What is a Root Pass in Welding? – Definition, Purpose, and Types
Published on: January 22, 2025 | Last modified: March 4, 2025
By: Joe Carter
A root pass is the first layer of weld metal applied to the joint between two pieces of material. It’s critical for ensuring a strong bond right from the start.
I often used to be asked, what is a root pass in welding? It’s essential because it sets the foundation for the entire weld. From my experience, a good root pass can make or break the integrity of your project.
In this article, we’ll explore how a root pass works, the different types, steps to perform it, factors that affect its quality, unique issues encountered, aftercare and inspection tips, typical applications, and even alternatives to root pass welding. By the end, you’ll understand not just the process, but also what the purpose of a root pass in welding really is.
Contents
- What is a Root Pass in Welding?
- How Does a Root Pass in Welding Work?
- Types Of Root Passes in Welding
- Steps to Perform a Root Pass
- Factors Affecting Root Pass Quality
- Understanding Root Pass Techniques
- Unique Issues in Root Pass Welding
- Aftercare, Inspection, and Advanced Tips for Root Pass Welding
- Typical Applications Of Root Pass Welding
- Exploring Alternatives to Root Pass Welding
- Frequently Asked Questions (FAQs)
- Conclusion
- Additional Reading
What is a Root Pass in Welding?
A root pass is the first layer of weld deposited in a joint. It helps to establish a solid foundation, ensuring proper penetration and fusion. You typically find root passes in pipe welding and thick materials, making them crucial for strength.
How Does a Root Pass in Welding Work?
A root pass in welding is the first layer of weld metal deposited in a joint. It establishes a solid foundation that bonds the workpieces together. In a groove weld, this initial weld usually penetrates to the root of the joint. Using techniques like Shielded Metal Arc Welding (SMAW), the root pass typically requires a depth of at least 1/8 inch (3.2 Mm) to ensure proper fusion.
This foundational layer is crucial for sound weld integrity. A well-executed root pass reduces the chance of defects, improving strength and durability. It ensures a minimal root gap, ideally about 1/16 inch (1.6 Mm), promoting effective penetration.
From my experience, the first time I laid down a root pass felt nerve-wracking, but I quickly learned its importance. A good root pass determines the overall quality of the weld. Without it, you risk issues like lack of fusion or blowholes.
Types Of Root Passes in Welding
What are the types of root passes?
-
Single Pass Root Welds
Single pass root welds use one continuous run. This technique shows how a root weld connects two materials in one sweep. To perform this type, set your welder to the correct voltage and speed for a neat execution. For an overview of the components of a GMA welding system, it’s crucial to understand how each part contributes to the overall welding process.
-
Multi-pass Root Welds
This approach uses several passes to build depth and strength. Essentially, it’s a series of weld overlays on the initial root. To execute, make the initial pass, then allow it to cool before adding more layers for added strength.
-
Fillet Root Passes
Fillet root passes create a triangular weld joint at the corner of two intersecting pieces. This connects them reliably. Aim to create an even bead that flows into both surfaces, ensuring the joint is fully fused. Proper setup of welding equipment is crucial and you can explore techniques to set up a Lincoln Electric welder here.
-
Sole Root Passes
Sole root passes involve a single, focused welding line along the material edge. It indicates the primary connection point between metals. Maintain a steady hand, keeping the arc length consistent to avoid gaps or burn-through.
-
Backhand Root Passes
Backhand root passes use a backward welding technique for better control. This method focuses heat toward the root, making it ideal for thicker materials. Tilt your electrode and pull it back along the seam to ensure a strong fusion at the base.
We have now covered the various types of root passes in welding. Next, we will examine the steps to perform a root pass.
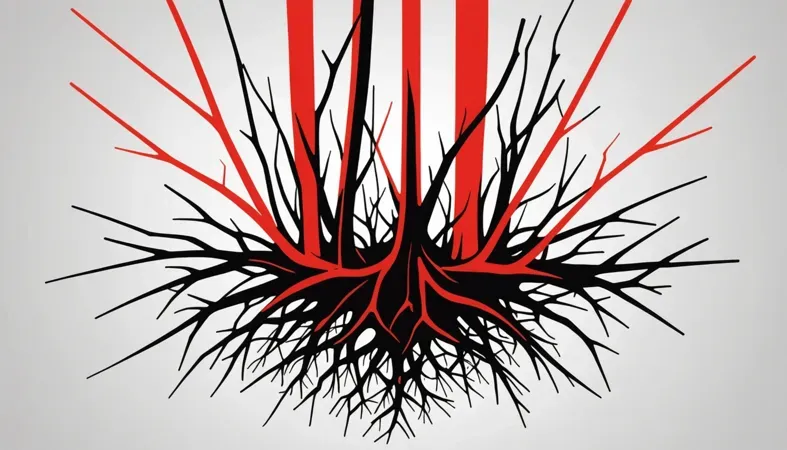
Steps to Perform a Root Pass
Now, we’ll cover the essential steps for executing a root pass in welding. Follow closely to master this crucial aspect of a weld!
-
Prepare the Joint
First, clean the joint between the two pieces of metal. Remove any rust, oil, or paint to ensure the weld sticks well. Use a wire brush or grinder; that’ll do the trick. Verify that the joint fits tightly—aim for a 0.5 mm (0.02 Inch) root gap to ensure proper penetration. Selecting the right shielding gas greatly affects weld quality and performance, offering protection and stability during the welding process. To explore more about what gas is used for welding, read further.
.
Next, set the bevel correctly. A 50-degree angle often works for two pieces of steel. Proper fit-up improves the architecture of your weld. Take your time here; this step is foundational for a high-quality weld.
Improving your technique with accurate joints may also include learning how to weld 45-degree angles.
-
Select the Filler Material
Choose the right filler material for your base metals. For low carbon steel, 7018 rods are usually suitable. For heavier sections, opt for a filler with higher strength. Always check the specifications of your base metals to ensure a match; you want the alloy to blend seamlessly.
The diameter of your filler matters! A 3.2 mm (1/8 Inch) diameter filler typically provides excellent control. Ensure compatibility with the welding process—MIG, TIG, or SMAW all require specific fillers. Don’t rush this decision; it can make or break your weld. Knowing how to decipher weld symbols is crucial in aligning your filler choice with the project requirements, and this knowledge can be expanded upon in the article on reading weld symbols.
-
Adjust the Welding Parameters
Next, fine-tune the welding parameters. Set your current to about 70-130 Amps based on the rod diameter and material thickness—thicker materials need more heat. Voltage should be around 20-30 volts to maintain a steady arc. For further details on optimizing your settings, be ready to make small adjustments during your weld for optimal performance.
Understanding welding current types is crucial as they significantly impact the quality of the weld, especially in context of what DCEP means in welding.
Never underestimate the importance of gas flow if you’re TIG welding. Set Argon to 15-20 CFH (Cubic Feet Per Hour) for effective shielding. Watch your travel speed; a steady, moderate pace delivers better consistency in the weld bead. Experiment to find what works best for you.
-
Execute the Root Pass
It’s time to lay down that root pass! Maintain a consistent arc length—about 3 mm (1/8 Inch) makes a big difference. Approach the joint at a 10-degree angle so the molten metal runs into the gap. Move at a slow, steady speed to ensure full penetration; rushing risks defects.
Be mindful of your bead shape. It should have a slight crown, not be flat; this enhances strength and keeps your joint secure. Ideally, you’ll fill that initial groove with a smooth, even layer of weld metal. Keep an eye on your filler usage; too little can lead to undercutting.
Choosing the appropriate current for your welding task can significantly affect the quality of the weld. If you’re curious about the specific amps needed for a 3/32 rod, it’s pivotal to ensure optimal performance and avoid common welding pitfalls.
That covers the steps to execute a root pass. Let’s now take a look at the factors influencing root pass quality.
Factors Affecting Root Pass Quality
What factors affect the quality of a root pass in welding?
-
Welding Speed
Welding speed affects penetration and heat distribution. For example, too fast a speed can lead to lack of fusion, while too slow may cause excessive heat, weakening the weld.
-
Heat Input
Heat input is crucial for proper fusion. Measured in joules per millimeter (J/mm), the ideal range varies by material; for steel, aim for 1.5 to 2.5 J/mm to maintain bead integrity.
-
Joint Preparation
Joint preparation is key. A well-prepped joint minimizes impurities and maintains a consistent root gap. If the root gap is too wide, it can create weak spots in the weld.
-
Filler Material Selection
The right filler material enhances weld strength. For instance, using E7018 for low-alloy steel provides excellent tensile strength, crucial for structural applications.
-
Welder Skill Level
A skilled welder has better control over heat and speed. Research shows that experienced welders achieve root pass defect rates 30% lower than novices.
That covers the elements influencing root pass quality. Let’s now take a look at techniques for achieving a successful root pass.
Understanding Root Pass Techniques
In addition to defining a root pass, it’s essential to grasp the techniques that can optimize this critical phase of welding.
Technique | Description | Benefits | Ideal Application |
---|---|---|---|
Weaving | A side-to-side motion creates a wider bead. | Enhanced penetration and bead control. | Used on wider joints. |
Stringer Beads | A linear movement deposits a narrow, continuous bead. | Better control and less undercut. | Thinner materials and critical joints. |
Circular Motion | A circular or spiral motion helps distribute heat evenly. | Prevents overheating and distortion. | Curved joints or when aiming for a smooth surface. |
Multi-Pass Technique | Applying multiple layers builds up the weld. | Increases joint strength significantly. | Heavy gauges or critical structural applications. |
Push vs Pull Technique | Push involves moving the gun away from the weld pool, while pulling brings it towards the pool. | Each method affects penetration and bead shape differently. | Controlled environments, depending on joint design. |
We’ve wrapped up root pass techniques and their significance here. Next up, we’ll look at unique challenges in root pass welding.
Unique Issues in Root Pass Welding
Let’s look at problems unique to the root pass in welding.
-
Incomplete Fusion
Incomplete fusion occurs when the weld metal doesn’t fully bond with the base metal. Look for signs like uneven edges. Adjust heat settings between 140-180 amps and ensure proper travel speed to troubleshoot.
-
Porosity Issues
Porosity means tiny gas pockets in the weld. Look for round holes on the weld’s surface. Increase shielding gas flow and clean surfaces before welding to resolve the issue.
-
Excessive Spatter
Excessive spatter can mar the weld’s appearance. Check your settings; too high voltage leads to spatter. Adjust the voltage to 16-20 volts and maintain a steady hand.
-
Cracking in Root Pass
Cracking can occur in the root pass. Quality inspection should reveal any fissures during cooling. Control heating and cooling rates, and avoid rapid temperature drops to mitigate this.
-
Root Penetration Inconsistency
Inconsistent root penetration can weaken the weld line. Watch the bead width; ideally, it should be around 3-5 mm. Increase travel speed or adjust the electrode angle to ensure full root penetration.
Aftercare, Inspection, and Advanced Tips for Root Pass Welding
Here’s crucial advice that’ll help ensure your root pass is sound and effective.
Aftercare Tips
After welding, clean the root area with a wire brush or grinder. Remove any slag or debris to prevent weaknesses in the weld. Maintain the joint at about 15°C (59°F) for 24 hours to avoid crack formation. Choosing the correct wire size for your welder is crucial for a strong and stable weld and can be better understood by exploring what size wire for a welder.
Inspection
Inspection starts with verifying the root gap, which should be around 1.6 mm (1/16 Inch) for optimal penetration. Use a magnet-based gauge, like the Miller M-18, to measure the bead size accurately every quarter inch of the weld. I recommend recording these measurements for repeat jobs. Understanding the intricacies of welding techniques can enhance your knowledge of different arc welding types.
Expert Tips
If you’re experienced, adjust your arc length between 2.5-3.5 mm (0.1-0.14 Inches) to control heat input. Clean the joint immediately before starting; oils can weaken your weld. Maintain a current of 40-60 amps for thick materials to ensure proper fusion in the root pass. Explore the techniques of welding an edge joint to refine your skills further.
Typical Applications Of Root Pass Welding
People use root passes in pipe welding to create strong joints. However, they have many other applications, such as:
- Piping Systems: Commonly used in oil and gas pipelines, the root pass ensures initial fusion and aligns the pipes for a solid foundation. Its integrity is crucial for safety, which is why it’s popular in the industry.
- Structural Steel Fabrication: In large steel beams, the root pass minimizes gaps, improving overall strength. It’s essential in construction, as safety depends on robust joints.
- Pressure Vessels: In heavy-duty applications, the root pass forms the backbone of welded joints that must withstand high-pressure conditions, making it essential for durability.
- Automotive Manufacturing: Used in frames and chassis, it strengthens weld integrity in vehicles. It’s key for safety and performance, ensuring longevity under stress.
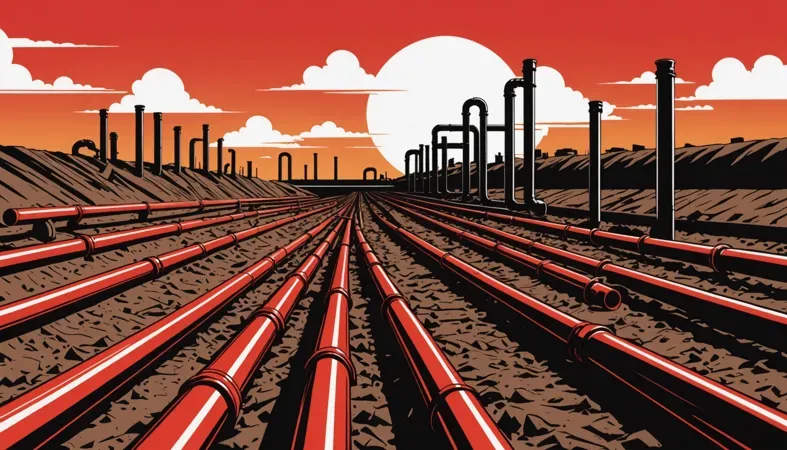
Exploring Alternatives to Root Pass Welding
There are several options to achieve similar results as a root pass. For instance, processes like flux-cored arc welding (FCAW) can sometimes replace root passes due to their fast travel speeds and good penetration. From what I’ve encountered personally, products such as E71T-11 flux-cored wires are handy when working on thinner materials or larger gaps that may not need a conventional root pass.
Another alternative is using gas tungsten arc welding (GTAW). This method excels in precision and control, making it a great choice for critical joints. For specific materials, I often see professionals reach for ER70S-2 filler rods to provide strong root integrity, especially when the base metals are more challenging to weld.
Frequently Asked Questions (FAQs)
Now let us look at some common welding questions I typically get asked.
What is the Purpose Of a Root Pass?
The purpose of a root pass is to create a strong foundation in a weld joint. This initial weld ensures proper fusion and alignment of materials, crucial for strength. A solid root pass reduces the chances of defects and contributes to achieving weld integrity, crucial in structural applications.
Where Should the Root Pass Be Started?
The root pass should be started at the bottom of the joint being welded. This starting point helps control heat and allows for better penetration into the base materials. By starting at the bottom, it also aids in eliminating slag and impurities from the joint area.
How Do You Clean a Root Pass in Welding?
To clean a root pass in welding, use a wire brush or grinder. This helps remove slag and contaminants that can weaken the weld. Ensuring a clean surface is vital, as any impurities can lead to defects during or after the welding process.
Why is 6010 Used for Root Pass?
6010 is used for a root pass due to its deep penetration capabilities. It provides a strong arc and helps ensure good fusion between the weld and base materials. This electrode is particularly effective for thicker materials and improves overall weld strength.
What is Root Gap in Welding?
Root gap in welding refers to the space between the edges of the materials being joined. The ideal root gap is typically between 1.5 mm (0.059 In) and 3 mm (0.118 In), depending on the materials and thickness. A proper root gap allows for better penetration and improves weld quality.
What is a Root Face in Welding?
A root face in welding is the flat surface at the edge of a joint where the root pass is applied. It’s vital for achieving proper weld pool geometry and ensuring good metal fusion. Maintaining a consistent root face leads to improved structural integrity in the final weld.
Conclusion
I hope this was worth your while. We covered topics like what is a root pass in welding, types of root passes, the steps to perform a root pass, factors that affect root pass quality, and unique issues in root pass welding. We also discussed aftercare and inspection, typical applications, and alternatives to root pass welding.
So, what is a root pass in welding? Simply put, it’s the first layer of weld that fuses the base metals together tightly. It’s crucial for ensuring the strength of the entire weld structure. Remember, don’t hesitate to get in touch for further assistance regarding the root pass or any related welding details.
For a deeper understanding and additional insights on welding topics, feel free to visit What is Welding.
Additional Reading
- American Society of Mechanical Engineers. (2019). ASME Section IX: Welding and Brazing Qualifications. New York, NY: ASME.
- American Welding Society. (2021). AWS B2.1: Standard for Welding Procedure and Performance Qualification. Miami, FL: AWS.
- Welding Institute (TWI): https://www.twi-global.com
Joe Carter is a retired welding professional with over 40 years of hands-on experience in the industry, spanning ship repair, structural welding, and even underwater projects. Joe is a master of MIG, TIG, and Stick welding. Passionate about mentoring the next generation of welders, Joe now shares his decades of expertise and practical insights to help others build rewarding careers in welding.
American Welding Society, Pipe Welding, Root Pass, Weld Integrity, Welding, Welding Applications, Welding Equipment, Welding Inspection, Welding Techniques