What Causes Most Electric Shock in the Welding Industry? Safety, Prevention, Protection
Published on: January 3, 2025 | Last modified: March 4, 2025
By: Tyler James
Electric shock happens when electricity flows through your body. It can cause injury, pain, or even death, depending on the voltage and duration of exposure.
People often ask what causes most electric shock in the welding industry. It’s important to know, as proper safety measures can save lives. From my experience, a sudden shock can be incapacitating and lead to serious mishaps if safety isn’t prioritized.
In this article, you’ll learn about types of electric shocks in welding, steps to prevent electric shock while welding, factors that influence incidents, and how to address common problems. You’ll also discover tips for inspection, aftercare, and when to try a different approach. Understanding how to protect yourself from electric shock when welding is crucial for safety, right?
Contents
- What Causes Most Electric Shock in the Welding Industry?
- What Causes Shocks When Welding?
- Types Of Electric Shocks in the Welding Industry
- Steps to Prevent Electric Shock in the Welding Industry
- Factors Influencing Electric Shock Incidents in Welding
- Common Myths About Electric Shock in Welding
- The Role of Training in Electric Shock Prevention
- How to Address Common Problems
- Aftercare, Inspection, and Advanced Tips for Electric Shock Prevention
- Applications Of Electric Shock Prevention in the Welding Industry
- When to Try A Different Approach
- Frequently Asked Questions (FAQs)
- Conclusion
- References
What Causes Most Electric Shock in the Welding Industry?
Electric shock often happens due to improper grounding or damaged equipment. Welders use high-voltage machines, which can easily lead to accidents if safety measures aren’t squared away. Always check your gear to stay safe. Selecting the right power source is crucial for optimal performance in welding tasks, and understanding what size generator to run a 140 amp welder ensures safety and efficiency.
.
What Causes Shocks When Welding?
Electric shock in welding mainly arises from the electrical current in the equipment. When you weld, the welding arc operates at voltages between 20 to 100 V (Volts), while the current can reach hundreds of A (Amps). If you complete the circuit by touch—such as holding metal parts—electricity can flow through your body. Statistics show that electric shock accounts for about 30% of welding injuries each year.
Let’s dive deeper. Many welders underestimate how wet conditions or poor insulation can increase the risk of electric shock. Understanding the link between higher voltage and greater risk is crucial.
In my experience, I recommend investing in proper protective gear. This equipment reduces the chance you’ll get shocked while welding. Always check your equipment, and remember, grounding isn’t just a suggestion; it’s essential to prevent electric shock in welding.
Types Of Electric Shocks in the Welding Industry
What types of electric shocks might you encounter while welding?
-
Direct Electric Shock
Direct electric shock occurs when a welder touches live wires or equipment. This often happens when the equipment’s insulation fails, allowing current to flow unexpectedly. To prevent this shock, ensure all welding tools, like arc welders, have intact insulation and proper grounding.
-
Indirect Electric Shock
Indirect electric shock happens when current flows through a conductive object that the welder touches, rather than directly through their body. For example, if welding equipment malfunctions, current can leak to the framework. Regular maintenance checks on equipment are crucial to avoid this.
-
Static Electric Shock
Static electric shock occurs from the sudden discharge of accumulated static electricity. When working with synthetic materials or moving around an insulated surface, like plastic mats, you might feel it. To reduce these shocks, use anti-static mats and wear grounded footwear.
-
Capacitive Electric Shock
Capacitive shock arises when electrical potential builds up on a body due to contact with electrified equipment. This is common in dry environments. To avoid it, use proper grounding and discharge techniques before handling machinery.
-
Ground Fault Electric Shock
Ground fault electric shock occurs when a wiring fault allows current to flow to the ground. This can be especially dangerous with wet equipment. To protect yourself, use Ground Fault Circuit Interrupters (Gfcis) as safety devices in your work area.
You should now have a good understanding of different electric shock types, their causes, and effects. In the next part, we’ll discuss prevention measures.
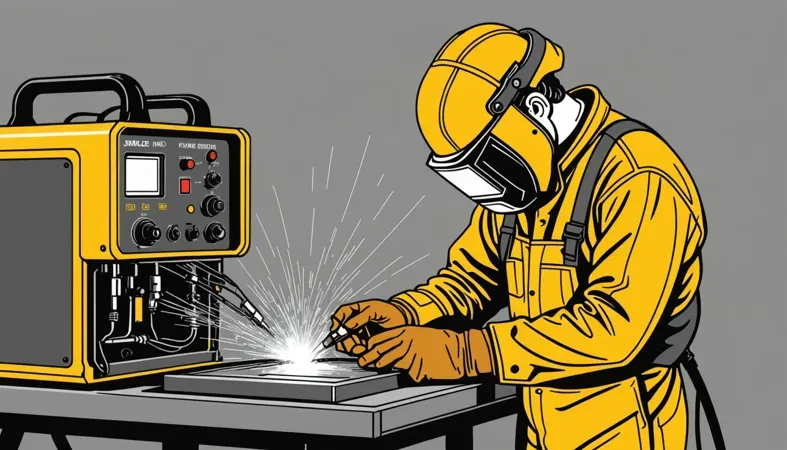
Steps to Prevent Electric Shock in the Welding Industry
Here are steps to avoid electric shock in welding operations.
-
Learn Proper Techniques
Mastering welding techniques is crucial. Follow best practices for holding the electrode and maintaining distance. Keeping your hands dry minimizes the chance of shock. Always position yourself to avoid movement or contact with wet surfaces.
-
Use Appropriate Personal Protective Equipment
Wearing the right PPE significantly reduces exposure risks. A welding helmet, gloves, and insulated footwear are essential. Choose gloves with an insulation rating of at least 1,000 volts (1,000 V). A quality helmet can mean the difference between a close call and serious injury.
-
Maintain Equipment Regularly
Regularly check your welding equipment for wear and tear. Inspect cables for frays or breaks, as these can cause serious shocks. Damaged cables are a common cause of electric shock in welding. Replace any cables showing damage immediately.
Mastering different welding positions is essential for safety and success, especially techniques like 3G welding.
-
Ensure Proper Grounding
Effective grounding is essential. This process eliminates voltages that can cause shock. Ensure your welder’s ground clamp is securely connected, as a loose clamp significantly raises shock risks. Don’t underestimate the importance of reliable grounding—it’s a key preventative measure.
-
Conduct Safety Inspections
Establish a routine for safety inspections. Review all setups, from ground connections to welding equipment, to ensure they meet the standards. By implementing proper welding safety precautions, you can conduct these checks daily before work. A little extra time here could prevent a dangerous accident later.
Additionally, knowing about preventing cancer from welding can significantly improve workplace safety.
We covered steps to avoid electric shock in welding. Next, we will discuss factors that influence electric shock incidents in welding.
Factors Influencing Electric Shock Incidents in Welding
What factors lead to electric shock during welding? Understanding these can save lives.
-
Welding Environment Conditions
Poor conditions, like wet floors and cluttered spaces, increase the risk of electric shock. Studies show that up to 30% of welding accidents occur in unsafe environments.
-
Electrical Equipment Condition
Damaged cables and faulty equipment raise the probability of shock. In fact, 50% of incidents can be traced to worn-out gear.
-
Operator Experience Level
Choose experienced welders. Novices may not recognize dangers, leading to shocks. It’s crucial—over 70% of electric shock victims were inexperienced.
-
Type Of Welding Process Used
Certain processes, like arc welding, are more prone to electric shocks. Arc welding operates at higher currents (Up to 600 A), increasing potential hazards.
-
Moisture Presence
Moisture makes welders more vulnerable to electric shock. Even a little dampness can significantly boost conductivity, raising risks substantially.
You should now have a good understanding of electric shock risks, causes, and prevention measures. In the next part, we’ll discuss common misconceptions regarding electric shock in welding.
Common Myths About Electric Shock in Welding
There are plenty of misconceptions about electric shock in the welding industry. Let’s debunk a few.
-
Myth: Only High Voltage Causes Electric Shock
Fact: Electric shock can occur at lower voltages as well. Even 24 V (Volts) can lead to serious injury if conditions are right, such as wet environments.
-
Myth: Electric Shock Only Happens During Active Welding
Fact: Shock can also occur while setting up equipment or during maintenance. Always treat equipment as live until verified otherwise.
-
Myth: Rubber Boots Are Enough Protection
Fact: While rubber boots help, they aren’t a substitute for proper grounding and insulated gear. Combining multiple safety measures is key.
-
Myth: Small Electric Shocks Are Harmless
Fact: Any electric shock can be dangerous. Even small shocks can lead to loss of control, resulting in serious accidents. Don’t take any shock lightly!
You should now have a good understanding of prevalent misconceptions regarding electric shock in welding. In the next part, we’ll discuss the importance of training in welding to prevent electric shock.
Submerged Arc Welding techniques can also play a crucial role in enhancing safety, and you can explore more about SAW welding processes.
.
The Role of Training in Electric Shock Prevention
Training isn’t just a box to check—it’s essential for safety. Here’s why:
Aspect | Importance | Effectiveness |
---|---|---|
Identifying Hazards | Helps workers recognize risky situations. | Can reduce incidents by up to 40%. |
Proper Equipment Usage | Ensures correct operation of machines. | Improves compliance with safety standards. |
Emergency Response | Prepares workers for shock incidents. | Can save lives during electrical accidents. |
Ongoing Refresher Courses | Keeps safety practices fresh in mind. | Maintains awareness of evolving standards. |
How to Address Common Problems
Let’s look at issues regarding electric shock.
-
Improper Grounding Techniques
Electric shock can occur with poor grounding. Check grounding connections regularly and use a multimeter to ensure resistance is 0 ohms.
-
Use Of Damaged Equipment
Electric shock can happen with frayed wires or worn plugs. Replace faulty equipment immediately. Inspect cables before each use.
-
Lack Of Safety Training
Electric shock can result from inadequate safety training. Schedule regular training sessions. Understanding hazards keeps workers safer.
-
Ignoring Proper Maintenance
Electric shock can stem from neglected maintenance. Develop a maintenance schedule for electrical systems. Routine checks catch issues before they escalate.
-
Workplace Environmental Hazards
Electric shock can arise in wet or cluttered environments. Keep areas dry and organized, and ensure adequate lighting to prevent trips and falls.
Aftercare, Inspection, and Advanced Tips for Electric Shock Prevention
Here’s some crucial aftercare and inspection information to prevent electric shock in welding.
Aftercare Tips
After encountering electric shock risks, check the power supply immediately. Switch off the main circuit breaker (CB) and test with a multimeter to ensure it’s de-energized—look for less than 1 volt (V). Perform a quick visual inspection of equipment, focusing on wires for any damage, burns, or exposed conductors.
Inspection Techniques
Begin by checking your welder (E.g., Lincoln Electric POWER MIG 215) for insulation integrity. Look for at least 2 megohms (MΩ) when testing insulation resistance. Inspect the ground connection; a poor ground can significantly increase electric shock risk.
Expert Tips
I recommend using a digital clamp meter to evaluate leakage current, which should always remain below 30 milliamps (Ma). Make it a habit to implement lockout/tagout (LOTO) procedures during maintenance. Finally, regularly assess your workplace layout; ensure wet areas are at least 1.5 meters (5 Feet) away from energized parts.
Applications Of Electric Shock Prevention in the Welding Industry
I’ve seen people use electric shock prevention devices in welding. They have several applications, such as:
- Insulating Material: Used in welding fixtures to prevent current transfer. This is crucial for tasks involving direct skin contact with conductive materials. It’s popular for protecting workers.
- Ground Fault Circuit Interrupters (GFCI): Essential when operating welders near water sources; they cut off power upon detecting water contact. They’re widely used on job sites for safety.
- Protective Gear: Specialized gloves and boots with insulating properties help reduce shock risks. In most welding environments, these are standard safety practices.
- Voltage Regulation Systems: Commonly used in arc welding to control output voltage and limit shock hazards. Their use is growing due to stricter safety regulations in the industry.
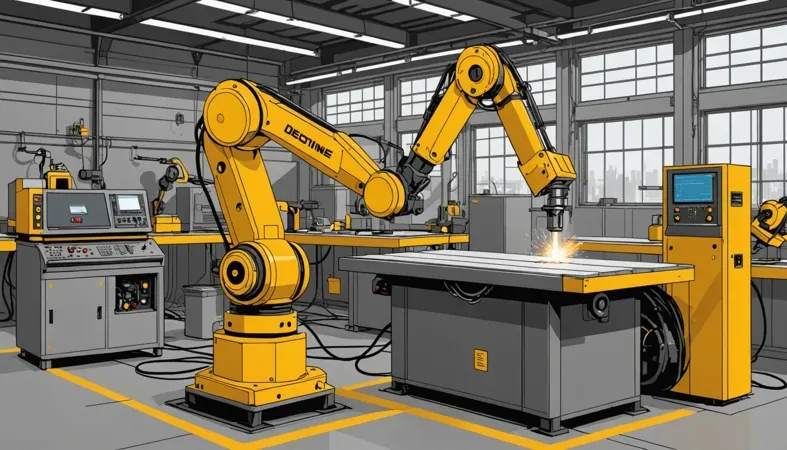
When to Try A Different Approach
If you’re looking for safer alternatives in your welding work, consider using insulated tools like those from Klein Tools. They can reduce the risk of electric shock significantly. Through years of practice, I’ve come to understand that employing proper PPE, such as dielectric gloves, offers extra protection during high-voltage tasks.
You might also explore the use of low-voltage systems, such as MIG or TIG welding setups. These options can minimize hazards while still providing excellent results. Ultimately, understanding the equipment and practices will keep you safer on the job, so make the effort to choose wisely.
Frequently Asked Questions (FAQs)
Now let us look at some questions I typically get asked about electric shock in welding.
Can You Get Shocked While Welding?
Yes, you can get shocked while welding. Electric shock can occur if there’s a faulty connection or improper grounding in the equipment. In the U.
S., around 1,000 workers suffer injuries from electric shocks every year, emphasizing the need for safety measures.
Exposure to fumes from welding galvanize-coated materials poses serious health risks when welding galvanized steel.
How Do You Protect Yourself From Electric Shock When Welding?
You can protect yourself from electric shock while welding by using proper gear and ensuring your welding machine is properly grounded. Wearing insulated gloves and non-conductive shoes is critical, as it can reduce your risk of receiving a shock significantly.
How to Avoid Electric Shock in Welding?
To avoid electric shock in welding, always inspect your equipment before use. Regular maintenance helps prevent short circuits and equipment failure. Utilizing circuit breakers set at 30 mA can help cut off current before it causes injury. Understanding the symbols and specifications on welding blueprints can further ensure safety during your projects. Discover more on how to read welding blueprints effectively.
Can a Shock From a Welder Kill You?
Yes, a shock from a welder can kill you. Electric currents as low as 100 mA (0.1 A) can be fatal across the heart if they pass through it. Awareness and adherence to safety protocols are critical for your protection. Proper safety measures also help prevent physical harm, such as eye injuries that can occur during welding. For more information on protecting your eyes, you can read about how welding can affect your eye health.
Can You Shock Yourself Welding?
Yes, you can shock yourself welding. Contact with the open circuit of a welder can lead to electric shock. Always ensure hands and surfaces are dry, and avoid welding in wet environments to minimize this risk.
Conclusion
That’s everything I wanted to share with you. We covered the causes of electric shock, types of shocks, prevention steps, factors influencing incidents, and tips for aftercare. Additionally, we discussed approaches for addressing common problems and when to consider alternative methods.
Hopefully, I was able to impart some of my experience on what causes most electric shock in the welding industry. In simple terms, electric shocks often result from improper grounding, inadequate equipment inspection, and poor practices. Remember, worker safety hinges on knowing these hazards and employing prevention steps.
To enhance your understanding of welding and ensure a safer work environment, feel free to explore our homepage: What is Welding.
References
- ISO. (2017). ISO 3834: Quality Requirements for Fusion Welding of Metallic Materials. Geneva, Switzerland: ISO.
- Canadian Welding Bureau (CWB): https://www.cwbgroup.org
Tyler is a passionate DIY welder and self-taught metal artist with years of hands-on experience transforming raw materials into functional and artistic creations. Specializing in MIG welding, Tyler crafts everything from custom furniture to outdoor sculptures, blending creativity with technical skill. Committed to making welding accessible, Tyler shares practical insights and project inspiration to help beginners and hobbyists confidently explore the world of metalworking.
Electric Shock Prevention, Grounding Techniques, Personal Protective Equipment, Regulations, TIG Welding, Welding, Welding Equipment, Welding Equipment Maintenance, Welding Safety, Welding Techniques, Workplace Safety