What Gas to Tig Weld Stainless Steel? Expert Tips, Gas Types, and Selection Steps!
Published on: January 23, 2025 | Last modified: March 4, 2025
By: Joe Carter
Stainless steel is a strong, corrosion-resistant metal made from iron, chromium, and other elements. It’s widely used in kitchens, construction, and automotive parts.
So, what’s the big deal about what gas to tig weld stainless steel? It’s crucial because the right gas affects the quality of your weld. From personal experience, using the wrong gas can lead to weak joints or defects, wasting time and materials.
In this guide, I’ll cover how gas works for TIG welding stainless steel, types of stainless steel, steps to choose the right gas, and factors influencing your gas choice. You’ll also find answers to common questions about what gas for stainless tig welding, so you’ll be prepared every time you start a project.
Contents
- What Gas to Tig Weld Stainless Steel?
- How Does the Right Gas for TIG Welding Stainless Steel Work?
- Types Of Stainless Steel
- Steps to Select the Right Gas
- Impact of Gas Flow Rate on TIG Welding Stainless Steel
- Factors Influencing the Choice Of Gas for TIG Welding Stainless Steel
- Frequently Asked Questions (FAQs)
- Conclusion
- References
What Gas to Tig Weld Stainless Steel?
Argon is your go-to gas for TIG welding stainless steel. It stabilizes the arc and provides a clean weld. Industries often use it for automotive and food processing to prevent contamination and ensure the highest strength.
How Does the Right Gas for TIG Welding Stainless Steel Work?
TIG welding, or Tungsten Inert Gas welding stainless steel, requires specific gases for optimal results. For stainless steel, Argon (Ar) is the best choice. Pure Argon provides excellent shielding, while adding up to 25% Helium can enhance the process by increasing heat input.
As you explore the welding world, you’ll notice the gas you choose can dramatically affect weld quality. Switching between pure Argon and a mixture can change arc behavior and weld penetration. Knowing the right blend is essential.
I can’t stress how crucial it is to use the right gas for TIG welding stainless steel. Argon protects the weld pool from contamination, ensuring strength and durability. From my experience, the right gas makes all the difference in achieving a clean, professional weld.
Types Of Stainless Steel
Austenitic Stainless Steels
Austenitic stainless steels are non-magnetic and contain high levels of chromium and nickel. To weld this type, use argon gas at a flow rate of 15-20 CFH (Cubic Feet Per Hour) for a clean weld. A welding machine precisely regulates electricity flow and generates the necessary heat, and understanding how a welding machine works will enhance your welding proficiency.
Ferritic Stainless Steels
Ferritic stainless steels are magnetic and have lower nickel content. Use argon gas for welding at a flow rate of 15-20 CFH to provide adequate shielding and prevent oxidation.
Martensitic Stainless Steels
Martensitic stainless steels have higher carbon levels, providing strength and hardness. Use argon for TIG welding, with a flow rate of 15-20 CFH for optimal protection against contamination.
Duplex Stainless Steels
Duplex stainless steels combine austenitic and ferritic properties. Use argon as the shielding gas, maintaining a flow rate of 20-25 CFH to manage the high alloy content and ensure a strong joint.
Precipitation-hardening Stainless Steels
Precipitation-hardening stainless steels can undergo additional heat treatment. Argon is still the preferred gas here. Set the argon flow to about 15-20 CFH to maintain a stable arc and secure weld.
That covers the different types of stainless steel. Let’s now take a look at how to choose the right gas.
Steps to Select the Right Gas
Here are the steps for selecting the best gas for TIG welding stainless steel. Take notes and follow along!
Determine the Type Of Stainless Steel
Identify the specific grade of stainless steel you’re welding, such as 304 or 316. The grade affects gas selection because different grades react differently during welding. For instance, 304 stainless steel typically requires pure argon, while 316 often performs well with an argon-helium mix. Knowing the type can enhance the weld’s durability and appearance. A critical step in achieving a strong weld is mastering techniques like the hot pass in welding.
Identify the Thickness Of the Material
Check the thickness of the stainless steel. For materials thicker than 3 mm (0.12 In), a mix of argon and helium provides a hotter arc. For thinner sections, use straight argon; it produces cleaner beads. Getting this wrong can lead to under-penetration or blow-through, so check your gauges!
Choose Between Argon, Helium, or a Mixture
Select your shielding gas based on your findings from the first two steps. For most stainless steel welding, argon is the preferred gas due to its stability and ease of use. Helium aids in heat management but is more expensive. Knowing your options is crucial—your weld quality depends on it!
Consider the Position Of the Weld
Determine if you’re welding flat, vertical, or overhead. The position affects your gas flow rate and coverage. For vertical or overhead welding, you may need increased gas flow to prevent contamination. Mismanaging this can lead to weld defects and costly rework!
Evaluate the Application Requirements
Examine the application, such as food processing, automotive, or structural uses. Each application may require a specific gas due to environmental conditions. For example, food-grade stainless often entails tighter controls on gas purity. Keep this in mind to ensure your weld meets both strength and compliance standards. For those considering more advanced techniques, it’s important to understand laser welder costs and options.
We have now covered the steps to choose appropriate gas for welding. Next, we’ll examine how gas flow rate affects TIG welding.
Impact of Gas Flow Rate on TIG Welding Stainless Steel
Understanding gas flow rate is key to achieving excellent welds. Let’s break down how it affects your work.
Weld Joint Type | Gas Flow Rate (CFH) | Recommended Mixture | Welding Position |
---|---|---|---|
Thin Materials (up to 1.6 mm / 0.0625 in) | 10-15 CFH | 100% Argon | Flat |
Medium Thickness (1.6 – 3 mm / 0.0625 – 0.12 in) | 15-20 CFH | 100% Argon | Vertical |
Thick Materials (above 3 mm / 0.12 in) | 20-25 CFH | 75% Argon, 25% Helium | Overhead |
Complex Welds | 20-30 CFH | 100% Argon (or mix) | All Positions |
As this table shows, correctly adjusting your flow rate enhances shielding and protects the weld pool from contaminants. Higher flow rates help cover larger gaps and thicker materials, preventing the weld from being affected by outside elements.
That covers the effects of gas flow rate on TIG welding stainless steel. Let’s now take a look at gas selection factors.
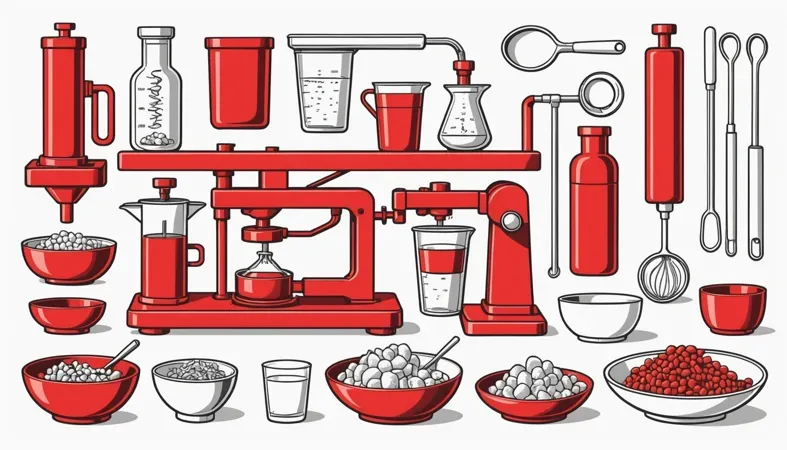
Factors Influencing the Choice Of Gas for TIG Welding Stainless Steel
What factors affect your gas choice when TIG welding stainless steel?
Welding Environment
Your welding environment matters. Indoor jobs usually require 100% argon for a stable shield against contaminants. Outdoor setups might need a helium mix to combat wind and improve arc stability.
Weld Joint Design
Joint designs dictate gas needs. For tight joints, 100% argon provides a fine finish. Wider joints may benefit from a gas mix for better penetration.
Heat Input Requirements
Heat input is crucial! Different grades of stainless steel, like 304 or 316, require specific heat settings. A higher input might need a helium blend due to its heat retention properties.
Shielding Gas Composition
The shielding gas mixture shapes arc characteristics. Pure argon is standard, but mixing in 25% helium increases heat input, allowing you to weld thicker sections more effectively.
Welding Technique
Your technique also impacts gas choice. A fast travel speed with a tight arc may work better with higher argon flow to avoid contamination. Slower, intricate welds often require less gas for better control.
We covered factors affecting gas selection for TIG welding stainless steel. We will now cover frequently asked questions.

Frequently Asked Questions (FAQs)
Now let us look at some common questions I typically get asked.
What Gas is Best for TIG Welding Stainless Steel?
The best gas for TIG welding stainless steel is generally 100% argon. Argon provides excellent shielding, preventing contamination and oxidation of the weld. Using argon ensures cleaner welds, reducing the need for post-weld cleaning and saving time. For effective techniques on how to weld thin metal, understanding the role of shielding gases is crucial.
Can You Use 100% Argon for TIG Welding Stainless Steel?
Yes, you can use 100% argon for TIG welding stainless steel. This gas effectively shields the weld area from atmospheric gases, which can cause defects. It’s standard practice and widely used in the industry because it results in high-quality welds.
What Stainless Gas for TIG Welding?
For TIG welding stainless steel, use 100% argon as the shielding gas. Argon minimizes the risk of oxidation, essential for a strong, durable weld. It’s suitable for most stainless steel applications, making it a preferred choice among welders.
What Color Tungsten for TIG Welding Stainless Steel?
Use green or yellow tungsten for TIG welding stainless steel. Green tungsten is typically 2% thorium, great for versatility, while yellow tungsten contains 1.5% lanthanum. These colors reflect the tungsten’s composition, allowing for better arc stability and improved performance.
Do You Need to Preheat Stainless Steel Before Welding?
Yes, you need to preheat stainless steel before welding. Preheating reduces stress and minimizes the risk of warping or cracking during the weld. Typically, a temperature of 150-200°F (65-93°C) is advised, which promotes better fusion of the materials.
How Thick Can Stainless Steel Be TIG Welded?
You can TIG weld stainless steel thicknesses up to 1 inch (25 mm) effectively. For thicker materials, you might need to bevel edges or use multi-pass welding. Using proper techniques enhances penetration and ensures a robust weld joint. Mastering techniques for welding vertical joints can significantly improve your skills and ensure weld integrity.
Conclusion
I’m glad we could cover this together. We discussed the right gas for TIG welding stainless steel, how it works, the types of stainless steel, steps to choose gas, and factors that influence your gas choice. Plus, I answered some frequently asked questions to clear things up.
Hopefully, I was able to impart some of my experience on what gas to TIG weld stainless steel. In simple terms, argon is your go-to gas and sometimes mixed with helium for greater heat. Remember, using pure argon gives you better results, especially when working on thin materials or specific stainless steel grades like 304 or 316.
For further insights and resources on welding techniques, tips, and best practices, feel free to explore What is Welding.
References
- American Welding Society. (2020). AWS Welding Handbook: Welding Science and Technology (Vol. 1). Miami, FL: AWS.
- Appleton, W. (2020). Welding and Cutting: A Practical Handbook. Hauppauge, NY: Nova Science Publishers.
Joe Carter is a retired welding professional with over 40 years of hands-on experience in the industry, spanning ship repair, structural welding, and even underwater projects. Joe is a master of MIG, TIG, and Stick welding. Passionate about mentoring the next generation of welders, Joe now shares his decades of expertise and practical insights to help others build rewarding careers in welding.
American Welding Society, Argon Gas, Construction, Gas Flow Rate, Stainless Steel, TIG Welding, Welding, Welding Materials, Welding Techniques