Can You Weld Aluminium With a MIG? Insights, Steps, and Tips
Published on: January 2, 2025 | Last modified: March 4, 2025
By: Joe Carter
Aluminium is a lightweight metal known for its strength and resistance to corrosion. It’s used in many industries due to its properties and versatility.
Many people have asked me, can you weld aluminium with a mig? It’s crucial to understand how to weld aluminium properly. From my experience, when using the right equipment and techniques, the results can be excellent and durable.
In this guide, we’ll explore whether you can weld aluminium with a MIG welder, the different types of aluminium and their weldability, prerequisites for welding, steps to follow, safety tips, MIG welding techniques, factors affecting weldability, common issues, and essential aftercare. You’ll gain valuable insights that will help you master the art of welding aluminium.
Contents
- Can You Weld Aluminium With a MIG?
- What is Aluminum?
- Types Of Aluminum and Their Weldability
- Prerequisites
- Steps to Weld Aluminum With a MIG Welder
- Safety Tips
- Types Of MIG Welding Techniques for Aluminium
- Factors Affecting Aluminum Weldability
- Common Issues
- Aftercare, Inspection, and Advanced Tips for Aluminum Welding
- Key Benefits
- MIG Welding Aluminum vs. TIG Welding
- Applications Across Different Fields
- Other Options for Welding Aluminium
- Frequently Asked Questions (FAQs)
- Conclusion
- Additional Reading
Can You Weld Aluminium With a MIG?
Yes, you can weld aluminium with a MIG. It’s a bit tricky due to the melting point and oxide layer on aluminium. To do it right, use a spool gun and 4047 aluminum wire for the best results.
What is Aluminum?
Aluminum is a lightweight, silvery-white metal with a density of about 2.7 g/cm³ (0.0975 Lb/in³), making it much lighter than steel. It’s known for its corrosion resistance due to a thin layer of oxide that forms naturally. With a melting point of 660°C (1220°F), aluminum’s unique properties make it ideal for various applications, from automotive parts to aerospace components.
Now, let’s address a common question—can you weld aluminum with a MIG? In my welding experience, this process can be quite specialized. When I first tried to weld aluminum with a MIG, I realized how crucial the settings and technique were for success.
I’ve heard from friends who shared their experiences. They often mention the careful adjustment of their MIG welder settings to achieve better results with aluminum. Regarding the question, “Can I weld aluminum with a MIG welder?” the consensus is clear: you can, but it requires practice and the right equipment to create a strong weld.
Types Of Aluminum and Their Weldability
-
6061 Aluminum
6061 is a versatile alloy known for good mechanical properties. You can use a MIG welder with this alloy. To weld 6061 effectively, adjust settings—use 4047 filler wire, set the voltage to about 18-20 volts, and maintain a travel speed of 10-20 inches per minute (254-508 Mm/min).
-
5052 Aluminum
5052 is strong and corrosion-resistant, making it suitable for marine applications. You can MIG weld this type too. Use ER5356 filler wire, set your machine to around 25 volts, and maintain a slower travel speed of about 5-10 inches per minute (127-254 Mm/min).
-
2024 Aluminum
This alloy is primarily used in aerospace due to its high strength-to-weight ratio. MIG welding 2024 is possible but challenging. Preheat it to 300°F (150°C), use 4047 filler wire, and operate at 22-24 volts. For a comprehensive overview of the various components involved, explore what components make up a GMA welding system.
-
7075 Aluminum
7075 is one of the strongest aluminum alloys but is less weldable. You can still use a MIG welder. Preheat the metal to about 300°F (150°C), use 5356 filler wire, and keep the voltage between 24-26 volts.
-
3003 Aluminum
3003 is a commonly used alloy due to its good workability and moderate strength. It’s easy to MIG weld. For strong welds on 3003, use 4047 filler wire, aim for 20 volts, and maintain a travel speed of 10-15 inches per minute (254-381 Mm/min).
We have now covered the various types of aluminum and their weldability. The next section will discuss prerequisites.
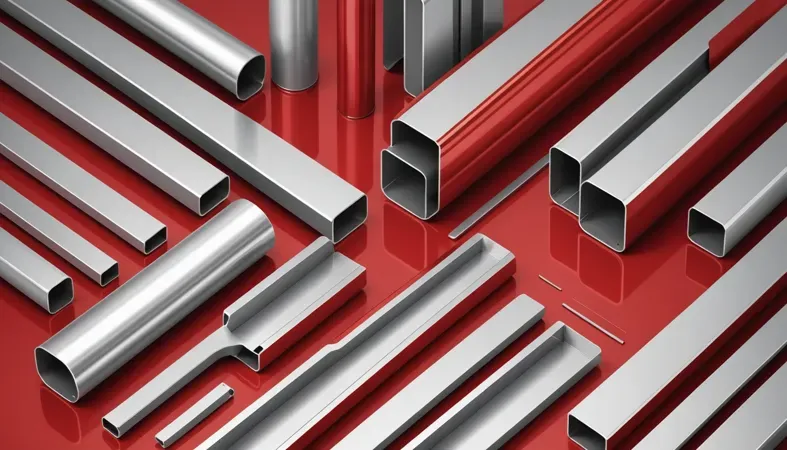
Prerequisites
What do you need to weld aluminum with a MIG?
- MIG Welder: Use a MIG welder like the Miller Multimatic 215 or Lincoln Electric Power MIG 140 to achieve strong aluminum welds.
- Aluminum MIG Wire: Choose aluminum filler wire, such as ER4047 or ER5356. It’s essential for effectively bonding aluminum.
- Spool Gun: A spool gun, like the Miller Spoolmate 150, is needed for optimal feeding of aluminum wire, preventing kinks and misfeeds.
- Argon Gas: Use pure argon gas (At Least 99.99% Purity). It shields the weld, ensuring high-quality results and better bead appearance.
So far we covered the necessary prerequisites. Let’s look at the upcoming steps for welding aluminum with a MIG welder.
Steps to Weld Aluminum With a MIG Welder
Here are the steps for successfully welding aluminum using a MIG welder. Follow them for a solid weld.
-
Prepare the Work Area
Clear debris or flammable materials from your workspace. Ensure good ventilation and plenty of light. Use a sturdy, flat surface to stabilize your welding. A clean area prevents contamination of your aluminum welds, which is crucial for understanding different welding processes.
-
Clean the Aluminum Surface
Use a stainless steel wire brush to remove oxidation from the aluminum surface. Oxidation can create weak spots in your weld. After brushing, wipe down the surface with isopropyl alcohol (At Least 91%) to eliminate grease or moisture that can interfere with the welding process.
-
Set Up the MIG Welder
Adjust your MIG welder settings for aluminum. Set the voltage between 18-22 volts and the wire feed speed between 300-400 inches per minute (760-1000 Mm/min). For best results, use an Argon gas mixture; it improves arc stability and reduces spatter. Proper settings can make a significant difference, so don’t skip this part!
If you need to adapt your equipment further, you might explore converting a 220 welder to 110.
-
Perform the Welding Process
Start welding by positioning the torch at a 5-15 degree angle. Maintain a travel speed of 4-12 inches per minute (102-305 Mm/min), adjusting for the thickness of the aluminum. Create a steady motion, like moving in a straight line, to avoid overheating the metal. Practice on scrap pieces to perfect your technique before tackling the final piece!
We’ve wrapped up the process for MIG welding aluminum. Let us turn our attention to essential safety tips.
Safety Tips
Let’s quickly explore essential precautions for welding aluminum.
- Proper Ventilation: Ensure good airflow to prevent fume buildup. Install an exhaust fan from your local hardware store.
- Heat Management: Keep surrounding materials away to avoid fires. Use flame-retardant barriers, like those from the Hoodsman line.
- Protective Gear: Wear appropriate gloves and eye protection. I recommend Lincoln Electric welding gloves; they withstand high heat!
- Check Equipment: Ensure your MIG welder is suitable for aluminum. The Hobart 500559 works well for this task.
Remember, following these safety precautions is vital for your safety.
You should now have a good understanding of safety guidelines, precautions, and best practices. In the next part, we’ll discuss MIG welding techniques for aluminum.
Types Of MIG Welding Techniques for Aluminium
Let’s explore the different types of MIG welding techniques for aluminium. We’ll cover Short Circuit Transfer, Globular Transfer, Spray Transfer, Pulsed MIG Welding, and the Weaving Technique.
-
Short Circuit Transfer
Short Circuit Transfer (SCT) is ideal for welding thin aluminium sections, usually under 1/8 inch (3.2 Mm). In this technique, the wire forms a short circuit with the workpiece before melting, creating minimal heat input. It’s suitable for positions like vertical or overhead, making it versatile for various aluminium welding applications.
-
Globular Transfer
Globular Transfer occurs when molten metal forms large droplets that transfer to the weld pool. This method can produce more spatter, so it’s not always preferred for aluminium. Nevertheless, for thicker aluminium materials, it can achieve good penetration but requires post-weld cleanup.
-
Spray Transfer
Spray Transfer is highly effective for welding thicker aluminium (Over 1/8 Inch, or 3.2 Mm). In this process, tiny droplets spray from the wire into the weld area. You’ll achieve a smoother finish across a range of travel speeds, making this technique popular among professionals.
-
Pulsed MIG Welding
Pulsed MIG Welding improves control over heat and penetration, making it ideal for welding heat-sensitive materials like aluminium. It uses a series of pulses to provide a controlled arc, which helps reduce distortion. This method allows you to work on both thick and thin materials while keeping your welds precise. Understanding what size wire for a welder is crucial when setting up for specific materials and thicknesses, which ensures optimal welding outcomes.
-
Weaving Technique
The Weaving Technique is a manual approach that enhances bead shape and penetration on larger welds. Instead of moving in a straight line, you guide the welding gun in a weaving pattern, which can be effective for horizontal welds. This method offers better heat control and results in an impressive finished product.
Factors Affecting Aluminum Weldability
What factors influence welding aluminum using the MIG process?
-
Material Thickness
Material thickness significantly impacts weld quality. For MIG welding, aluminum up to 6 mm (0.24 In) can be welded easily, but thicker aluminum requires specific settings and techniques.
-
Joint Design
Proper joint design ensures better weld penetration. Designs like butt joints or lap joints help achieve smoother welds, reducing the risk of defects.
-
Welding Speed
Maintain a steady speed. Faster speeds can result in weak welds, while too slow can cause burning. Ideal speeds are around 200 mm/min for thin aluminum.
-
Heat Input
Controlling heat input is crucial for preventing distortion. The ideal heat input for MIG welding aluminum should range from 1 to 2.5 kJ/cm (2.5 To 6.3 Kj/in).
-
Filler Material Selection
Your choice of filler material affects strength and corrosion resistance. Common filler wires include ER4047 and ER5356, varying based on the aluminum type and application.
Common Issues
Let’s now look at unique issues related to aluminum welding.
-
Porosity in Welds
Porosity in aluminum occurs when gas gets trapped in the weld. Look for tiny holes. Use argon or helium to remove contaminants.
-
Inconsistent Heat Distribution
Aluminum’s conductivity can cause uneven heat. I recommend adjusting your amperage to 150-200 A (Amps) for optimal results.
-
Cracking in Welds
Cracking occurs due to rapid cooling. Inspect for visible cracks. Preheat to 150°C (302°F) to prevent this.
-
Burn-through
Burn-through can occur in aluminum if the material is too thin. Look for holes. Reduce your voltage and consider MIG (Metal Inert Gas) settings.
-
Welding Spatter
Spatter during aluminum welding can create cleanliness issues. Identify excess spatter. Adjust your gas flow rate and use anti-spatter spray.
Aftercare, Inspection, and Advanced Tips for Aluminum Welding
Here’s key advice to keep your aluminum welding projects in top shape.
Aftercare Tips
After welding aluminum, clean the seam with a non-abrasive cleaner designed for aluminum, like EarthSafe Cleaners. Protect finished welds with an anti-corrosion spray, like Rust-Oleum’s Aluminum Protectant. Finally, store your welded pieces in a dry place—moisture can cause oxidation and ruin your work.
Inspection Guidelines
Inspect the weld for porosity (Tiny Holes) using a magnifying tool in sunlight or with a UV light. Check for lack of fusion by performing a hardness test; aim for 50-100 HV (Vickers Scale). I often use ultrasonic thickness gauges to monitor weld integrity more precisely.
Expert Tips
Preheat your aluminum to 200°F (93°C) to prevent cracking and ensure better penetration. Use a spool gun for consistent wire feeding; I find that 4047 alloy wire improves interpass temperature control. Set your transport speed at around 12 inches/min (Approx. 30.5 Cm/min) for optimal feed rate and bead structure.
Key Benefits
The main benefit of using a MIG (Metal Inert Gas) welder for aluminum is its speed. Friends have told me how it worked wonders for their projects, significantly cutting down time.
Moreover, MIG welding offers versatility, ease of use, and produces clean welds. It’s great for both thin and thick aluminum, reduces distortion, and minimizes the need for extensive cleanup afterward.
For those considering advanced alternatives, understanding the investment required for precision equipment can be crucial, especially when exploring how much a laser welder costs.
MIG Welding Aluminum vs. TIG Welding
Many ask, what’s the difference between MIG and TIG welding for aluminum? Both methods have their places, but knowing the advantages of each helps you choose the right technique.
Aspect | MIG Welding | TIG Welding |
---|---|---|
Speed | Faster process, ideal for production runs. | Slower speed, better for detailed work. |
Control | Good control over weld bead. | Excellent control, especially on thin materials. |
Heat Input | More heat input can lead to distortion. | Lower heat input minimizes distortion. |
Simpler Setup | Easy setup; great for beginners. | More complicated; requires practice. |
Finishing Quality | Good, but can require more cleanup. | Superior finish; less post-weld cleanup. |
In most cases, I’d lean towards MIG for speed and convenience. However, if precision and appearance matter, go TIG. Each has pros and cons, so consider what you need for your project.
Applications Across Different Fields
I’ve used MIG welding to fix aluminum bike frames, but it has many applications, such as:
- Aerospace Manufacturing: MIG welding is essential for lightweight aluminum components, enhancing fuel efficiency. Its popularity in this industry stems from quick processing and high strength.
- Automotive Repair: Many car body shops use MIG welding for aluminum parts, especially in collision repairs. It’s favored for speed and consistency in restoring vehicle frames.
- Marine Fabrication: MIG welding is common in boat building and repairs. It’s ideal for aluminum hulls due to its corrosion resistance and watertight seams.
- Architectural Structures: Many architects choose MIG welding for aluminum facades and supports. It enables sleek designs while ensuring structural integrity and durability.
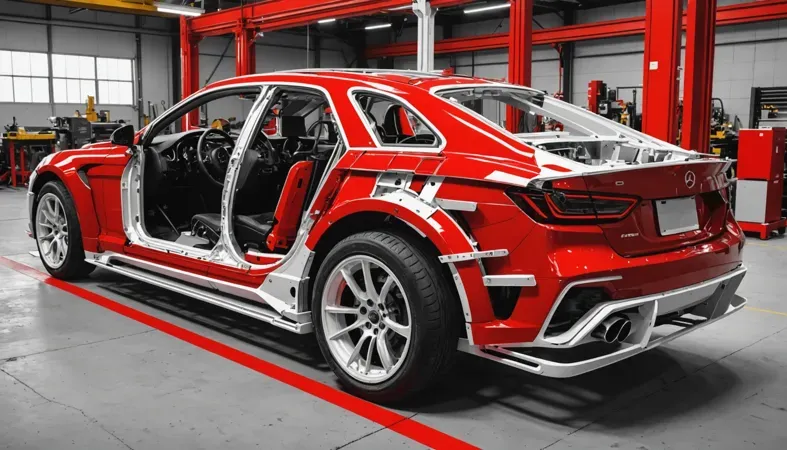
Other Options for Welding Aluminium
When you want alternatives for welding aluminium, consider TIG welding or laser welding. TIG welding, like the Miller Syncrowave 210, offers superior precision and control, making it perfect for delicate aluminium projects. On the other hand, laser welding presents a clean, fast option with minimal heat distortion.
For thicker materials, consider using stick welding with a specialized electrode, like the Lincoln Electric Excalibur. This can handle tough jobs but requires more skill. Each method has its pros and cons, so choose the one that fits your specific project needs.
Frequently Asked Questions (FAQs)
Here are some common questions I typically get asked about welding aluminium.
Can You Use a MIG Welder to Weld Aluminium?
Yes, you can use a MIG welder to weld aluminium. However, it’s crucial to use the right filler wire, typically ER4047 or ER5356, to ensure a strong bond. Using the wrong wire can result in weak welds or even failures.
Will MIG Weld Stick to Aluminum?
Yes, MIG weld will stick to aluminium when using the proper techniques and materials. Clean the aluminium surface thoroughly to remove any oxidation; otherwise, it won’t adhere well. Cleanness is key to achieving a reliable weld.
What MIG Wire Do I Need to Weld Aluminum?
You need ER4047 or ER5356 MIG wire to weld aluminium effectively. ER4047 is ideal for general-purpose welding, while ER5356 is suitable for stronger applications. Choosing the right wire plays a vital role in ensuring good penetration and a strong weld pool.
What Happens if You MIG Weld Aluminum With Steel Wire?
If you MIG weld aluminium with steel wire, the weld won’t hold. The fusion between aluminium and steel wire creates a weak joint that can fail under stress. It’s crucial to use aluminium-specific wires to achieve proper fusion and strength.
Can You Weld Thick Aluminium With a MIG Welder?
Yes, you can weld thick aluminium with a MIG welder, but it requires higher settings and possibly preheating. Typical thickness limits are around 6 mm (0.24 In) for MIG welding. Proper settings help prevent burn-through and ensure good penetration.
Do I Need a Spool Gun for Welding Aluminium?
Yes, a spool gun is highly recommended for welding aluminium. It keeps the wire feed consistent, preventing bird-nesting, which occurs with standard guns due to aluminium’s softness. A spool gun greatly enhances your welding experience and improves the quality of the weld.
What Technique Should I Use for MIG Welding Aluminum?
You should use the push technique for MIG welding aluminium. Pushing the torch directly into the weld pool improves penetration and control. This technique also helps maintain a stable arc and better bead shape compared to pulling the torch.
Is Shielding Gas Necessary for MIG Welding Aluminium?
Yes, shielding gas is essential for MIG welding aluminium. Use 100% argon or an argon-helium mix for optimal results. Shielding gas protects the weld pool from contamination, ensuring a clean, strong weld every time. Understanding how electrical components work in welding setups is crucial, and a fundamental skill includes knowing how to build a bridge rectifier.
Can You Use a TIG Welder for Aluminium?
Yes, you can use a TIG welder for aluminium. In fact, TIG offers greater control for thin materials and is often the preferred choice for intricate welds. While MIG is faster, TIG provides better appearance and quality in your aluminium welds.
Conclusion
We’ve gone through a lot, thank you for sticking it out. We covered many important items, including what aluminum is, types of aluminum and their weldability, prerequisites for welding, steps using a MIG welder, safety tips, MIG welding techniques, factors affecting aluminum weldability, common issues, aftercare, and inspection, as well as the key benefits and applications across various fields. We even touched on other options for welding aluminum and answered popular FAQs.
So, can you weld aluminum with a MIG? Yes, you can, but it requires specific techniques, a suitable MIG welder, and proper settings. In summary, consider factors like the aluminum type, your welder’s capabilities, and safety. Wishing you success in your welding projects with aluminum!
If you’re interested in learning more about welding and expanding your knowledge, be sure to check out what What is Welding has to offer.
Additional Reading
- American Society of Mechanical Engineers. (2019). ASME Section IX: Welding and Brazing Qualifications. New York, NY: ASME.
- International Organization for Standardization. (2017). ISO 3834: Quality Requirements for Fusion Welding of Metallic Materials. Geneva, Switzerland: ISO.
Joe Carter is a retired welding professional with over 40 years of hands-on experience in the industry, spanning ship repair, structural welding, and even underwater projects. Joe is a master of MIG, TIG, and Stick welding. Passionate about mentoring the next generation of welders, Joe now shares his decades of expertise and practical insights to help others build rewarding careers in welding.
Aluminium Alloys, MIG Welding, Safety Tips, Welding, Welding Aluminium, Welding Applications, Welding Equipment, Welding Techniques