What is 7018 Welding Rod Used for? Overview, Benefits, and Applications
Published on: November 22, 2024 | Last modified: March 4, 2025
By: Joe Carter
A 7018 welding rod is a type of electrode used in arc welding. It’s primarily known for its strong welds and ease of use.
A question that keeps coming up is, what is 7018 welding rod used for? It’s crucial to understand its applications because using the right rod can make or break your project. From my own experience, I’ve seen how choosing the right welding rod like the 7018 can significantly enhance weld quality and durability.
In this article, we’ll cover what a 7018 welding rod is used for, how it works, various types, steps for using it, factors that affect its use, typical problems you might face, aftercare tips, industry applications, and some alternatives. We’ll also discuss related topics, such as what is 7014 welding rod used for and what is er70s-6 welding wire used for.
Contents
- What’s 7018 Welding Rod Used for?
- How Does the 7018 Welding Rod Work?
- Types Of 7018 Welding Rods
- Steps for Using 7018 Welding Rod
- Factors Affecting the Use Of 7018 Welding Rods
- Typical Problems to Be Aware Of
- Welding Techniques Compatible with 7018 Rods
- Aftercare, Inspection, and Advanced Tips for 7018 Welding Rod Use
- Industry Applications for 7018 Welding Rod
- Alternatives That Might Work Better for Welding Applications
- Frequently Asked Questions (FAQs)
- Conclusion
- References
What’s 7018 Welding Rod Used for?
The 7018 welding rod excels in creating strong, durable welds, especially in structural applications. It’s commonly used for welding low-alloy steels and repair jobs due to its high tensile strength. Ideal for heavy machinery and construction projects!
How Does the 7018 Welding Rod Work?
The 7018 welding rod is mainly used for stick welding and excels at joining carbon steels. It has a low hydrogen composition that helps prevent cracking. Typically, it contains 0.07% carbon, 1.50% manganese, and 0.30% molybdenum. This rod performs best with a welding current between 70 and 120 amperes (A).
Expert welders value the 7018 rod for its arc stability and strong welds, with tensile strengths reaching 70,000 pounds per square inch (Psi), or about 482 megapascals (Mpa). It’s perfect for heavy fabrication and structural steel applications.
I’ve used the 7018 rod for various projects, especially on thicker materials and critical structures. It’s reliable, and I’ve always trusted the strength of the joints I create with it. If you’re choosing a welding rod for your industrial work, the 7018 simply can’t be beat!
Types Of 7018 Welding Rods
What types of 7018 welding rods are available?
-
Low Hydrogen Electrodes
Low hydrogen electrodes help prevent cracks. They’re used for critical welds in structural steel and handle high-stress applications. Weld in a clean, dry area for the best results.
-
Diameter Variations
They come in various diameters, typically from 1/16 inch (1.6 Mm) to 3/16 inch (4.8 Mm). Larger rods provide deeper penetration in thicker materials. Choose the right diameter based on the steel’s thickness to ensure a strong joint.
-
Acid-coated Rods
Acid-coated rods have a unique coating that enhances arc stability. They’re ideal for general welding on mild steel. For best performance, use a clean surface and apply steady movement for consistent welds.
-
Basic-coated Rods
These rods offer excellent toughness and stress resistance. They’re perfect for heavy structural welding. Maintain proper arc length and speed to ensure uniform penetration and strength.
-
High Tensile Strength Rods
High tensile strength rods produce durable welds that withstand heavy loads. They’re often used in construction and machinery repairs. Apply the correct amperage, typically between 70 and 100 amps, for optimal penetration.
So far we covered the different varieties of 7018 welding rods. Next, let’s look at how to use 7018 welding rods.
Steps for Using 7018 Welding Rod
Here are the core steps for using 7018 welding rods.
-
Prepare the Base Material
Clean the base material thoroughly. Remove paint, rust, or grease, as these contaminants can affect weld quality. Ensure a clean surface of about 1 cm² (0.15 In²) for proper adhesion.
If needed, use a wire brush or grinder. For thick materials, use a bevel to aid penetration. A good fit-up is crucial for achieving full fusion and strength in your weld!
-
Select the Correct Welding Settings
Next, set your welder for the job. For 7018 rods, adjust the amperage between 125 A and 180 A, depending on the rod size. For a 1/8-inch (3.2 Mm) rod, 125 A is often ideal.
Use DC Reverse Polarity for better penetration and smoother arc stability. You may also need to adjust settings for different joint designs to achieve a strong weld seam!
-
Strike an Arc
Now, initiate the welding arc. Hold the 7018 rod at a 15 to 20-degree angle and tap it against the base material to create the arc. This ignites the electrode coating, causing the rod to melt and fill the weld joint effectively. It’s important to consider safety precautions when welding different metals, as welding galvanized steel can pose significant health risks, as discussed in the dangers of welding galvanized steel.
Keep the arc length short for better control. Aim for a distance of about 3 to 5 mm (0.12 To 0.20 In) for optimal performance and reduced spatter.
-
Maintain Proper Travel Speed
Move along the joint at a consistent speed to avoid weak spots. Typically, travel at 10 to 15 cm/min (4 to 6 In/min), depending on the situation. A steady hand is essential for achieving clean, even beads.
If you move too slowly, excessive heat can cause distortion or burn-through. Conversely, speeding up might result in insufficient penetration or a poor bead appearance. Find that sweet spot!
-
Complete the Weld
Finish the weld by gently lifting the rod as you complete the joint. Tapering off the arc allows the molten metal to cool smoothly and form a solid bond. Stay fluid to avoid defects.
Once cool, inspect your work. Grind off any slag for a clean finish. A strong weld typically has a smooth appearance and good penetration—that’s the hallmark of a quality 7018 rod.
That covers the procedures for using 7018 welding rods. Let’s now take a look at the factors influencing their usage.
Factors Affecting the Use Of 7018 Welding Rods
What factors influence the application of 7018 welding rods? Here’s the rundown.
-
Material Thickness
Thicker materials need specific settings. For every 1/16 inch (1.59 Mm) of thickness, increase your amperage by about 40 amps.
-
Joint Configuration
Welding in a groove joint compared to a corner joint affects penetration. A groove joint may require more heat, while a corner joint can use lower heat input.
-
Welding Position
Flat and horizontal positions suit 7018 well. If you’re welding overhead, use a rod designed for that angle.
-
Ambient Temperature
Cold temperatures can affect the weld pool and arc stability. In winter, it’s wise to raise your electrode preheat to about 70°F (21°C).
-
Electrode Storage Conditions
7018 rods must stay dry. If they absorb moisture, they lose strength and create hydrogen inclusions, which lead to cracking.
We covered the factors influencing the use of 7018 welding rods. Next, we will address common issues to consider.
Typical Problems to Be Aware Of
Let’s look at issues unique to the 7018 welding rod.
-
Cracking During Cooling
The 7018 welding rod can crack as it cools. Check for linear fractures. To fix this, control the cooling rate by preheating or keeping the weldment warm.
-
Inconsistent Arc Stability
I’ve encountered this issue with the 7018 welding rod. It creates erratic arcs. Check your machine settings and rod angle. Stabilize the voltage or adjust your technique to resolve it.
-
Weld Defects From Contamination
The 7018 welding rod can suffer from contamination, like rust or dirt. Inspect the base metal and surroundings. Remove contaminants by grinding or cleaning with a solvent for better welds.
-
Excessive Spatter
Using the 7018 welding rod can cause spatter. You know there’s a problem if you see many small balls around your weld. To reduce this, adjust the voltage and travel speed.
-
Difficulty in Striking an Arc
The 7018 welding rod can be finicky when striking an arc. It might not ignite easily. If so, check the electrode angle and ensure the rod is dry.
We covered common issues to watch out for, including rod handling and electrode storage. Next, we will cover compatible welding techniques.
Welding Techniques Compatible with 7018 Rods
Using the right welding techniques can elevate your 7018 welding experience. Here are some techniques that pair well with 7018 rods:
Technique | Description | Recommended Use Cases |
---|---|---|
Stringer Beads | Low travel speed and narrow bead. Helps avoid overheating. | Thin materials and vertical positions. |
Weaving Technique | Side-to-side motion for wider beads. Ideal for thicker materials. | Heavy-duty applications, like structural welding. |
Push Technique | Welding with the current flowing toward the weld puddle. Offers better penetration. | For all positions, particularly horizontal. |
Pull Technique | Pulling the rod away from the weld puddle. Reduces spatter. | For flat and horizontal positions. |
Circle Technique | Small circular motion while welding. Increases alignment and bead consistency. | Complex shapes and joint preparations. |
Are you ready to enhance your skills? Using these welding techniques can maximize the effectiveness of your 7018 welding rod! Incorporate them, and you’ll create stronger, cleaner welds.
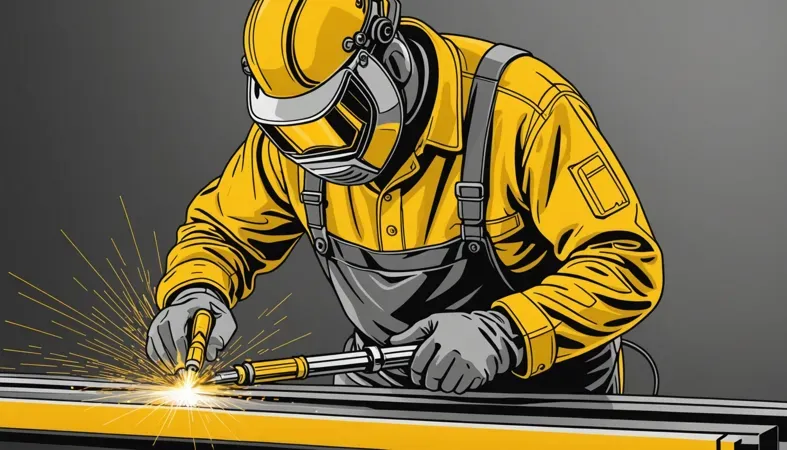
Aftercare, Inspection, and Advanced Tips for 7018 Welding Rod Use
Here’s key information about post-welding care, inspections, and advanced techniques to maximize 7018 welding rod performance.
Aftercare Tips
After using a 7018 welding rod, tightly close the container to prevent moisture exposure. Store rods in a dry oven or storage unit set to 110°C (230°F) if you won’t use them for more than a day. Clean puddles with a wire brush or grinder within 20 minutes to maintain integrity.
Inspection Techniques
Inspect welds for slag inclusions, which can weaken your joint. Perform a thorough visual inspection and, if needed, a continuity test using a multimeter like the Klein Tools MM300. Check beads for undercuts or insufficient penetration; aim for a penetration depth of at least 5 mm (0.2 Inches) for solid joints.
Expert Tips
For seasoned welders, adjust your arc length to about 3 mm (1/8 Inch) for an optimal balance between penetration and bead appearance. Consider preheating your material to around 150°C (302°F) to reduce cracking, especially in thicker sections. Always account for oxidation buildup—periodically check your ground clamp to maintain stable conductivity. Choosing the right shielding gas plays a crucial role in determining the quality of your welds, influencing both penetration and bead profile. To explore what type of gas is used in welding for different materials, learn about welding gas options.
Industry Applications for 7018 Welding Rod
I’ve known people to use 7018 welding rods for various tasks in the field. However, it has many specific applications, such as:
- Structural Welds: 7018 rods are ideal for heavy-duty structural applications, like bridges and buildings. They provide high strength and durability, making them a popular choice in construction.
- Pipe Welding: This rod excels in API 5L pipeline work, especially in the oil and gas sectors. Its low hydrogen content helps prevent cracks, which is crucial in high-pressure conditions.
- Manufacturing Equipment: Extensively used in fabricating machinery, its tensile strength allows it to withstand heavy loads and stress—vital for industrial settings.
- Shipbuilding: 7018 is often the preferred choice for welding ship hulls. Its resistance to impact and fatigue makes it suitable for harsh environments.
Alternatives That Might Work Better for Welding Applications
Several alternatives might suit your welding needs just as well, if not better. For instance, the 7014 welding rod provides a smoother finish and better resistance to undercutting. Similarly, when it comes to thinner materials, the ER70S-6 welding wire excels in producing a clean weld with minimal spatter. A basic understanding of semiautomatic welding systems is essential for optimizing these tools effectively.
From both successes and failures, I’ve learned that context matters. The 6013 welding rod works perfectly for general-purpose welding and even for vertical positions. In cases requiring greater strength, consider turning to the 7010 welding rod, known for its high strength and versatility.
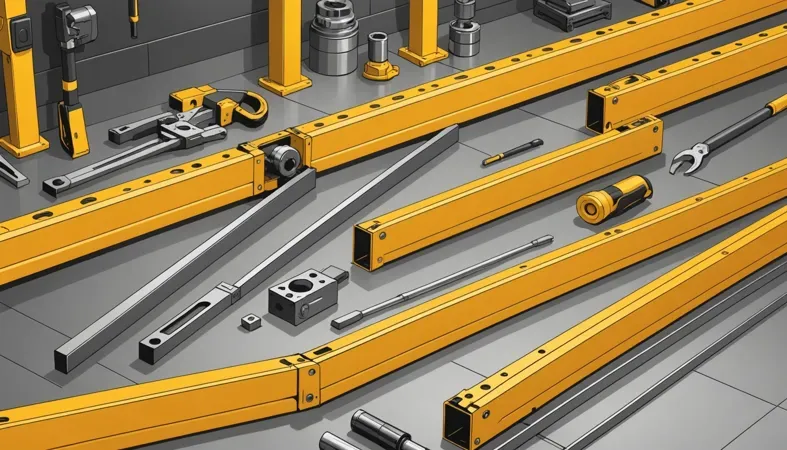
Frequently Asked Questions (FAQs)
Now let us look at some questions I typically get asked.
When to Use 7018 Welding Rods?
Use 7018 welding rods when you need high strength and low hydrogen deposits. They’re perfect for steel applications, especially in structural steel, with a tensile strength of about 70,000 psi (482 Mpa). Understanding different welding processes can help you select the right materials for your project.
Welding thin metal requires different techniques to prevent warping and ensure precision, as detailed in the guide on welding thin metal.
What’s the Difference Between 6011 and 7018?
The difference between 6011 and 7018 lies in their composition and usage. 6011 rods work well on dirty or rusty materials, while 7018 rods are best for clean steel, offering superior strength and a smoother finish.
What Are the Disadvantages Of a 7018 Welding Rod?
A drawback of 7018 welding rods is the need for dry storage. They can absorb moisture easily, which may lead to porosity in your welds. If you don’t keep them dry, you might face issues.
What is the Easiest Welding Rod to Use?
The easiest welding rod to use is often considered 7014. It has a forgiving arc and works well on mild steel, making it beginner-friendly compared to other rods. Users find it easier to control.
If you are looking to expand your skills beyond basic rods, you’ll need to explore techniques for welding 16-gauge sheet metal.
What Are 7014 Welding Rods Used for?
7014 welding rods are used for general-purpose welding on mild steel. They offer good versatility and produce a clean weld with a tensile strength of about 70,000 psi (482 Mpa), making them suitable for both interior and exterior projects. For those interested in learning more about these materials, the characteristics of different welding rods can help in selecting the right type for specific applications.
What is the 7010 Welding Rod Used for?
The 7010 welding rod is used primarily for welding high-strength steels. It’s commonly found in pressure vessel and shipbuilding industries due to its excellent toughness and impact resistance at low temperatures.
Conclusion
I hope this was worth your while. We covered what is 7018 welding rod used for, how it works, different types of rods, steps for using them, factors that affect their use, common issues, aftercare tips, industry applications, and alternatives. This should give you a solid understanding of 7018 welding rod and its importance in various tasks.
So, what is 7018 welding rod used for? Simply put, it’s your go-to for high-strength welds, especially in structural steel applications. With a tensile strength of 70,000 psi (Pounds Per Square Inch) and low hydrogen properties, it’s excellent for welding thick materials like beams and frames. Feel free to reach out if you have further questions about 7018 or any other welding rods.
If you’re interested in expanding your welding knowledge, be sure to check out What is Welding for more tips and tricks.
References
- European Welding Federation (EWF): https://www.ewf.be
- American Welding Society. (2020). AWS C5.6: Recommended Practices for Gas Metal Arc Welding. Miami, FL: AWS.
Joe Carter is a retired welding professional with over 40 years of hands-on experience in the industry, spanning ship repair, structural welding, and even underwater projects. Joe is a master of MIG, TIG, and Stick welding. Passionate about mentoring the next generation of welders, Joe now shares his decades of expertise and practical insights to help others build rewarding careers in welding.
7018 Welding Rod, American Welding Society, Arc Welding, Pipe Welding, Structural Steel, Welding, Welding Applications, Welding Rod Types, Welding Techniques, Welding Wire