What is a Plug Weld? Understanding Its Process, Types, Steps, and Applications
Published on: March 5, 2025 | Last modified: March 4, 2025
By: Joe Carter
It’s a question I’m often asked: what is a plug weld? Understanding what a plug weld is crucial for anyone in welding. From my experience, it ensures strong joins and helps avoid weaknesses in metal works.
In this guide, we’ll explore the ins and outs of plug welds including how they work, the different types, precise steps for creating a plug weld, factors that influence them, common issues, aftercare tips, their typical uses, and alternatives to achieve similar results. We’ll also touch on related topics like how is a plate prepared for a plug weld and what dimensions can be given for a plug weld.
Contents
- What’s a Plug Weld?
- How Does a Plug Weld Work?
- Types Of Plug Welds
- Steps for Creating a Plug Weld
- Factors Influencing Plug Welds
- Understanding Plug Weld Design Considerations
- What Could Go Wrong: Common Issues
- Aftercare, Inspection, and Advanced Tips for Plug Welds
- Typical Applications Of Plug Welds
- Alternatives for Achieving Similar Results As A Plug Weld
- Frequently Asked Questions (FAQs)
- Conclusion
- References
What’s a Plug Weld?
A plug weld joins two pieces by filling a hole in one with molten metal. It offers strong, reliable connections in fabrication, like joining sheets or reinforcing joints. You’ll often see it in automotive, bridge, and structural projects.
How Does a Plug Weld Work?
A plug weld is a type of weld that joins two pieces of metal. It involves drilling a hole in the top piece and welding the bottom piece through this opening. The hole’s diameter typically ranges from 6.35 mm (1/4 Inch) to 25.4 mm (1 Inch), depending on the thickness of the materials. Plug welds create strong joints by melting the filler metal and base metal at high temperatures, making the weld area durable.
Plug welding requires proper preparation of the plates to ensure a solid bond. The surfaces must be clean and free from contaminants like rust or oil. This step significantly affects the strength and quality of the weld.
Pay careful attention to the proper dimensions for a plug weld—if the hole is too big or too small, it can compromise strength. The plug’s diameter should be about 1.5 times the thickness of the thinner plate. Understanding effective plug welding boosts joint integrity in various projects.
Types Of Plug Welds
So, what are the types of plug welds?
-
Full Plug Welds
A full plug weld fills the entire drilled hole, providing a strong bond between two workpieces. To perform this, drill the hole and ensure the filler material fills it completely during welding.
-
Partial Plug Welds
A partial plug weld only fills part of the hole. It’s weaker but can be useful. To make one, drill the hole and control how much filler metal you add, leaving some space inside.
-
Seam Plug Welds
Seam plug welds join metal sheets along seams. They create a series of connected joints for added strength. To achieve this, drill holes along the seam, then weld each hole to secure the sheets together.
-
Fillet Plug Welds
Fillet plug welds connect metals at intersections. They’re done at corners and edges where strength is needed. To make this weld, place filler between the joined areas and heat it to bond the joint. It is crucial to use protective gear when welding, as overlooking this can expose you to serious risks; learn about welding without a mask.
-
Offset Plug Welds
Offset plug welds compensate for misalignment in components. They stabilize connections where parts don’t line up perfectly. To execute, drill holes aligned offset from true alignment, and fill with weld metal to reinforce the assembly.
We have now covered the various types of plug welds. Next, we will examine the steps for creating a plug weld.
Steps for Creating a Plug Weld
Here are the essential steps for creating a plug weld.
-
Prepare the Base Plate
First, clean the area of the base plate where you’ll create the plug weld. Use a wire brush or grinder to remove rust, dirt, or contaminants. Ensure the hole diameter is accurate, typically 6 mm to 12 mm (0.24 In to 0.47 In). An improperly sized hole can lead to weak welds.
Next, align the metal pieces so they fit snugly around the hole. Use a caliper to check this. Most plug welds require precise contact to prevent air gaps during welding. Double-check dimensions and fit before proceeding. Understanding the operation of an IGBT inverter welding machine can enhance the efficiency of these welding tasks.
.
-
Set Up Properly for Welding
Before powering your equipment, ensure you’re using the right settings for plug welding. Set your MIG welding machine to 18-22 volts and your wire feed speed to 5-7 m/min (16-23 Ft/min) for optimal penetration and fill. Adjust these parameters based on the material thickness.
Choose the right filler material; ER70S-6 is excellent for carbon steel. If you’re welding different materials, like stainless steel, switch your filler accordingly. Proper settings enhance joint strength.
-
Position the Workpieces Correctly
Align the workpieces over the prepared hole. They should rest flat for a solid foundation. Use clamps to hold them in place to prevent movement during welding, ensuring a steady arc and uniform bead. Pay attention to the clearance between the rod and the base plate; keep it as small as possible, around 1 to 2 mm (0.04 In to 0.08 In). This minimizes distortions and improves penetration. Understanding how a 220 welder converts to 110 can further enhance your welding technique.
.
-
Perform the Plug Welding
Now it’s time to start welding! Place the welding gun over the hole and feed the filler into it. Keep the gun at a 90-degree angle for uniform coverage. Use a sweeping motion to build up the weld against the hole edges while maintaining a consistent speed to prevent uneven surfaces. Avoid small pops or irregular sparks; they indicate poor arc stability. If you notice this happening, double-check your settings. I’ve missed this step before and ended up with bad connections, so stay focused and adjust as necessary for an even weld pool.
During welding, it’s vital to be aware of potential hazards such as weld flash risks which can cause eye damage if proper protection isn’t worn.
-
Finish the Weld
After achieving a good weld, allow it to cool naturally. Fast cooling can cause cracking or warping. Once it’s cool, grind away any excess bead for a cleaner finish using a flap disc or angle grinder.
Lastly, inspect the finished weld carefully. Look for smooth transitions and uniform color. An uneven surface may indicate inconsistencies in your weld. Taking time here can save significant effort later.
We have now covered the process of creating plug welds. Next, we will examine the factors that affect them.
Factors Influencing Plug Welds
What factors affect the creation of effective plug welds?
-
Material Thickness
Material thickness dictates the plug weld’s penetration depth. Thicker materials often require deeper welds, reaching up to 10 mm (0.4 In) or more to ensure a strong bond.
-
Welding Technique
The welding technique used significantly affects weld quality. Techniques like MIG (Metal Inert Gas) or TIG (Tungsten Inert Gas) produce different heat inputs, altering fusion quality and strength. Understanding the various welding processes is essential for achieving optimal results in any project.
Choosing the appropriate wire size plays a critical role in achieving the desired weld strength and quality; it’s essential to know what size wire for a welder best suits your needs.
-
Heat Input
Monitoring heat input is essential. Excessive heat can warp the material, while too little can result in an undersized weld. Aim for 1-2 kJ/mm for mild steel.
-
Electrode Type
The electrode type directly impacts the weld’s mechanical properties. For instance, ER70S-6 electrodes work well for mild steel plug welds, enhancing ductility (Flexibility) and toughness (Strength).
-
Base Material Preparation
Surface preparation is crucial; contaminants can weaken the weld. Clean the surfaces thoroughly, as a blasted or ground finish significantly boosts weld integrity.
We’ve wrapped up the factors affecting plug welds here. Next up, we’ll look at considerations for designing plug welds.
Understanding Plug Weld Design Considerations
Plug welds aren’t just about joining metals; design plays a crucial role in their effectiveness. Here’s what you need to know about factors that impact plug weld design.
Key Factors in Plug Weld Design
Factor | Description | Considerations |
---|---|---|
Diameter of Hole | The hole size impacts heat distribution and weld penetration. | Should be 1.5 times the thinner plate thickness. |
Material Type | Different materials require specific filler metals for strength. | Mild steel works best with ER70S-6; stainless steel needs different fillers. |
Weld Depth | Depth must match the thickness of the material for a strong bond. | Typically matches the plate thickness, often 6-12 mm (0.24-0.47 in). |
Joint Design | Overlapping joints reduce stress concentrations on the weld. | Design joints to allow some movement to mitigate stress risers. |
Heat Input Management | Control heat input to avoid warping and overstressing the base material. | Optimal heat input is around 1-2 kJ/mm for mild steel. |
We have now covered plug weld design considerations. Next, we will examine common issues that could arise.
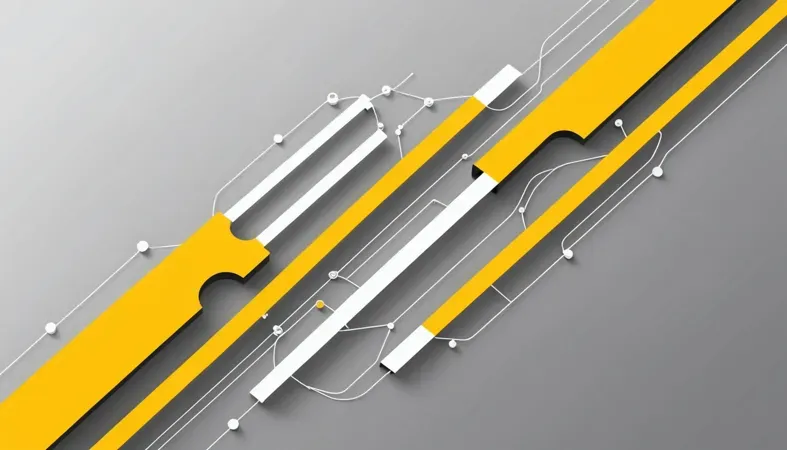
What Could Go Wrong: Common Issues
Let’s look at the unique problems that can arise with plug welds.
-
Porous Welds
Porosity in plug welds appears as small holes. Use the correct shielding gas to resolve this.
-
Inadequate Fusion
Check for gaps in the plug weld seam. Heat settings might be incorrect. Adjust the amperage between 90-130 A for better fusion.
-
Overheating
Plug welds can overheat, leading to discoloration. Look for blue or purple hues. Reduce heat input to fix this.
-
Weld Cracking
Weld cracking can occur in plug welds. Look for visible cracks after cooling. Preheat the plate before welding to prevent this.
-
Insufficient Penetration
Insufficient penetration in plug welds results in a weak bond. Assess joint fusion to identify this. Use the proper technique to ensure full fill.
Aftercare, Inspection, and Advanced Tips for Plug Welds
Here’s essential guidance on keeping your plug welds in top shape through aftercare, inspection, and expert tips.
Aftercare Tips
After installing plug welds, clean any slag or debris. Use a wire brush rated for steel or stainless steel to prevent rust. Make sure your joints cool to at least room temperature (20°C/68°F) before applying protective coatings.
Inspection
Inspect weld penetration with a magnetic particle test (MT) for flaws. Ensure plugs have proper fill; a typical depth is 6 mm (0.24 In), depending on the base metal thickness. Use a visual inspection gauge like the 90070 Caliper for precise measurement.
Expert Tips
If this isn’t your first time plug welding, pay attention to heat settings; optimal amperage is usually between 120-180 A for 3 mm (0.12 In) metal. Consider using a backing bar for even heat distribution. Adjust travel speed between 100-200 mm/min (4-8 In/min) to control bead appearance and joint strength effectively.
Typical Applications Of Plug Welds
I’ve seen plug welds used in various settings, but they excel in applications such as:
- Automotive Manufacturing: Plug welds join sheet metal components, like floor pans and reinforcement strips. They’re strong and resistant to vibration, which is crucial for vehicle safety.
- Construction of Pressure Vessels: Used to attach nozzles or plates, plug welds withstand high-stress environments. They’re popular for resisting leaks under pressure.
- Heavy Equipment Assembly: In excavators or cranes, plug welds provide structural integrity while minimizing weight. That’s a win for equipment performance!
- Aerospace Components: Plug welds bond aluminum or titanium parts, important for weight reduction in aircraft design. Their reliability in flight applications is invaluable.
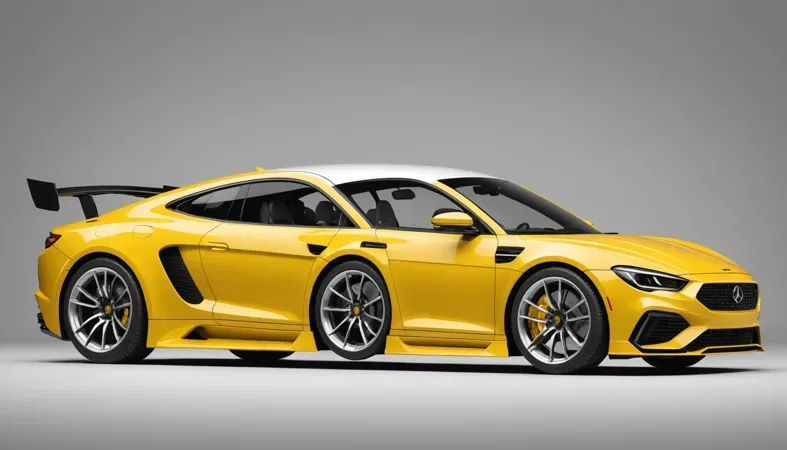
Alternatives for Achieving Similar Results As A Plug Weld
There are several effective methods to achieve results akin to plug welding, such as spot welding and seam welding. These techniques might be preferred in situations where speed is crucial or when working with thin materials. One thing I’ve come to realize is that when you need a solid joint but want less heat input, laser welding, such as with a Trumpf TruLaser, can provide a great alternative too.
Also, using adhesive bonding can work wonders for specific applications, especially where thermal distortion needs to be minimized. A product like 3M’s Scotch-Weld can create strong connections without risking the heat damage typical of welding processes. Depending on your project’s demands, considering these alternatives might save you time and enhance joint performance.
Frequently Asked Questions (FAQs)
Now let’s look at some common questions I typically get asked about plug welding.
Is a Plug Weld As Strong As a Spot Weld?
Yes, a plug weld is as strong as a spot weld when done correctly. A plug weld has a similar shear strength, often around 70% to 90% of the base metal strength. This makes it reliable for joining overlapping materials without compromising integrity.
What is Another Name for Plug Weld?
Another name for a plug weld is a “puddle weld.” Both terms describe the process of welding through a hole to join two sheets together. Puddle welds achieve strong connections, often used for repairs and in auto bodywork.
What is the Difference Between Plug Weld and Puddle Weld?
The difference between a plug weld and a puddle weld lies in their applications. A plug weld fills a hole while a puddle weld creates a molten pool to join metals. Both techniques ensure sturdy connections but work best in different situations.
How is a Plate Prepared for a Plug Weld?
A plate is prepared for a plug weld by cleaning the surfaces and drilling a hole in one plate. Proper cleaning removes contaminants, ensuring good fusion. Use a drill size about 1/16 inches (1.5 Mm) larger than the filler material for optimal results.
What Dimensions Can Be Given for a Plug Weld?
Typically, plug weld dimensions vary but are often around 3/8 inches (9.5 Mm) to 1 inch (25.4 Mm) in diameter. Moreover, the depth should match the plate thickness to ensure a strong bond. Always tailor the dimensions based on your specific application.
Conclusion
I hope this gave you what you needed. We covered what a plug weld is, how it works, types of plug welds, the steps to create one, factors influencing plug welds, common issues that can arise, aftercare and inspection tips, typical applications, and alternatives to achieve similar results. This comprehensive look should equip you with a solid understanding of plug welding and its nuances.
I trust these insights have been helpful in answering ‘what is a plug weld.’ In simple terms, a plug weld is a type of weld that connects two pieces of metal through a hole in the top piece. Key data showed us the importance of proper plate preparation, correct dimensions, and awareness of potential issues which can affect quality. Armed with this knowledge, you’re better prepared for successful welding projects.
For more insightful information and the latest updates on welding topics, feel free to return to our homepage at What is Welding.
References
- American Society of Mechanical Engineers. (2019). ASME Section IX: Welding and Brazing Qualifications. New York, NY: ASME.
- Lancaster, J. F. (1999). The Physics of Welding (2nd ed.). Oxford, UK: Pergamon Press.
- Howard B. Cary. (1997). Welding Manual. Upper Saddle River, NJ: Prentice Hall.
Joe Carter is a retired welding professional with over 40 years of hands-on experience in the industry, spanning ship repair, structural welding, and even underwater projects. Joe is a master of MIG, TIG, and Stick welding. Passionate about mentoring the next generation of welders, Joe now shares his decades of expertise and practical insights to help others build rewarding careers in welding.
Adhesive Bonding, Construction Applications, Metal Fabrication, MIG Welding, Plug Weld, Repair Techniques, Spot Welding, Structural Integrity, Welding, Welding Processes, Welding Techniques