What is Nitrogen Gas Used for in Welding? | Applications, Techniques, and Tips
Published on: April 19, 2025 | Last modified: March 4, 2025
By: Tyler James
Nitrogen is a colorless, odorless gas that makes up about 78% of our atmosphere. It’s essential for life, playing a crucial role in many industrial processes.
I’ve received numerous inquiries about what is nitrogen gas used for in welding. Understanding its role is vital; it can enhance weld quality and reduce defects. Personally, I’ve seen projects drastically improve when nitrogen was used to shield the weld area.
In this article, I’ll delve into various topics like how nitrogen gas works in welding, types of nitrogen used, steps for effective use, factors affecting its application, unique issues, aftercare and inspection tips, and alternative gases. Plus, I’ll help answer if you can use nitrogen for MIG or TIG welding, and clarify what compressed nitrogen is used for in welding.
Contents
- What is Nitrogen Gas Used for in Welding?
- How is Nitrogen Gas Used in Welding?
- Types Of Nitrogen Gas Used in Welding
- Steps for Using Nitrogen Gas in Welding
- Factors Affecting the Use Of Nitrogen Gas in Welding
- Unique Issues Related to Nitrogen Gas in Welding
- Aftercare, Inspection, and Advanced Tips for Nitrogen Gas in Welding
- Applications Of Nitrogen Gas in Welding
- Benefits of Using Nitrogen Gas in Welding
- Exploring Alternatives to Nitrogen Gas in Welding
- Frequently Asked Questions (FAQs)
- Conclusion
- References
What is Nitrogen Gas Used for in Welding?
Nitrogen gas protects molten weld pools from oxygen and contamination. It provides a stable environment during welding, ensuring clean, strong joints. Typical applications include MIG and TIG welding, where it enhances weld quality.
How is Nitrogen Gas Used in Welding?
Nitrogen gas plays a critical role in welding, especially in shielding. It’s an inert gas, meaning it won’t chemically react with other elements during the process. This helps maintain weld quality and stability, resulting in a cleaner outcome. In fact, using nitrogen can reduce oxidation rates by up to 90%, which is impressive.
When considering what nitrogen is used for in welding, note that it improves arc stability and offers a cooler weld. This is crucial when working with materials that can warp easily or oxidize.
Using nitrogen for MIG or TIG welding has its advantages. I’ve seen better results in weld penetration and strength, particularly when welding stainless steel. Plus, you won’t have to worry about oxidation issues interfering with your work.
Types Of Nitrogen Gas Used in Welding
-
Liquid Nitrogen
Liquid nitrogen is extremely cold, about -196°C (-321°F). In welding, it cools materials quickly, preventing heat distortion. To use liquid nitrogen, cool the welded area at a controlled rate, then safely dispose of the excess nitrogen gas produced.
-
Gaseous Nitrogen
Gaseous nitrogen is a non-flammable gas commonly found in the atmosphere. It protects the weld area from oxidation during processes like MIG (Metal Inert Gas) and TIG (Tungsten Inert Gas) welding. To use it, maintain a flow of nitrogen around the weld joint to create an inert atmosphere.
A crucial factor in welding is choosing the appropriate welding rod for your specific application, which can significantly affect the quality of the weld. Learn more about the right welding rod to use to ensure optimal results.
-
Nitrogen Mixtures
Nitrogen mixtures combine nitrogen with other gases, often argon or CO2 (Carbon Dioxide). These blends enhance arc stability and improve weld quality. To use a mixture, determine the right ratio for your welding process and set up a gas delivery system accordingly.
Understanding the role of a hot pass in welding is crucial when aiming for optimal weld integrity and strength.
-
High-purity Nitrogen
High-purity nitrogen has minimal impurities, making it ideal for sensitive welding jobs. It ensures a clean weld by reducing contaminants. To apply high-purity nitrogen, use a dedicated cylinder designed to maintain gas quality throughout the welding process.
-
Reinforced Nitrogen
Reinforced nitrogen is specially prepared with added elements to improve performance. It enhances the penetration and strength of welds. To utilize reinforced nitrogen, follow the manufacturer’s guidelines on mixing and application with your welding equipment.
You should now have a good understanding of the different nitrogen gas types used in welding. In the next part, we’ll discuss the steps for using nitrogen gas in welding.
Steps for Using Nitrogen Gas in Welding
Now, we’ll cover the steps for using nitrogen gas in welding. Follow these steps closely for successful results.
-
Prepare the Equipment
First, ensure your welding machine is compatible with nitrogen. MIG and TIG welders work well with this gas, but check the specifications! Proper gas regulators and flow meters are vital. Aim for a gas flow rate of 3 to 10 liters per minute (L/min), depending on the process and application. Knowing the cost of welding rods can also influence your project budgeting and resource allocation, so it’s important to explore the price range of welding rods.
Having the correct fittings is crucial. Mismatched fittings can cause leaks and problems. Test your setup for leaks regularly, as they can significantly impact welding quality.
-
Set the Parameters
Next, set the voltage and wire feed speed on your welder. For MIG, set it to 22-26 volts, adjusting for material thickness. For TIG, ensure your settings match your tungsten and filler rod sizes. Proper setup can help minimize issues such as weld spatter causes.
If you’re using nitrogen instead of argon, adjust the shielding gas mixture. Aim for a blend of 25% nitrogen and 75% argon for MIG. This also helps improve arc stability. The right settings lead to a better bead and less spatter.
-
Introduce Nitrogen Gas
Now, it’s time to introduce nitrogen into your welding process. Gradually open the gas valve while monitoring the flow gauge. You want a steady flow to effectively shield the weld zone. Too much nitrogen can create poor arc characteristics.
If you notice excessive hissing or unstable arcs, adjust your flow. Aim for even gas coverage, which is key to preventing oxidation. Keep hydrogen content in the welding environment low, ideally below 0.005%. This leads to cleaner welds. Proper care for skin is crucial after exposure, so it is important to know what to do for welding burns.
-
Monitor the Welding Process
Keep a close eye on your welding procedure. Watch for changes in bead appearance or inconsistencies in penetration. If the weld looks too bright or a different color, your nitrogen settings might need adjusting. A well-controlled environment outperforms any welding skill.
When welding on a vehicle, knowing the components you need to disconnect is essential for ensuring safety and preventing damage to the electrical systems. For detailed guidance on what to disconnect when welding, consider exploring the topic further.
Sometimes, you can feel the difference in how the torch behaves. If it feels off, don’t hesitate to tweak the parameters on the fly. Being responsive is key—that’s where experienced welders excel. A common issue that welders face is porosity in welding, which requires understanding its causes and solutions to improve welding quality. For more on this topic, explore what causes porosity in welding.
.
We have now covered the steps for using nitrogen gas in welding. Next, we will examine factors affecting its use.
Factors Affecting the Use Of Nitrogen Gas in Welding
What factors influence nitrogen gas applications in your welding projects?
-
Welding Material Type
The material you’re welding significantly affects nitrogen’s role. For example, nitrogen helps prevent oxidation in stainless steel and aluminum alloys during welding.
-
Environmental Conditions
Your welding environment matters. Humidity, temperature, and airborne contaminants can increase oxidation and affect nitrogen’s effectiveness.
-
Gas Purity Levels
The purity of nitrogen gas is crucial. Low purity levels can introduce impurities, leading to defects in the weld joint. Ideally, use nitrogen with a purity of 99.99% for optimal results.
-
Welding Technique
Your technique also plays a significant role. Nitrogen can effectively enhance arc stability and improve weld quality in MIG and TIG welding.
-
Cost Considerations
Cost can limit your choice of nitrogen gas. While nitrogen is generally affordable, higher grades may be pricier but yield superior weld quality.
We’ve wrapped up the factors influencing nitrogen gas use in welding. Next up, we’ll look at unique challenges associated with it.
Unique Issues Related to Nitrogen Gas in Welding
Let’s explore unique technical problems you may face with nitrogen in welding.
-
Oxidation Risks
Nitrogen can promote oxidation under certain conditions. Look for discoloration to identify oxidation. Adjust the shielding gas blend to reduce this risk.
-
Gas Contamination
Nitrogen can get contaminated with moisture. Check for condensation in your system and use proper filtration to prevent it.
-
Cost Variability
Nitrogen costs may fluctuate, affecting your budget. Track current prices from suppliers. Planning your purchases helps manage expenses.
-
Pressure Regulation Challenges
Nitrogen requires precise pressure settings. A fluctuating pressure gauge may indicate problems. Use a reliable regulator to maintain stable pressure.
-
Improper Gas Mixtures
Incorrect nitrogen mixtures can lead to poor welds. Check the gas composition with a gas analyzer and adjust as necessary for optimal results.
We have now covered unique challenges with nitrogen gas in welding. Next, we will examine aftercare, inspection, and advanced tips.
Aftercare, Inspection, and Advanced Tips for Nitrogen Gas in Welding
Here’s practical advice on aftercare, inspection, and advanced tips for using nitrogen gas in welding.
Aftercare Tips
After using nitrogen gas for purging, first exhaust any remaining gas from the welding chamber. Monitor nitrogen levels with a calibrated gauge; aim for less than 1% oxygen for optimal results. Finally, clean your equipment thoroughly with a solvent like acetone (C3H6O) to prevent contamination in future jobs.
Inspection Items
Inspection should include checking nitrogen purging equipment for leaks or pressure drops; use a manometer (Pressure Measuring Tool) for accurate readings. Ensure connectors are sealed with products like Loctite (Industrial Adhesive). Make it a habit to check all hose fittings regularly to prevent nitrogen loss and ensure consistent performance.
Expert Tips
If you’re experienced, use high-precision regulators to minimize flow fluctuations. Set nitrogen pressure between 6 and 10 psi (Pounds Per Square Inch) for stable gas feed during welding. Consider adding a digital dynamometer for precise performance tuning, keeping defect rates under 1% on weld joints. It’s crucial to be aware of how dangerous welding is as this knowledge can impact safety measures and operational protocols.
.
Applications Of Nitrogen Gas in Welding
I’ve seen people use nitrogen gas for various welding tasks. It has several unique applications, such as:
- Controlling Shielding Gas: Nitrogen is often mixed with argon for TIG (Tungsten Inert Gas) welding. It prevents oxidation and ensures a cleaner weld. This mix is common in stainless steel welding.
- Purging: Welders use nitrogen to purge pipes before welding. It replaces oxygen inside, reducing contamination. This application is prevalent in the oil and gas industry.
- Filler Metal Protection: Nitrogen shields filler metals from moisture and oxidation. This method is essential for high-quality aluminum welding, ensuring excellent results.
- Reducing Hardness in Welds: Adding nitrogen during welding creates softer seams and helps avoid cracks in high-strength steel applications.
Benefits of Using Nitrogen Gas in Welding
Nitrogen gas isn’t just helpful; it offers several notable advantages in welding applications. Here’s what you should know:
Benefit | Description | Impact on Welding |
---|---|---|
Reduced Oxidation | Nitrogen creates an inert atmosphere that minimizes oxidation during welding processes. | Leads to cleaner, stronger welds and better overall quality. |
Improved Weld Consistency | Providing a stable shielding environment helps maintain consistent arc characteristics. | Results in uniform bead appearance and penetration. |
Cost-Effectiveness | Nitrogen is often less expensive compared to other shielding gases like argon and helium. | Reduces operational costs while still enhancing weld quality. |
Versatility | Nitrogen can be effectively used with various welding processes like MIG and TIG. | Broadens the range of applications for welders. |
Control of Heat Affected Zone (HAZ) | Using nitrogen can help cool the molten metal more effectively. | Reduces the size of the heat affected zone, minimizing warping and distortion. |
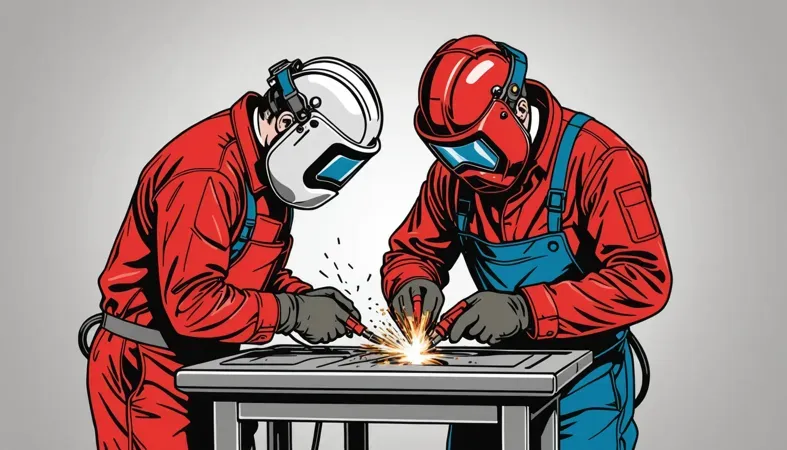
Exploring Alternatives to Nitrogen Gas in Welding
For tasks similar to those tackled by nitrogen gas, you might consider using argon or carbon dioxide. Argon, for example, is great for TIG welding aluminum because it provides a clean shielding atmosphere and saves costs. Carbon dioxide is often preferred in MIG welding for its availability and effectiveness when dealing with steel, making it a smart choice in certain scenarios.
Having navigated similar challenges before, I’ve found that helium can also play a role, especially in stainless steel applications. It increases heat input and improves penetration, which can be beneficial. So, depending on your project requirements, you have several options that can work just as well as nitrogen.
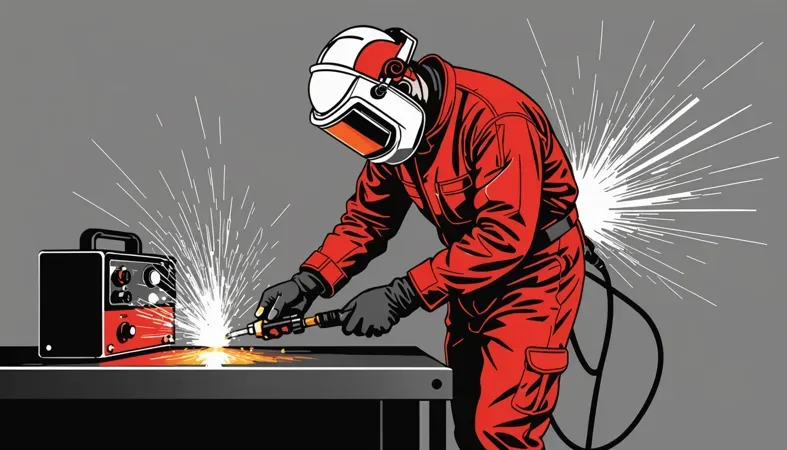
Frequently Asked Questions (FAQs)
Here are some unique questions I typically get asked about nitrogen in welding.
Can I Use Nitrogen for MIG Welding?
Yes, you can use nitrogen for MIG welding. Using nitrogen stabilizes the arc and reduces oxidation, especially in aluminum and reactive metals. Nitrogen applications in welding can boost the quality of the weld by preventing contamination.
Can Nitrogen Be Used for TIG Welding?
Yes, nitrogen can be used for TIG welding. In certain applications, it acts to protect the weld pool from atmospheric contamination. It’s ideal for specific alloys, maintaining weld integrity when argon is insufficient.
Can I Use Nitrogen Instead Of Argon for TIG Welding?
No, you shouldn’t use nitrogen instead of argon for TIG welding. Argon provides the necessary inert shielding environment needed for most metals like stainless steel. Nitrogen might disrupt the arc control and affect the quality of the weld.
Why is Nitrogen Not Commonly Used in Welding?
Nitrogen isn’t commonly used in welding primarily due to its reactive nature. It can lead to embrittlement in certain materials. Most welding processes rely on inert gases like argon to avoid complications and ensure strong welds.
What is Compressed Nitrogen Used for in Welding?
Compressed nitrogen is often used in welding to purge systems and prevent oxidation. In processes like tungsten inert gas (TIG) welding, it helps keep the atmosphere clean for the weld. This is crucial for maintaining high weld quality.
Conclusion
We’ve gone through a lot, thank you for sticking it out. We covered what nitrogen gas is used for in welding, how it’s used, different types, essential steps for usage, factors affecting its application, unique issues, aftercare, and applications. We also looked at alternatives to nitrogen gas, plus some frequently asked questions.
Hopefully, I was able to impart some of my experience regarding what nitrogen gas is used for in welding. In summary, nitrogen serves key roles like preventing oxidation, enhancing metal strength, and improving weld quality. These aspects are critical, especially when you consider using nitrogen for TIG or MIG welding effectively.
For more insights and resources, visit What is Welding, where we are dedicated to providing you with the latest technical expertise.
References
- Lincoln Electric. (2020). The Procedure Handbook of Arc Welding (15th ed.). Cleveland, OH: Lincoln Electric Company.
- American Welding Society. (2020). AWS C5.6: Recommended Practices for Gas Metal Arc Welding. Miami, FL: AWS.
- Parmar, R. S. (1997). Welding Engineering and Technology. New Delhi, India: Khanna Publishers.
Tyler is a passionate DIY welder and self-taught metal artist with years of hands-on experience transforming raw materials into functional and artistic creations. Specializing in MIG welding, Tyler crafts everything from custom furniture to outdoor sculptures, blending creativity with technical skill. Committed to making welding accessible, Tyler shares practical insights and project inspiration to help beginners and hobbyists confidently explore the world of metalworking.
American Welding Society, Filler Metal, MIG Welding, Nitrogen Gas, Shielding Gas, TIG Welding, Weld Quality, Welding, Welding Applications