How to Weld Inconel? Techniques, Tips, & Common Issues
Published on: February 23, 2025 | Last modified: March 4, 2025
By: Joe Carter
Inconel is a high-performance alloy made mainly of nickel and chromium. It’s known for its excellent heat and corrosion resistance, making it invaluable in extreme environments.
I regularly get inquiries regarding how to weld inconel. It’s super important to get this right to ensure strong, durable joints. In my experience, following proper welding techniques can save you from costly mistakes down the road.
In this guide, you’ll find all you need to know about how to weld inconel. We’ll cover various types and their weldability, prerequisites, step-by-step welding processes, safety precautions, suitable welding techniques, influencing factors, common issues, aftercare and inspection tips, advantages of welding this alloy, applications, and some alternatives for achieving effective inconel welds.
Contents
- How to Weld Inconel?
- What is Inconel?
- Types Of Inconel and Their Weldability
- Prerequisites
- Welding Parameters for Inconel
- Steps to Weld Inconel
- Precautions
- Types Of Welding Techniques for Inconel
- Factors Affecting Inconel Welding
- Common Issues Unique to Inconel
- Aftercare, Inspection, and Advanced Tips for Welding Inconel
- Advantages Of Welding Inconel
- Applications You Should Know About
- Other Options for Achieving Inconel Weld Results
- Frequently Asked Questions (FAQs)
- Conclusion
- References
How to Weld Inconel?
Inconel is a nickel-chromium alloy known for its high heat resistance. To weld Inconel, use TIG welding with ERNiCr-3 filler metal. It can be tricky due to its susceptibility to cracking. Typical applications include aerospace and chemical processing.
What is Inconel?
Inconel is a family of superalloys made mainly from nickel, chromium, and iron. It’s known for its exceptional heat and corrosion resistance at high temperatures, making it ideal for extreme environments. For instance, Inconel 625 contains about 58% nickel and 22% chromium, which provide strength and oxidation resistance up to 1,800°F (982°C). It’s widely used in aerospace, chemical processing, and marine applications due to these outstanding properties.
Now, let’s discuss how to weld Inconel. Welding this alloy presents unique challenges due to its toughness and high thermal conductivity. I’ve found that the right settings make a significant difference; using the proper amperage while TIG (Tungsten Inert Gas) welding is crucial for success.
One notable project involved welding Inconel 625 pipe for a high-pressure system. It required precision and attention to detail, especially regarding the welding process. Techniques such as preheating can enhance quality, particularly when connecting to different materials. You might wonder, can you weld Inconel to carbon steel? Differences in properties can complicate this, but with the right approach, it’s possible!
Types Of Inconel and Their Weldability
What types of Inconel can you weld?
-
Inconel 625
Inconel 625 is known for its excellent corrosion resistance and high strength. Weld this type using TIG (Tungsten Inert Gas) welding with low heat input. Preheat the base metal to about 150°C (302°F) and use ERNiCrMo-3 filler rod to ensure a strong bond. Enhance your skills in this area by exploring how to heliarc weld.
-
Inconel 718
Inconel 718 is a high-strength alloy that performs well in high-temperature environments. When welding it, employ post-weld heat treatment to relieve stress. Preheat to about 100°C (212°F), use ERNi-1 filler material, and cool slowly to avoid cracking.
-
Inconel X-750
Inconel X-750 offers excellent oxidation resistance and high durability. Weld X-750 using the GTAW (Gas Tungsten Arc Welding) process with a nickel-based filler. Preheat to 200°C (392°F) and maintain a steady travel speed during welding for consistent penetration.
-
Inconel 600
Inconel 600 is valued for its good thermal and mechanical properties. Stick to the TIG process for solid results. Preheat to 150°C (302°F) and control arc stability for a clean joint.
-
Inconel 800
Inconel 800 combines high strength with oxidation resistance. When welding, use the TIG method with the appropriate filler rod. Preheat to about 50°C (122°F) and monitor heat input throughout the process. To ensure smooth welds without imperfections it is crucial to understand what causes weld spatter.
We’ve wrapped up the different types of Inconel and their weldability here. Let us turn our attention to prerequisites.
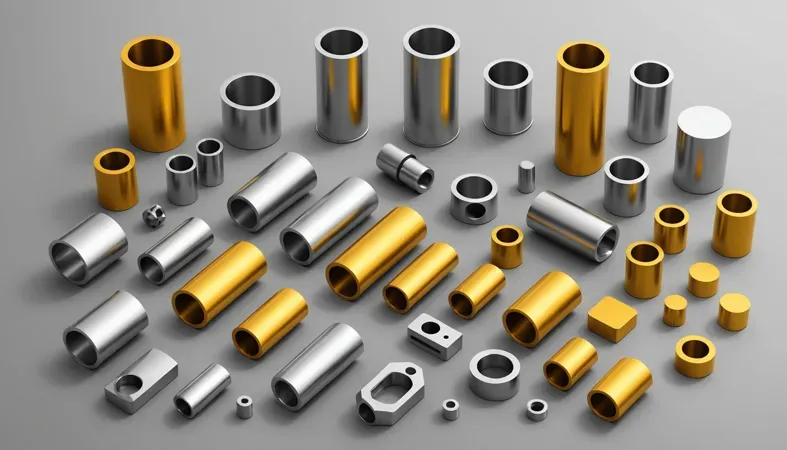
Prerequisites
What do you need to weld Inconel?
- TIG Welder: Use a specific TIG welder, like the Miller Dynasty 210. It provides precise heat control, which is crucial for welding Inconel.
- Inconel Welding Filler Rod: Get ERNiCr-3 rods, designed specifically for Inconel, ensuring strong joints.
- Welding Machine Specifications: You need a machine capable of at least 150 A (Amps). Inconel requires high heat and strong power.
- Back Purging Equipment: Use a back purging kit, such as the Miller 264081, for argon shielding. This prevents oxidation during welding.
- Welding Blanket: Invest in a high-temperature blanket, like the Tillman 1351. It protects surrounding areas and maintains heat distribution.
We covered the necessary prerequisites for working with Inconel. We will now cover the welding parameters specific to Inconel.
Welding Parameters for Inconel
Understanding welding parameters is crucial for effective Inconel welding. They directly influence the quality of your welds.
Parameter | Description | Recommended Range |
---|---|---|
Amperage | The amount of current used during welding. | 90-200 A (Amps) depending on thickness |
Voltage | The electric potential difference during the process. | 10-15 V for TIG welding |
Travel Speed | The speed at which the welding torch is moved. | 5-15 inches/min (12.7-38.1 cm/min) |
Heat Input | The total thermal energy applied during welding. | 1.0 to 1.5 kJ/in (39 to 59 kJ/m) |
Preheat Temperature | The initial heating of the base material before welding. | up to 300°F (150°C) |
We have now covered welding parameters for Inconel. The next section will discuss the steps involved in welding Inconel.
Steps to Weld Inconel
Now, we’ll cover the steps to weld Inconel. Here are the essential actions you need to follow closely.
-
Prepare the Work Area
Start by organizing your workspace. Ensure it’s clean, well-lit, and has ample ventilation—aim for at least 10 air changes per hour. Proper airflow helps minimize fumes. To enhance your setup, familiarize yourself with various welding processes that can affect your workspace efficiency. Eliminate any flammable materials nearby to ensure a safer welding environment.
-
Clean the Inconel Surface
Remove any contaminants like grease, dirt, or oxidation from the Inconel surface. Use a stainless steel brush or a grinder, then follow up with a solvent like acetone. This ensures strong adhesion and a quality weld. If you skip this step, you’ll likely regret it when you see defects in your weld.
-
Set Up the Welding Machine
Choose the right welding process for Inconel, typically TIG welding due to its precision. Set your machine to the appropriate parameters—usually around 90-130 amps for Inconel 625 with a thickness of 1/8 in (3.2 Mm). Select a filler rod like ERNiCrMo-3 for optimal fusion. Proper settings avoid issues like cracking or distortion in the weld.
-
Perform the Welding Process
Begin welding with a steady hand. Aim for a travel speed of 5-15 inches per minute (12.7-38.1 Cm/min) based on material thickness. Maintaining a 70-80° angle when feeding the filler rod is crucial to promote penetration and fusion. For more advanced techniques, you might explore specialized welding applications that can help create a uniform bead to enhance weld strength.
Proper handling can prevent a common issue known as weld flash accidents.
As you weld, monitor your heat input—generally, keep it below 1,000°F (538°C) to avoid warping. Adjust your machine if you notice any distortion. Remember, small mistakes can lead to significant issues, so stay focused!
We have now covered the steps to weld Inconel. In the next section, we will discuss important precautions.
Precautions
Let’s review essential safety tips for welding Inconel.
- Proper Ventilation: Always ensure good airflow to avoid fumes. Use a portable fan or exhaust hood.
- Proper Protective Gear: Wear a welding helmet and gloves to protect against sparks. I recommend the Lincoln Electric K3034-4 for excellent protection.
- Safe Workspace: Keep your environment free of flammable materials. Clear the area of debris and tools to ensure a clean setup for maximum safety.
- Emergency Equipment: Have a fire extinguisher ready, preferably a Class B, to quickly tackle metal fires.
Remember, staying safe while welding isn’t just smart—it’s crucial for achieving the best results!
Types Of Welding Techniques for Inconel
Let’s explore different welding techniques: TIG, MIG, Stick, Plasma Arc, and Electron Beam welding.
-
TIG Welding
TIG (Tungsten Inert Gas) welding is excellent for Inconel. It offers precise control, using a tungsten electrode and argon as the shielding gas. For Inconel 625, you’ll need about 150-200 amps for optimal results.
-
MIG Welding
MIG (Metal Inert Gas) welding is effective, especially with Inconel 718. This method is faster and uses a continuous wire feed as the electrode. Aim for a voltage of 20-30 volts for a strong bond. To ensure your tools run efficiently, it’s crucial to determine the right generator size for your equipment.
.
-
Stick Welding
Stick welding is versatile for Inconel, particularly outdoors. It uses a coated electrode and generates high heat, suitable for thick sections. Target an amperage of 120-180 amps for best results.
-
Plasma Arc Welding
Plasma Arc Welding (PAW) offers more precision than TIG. This technique uses a plasma torch to create a small, concentrated arc, effectively handling Inconel up to 10 mm (0.39 In) thick.
-
Electron Beam Welding
Electron Beam Welding (EBW) is a high-vacuum process that efficiently joins Inconel alloys with minimal heat-affected zones. It can penetrate thick sections, up to 50 mm (1.97 In).
Factors Affecting Inconel Welding
What factors influence your success when welding Inconel? Let’s break it down.
-
Material Thickness
Material thickness directly affects heat distribution during welding. Thicker sections over 1 inch (25.4 Mm) require higher heat input for proper fusion.
-
Welding Heat Input
High heat input can cause warping and changes in microstructure. For Inconel, aim for a heat input of 1.0 to 1.5 kJ/in (39 to 59 Kj/m) for optimal results.
-
Electrode Type
The right electrode can make or break your weld. Use ERNiCr-3 or ERNiCr-4 for Inconel 625; they enhance corrosion resistance. Incorrect choices can lead to weak joints.
-
Shielding Gas Composition
Proper shielding is crucial to prevent oxidation. A mix of 98% argon and 2% hydrogen provides excellent coverage for Inconel welding.
-
Preheat Temperature
Preheating Inconel can reduce stress and cracking. Target a preheat temperature of 300°F (150°C) for better results.
Common Issues Unique to Inconel
Here are some unique challenges you might face when welding Inconel.
-
Cracking During the Weld
Inconel can crack during welding due to rapid cooling. Look for visible fissures. To resolve this, preheat the material to 300°F (About 150°C) and limit cooling in air.
-
Deterioration Of the Weld Pool
Inconel’s high nickel content can lead to oxidation if not shielded properly. A dull finish indicates deterioration. Using the right shielding gas like argon can prevent this.
-
Inadequate Fusion
Inconel may have inadequate fusion between layers. Use visual inspection to spot gaps. Increase your amps for better penetration, but monitor heat input closely.
-
Overheating Of the Base Metal
Inconel requires balanced heat input; too much can cause warping. Monitor temperatures using a thermocouple, aiming for a maximum of 1,500°F (800°C) during welding.
-
Contamination Of the Weld Metal
Inconel welds can easily become contaminated. Watch for foreign materials in your workspace. Clean the joint with a wire brush and wipe surfaces with acetone before welding.
Aftercare, Inspection, and Advanced Tips for Welding Inconel
Here are some tips for after you’ve welded Inconel.
Aftercare Tips
After welding Inconel, allow it to cool slowly to avoid thermal stress. Keep the heat below 300°F (149°C) to prevent unwanted grain growth. Use saturated steam or a wet cloth to remove slag within an hour for better surface integrity.
Inspection Techniques
First, inspect welded joints visually for color and texture anomalies. Use a non-destructive testing (NDT) method, like ultrasonic testing (UT), to find subsurface flaws. I recommend using a Sonatest Tester Model T4; it provides unmatched clarity in results.
Expert Tips
I focus on interpass temperature—keep it below 300°F (149°C) using a pyrometer during pulls. Enhance the preheat phase; while moving the torch, maintain at least 100°F (38°C) for better penetration. Lastly, I always use high-performance filler material like INCONEL 625 in my passes for added strength.
Advantages Of Welding Inconel
The main benefit of welding Inconel is its excellent resistance to extreme temperatures and corrosion. This makes it ideal for high-performance applications, like aerospace and chemical processing. When it comes to repairing alloy wheels, understanding how many times you can weld them would be crucial for maintaining their structural integrity.
Inconel also offers exceptional mechanical strength, durability, and versatility. It provides improved weld integrity, a reduced risk of cracking, and enhanced fatigue resistance. Lastly, Inconel’s compatibility with various welding methods, such as MIG and TIG, makes it easier to work with.
Applications You Should Know About
I’ve used Inconel welding for gas turbines, but it has many applications such as:
- Marine Components: Inconel is ideal for underwater parts. Its corrosion resistance is key in harsh salty environments, making it popular in naval engineering.
- Aerospace Structures: Welded Inconel parts are essential in jet engines. They endure high temperatures, making them a preferred choice for aircraft components.
- Chemical Processing: Inconel is utilized for reactors in processing plants. Its capability to handle extreme heat and pressure is favored in the industry.
- Pump Shafts: Inconel is found in pump shafts that operate in harsh conditions. It’s strong, durable, and resists wear better than most materials.
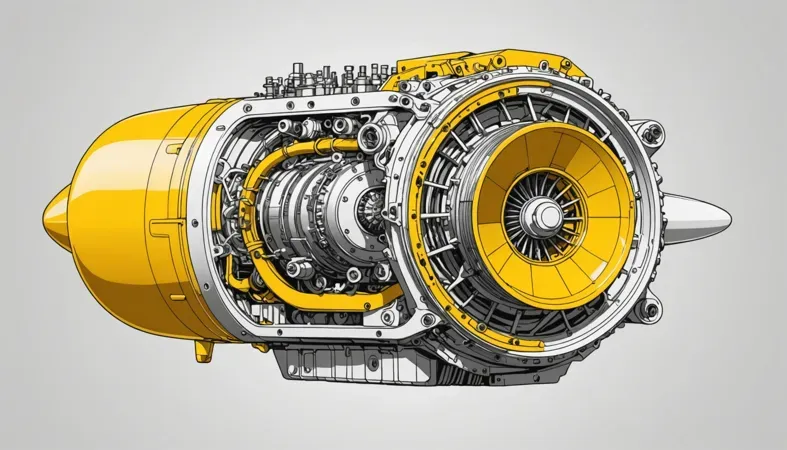
Other Options for Achieving Inconel Weld Results
There are several alternatives if you need to achieve similar results to the process of welding Inconel. Using superalloys like Hastelloy C276 can work effectively in high-temperature environments due to their corrosion resistance and strength. Based on my observations, methods such as Laser Beam Welding (LBW) can provide precise control and reduce heat input, making it ideal for delicate applications.
Another good route is to use filler metals like Inconel 625 welding rods. They can improve the joint’s properties, especially in dissimilar metal applications, like welding Inconel to carbon steel. These products can offer great advantages depending on your project needs.
Frequently Asked Questions (FAQs)
Here are some questions I typically get asked about Inconel welding.
What is the Best Way to Weld Inconel?
The best way to weld Inconel is by using the TIG (Tungsten Inert Gas) method. This method provides precision, reduces contamination risk, and works well with Inconel’s high nickel content, which can range from 50% to 70%. TIG welding ensures deep penetration and clean welds. Mastering specialized techniques can simplify challenging tasks such as welding upside down.
What Rod is Used to Weld Inconel?
You typically use Inconel filler rods, such as Inconel 625, to weld Inconel. Using the correct filler rod ensures compatibility with the base metal and helps maintain strength and corrosion resistance. The choice of filler can depend on the specific Inconel grade being welded. For effective techniques on pipe welding using popular electrodes, explore welding pipe with 6010.
What is Required for Welding Inconel?
Welding Inconel requires high-quality filler rods, proper shielding gas, and often preheating. Shielding gas like Argon is essential to prevent contamination; it’s recommended to use a flow rate of approximately 15 to 20 cubic feet per hour (CFH). Advantages include minimized oxidation and a better weld finish.
What Gas Do You Use to Weld Inconel?
Argon is the preferred gas used for welding Inconel. Argon protects the molten weld pool from atmospheric contamination. Stability helps maintain the quality of the weld, especially at elevated temperatures, where Inconel can be sensitive to oxidation and nitrides.
Can You Weld Inconel to Carbon Steel?
Yes, you can weld Inconel to carbon steel, but it requires careful preparation and specific techniques. The weld joint can experience thermal stresses, and utilizing a transition filler rod can minimize issues. You may need to monitor heat input to prevent cracking.
Conclusion
We covered different aspects of welding Inconel, including what Inconel is, types and weldability, prerequisites, steps for welding, precautions, and various welding techniques. We also looked at factors affecting Inconel welding, common issues you may face, as well as aftercare, inspection, and advanced tips. Finally, we chatted about the advantages of welding Inconel and explored some applications.
So, how to weld Inconel? In a nutshell, prepare your materials, choose the right technique, and follow the steps. Keep in mind factors like temperature, filler materials, and potential issues, as they can make or break your weld quality. Remember, Inconel isn’t just any metal; it’s a specialty alloy that requires your full attention.
For further insights and expert recommendations on welding techniques, please visit What is Welding.
References
- American Society of Mechanical Engineers. (2019). ASME Section IX: Welding and Brazing Qualifications. New York, NY: ASME.
- Smith, D. L. (2010). Welding: A Journey to Explore Its History. Dubuque, IA: Kendall Hunt Publishing Company.
Joe Carter is a retired welding professional with over 40 years of hands-on experience in the industry, spanning ship repair, structural welding, and even underwater projects. Joe is a master of MIG, TIG, and Stick welding. Passionate about mentoring the next generation of welders, Joe now shares his decades of expertise and practical insights to help others build rewarding careers in welding.
Alloy, Inconel, Materials Engineering, Pipe Welding, Safety Tips, TIG Welding, Welding, Welding Applications, Welding Techniques