it.
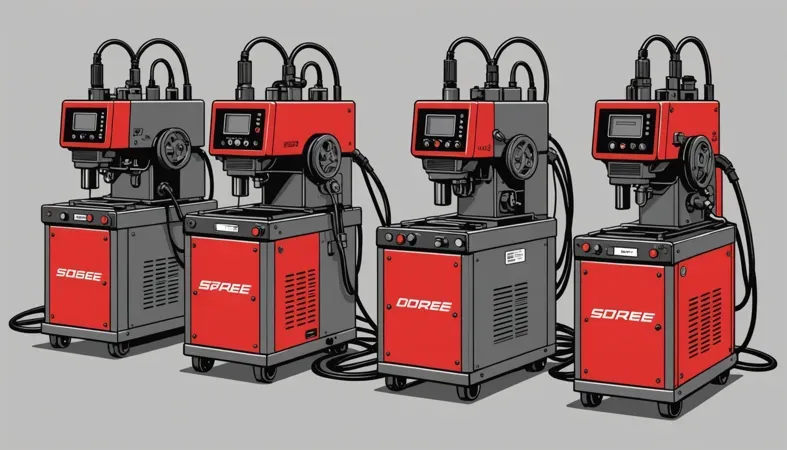
Steps for Understanding Duty Cycle in Welding
Now, we’ll dive into the steps for grasping what a duty cycle in welding entails.
Identify the Welding Process
Start by identifying the type of welding process you’re using. Common methods include MIG, TIG, and Stick welding. Each has a different duty cycle rating that affects how long you can weld before needing a cool-down. For example, MIG welders typically have higher duty cycles than Stick welders.
Depending on your machine, you might see a 20%, 60%, or even a 100% duty cycle rating. This indicates how long you can weld in a specific timeframe. Always check your machine’s specifications to understand its limits. Knowing this upfront prevents overheating the welder and damaging it. It’s also crucial to grasp concepts like what DCEP means in welding for effective and safe operations.
Determine the Duty Cycle Rating
Find your welder’s duty cycle rating, usually expressed as a percentage, indicating how many minutes you can weld in a 10-minute cycle. For example, a 60% duty cycle means you can weld for 6 minutes and must cool down for 4 minutes. Every welder is different, so pay close attention.
If you’re unsure, consult the manual or check the manufacturer’s website. Understanding this percentage will guide your welding strategy and ensure efficient work while maintaining the equipment’s health. When welding 3/8-inch stainless steel, selecting the appropriate amperage is crucial for achieving strong welds efficiently. Learn more about the correct amperage settings to enhance your welding results.
Assess the Cooling Time
Calculate your welder’s cooling time based on the duty cycle. If running at 60%, you’ll need 4 minutes of downtime for every 6 minutes of usage. Underestimating cooling time can lead to overheating.
Consider your environment; a hot workshop might require longer cooling times. Monitoring your welder’s temperature can prevent long-term damage. Always plan tasks to include these necessary cooling breaks.
Evaluate Welding Intervals
Structure your welding intervals to match your duty cycle. For instance, with a 30% duty cycle, balance your weld time with cooling time. A good rule of thumb: if you weld for 3 minutes, cool for 7 minutes. This prevents overheating and maintains productivity.
Mastering different positions is crucial for effective welding, and honing skills in complex scenarios can be challenging. Discover techniques for welding overhead surfaces.
Adjust your weld speed to maximize work time within these constraints. Arranging tasks effectively will minimize interruptions and ensure you get the most out of your machine.
Calculate Effective Welding Time
Finally, calculate your effective welding time based on current conditions. Consider factors like material thickness, joint type, and voltage settings. For more insightful details on optimizing your process, refer to this welding guidance. Changing these variables might alter your duty cycle. Fine-tuning settings gives you an advantage.
Exploring different techniques ensures you see better when welding, which can significantly improve precision and safety during your projects. For tips on optimizing visibility, see better when welding.
To calculate, apply your duty cycle percentage to the cycle time. For a welder with a 60% duty cycle, you can effectively weld for 6 out of 10 minutes. Keeping a note of these calculations handy can help you efficiently plan your day. Understanding more about arc welding techniques can further enhance your welding efficiency and productivity.
We covered the steps to understand duty cycle in welding. Next, we will cover the factors that affect duty cycle.
Factors Affecting Duty Cycle in Welding
What factors influence a welder’s duty cycle performance and efficiency?
Welding Machine Specifications
The welding machine’s power capacity significantly impacts the duty cycle. For example, a machine rated for 200 amps may have a 60% duty cycle, allowing you to weld for 6 minutes out of every 10 before it needs cooling.
Electrode Size and Type
Larger electrodes generate more heat, affecting the duty cycle. A 3/16 inch (4.76 Mm) electrode may require a machine with a higher duty cycle than a smaller 1/8 inch (3.17 Mm) one, influencing how long you can weld before a break.
Welding Environmental Conditions
Your work environment matters. Extreme heat or cold can affect your welder’s performance. Welding in hot conditions can allow for a higher duty cycle due to reduced cooling needs between heats. Selecting the right gas mixture is also crucial for optimal results in various conditions, and you might find tri-mix welding gas applications particularly helpful.
Cool Down Periods
Regular cool down periods extend your welder’s life. If your machine has a 60% duty cycle, ensure it cools for 4 minutes after running for 6 minutes to avoid overheating.
Workpiece Thickness
The thickness of your workpiece impacts your welding speed. Thicker materials may require higher amps and longer duty cycles, increasing risks of overheating.
We have now covered the factors influencing duty cycle in welding. Next, we will examine duty cycle ratings in various welding processes.
Understanding Duty Cycle Ratings in Different Welding Processes
Let’s break down how duty cycle ratings vary across common welding processes.
Welding Process | Typical Duty Cycle Range | Notes |
---|---|---|
MIG Welding | 60% – 100% | High duty cycles make it ideal for continuous production. Great for thinner materials. |
TIG Welding | 30% – 60% | Lower duty cycles due to more precise heat control. Useful for intricate welds. |
Stick Welding | 20% – 80% | Lower ranges generally found; requires understanding of cooling periods. |
Flux-Cored Welding | 50% – 90% | Similar to MIG but often used outdoors. Must manage spatter and heat. |
Submerged Arc Welding | 80% – 100% | Higher duty cycles, perfect for large fabrication projects. Less operator fatigue. |
Understanding these ratings helps you select the right welding process for your needs and optimize productivity.
You should now have a good understanding of duty cycle ratings in various welding processes. In the next part, we’ll discuss common problems and solutions.
Common Issues and Troubleshooting
Let’s look at challenges related to duty cycles in welding.
Overheating Of Equipment
The duty cycle can cause equipment to overheat if maxed out. If your welder runs continuously for too long, it’ll get hotter than a summer day. Look for thermal overload indicators. To fix this, allow the machine to cool between uses, following recommended periods. For example, a 60% duty cycle allows 6 minutes of work followed by a 4-minute rest.
Inconsistent Weld Quality
High duty cycle stress can lead to inconsistent welds. If you notice variations, it often traces back to improper timing. Monitor your travel speed and electrode angle. Adjust the amperage to maintain consistency and quality throughout the duty cycle.
Frequent Machine Shutdowns
A faulty duty cycle might cause machines to shut down unexpectedly. Check the circuit for damage. If it’s tripping, assess your load; a 50% duty cycle means long stretches of use, leading to burnout. Balance your operations to fully utilize the machine’s capacity.
Shortened Equipment Lifespan
Working continuously at or above duty cycle limits can lead to breakdowns. If parts show wear too soon, consider a maintenance schedule. Properly managing the duty cycle can extend lifespan by keeping parts within optimal limits.
Improper Electrode Usage
The duty cycle can affect electrode performance. An unsuitable electrode for high-duty cycles will wear out quickly. Choose the right type based on your cycle; a 0.45 mm (1/8-inch) electrode performs well at moderate cycles under proper settings.
Industry Applications for Duty Cycle in Welding
I’ve known people who use the duty cycle to determine how long they can weld without overheating their equipment. However, it has many applications, such as:
- Pipe Welding: In pipe fabrication, understanding the duty cycle helps welders prevent machine wear and maintain consistency during long shifts, especially under high temperatures. This application is crucial in industrial sectors.
- Automotive Repairs: For auto body shops, knowing the duty cycle keeps welders operating at peak performance. They need reliable equipment to keep up with demand, particularly during high-volume repairs.
- Construction Welding: Builders often consider duty cycles to manage multiple projects simultaneously, minimizing downtime and improving timelines. It’s essential for site productivity.
- Shipbuilding: In marine welding, managing the duty cycle is vital due to long hours of continuous welding in challenging environments. Safety and efficiency are top priorities here.
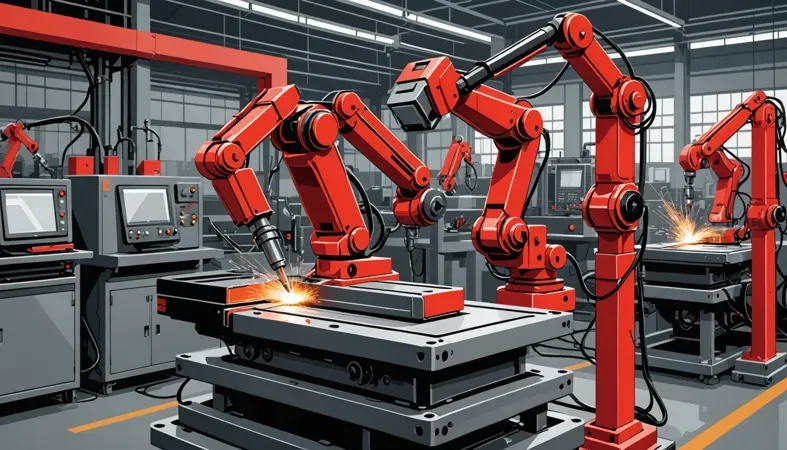
Exploring Alternatives to Duty Cycle in Welding
You’ve got options if you’re looking to avoid issues with duty cycle limits. Techniques like pulsed MIG welding, using machines such as the Lincoln Electric POWER MIG 210, can help maintain heat levels while reducing continuous operation time. From both successes and failures, I’ve learned that these alternatives can offer flexibility, especially when working on intricate sections or thin materials.
Another method is to leverage the benefits of TIG welding, especially with machines like the Miller Multimatic 215. These setups allow for precise control over heat and help minimize excess power usage. So, why not experiment with these alternatives to see which best fits your project needs?
Frequently Asked Questions (FAQs)
Now let us look at some questions I typically get asked.
What Does 20% Duty Cycle Mean on a Welder?
Yes, a 20% duty cycle on a welder means you can weld for 2 minutes out of every 10 minutes. It’s essential to understand this because it helps prevent overheating. If you’re planning long projects, you might want a welder with a higher duty cycle for efficiency.
What Does 60% Duty Cycle Mean?
A 60% duty cycle means you can weld for 6 minutes within a 10-minute span. This is important for tasks needing longer continuous operation. Choosing a welder with this duty cycle helps you maintain better productivity without risking equipment damage.
Is There a 100% Duty Cycle Welder?
Yes, there are 100% duty cycle welders available. This means you can operate it continuously without downtime. They’re great for heavy-duty fabrication but can be more expensive, often costing several thousand dollars.
What Does It Mean if a Welder Has a 75% Duty Cycle?
A welder with a 75% duty cycle allows you to weld for 7.5 minutes out of 10 minutes. This can be a sweet spot for most welding jobs. It offers a balance between performance and affordability, making it suitable for many professionals.
How Does Duty Cycle Affect Welding Performance?
The duty cycle affects welding performance by determining how long you can weld before needing a break. Higher duty cycles generally mean less downtime and more work done per hour. For high-volume projects, this could mean a significant impact on productivity.
Conclusion
We’ve made it to the end, and I hope it was helpful. We covered what duty cycle is, how it works, different types, steps for understanding, factors affecting it, common issues, advanced tips for aftercare, industry applications, and even explored alternatives. Each item sheds light on the crucial aspects of welding fundamentals in welding.
I trust these insights have been helpful in clarifying what duty cycle in welding is. Simply put, it’s the amount of time a welder can operate over a fixed period, often expressed as a percentage. For instance, a 60% duty cycle allows you to weld for 6 minutes out of every 10 minutes while resting for 4 minutes to avoid overheating.
For a deeper understanding of welding and its various aspects, I encourage you to visit What is Welding.
References
- ISO. (2017). ISO 3834: Quality Requirements for Fusion Welding of Metallic Materials. Geneva, Switzerland: ISO.
- Kou, S. (2003). Welding Metallurgy (2nd ed.). Hoboken, NJ: Wiley.
- International Organization for Standardization. (2017). ISO 3834: Quality Requirements for Fusion Welding of Metallic Materials. Geneva, Switzerland: ISO.
Joe Carter is a retired welding professional with over 40 years of hands-on experience in the industry, spanning ship repair, structural welding, and even underwater projects. Joe is a master of MIG, TIG, and Stick welding. Passionate about mentoring the next generation of welders, Joe now shares his decades of expertise and practical insights to help others build rewarding careers in welding.
Duty Cycle, MIG Welding, Pipe Welding, Types Of Welding, Welder Efficiency, Welding, Welding Applications, Welding Equipment, Welding Performance, Welding Techniques