What Does NDE Stand for in Welding? – Definition, Importance, and Types
Published on: March 6, 2025 | Last modified: March 4, 2025
By: Joe Carter
NDE, or Non-Destructive Examination, is a way to inspect materials without causing damage. It helps ensure the quality and safety of welds in various applications.
I’ve been asked many times, what does nde stand for in welding? It’s crucial to understand this because NDE helps prevent failures in structures. Personally, I’ve seen how proper NDE can catch small flaws before they become big problems, saving time and money.
In this article, I’ll cover what NDE is in welding, how it works, the types of NDE, the steps to conduct NDE, and the factors that affect its effectiveness. You’ll also find answers to frequently asked questions. Knowing this helps grasp not just what is NDT testing of welds but its significance in ensuring your welds are strong and reliable.
Contents
What is NDE in Welding?
NDE stands for Non-Destructive Examination, a vital process in welding. It evaluates materials without causing damage, ensuring quality and safety. You’ll find it in industries like aerospace and construction to detect flaws early. Also, understanding the duty cycle in welding is essential as it affects how effectively welders can perform their tasks.
How Does NDE Work in Welding?
NDE stands for Non-Destructive Examination. It’s a method used to evaluate weld integrity without causing harm. Technicians use various techniques, like ultrasonic or radiographic testing, to detect defects in welds. Did you know these methods can find flaws as small as 1 mm (0.04 Inches)?
In the welding industry, NDE is vital for ensuring quality and safety. Professionals follow standards from organizations like ASNT (American Society for Nondestructive Testing) to conduct these examinations thoroughly.
Working with NDE has its rewards. I’ve seen how effective these tests are in preventing future failures. Remember, using methods like NDT (Non-destructive Testing) can save you thousands in repairs down the line!
Types Of NDE in Welding
What are the non-destructive testing methods used in welding?
-
Visual Inspection
Visual inspection involves closely examining the welds. It’s the first step in understanding NDE in welding, focusing on surface quality. Check for cracks, discoloration, or improper bead shapes using your eyes and magnifying tools.
-
Magnetic Particle Testing
This technique detects surface and slightly subsurface defects in ferromagnetic materials. It clarifies the non-destructive testing concept by using magnetic fields and particles. To conduct this test, magnetize the weld and sprinkle ferromagnetic particles. They’ll cluster around defects, making them visible.
-
Ultrasonic Testing
Ultrasonic testing uses high-frequency sound waves to detect inconsistencies in welds. It shows the importance of NDE, as it penetrates materials without causing damage. Begin by emitting sound waves into the material. Reflective waves indicate potential flaws based on their returning signals.
-
Radiographic Testing
This method uses X-rays or gamma rays to examine internal weld structures. It highlights the significance of non-destructive examination in identifying hidden flaws. To carry out this test, expose the weld to radiographic energy and analyze the resulting images on film or digital surfaces.
Choosing the right equipment is crucial for ensuring high-quality welds in pipeline projects, and you might find detailed information about the best welding machine for pipeline.
-
Liquid Penetrant Testing
Liquid penetrant testing finds surface defects through color contrast. It reinforces the meaning of NDE by making hidden flaws visible. To execute, apply a liquid penetrant over the weld, let it sit, then wipe the surface. Finally, apply a developer, which pulls the penetrant from the flaws, revealing them.
So far we covered various types of non-destructive evaluation in welding. Next, let’s look at the steps to perform NDE in welding.
Steps to Conduct NDE in Welding
Now, let’s cover the steps for understanding non-destructive examination (NDE) in welding.
-
Preparation Of the Weld Area
Clean the weld area thoroughly. Remove any contaminants, dirt, or grease. Use a brush or solvent to ensure the surface is pristine. The cleaner the surface, the more accurate your NDE results will be.
Next, inspect the weld area for visible cracks or damage. According to ASNT (American Society for Nondestructive Testing) guidelines, a clean environment enhances testing effectiveness. This step can’t be skipped; you want a reliable reading.
-
Selection Of NDE Method
Choose the right NDE method based on the material and application. Common methods include ultrasonic testing (UT) and radiographic testing (RT). Each method has its specifics; for example, UT is ideal for detecting internal flaws in metals using high-frequency sound waves.
Consider the operational environment. If you’re working with complex shapes, use eddy current testing. It’s quick and effectively covers detailed areas. Your choice significantly impacts test effectiveness, so think it through!
-
Execution Of the Test
Carry out the selected NDE method according to the procedure outlined in relevant codes. For ultrasonic testing, calibrate the equipment first. Adjust your probe frequency according to the material thickness, ideally within ±10% of the actual thickness.
Practice makes perfect! I made mistakes early by rushing this part. Allow enough time for data collection and verification. Follow each step to get reliable results; don’t cut corners.
-
Documentation Of Results
Record all results systematically. Include details like the method used, test parameters, and findings. Use clear, concise language and standardized forms to stay organized. This information is vital for future reference and compliance.
Retain your data for at least 5 years, as issues may arise later. The documentation should allow for easy interpretation, as good records can save time down the road. Trust me, you want to avoid confusion later!
-
Analysis Of Findings
Review the data collected. Identify any defects or anomalies indicated by your tests. Compare these against industry standards or predefined limits. A thorough analysis helps in making crucial decisions on repairs or the usability of the weld. To effectively conduct such an analysis, it is beneficial to explore the welding procedure qualification process.
Collaborate with a qualified engineer whenever possible to ensure you catch every detail. Discuss findings and verify if any corrective actions are needed. Ultimately, the quality of your welding reflects on your final product. Knowing the cost of welding rods can significantly impact your project’s budget estimation!
We covered steps for conducting NDE in welding. Next, we will cover factors influencing NDE in welding.
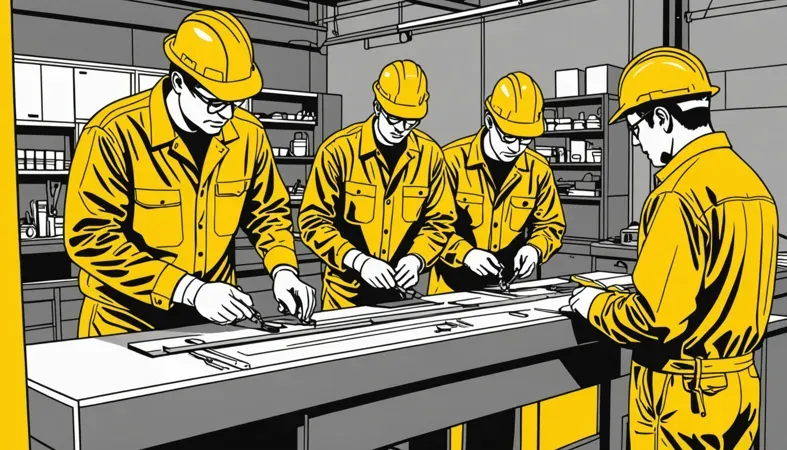
Factors Affecting NDE in Welding
What factors influence NDE in welding? Here are the key ones.
-
Weld Material Properties
The type of materials affects NDE’s effectiveness. For example, steel may require different tests than aluminum due to their unique properties.
-
Weld Joint Design
A design’s complexity impacts how NDE is performed. Simple joints are easier to inspect than complex geometries, influencing your choice of NDE methods.
-
Testing Methodology
The method you use shapes the NDE outcome. Techniques like ultrasonic testing (UT) or radiographic testing (RT) can reveal various defects, significantly affecting interpretation.
-
Environmental Conditions
Poor weather can hinder inspections. Changes in temperature or humidity may impact accuracy, so always consider the environment.
-
Operator Skill Level
Your expertise affects NDE results. A skilled operator can spot issues that a novice may overlook, affecting the entire inspection process.
So far we covered the elements influencing non-destructive examination in welding. Next, let’s look at the significance of NDE in welding.
Importance of NDE in Welding
NDE plays a crucial role in maintaining safety and integrity in welding applications. Here’s why it matters:
- Prevention of Failures: NDE techniques detect flaws early, preventing potential structural failures that could lead to accidents or costly repairs.
- Regulatory Compliance: Many industries have standards requiring NDE to ensure safety. Adhering to these regulations keeps companies compliant and protects public safety.
- Cost Savings: Identifying defects before they escalate saves time and money. Think about it—preventing a failure is more economical than fixing one.
- Quality Assurance: Regular NDE ensures consistent quality in welding practices, which is vital in critical sectors like aerospace and infrastructure.
We covered the significance of NDE in welding. Next, we will explore common applications of NDE.
Common Applications of NDE
NDE is used across various industries. Here are a few key applications:
Industry | Application | NDE Methods Used |
---|---|---|
Aerospace | Inspecting aircraft structures | Ultrasonic Testing, Radiographic Testing |
Construction | Ensuring structural integrity of buildings | Magnetic Particle Testing, Visual Inspection |
Oil and Gas | Pipeline integrity checks | Radiographic Testing, Ultrasonic Testing |
Manufacturing | Quality control in welds | Liquid Penetrant Testing, Visual Inspection |
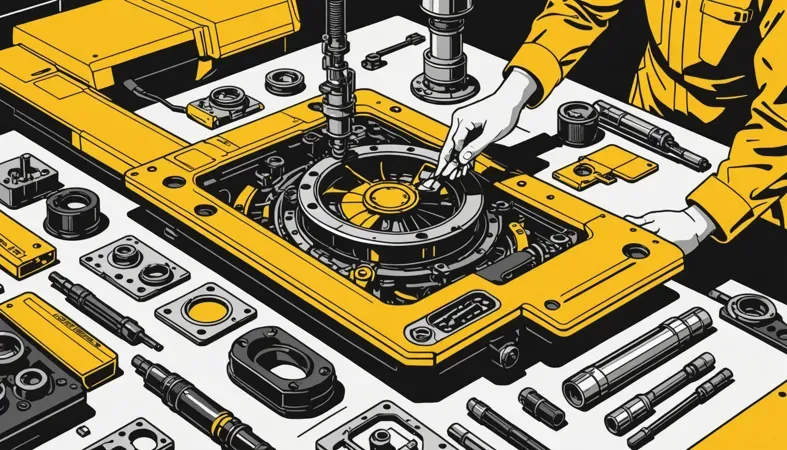
Frequently Asked Questions (FAQs)
Now let us look at the questions I typically get asked.
What’s the Difference Between NDT and NDE?
The difference between NDT and NDE lies in their scope. NDT, or Non-Destructive Testing, checks for defects without damaging the material. NDE, or Non-Destructive Evaluation, includes both testing and assessment to determine your structure’s overall integrity. Essentially, NDE is a broader term encompassing NDT.
What Does NDE Inspection Stand for?
NDE inspection stands for Non-Destructive Evaluation inspection, and it focuses on assessing the integrity of materials without causing any harm. It combines methods like radiography and ultrasonic testing, helping industries save costs and time by detecting flaws efficiently.
What is an NDE Technician?
An NDE technician is a skilled professional who performs Non-Destructive Evaluation. They use techniques like ultrasonic testing, magnetic particle inspection, and liquid penetrant methods to detect flaws. These technicians typically hold certifications, ensuring quality evaluations in various industries, including aerospace and construction.
What is the Most Common NDE Method Used?
The most common NDE method used is ultrasonic testing. This technique uses high-frequency sound waves to detect flaws in materials. It’s popular because it’s accurate and can be applied to various materials, including metals and composites. Ultrasonic testing often gives results within a few hours, making it efficient.
What is NDT Testing Of Welds?
NDT testing of welds refers to Non-Destructive Testing specifically for welds to identify defects without damaging the structure. Common methods include visual inspection, radiography, and ultrasonic testing. This is crucial in sectors like aerospace, where weld quality can affect safety and performance.
For those engaged in welding practices, understanding how different welding technologies like DC inverter welding machines operate can enhance the quality and efficiency of their work.
Conclusion
We’ve gone through a lot, thank you for sticking it out. We covered what NDE means in welding, how it works, its different types like ultrasonic, radiographic, and visual inspections, as well as the steps to conduct NDE and the factors that can impact its effectiveness. We also touched on common questions about its relation to NDT and relevant standards like ASNT.
So, what does NDE stand for in welding? Simply put, NDE is Non-Destructive Evaluation. It lets you assess welds without damaging them, ensuring they meet safety and quality standards. If you’d like more guidance or have questions about NDE practices, contact me.
If you’re interested in exploring more about welding and related topics, be sure to check out What is Welding for additional insights and resources.
References
- Lincoln Electric. (2020). The Procedure Handbook of Arc Welding (15th ed.). Cleveland, OH: Lincoln Electric Company.
- Blodgett, O. W. (1995). Design of Weldments. Cleveland, OH: James F. Lincoln Arc Welding Foundation.
Joe Carter is a retired welding professional with over 40 years of hands-on experience in the industry, spanning ship repair, structural welding, and even underwater projects. Joe is a master of MIG, TIG, and Stick welding. Passionate about mentoring the next generation of welders, Joe now shares his decades of expertise and practical insights to help others build rewarding careers in welding.
Construction, Inspection Techniques, NDE, Non-Destructive Examination, Quality Assurance, Regulations, Safety Standards, Structural Integrity, Welding, Welding Applications