Can You Weld Cast Aluminum? A Guide to Techniques, Tips, and Benefits
Published on: May 4, 2025 | Last modified: March 4, 2025
By: Joe Carter
Cast aluminum is a type of aluminum created by pouring molten metal into a mold. Once it cools, it forms a solid structure, perfect for various uses.
So, if you are wondering can you weld cast aluminum, it’s a good question! It’s crucial to know because welding can change the strength and look of the metal. I’ve worked with cast aluminum before, and I can tell you—it’s not always straightforward!
In this guide, we’ll explore the weldability of cast aluminum, different types of cast aluminum, prerequisites for welding, essential steps to weld, necessary precautions, types of welding you can use, factors affecting weldability, common issues you might face, and aftercare tips. We’ll also dive into key benefits and real-world applications, alongside alternatives to welding cast aluminum. By the end, you’ll have a clearer understanding of how to weld cast aluminum effectively.
Contents
- Can You Weld Cast Aluminum?
- What is Cast Aluminum?
- Types Of Cast Aluminum and Their Weldability
- Prerequisites
- Precautions
- Steps to Welding Cast Aluminum
- Types Of Welding for Cast Aluminum
- Factors Affecting Weldability Of Cast Aluminum
- Welding Techniques for Different Cast Aluminum Alloys
- Common Issues
- Aftercare, Inspection, and Advanced Tips for Welding Cast Aluminum
- Key Benefits Of Welding Cast Aluminum
- Applications You Should Know About
- Exploring Alternatives to Welding Cast Aluminum
- Frequently Asked Questions (FAQs)
- Conclusion
- References
Can You Weld Cast Aluminum?
Yes, you can weld cast aluminum, but it can be tricky. The challenge lies in its composition and oxidation. For the best results, use a spoolgun with ER4047 filler metal, and preheat the material to reduce cracking.
What is Cast Aluminum?
Cast aluminum is a strong, lightweight material made by pouring molten aluminum into molds. It has a density of about 2.7 g/cm³ (0.098 Lb/in³) and excellent corrosion resistance. Cast aluminum also has great thermal and electrical conductivity, making it popular in various industries. About 80% of cast aluminum is used to manufacture products like automotive parts and aerospace components.
Can you weld cast aluminum? That’s a common question among welders. In my experience, welding this alloy can be tricky due to its unique properties, which affect how it accepts the weld. I’ll discuss that shortly.
When I worked on a custom motorcycle frame, cast aluminum proved useful for its lightweight and sturdy nature. We needed precise welds for our design, so understanding how to weld cast aluminum was crucial. I found that knowing how to repair (Fix) cast aluminum without welding was just as important as the welding techniques themselves. It really helped me fine-tune the overall project.
Types Of Cast Aluminum and Their Weldability
What are the types of cast aluminum related to welding?
-
Permanent Mold Cast Aluminum
Permanent mold cast aluminum uses reusable molds to create precise shapes. This type can be welded. To weld permanent mold cast aluminum, clean the surface, preheat to about 200°F (93°C), and use suitable filler materials like 4047 or 4045 for better results. A welding mask offers protection during the welding process and can also provide sufficient eye safety when viewing solar events like an eclipse, as discussed in using a welding mask for eclipse viewing.
-
Die Cast Aluminum
Die cast aluminum is formed under high pressure for strong, thin-walled parts. It’s tricky, but you can weld it. Clean contaminants, use a TIG welder, and consider 5356 filler wire; preheating may help avoid cracking. Selecting the appropriate welding rod is crucial for optimal results; understanding what welding rod to use can make all the difference.
-
Sand Cast Aluminum
Sand cast aluminum is made by pouring metal into sand molds. Yes, it can be welded! To weld sand cast aluminum, clean the weld area, preheat to about 300°F (149°C), and use 4047 filler to improve fusion. For those looking to explore specific techniques in detail, learning how to heliarc weld sand cast aluminum can be particularly useful.
-
Gravity Cast Aluminum
Gravity cast aluminum involves pouring molten metal into a mold using gravity. You can weld this type! Clean thoroughly, preheat to 250°F (121°C), and use 4047 filler for optimal results.
-
Investment Cast Aluminum
Investment cast aluminum is made by creating a wax pattern and coating it with ceramic. You can weld it! To weld investment cast aluminum, ensure you clean the weld site, preheat to about 350°F (177°C), and choose 4047 filler for the best outcome. Selecting the right welding rods is crucial for ensuring optimal weld quality, and exploring the costs of welding rods can provide valuable insights into your project planning.
You should now have a good understanding of various cast aluminum types and their weldability. In the next part, we’ll discuss prerequisites.
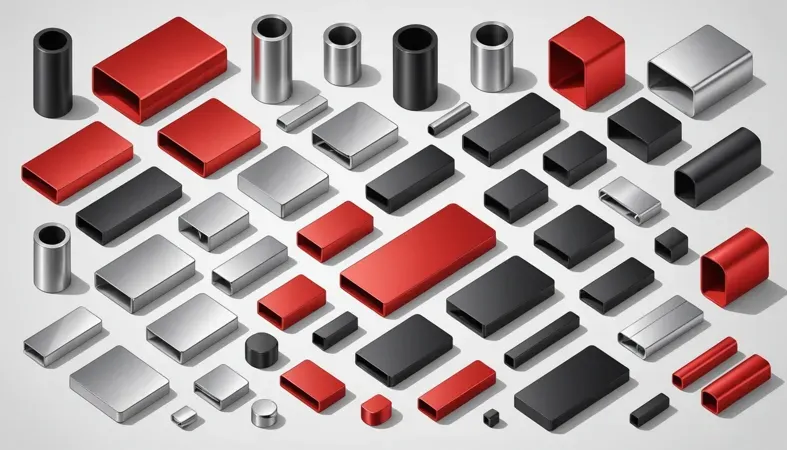
Prerequisites
What do you need to weld cast aluminum?
- Aluminum MIG Welder: You’ll need a MIG welder, like the Lincoln Electric Power MIG 210MP, for clean, strong welds. It’s crucial for penetration and control.
- Aluminum Welding Wire: Get 4047 or 5356 wire, such as Miller Electric ER4047. This wire is vital for accurately joining cast aluminum.
- Welding Flux: Use a flux like Harris 0100210 aluminum welding flux. It prevents oxidation during welding, ensuring quality seams.
- TIG Welding Torch: A torch like the Weldcraft WP-17 is needed for TIG welding; it provides the precise control necessary for intricate aluminum repairs.
- Heat Sink Plate: Obtain a heat sink plate to manage excessive heat. Keeping temperatures below 343°F (175°C) prevents warping and damage.
You should now have a good understanding of the necessary requirements, skills, and knowledge. In the next part, we’ll discuss safety measures.
Precautions
Here are essential safety tips for welding cast aluminum.
- Proper ventilation: Good airflow prevents harmful fumes. Use exhaust fans or a mask like the 3M Respirator.
- Fire safety gear: Wear fire-resistant clothing, like a leather jacket, to avoid burns. Aluminum sparks can ignite easily.
- Eye protection: Always wear welding goggles, such as the Jackson Safety V30, to protect your eyes from bright arcs and particles!
- Component cleaning: Thoroughly clean surfaces with a wire brush or grinder for high-quality welds. Dirt affects weld penetration.
Staying safe is crucial—always take precautions while welding!
You should now have a good understanding of safety measures, necessary preparations, and potential risks. In the next part, we’ll discuss techniques for welding cast aluminum.
Steps to Welding Cast Aluminum
Now, we’ll cover steps to effectively weld cast aluminum—follow each closely to ensure success.
-
Prepare the Workspace
Ensure your workspace is clean and well-lit, with enough room to maneuver. An ideal temperature is 20-25°C (68-77°F) to avoid extreme thermal changes. Use a welding table with proper grounding to prevent electric shock. Dust, moisture, or grease can weaken your welds. In the welding industry, it is crucial to understand what causes most electric shocks to ensure safety and effective operations.
-
Clean the Aluminum Surface
Use a wire brush or grinder to remove oxidation from the aluminum surface. You should see a shiny surface underneath; any black residue means it’s still dirty. Then, wipe the surface with a clean cloth and a solvent like acetone to remove all contaminants. A clean surface dramatically boosts your weld quality. Ensuring proper safety procedures is crucial, especially knowing what parts to disconnect when welding on a vehicle.
-
Select Appropriate Filler Material
Choose filler material that matches your base aluminum. For most cast aluminum, ER4047 (Or ER4045) works well, with a melting point around 660°C (1220°F). Check the aluminum alloy type first to ensure compatibility. Mismatched filler can result in weak welds or warping; don’t take shortcuts here!
-
Set Up Welding Equipment
Configure your welding machine for the process you’re using. For TIG welding, set the amperage between 90-150 A for cast aluminum. Ensure gas flow is steady at about 12-15 liters per minute (7-9 Cubic Feet Per Hour) when using argon. A fine-point tungsten electrode (1.6 Mm or 0.0625 Inches) typically provides better arc stability.
-
Perform Test Welds
Before starting, do some test welds on scrap pieces of similar cast aluminum. This helps fine-tune your voltage and travel speed for optimal results. Aim for a travel speed of 70-110 mm/min for consistent fusion. If the weld looks uneven or has patches, adjust your settings until the weld bead looks uniform.
That covers the steps for welding cast aluminum. Let’s now take a look at the various types of welding for cast aluminum.
Types Of Welding for Cast Aluminum
Let’s explore the different types: Gas Tungsten Arc Welding, Metal Inert Gas Welding, Stud Welding, Shielded Metal Arc Welding, and Electron Beam Welding.
-
Gas Tungsten Arc Welding
This method uses a non-consumable tungsten electrode to create the weld. It’s effective for thin cast aluminum sections, offering better heat control. Typically, use a direct current (DC) electrode negative (DCEN) setting.
-
Metal Inert Gas Welding
Known as MIG welding, this method feeds a continuous solid wire electrode. It’s ideal for thicker cast aluminum pieces and usually involves an argon gas shield to prevent contamination, making it popular among welders.
-
Stud Welding
In stud welding, a stud is attached to cast aluminum by melting its end and pressing it against the workpiece. This method is effective for joining metal fasteners without pre-drilling and is commonly used in manufacturing and construction.
-
Shielded Metal Arc Welding
This traditional method employs a consumable electrode coated in flux. While less common for aluminum, it can be effective with the right electrode. Good joint preparation is crucial for proper penetration when welding cast aluminum.
-
Electron Beam Welding
Electron beam welding uses high-velocity electrons to melt the base metal. It’s highly precise and suitable for complex shapes and heavy cast aluminum sections. However, it requires a vacuum environment, making it less accessible for DIY projects.
Factors Affecting Weldability Of Cast Aluminum
What factors impact the ability to join cast aluminum parts effectively?
-
Aluminum Alloy Composition
The specific alloy you’re working with can greatly affect weldability. For example, alloys like 356 and 535 contain silicon, which facilitates welding. However, high-silicon alloys may crack, so understand your alloy’s properties.
-
Presence Of Impurities
Impurities like dirt, oil, and rust can undermine your weld. Ideally, aluminum should contain less than 0.1% contaminants. Always clean surfaces thoroughly to enhance joint quality.
-
Welding Technique
Consider using TIG (Tungsten Inert Gas) or MIG (Metal Inert Gas) welding for better results with cast aluminum. Each method requires different settings—low heat input minimizes distortion and prevents porosity. Understanding welding by metals can also help you choose the right technique for your project.
-
Thermal Effects
Heat can cause warping and cracking in cast aluminum. Keep heat input below 8-10 kJ/m (For Joints), and preheating can enhance quality by reducing stress. Monitor temperatures carefully!
-
Base Metal Thickness
Thinner metals (Under 5 Mm or 0.2 Inches) can be challenging. You may need to adjust your technique or settings to avoid burn-through. Thicker pieces can handle more heat, yielding a stronger joint.
Welding Techniques for Different Cast Aluminum Alloys
Different aluminum alloys require unique welding techniques to achieve the best results. Let’s break down those techniques.
Alloy Type | Welding Method | Temperature Control | Filler Material |
---|---|---|---|
356.0 | TIG Welding | Preheat to 250°F (121°C) | ER4047 |
319.0 | MIG Welding | Preheat to 300°F (149°C) | ER4045 |
A356.0 | Welding with Heat Stick | Keep below 350°F (177°C) | ER5356 |
ADC12 | Gas Welding | Preheat to 200°F (93°C) | ER4047 |
Each alloy type demands a specific approach. By following these guidelines, you’ll ensure a stronger bond and reduce the likelihood of common welding issues.
Common Issues
Let’s look at unique problems specific to cast aluminum.
-
Cracking During Welding
Cracking in cast aluminum often occurs due to improper heating. Preheat the area to 300°F (150°C) to troubleshoot. Use a slower cooling method, like enclosing it in a blanket.
-
Poor Metal Fusion
Poor fusion can result from inadequate workmanship. Ensure clean edges and proper fit-up. Use the TIG (Tungsten Inert Gas) process for better control.
-
Gas Porosity
Gas porosity occurs when impurities are trapped in the weld pool of cast aluminum. Look for small pinholes and rough textures. Use high-purity argon gas at about 15-20 CFH (Cubic Feet Per Hour) to prevent this.
-
Heat-affected Zone Distortion
The heat-affected zone (HAZ) in cast aluminum may distort if not managed. Check for warping or surface changes. Minimize distortion by welding in small sections.
-
Inconsistent Weld Quality
Inconsistent welds on cast aluminum can indicate irregular parameters. Look for uneven beads. Adjust your travel speed and voltage settings for uniform results.
Aftercare, Inspection, and Advanced Tips for Welding Cast Aluminum
Here’s crucial advice on aftercare, inspection, and expert tips for finishing your work with cast aluminum.
Aftercare Tips
After welding, cool the cast aluminum immediately with water (H₂O) or air to maintain structural integrity. Avoid letting it sit in a hot area for more than five minutes to minimize distortion. Finally, apply an anti-corrosive primer, like a zinc-rich coating, before any protective paint to ensure long-lasting durability.
Inspection Guidelines
Inspection involves checking weld penetration. Ensure at least 60% penetration for optimal strength using a standard ultrasonic testing tool. I use the Sonatest VEO to detect internal defects that are invisible to the naked eye. Common casting defects, like porosity, require careful attention; even a single void can compromise strength.
Expert Tips
Here’s a pro tip from my experience—always preheat the cast aluminum to at least 93°C (200°F) using an infrared heat gun for better fusion. This effectively reduces cracking caused by thermal shrinkage. Also, invest in a TIG (Tungsten Inert Gas) rig for precision; maintaining a balanced amperage of 120–180 amps helps avoid burn-through and ensures strong welds.
Key Benefits Of Welding Cast Aluminum
The main benefit of welding cast aluminum is its strength. When I worked on a custom trailer, it was useful for creating durable joints that could withstand heavy loads.
Additionally, it offers excellent corrosion resistance, making it suitable for harsh environments. You can also achieve lightweight structures, reduce assembly costs, and increase design flexibility.
Applications You Should Know About
People use welding on cast aluminum for various practical tasks. It has unique applications, such as:
- Automotive Repair: You can repair cracked cast aluminum engine blocks and components. It’s popular because it’s cost-effective and restores functionality.
- Aerospace Components: Engineers weld cast aluminum parts for aircraft to save weight and maintain strength. This application is critical due to high safety standards.
- Marine Structures: Boats often use welded cast aluminum frames to withstand harsh environments. Its corrosion resistance makes it the go-to choice.
- Artistic Sculptures: Artists often weld cast aluminum to create unique sculptures and installations. This technique allows for creative expression with durable materials.
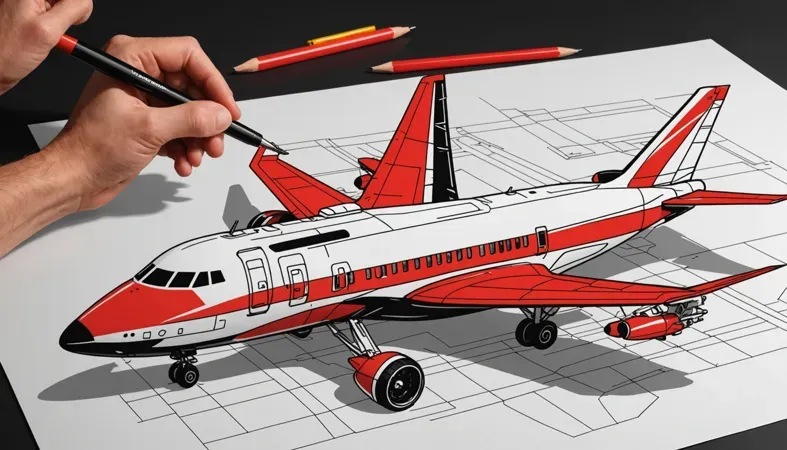
Exploring Alternatives to Welding Cast Aluminum
There are solid alternatives to achieve results similar to welding cast aluminum. For instance, consider epoxy adhesives such as J-B Weld or Loctite for durable bonding. In my professional journey, I’ve found that using a combination of mechanical fasteners, like rivets, works well for certain applications and provides strong holds without needle-sharp heat.
Additionally, you can use metal-filled epoxies, which can take harsh conditions while providing a smoother finish. These methods sometimes offer easier applications and less risk of cracking than welding. So, next time you face this dilemma, keep these options in mind!
Frequently Asked Questions (FAQs)
Here are some questions I typically get asked about welding techniques and cast aluminum.
What is the Best Way to Weld Cast Aluminum?
Yes, the best way to weld cast aluminum is through MIG welding or TIG welding. MIG welding offers speed and ease while TIG welding delivers precision. Both methods work well when temperatures range from 200 °C to 300 °C (392 °F to 572 °F), minimizing warping and ensuring strong welds.
Can You Fix Broken Cast Aluminum?
Yes, you can fix broken cast aluminum by using welding or using adhesive methods. For larger projects or structural repairs, welding, particularly with a MIG or TIG setup, provides a stronger bond. Repairs can typically withstand stress if done properly with the right temperature control techniques.
What Type Of Welding Rod for Cast Aluminum?
The best type of welding rod for cast aluminum is 4047 or 5356 aluminum rods. These rods provide compatible melting points and excellent fusion with aluminum. They melt at around 660 °C (1220 °F), ensuring proper bonding without overheating the base material.
Can You Weld Cast Aluminum With a Stick Welder?
Yes, you can weld cast aluminum with a stick welder. Use specialty aluminum rods designed for stick welding, like EPAW-4047. However, stick welding is less common for aluminum due to higher thermal distortion risks, which you’ll want to avoid in your projects.
How Do You Weld Cast Aluminum?
To weld cast aluminum, first clean the surface thoroughly and preheat to avoid cracking. A recommended preheating range is 200 °C to 300 °C (392 °F to 572 °F). Then, choose MIG or TIG welding, ensuring you use suitable filler material for the best results.
How to Repair Cast Aluminum Without Welding?
You can repair cast aluminum without welding by using epoxy or adhesive methods. Products like J-B Weld work effectively and are heat-resistant. They’re great for small fixes and can bond well on surfaces, saving both time and hassle without the need for welding equipment.
Conclusion
I hope this gave you what you needed on whether you can weld cast aluminum. We covered what cast aluminum is, types and their weldability, prerequisites, steps to weld, precautions, and common issues. We also explored the benefits of welding, applications, and alternatives to welding cast aluminum.
So, can you weld cast aluminum? Yes, you can. It requires the right techniques, like using proper welding rods and understanding the factors that affect weldability, such as alloy composition and heat treatment. Contact me if you’d like more guidance on how to weld cast aluminum effectively.
For further insights and information on welding techniques and practices, feel free to explore What is Welding.
References
- Miller Electric. (2021). Welding Safety: A Complete Guide. Appleton, WI: Miller Electric Manufacturing Company.
Joe Carter is a retired welding professional with over 40 years of hands-on experience in the industry, spanning ship repair, structural welding, and even underwater projects. Joe is a master of MIG, TIG, and Stick welding. Passionate about mentoring the next generation of welders, Joe now shares his decades of expertise and practical insights to help others build rewarding careers in welding.
Cast Aluminum, Metallurgy, MIG Welding, Safety Tips, TIG Welding, Welding, Welding Equipment, Welding Table, Welding Techniques