What is Welding WPQ? Exploring Performance Qualification, Types, and Steps
Published on: March 16, 2025 | Last modified: March 4, 2025
By: Tyler James
WPQ stands for Welding Performance Qualification. It’s a process that ensures welders are qualified to perform specific types of welding jobs.
Many people are curious about what is welding wpq. Understanding WPQ is crucial because it guarantees a welder can meet industry standards and safety requirements. From my experience, following these qualifications helps in producing high-quality welds while minimizing risks on the job site.
In this article, we’ll cover how welding performance qualification works, types of welding procedure qualifications, steps to obtain these qualifications, factors that influence them, and frequently asked questions. We’ll also touch on related topics like what is WPS PQR in welding and the differences between WPS and PQR in welding. You’ll get clear insights to improve your welding knowledge!
Contents
- What is Welding WPQ?
- How Does Welding Performance Qualification (WPQ) Work?
- Types Of Welding Procedure Qualifications
- Steps to Obtain Welding Procedure Qualifications
- Factors Influencing Welding Procedure Qualifications
- Related Terms in Welding Qualification
- Frequently Asked Questions (FAQs)
- Conclusion
- Additional Reading
What is Welding WPQ?
Welding performance qualification (WPQ) verifies a welder’s skill and technique. It ensures welds meet specific strength and quality standards. Typical applications include construction and manufacturing, where strong, reliable joints are crucial.
How Does Welding Performance Qualification (WPQ) Work?
Welding Performance Qualification (WPQ) defines a welder’s ability to create reliable welds. It involves direct testing of a welder’s skills using specific weld types, materials, and procedures. Tests typically include various positions, such as flat, horizontal, and vertical. Parameters like tensile strength, measured in megapascals (Mpa) or pounds per square inch (Psi), ensure the weld meets industry standards.
To achieve a WPQ, you must follow strict technical guidelines. For example, a welder may need a minimum passing rate of 70% tensile strength compared to material specifications. This guarantees safety and the welded joint’s longevity.
To succeed at WPQ, practice various welding techniques regularly to master necessary skills. Then, review the Procedure Qualification Record (PQR) to understand the specific welding parameters, like filler material and heat input, relevant to the WPQ process. Knowing the relationship between WPQ and procedures like Welding Procedure Specification (WPS) or PQR can significantly enhance your expertise.
Types Of Welding Procedure Qualifications
-
MIG Welding Procedure Qualifications
MIG welding (Metal Inert Gas Welding) uses a continuous wire feed to join metals. Qualifications show you can use the correct wire types, like ER70S-6, and achieve good penetration. To qualify, set parameters like wire speed and voltage, then pass tests on weld strength and appearance.
-
TIG Welding Procedure Qualifications
TIG welding (Tungsten Inert Gas Welding) uses a non-consumable tungsten electrode. It demonstrates your ability to produce clean, high-quality welds on materials like aluminum and stainless steel. To qualify, practice controlling the arc length, gas flow, and filler rods based on material thickness.
-
Stick Welding Procedure Qualifications
Stick welding (Shielded Metal Arc Welding) uses a consumable electrode to fuse materials. This process covers your skill in joining metals like mild steel with various rods, such as E6011. To qualify, you’ll need to demonstrate proper technique in different positions to ensure penetration and arc stability.
-
Submerged Arc Welding Procedure Qualifications
Submerged Arc Welding (SAW) uses granular flux to protect the weld, resulting in deep penetration. Your qualifications prove proficiency in setting up equipment with appropriate currents for thick steels. To qualify, adjust voltage and travel speed while passing tests on weld quality and consistency. For more details on choosing the right welder settings, you can explore how many amps a welder uses here.
-
Flux-cored Arc Welding Procedure Qualifications
Flux-Cored Arc Welding (FCAW) uses tubular electrodes filled with flux to shield the molten weld. Your qualifications demonstrate your ability to weld galvanized and non-galvanized steels effectively. To qualify, ensure accurate settings, conduct multiple passes, and pass strength tests. Understanding the nuances of different welding techniques, such as MAG welding methods, can further enhance your expertise.
So far we covered the various welding procedure qualifications. Next, let’s look at the process to obtain these qualifications.
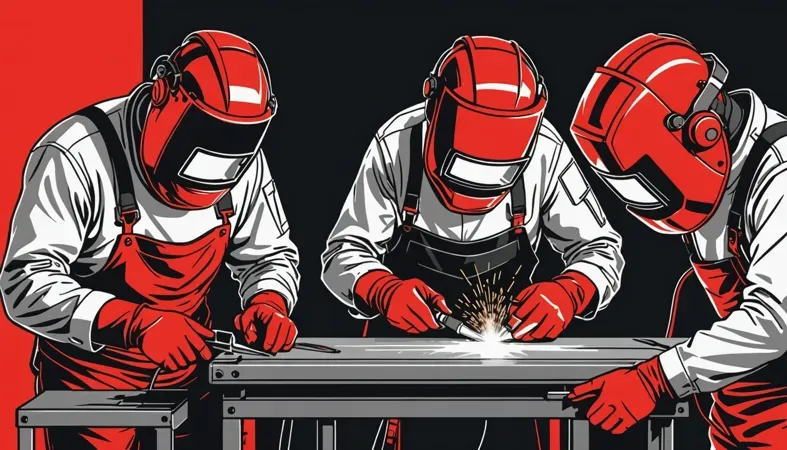
Steps to Obtain Welding Procedure Qualifications
Now, we’ll cover the essential steps for understanding WPQ in welding.
-
Identify Welding Requirements
Start by determining the welding standards for your project. Check specifications like AWS D1.1 for structural steel or ASME for pressure vessels. Knowing the exact codes aligns your WPQ with industry expectations. Consider the materials, thickness (From 1 Mm to Over 25 Mm), and service conditions involved.
Pay attention to the service conditions as well. API standards vary for oil and gas compared to construction. Understand your end-use scenario, as it shapes your qualification needs and performance. In industrial applications, a solid understanding of joint types is crucial, including how a butt weld compares to others.
-
Develop Welding Procedure Specification
Your next step is to create a Welding Procedure Specification (WPS). This document outlines how you’ll perform the weld. Include details such as the type of weld, filler metal, and preheating temperatures, which can range from 100°C (212°F) to 200°C (392°F) based on welding requirements. Detail each step to guide your welding process.
In welding, understanding different materials and obstacles is crucial, and exploring what dross in welding is can help enhance your technical execution.
Adjust the WPS based on the materials used. For example, if you’re working with a steel alloy classified as a P-number, choose your filler metals accordingly. This keeps your qualification relevant and accurate.
-
Conduct Qualification Tests
Next, test the WPS you’ve drafted. Perform welds using the exact parameters documented, following your WPS precisely. This is crucial for forms like the Welder Performance Qualification (WPQ) test, which measures your welders against code requirements. Arc welding plays a pivotal role in achieving the standards set out in these qualification tests, ensuring each weld meets the necessary criteria. Explore more about the intricacies of arc welding.
Test multiple samples to verify reproducibility. If you’re qualifying a stainless steel process, tests could involve 3-5 sample welds across different thicknesses (3 Mm to 25 Mm). Each result must meet your engineering and industry standards to receive approval.
-
Evaluate and Document Results
Next, thoroughly evaluate your qualification test results. Document everything, including test conditions and outcomes. Use visual inspections and Non-Destructive Testing (NDT) techniques such as Ultrasonic Testing (UT) or Radiographic Testing (RT). Record metrics like diameter size or the presence of porosity and cracks.
Your documentation is your proof. Keep records of all tests to support your WPQ. Create a clear, concise report outlining all findings to address future welding challenges and support requalification if needed.
-
Implement Approved Procedures
With your approved WPQ, it’s time to implement those procedures. Train your welders using the specifications you’ve outlined. Clarity is key—understanding every requirement reduces variances in the final product. This phase ensures your workforce aligns with the standard practices you’ve established.
Continue to conduct checks. Regulatory bodies expect you to keep updates on each implemented procedure. Adjust based on site conditions, so stay adaptable to ensure compliance.
We have now covered the steps for obtaining welding procedure qualifications. Next, we will examine the factors that influence these qualifications.
Factors Influencing Welding Procedure Qualifications
So, what factors affect welding procedure qualifications? Let’s dive in!
-
Welding Method Selection
The welding method impacts the process, efficiency, and quality. For example, MIG welding can handle thin materials, while TIG welding is better for precision work. Choosing the wrong method can make it hard to meet the WPQ (Welding Procedure Qualification) requirements. Understanding the costs, including essential materials like welding rods prices, is crucial for budgeting and executing a successful welding project.
-
Material Types and Properties
Material selection directly affects the weld. Metals have different melting points, tensile strengths, and behaviors under heat. For instance, steel (Melting Point Around 1,370 °C or 2,500 °F) requires a different approach compared to aluminum (Around 660 °C or 1,220 °F). It is also important to select the right equipment for home welding projects, which can be explored on the best welding machine for home use.
-
Joint Configuration and Design
The joint design determines how well the components fit together. If the joint isn’t designed properly, it can create weak areas in the weld. In WPQ, joints like butt, lap, and corner must follow specific guidelines to meet quality standards.
-
Environmental Conditions
External conditions can drastically affect weld quality. High humidity or wind can lead to contamination and cooling issues. Maintaining a controlled environment ensures weld integrity and adherence to WPQ standards.
-
Operator Skill Level
The operator’s skill level greatly influences welding quality. Experienced welders know how to adjust parameters based on real-time feedback. A skilled operator can reduce defects by up to 50% compared to a novice welder. Submerged Arc Welding is a process that benefits remarkably from an operator’s skill, as it involves selecting appropriate materials and techniques for optimal results. Understanding the profound impact of SAW welding processes can significantly improve welding outcomes.
So far we covered the elements that affect welding procedure qualifications. Next, let’s look at terms associated with welding qualification.
Related Terms in Welding Qualification
Let’s dig into some terms related to WPQ that are important for your understanding.
Term | Definition | Importance |
---|---|---|
WPS (Welding Procedure Specification) | A document detailing how a specific welding task should be carried out. | Guides the welder on materials, techniques, and settings to ensure consistent quality. |
PQR (Procedure Qualification Record) | A record documenting the results of the welding procedure tests to validate WPS. | Proves that the specified welding procedure can create welds meeting standards. |
Welder Qualifications | Proficiency that certifies a welder’s skill based on performance in specific tasks. | Ensures welders can achieve consistent quality and safety in various conditions. |
Welding Codes | Standards that define how welding should be performed in different industries. | Establishes legal and safety requirements, helping to maintain industry integrity. |
Welding Metallurgy | The study of metal properties and behaviors during the welding process. | Helps welders understand how different materials respond to heat and stress. |
That covers related terms in welding qualification. Let’s now take a look at frequently asked questions.
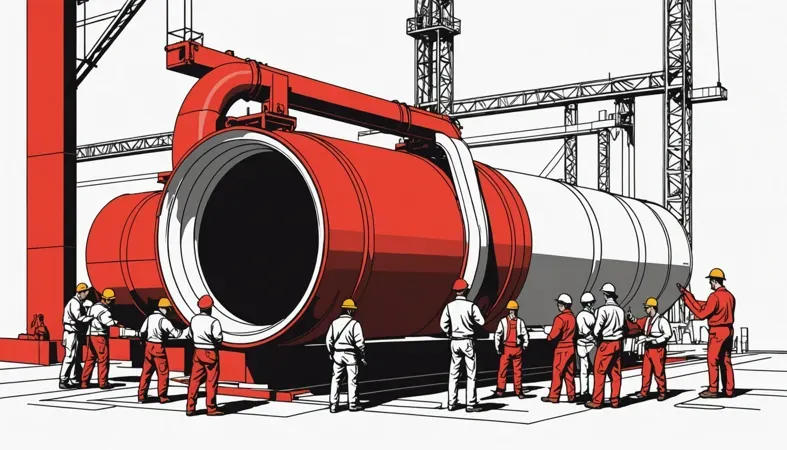
Frequently Asked Questions (FAQs)
Now let us look at some questions I typically get asked.
What is WPQ in Welding?
WPQ in welding stands for Welding Performance Qualification. WPQ ensures a welder can create strong welds to meet specifications. For example, a welder may need to work with materials like carbon steel and qualify under a controlled standard, usually after rigorous testing.
What is the Difference Between WPS, PQR, and WPQ?
The difference between WPS, PQR, and WPQ lies in their functions. WPS (Welding Procedure Specification) provides guidelines for welding, PQR (Procedure Qualification Record) documents the testing, and WPQ evaluates the welder’s capability. Together, they ensure safety and quality in welding processes.
How Long is the WPQ Valid for?
The WPQ is typically valid for up to two years. However, requalification may be necessary if the welder doesn’t perform welding tasks within that timeframe. Regulations may vary, so check the specific requirements applicable in your area or industry.
What Does PQR Stand for in Welding?
PQR stands for Procedure Qualification Record in welding. It’s essential for proving that a particular welding procedure can produce strong welds. The PQR includes details like the materials, welding process, and test results that demonstrate the procedure’s effectiveness.
What is a P Number in Welding?
A P number in welding classifies materials for welding. It helps in selecting the right welding procedure for specific materials. For instance, carbon steels often fall under P numbers 1, while low-alloy steels may range from P numbers 6-9. This classification simplifies the qualification process. Welding equipment also has versatile applications, including its use to thaw frozen pipes.
What is Meant by WPS in Welding?
WPS stands for Welding Procedure Specification. It outlines specific steps for the welding process, including materials and techniques. Following the WPS helps ensure consistency and quality in welding, crucial for critical applications like pressure vessels and pipelines.
Conclusion
Phew, that’s a lot to digest. We covered what welding WPQ is, how it works, types of qualifications, the steps to obtain them, and factors influencing these processes. Additionally, we looked at related topics like WPS, PQR, and the differences between procedures that are essential for understanding the fundamentals of welding.
So, what is welding WPQ, really? In simple terms, it’s the process of qualifying a welder to ensure they can perform according to specific standards. We discussed the steps you need, the various qualifications, and the importance of factors affecting them. Don’t hesitate to get in touch for further assistance with your welding journey.
For additional insights into welding techniques and information, visit What is Welding.
Additional Reading
- American Welding Society (AWS): https://www.aws.org
- International Institute of Welding (IIW): https://www.iiwelding.org
Tyler is a passionate DIY welder and self-taught metal artist with years of hands-on experience transforming raw materials into functional and artistic creations. Specializing in MIG welding, Tyler crafts everything from custom furniture to outdoor sculptures, blending creativity with technical skill. Committed to making welding accessible, Tyler shares practical insights and project inspiration to help beginners and hobbyists confidently explore the world of metalworking.
American Welding Society, Certification, Performance Qualification, Welding, Welding Equipment, Welding Procedures, Welding Standards, Welding Techniques, WPQ