How to Make a Spot Welder? DIY Steps, Safety Tips, and Essential Tools
Published on: February 4, 2025 | Last modified: March 4, 2025
By: Joe Carter
A spot welder is a machine used to join two pieces of metal together by applying heat and pressure. It’s quick, efficient, and great for tasks like welding car parts.
It’s a question that often arises: how to make a spot welder. Knowing how to make a spot welder is key if you want to tackle sheet metal projects at home. In my experience, having a reliable spot welder can save you time and money, and knowing the right steps is crucial.
In this guide, we’ll cover the different types of spot welders, essential prerequisites for setting up, detailed steps to make your own spot welder, safety tips, factors that affect performance, and even common issues to watch out for. You’ll get insights into how to make a spot welder from a battery charger, aftercare for your device, applications you should know about, and alternative methods too.
Contents
- How to Make A Spot Welder?
- What is a Spot Welder?
- Types Of Spot Welders
- Essential Prerequisites to Get Started
- Safety Tips
- Steps to Make a Spot Welder
- Types Of Welding Options for Spot Welders
- Factors That Affect Spot Welder Performance
- Common Issues
- Benefits of Homemade Spot Welders
- Key Benefits Of Spot Welding
- Applications You Should Know About
- Alternatives for Making a Spot Welder
- Frequently Asked Questions (FAQs)
- Conclusion
- References
How to Make A Spot Welder?
A spot welder is a device that joins metal pieces using electric current. To make one, use a 240 V (110 V) transformer and copper electrodes. It’s moderate in difficulty, ideal for automotive and metalworking projects. If you are considering whether it’s permissible to apply your welding skills on vehicle components, you might want to understand if you can legally weld a car frame.
What is a Spot Welder?
A spot welder is a device used to weld metal components together by applying heat and pressure at specific points, or “spots.” Typically, a spot welder employs two electrodes to deliver a high current pulse, usually around 10,000 to 20,000 amps. This surge of electricity causes the materials to melt and fuse, creating a strong bond. Spot welders work best on thin sheets of metal, with thicknesses ranging from 0.5 mm to 3 mm (0.02 In to 0.12 In), making them popular in industries like automotive manufacturing.
If you’re curious about how to make a spot welder, I’ve got you covered. Building your own spot welder can be an engaging project, especially if you use tools and materials you already have. I remember using an old battery charger to create a simple spot welder; it turned out pretty well!
It came in handy when I needed to join metal parts quickly and couldn’t find a commercial unit. I decided to make a homemade spot welder, and it saved the day! With resources like tutorials on making a spot welder from a battery charger, you can easily set up your own system at home, just like I did. It’s fascinating how accessible these projects can be!
Types Of Spot Welders
What types of spot welders should you know about?
-
AC Spot Welders
AC spot welders use alternating current to create welds. They require a 240V AC supply and a basic transformer with an electrode setup to regulate power.
-
DC Spot Welders
DC spot welders use direct current for consistent heat. You can create one using a car battery or power supply. Connect it with proper cables to the welding tips for strong joints.
-
Pneumatic Spot Welders
Pneumatic welders use air pressure to press the electrodes together. To build one, incorporate an air compressor with a solenoid valve and connect it to a basic welding setup for consistent clamping force.
-
Manual Spot Welders
Manual spot welders require human operation for precise control. You can create one using basic clamps and high-current wires connected to a switch and power source.
-
Automated Spot Welders
Automated machines control the welding process for efficiency. To build one, use a microcontroller (Like Arduino), robotic arms, and spot welding tips. Integrate these components for precise operations.
That covers various types of spot welders. Let’s now take a look at the essential prerequisites to get started.
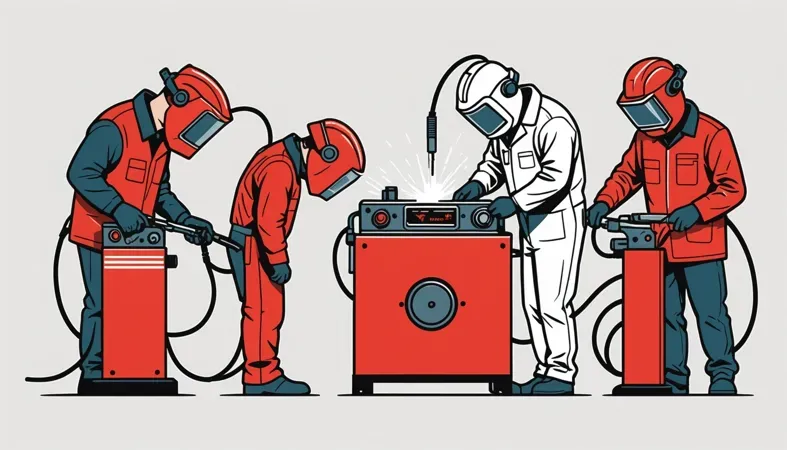
Essential Prerequisites to Get Started
What do you need to start making a spot welder?
- Transformer: You’ll need a transformer like the Sunkee 160W Variable. It reduces voltage for safe welding at 120V (About 30A).
- Steel Electrodes: You’ll need electrodes such as the 8mm Copper Spot Welding Electrodes. They conduct electricity effectively for strong welds.
- Thermal Paste: You’ll need thermal paste like Arctic Silver 5. It improves thermal conductivity for quicker, more stable welds.
- Battery or Power Supply: You’ll need a power source, such as a 12V (About 7ah) car battery, to ensure adequate current for reliable welding.
- Copper Cable: You’ll need high-quality copper cable, like 10 AWG (American Wire Gauge), to safely handle the high current during welding.
That covers the key essentials to get started. Let’s now take a look at important safety tips.
Safety Tips
Here are essential precautions for making a spot welder.
- Wear Protective Gear: Always wear gloves and goggles when welding to prevent burns and eye damage. Consider using welding gloves like 3M Highland for better grip.
- Check for Fire Hazards: Keep flammable materials away from your welding area. Use a fireproof blanket, like the YesWelder Fire Blanket, to protect your surroundings.
- Inspect Equipment: Ensure your electrical connections are tight and safe to reduce shock risks. Use a multimeter to check proper voltage before starting your project.
- Ventilate the Workspace: Weld in a well-ventilated area to avoid harmful fumes. A simple fan can significantly increase airflow—about 50 cubic feet per minute (Cfm) helps.
Safety precautions matter—I’ve learned this the hard way, and I want you to stay safe!
So far we covered essential safety precautions. Let’s look at the process of building a spot welder next.
Steps to Make a Spot Welder
Here are the steps to create your own spot welder from a few key components.
-
Construct the Electrode Tips
First, cut two copper rods into 10 cm (4 Inches) pieces. These rods serve as the electrode tips, where the actual welding occurs. Use a file to smooth the ends; this improves conductivity and leads to better welds. Ensure the ends of your electrodes fit snugly against the material you plan to weld. Proper understanding of what weld flash is can enhance your welding safety and efficiency.
Choose the right copper for your design. Soft copper works best, but you might also find success with brass. If you don’t have copper, repurpose any old electrical wire that’s about 1.5 mm (0.06 Inches) thick.
-
Assemble the Transformer
Next, obtain a transformer to reduce the voltage. Salvage one from a microwave oven or buy a 12V transformer. This step is crucial to prevent overheating and increase efficiency. Connect the primary coil to your power source and ensure the secondary side is intact for a stable 12V output.
Aim for at least 100 Amperes for effective welding. If you’re using a battery, a lead-acid battery delivers a solid current without fluctuating.
-
Wire the Circuit Properly
Now, connect everything. Start by connecting one end of the transformer to the electrodes and the other end to your switch. Use thick wires rated for high current for reliable performance. In my builds, 8 AWG wire minimizes voltage drop.
After wiring, check your connections closely. A loose connection can ruin your welder’s performance or damage components. Double-check your setup before powering it on to avoid future headaches.
-
Test the Spot Welder
Finally, conduct a test weld on a scrap metal piece. Adjust the pressure between the electrodes—ideally around 150-200 grams (5.3-7.1 Ounces) of applied pressure. Keep your weld time to about 1-3 seconds for thin sheets and longer for thicker materials. Monitor the results to ensure good fusions.
After achieving satisfactory welds, continue adjusting as needed. I once mistakenly applied the same pressure for different materials and learned that various metals react differently under the same conditions.
We have now covered the steps to create a spot welder. Next, we will explore various welding options for spot welders.
Types Of Welding Options for Spot Welders
Let’s look at the different welding types: Resistance Spot Welding, TIG Welding, MIG Welding, Laser Spot Welding, and Ultrasonic Spot Welding.
-
Resistance Spot Welding
Resistance Spot Welding (RSW) uses heat from electrical resistance. You apply pressure to weld two metal parts together. It’s fast, reliable, and common in the automotive industry. This method usually requires about 2 to 5 kilovolts (Kv) for effective welding. Efficient use of resistance welding is crucial, but it’s important to be aware that welding can pose risks to eye health; for more information, find out how welding affects vision.
-
TIG Welding for Spot Applications
TIG (Tungsten Inert Gas) Welding allows for precise control over the weld pool. You can use a foot pedal for variable heat. It’s ideal for smaller, intricate welds, often needing 20 to 300 amps depending on material thickness. I recommend this for anyone making a spot welder at home for precision work. Understanding the various welding processes can help you choose the best technique for your project.
In welding, a hot pass is crucial for refining the weld bead by melting away slag inclusions and ensuring a smooth finish, making it essential to understand what a hot pass in welding involves.
-
MIG Welding Techniques
MIG (Metal Inert Gas) Welding is known for its versatility and speed. It uses continuously fed wire and works well with various metals. Settings typically range from 50 to 600 amps, allowing you to create strong spot welds on thicker materials easily. It can also be modified to build your own spot welder. To ensure consistent performance with a 140 amp welder it’s important to understand what size generator you need.
-
Laser Spot Welding
Laser Spot Welding uses high-energy laser beams to create welds. It’s precision-focused and minimizes thermal impact on surrounding materials. Typically, it requires a power of 1000 watts or more, making it ideal for industries needing delicate work or unique materials.
-
Ultrasonic Spot Welding
Ultrasonic Spot Welding uses high-frequency vibrations to join materials. This technique is effective with thin materials or plastics. It works within milliseconds, requiring very little pressure, which is advantageous for creating compact fabrications, such as those you might develop in a mini spot welder. One of the essential considerations in welding is understanding how dangerous welding can be, especially when high-frequency equipment is involved.
Factors That Affect Spot Welder Performance
What factors influence how effectively you can weld? Here are the key ones.
-
Material Thickness
Material thickness affects the heat and pressure needed for a strong weld. Typically, materials ranging from 0.5 mm to 3 mm (0.02 In to 0.12 In) are spot-welded using various techniques, so assess your materials to choose the right setup. Proper electrical setup is crucial for operating welding equipment safely, and you may refer to this guide on wiring a 220 outlet for a welder to ensure correct installation.
-
Electrode Pressure
Electrode pressure must be precisely controlled to create firm, quality welds. Too little pressure can lead to weak welds, while excessive pressure may cause burn-through. Ideal pressure is typically 40-80 kg (88-176 Lbs).
-
Current Level
Target a current level of around 7,000 to 12,000 amps for proper weld penetration. Different types of spot welders may need adjustments, so ensure your welder is compatible with your material.
-
Weld Time
Weld time indicates how long the current runs during welding. A typical range is 5 to 50 cycles; shorter for thinner materials and longer for thicker ones, allowing enough time for proper heating without overheating.
-
Cooling Rate
The cooling rate after welding affects strength and durability. Rapid cooling helps achieve harder metals, while slower cooling can improve toughness. Cooling water or forced air can enhance this process.
Common Issues
Let’s look at unique spot welder problems you might face.
-
Inconsistent Welds
A spot welder may produce inconsistent welds due to fluctuating current. Check the machine’s power settings and adjust them. Aim for a steady current of 800-1,200 amperes.
-
Electrode Wear
Spot welders often experience electrode wear that affects performance. Check electrode tips every 100 welds. Replace worn tips promptly to ensure quality.
-
Overheating Components
Your spot welder’s components can overheat, leading to failures. Look for thermal overloads. Add cooling to the transformers or reduce work cycles to fix this.
-
Poor Electrical Connections
A spot welder can struggle if electrical connections are loose or corroded. Examine all connections and tighten or clean as necessary to maintain a good flow of electricity.
-
Alignment Problems
Spot welders can misalign pins, causing inconsistent contact. Check the gripper and electrode alignment; adjust as needed to maintain proper weld contact.
Benefits of Homemade Spot Welders
If you’re considering making your own spot welder, you should know the numerous benefits it offers.
Benefit | Description | Cost Savings | Customization |
---|---|---|---|
Cost Efficiency | Building your spot welder can save you hundreds of dollars compared to buying a commercial model. | Up to 60% savings by using simple parts. | You can tweak the design to fit your unique needs. |
Skill Development | You gain hands-on experience with welding, electronics, and tool assembly. | Invaluable skills applicable to various projects. | Learn to troubleshoot and maintain your machine. |
Accessibility | Homemade welders can use easily sourced materials; no need for high-end equipment. | A budget-friendly way to get started. | Adaptable to available components to optimize results. |
Learning Opportunity | Every build teaches you about electricity, welding methods, and material properties. | Understanding the science behind welding can improve your skills exponentially. | Hands-on projects build confidence for future builds. |
Building your own spot welder isn’t just about the task at hand; it’s a gateway to greater DIY projects and enhanced mastery in metalworking. Are you ready to dive in?
Key Benefits Of Spot Welding
The main benefit of making a spot welder is cost savings. It proved useful for my work when I needed a reliable tool without spending a fortune.
You also gain flexibility. You can create various designs and sizes that meet your specific needs, customize parts, and use readily available materials. Plus, it’s a great learning experience that enhances your skills in welding and electronics. Imagine tackling projects like building a mini spot welder or a homemade unit!
Applications You Should Know About
I’ve known people who use spot welders for various tasks. They have unique applications such as:
- Automotive Repairs: Spot welders fix car frames quickly and securely, making them popular in auto shops.
- Sheet Metal Fabrication: These welders bond thin sheets of metal, like aluminum for appliances. Strong joints are essential for durability.
- Electronics Assembly: In circuit board manufacturing, spot welders connect battery tabs. Precision is crucial, and they excel at this.
- Art and Sculptures: Artists use handmade spot welders to create intricate metal art. It’s all about making seamless connections effortlessly.
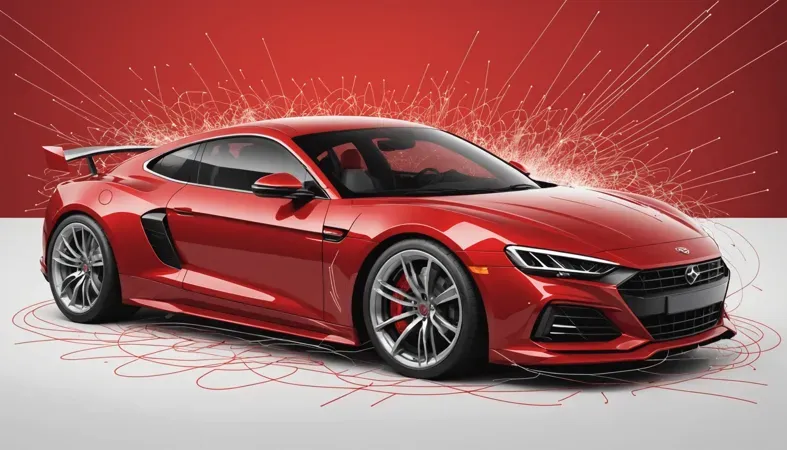
Alternatives for Making a Spot Welder
You’ve got options if you wanna achieve similar results as making your own spot welder. Products like the Mini Spot Welding Machine offer an easy plug-and-play solution, perfect for lighter projects. You might prefer a Battery Spot Welder since it’s portable and runs on 12V battery power, making it convenient for outdoor work.
Don’t forget about using tools you might already own. You can make a spot welder using an arc welder for more robust tasks without the hassle of building from scratch. Again, these methods are quick ways to tackle your welding needs efficiently and effectively!
Frequently Asked Questions (FAQs)
Here are some questions I typically get asked regarding spot welding.
How Many Volts Are Needed to Spot Weld?
To spot weld effectively, you’ll typically need between 4 to 6 volts. This low voltage allows current to flow easily through the materials, creating enough heat for fusion. Most industrial spot welders operate at around 1000 to 2000 amps, ensuring a strong weld in milliseconds.
Can You Spot Weld With a Regular Welder?
No, you can’t spot weld with a regular welder. Spot welding requires precise, high-voltage bursts of energy that standard MIG or TIG welders don’t provide. Using a regular welder might not only yield poor results but can also damage your materials.
Can You Turn a MIG Welder Into a Spot Welder?
Yes, you can turn a MIG welder into a spot welder with modifications. By reducing the voltage and adjusting the feed settings, you can achieve a suitable output for spot welding. However, be aware that this could limit the versatility and efficiency of your MIG machine.
Can You Make a Spot Welder With a Microwave?
No, making a spot welder with a microwave isn’t practical. Microwaves don’t generate the high current and low voltage needed for effective spot welding. While it’s creative thinking, it simply doesn’t match the requirements for a strong, durable weld.
How Thick Of Material Can a Spot Welder Handle?
A spot welder can typically handle materials up to 3 mm (0.125 Inches) thick. For thicker materials, the weld quality diminishes, and more complex welding techniques may be necessary. Spot welding is best suited for thinner sheets, often used in automotive panels.
What Materials Can Spot Welding Be Used on?
You can spot weld various materials, especially mild steel, stainless steel, and aluminum. Each material has specific current and time requirements; for instance, aluminum needs higher heat due to its thermal conductivity. Understanding these quirks helps ensure quality welds.
Conclusion
I’m glad we could cover this together. We talked about how to make a spot welder, the types of spot welders available, essential prerequisites, safety tips, and steps to create one. Plus, we touched on welding options, performance factors, common issues, and aftercare.
Hopefully, I was able to impart some of my experience about making a spot welder. In simple terms, you gather the right materials, follow the setup steps, and prioritize safety. Remember, whether you want to make a spot welder from a battery charger, an arc welder, or even build a mini one, you can do it safely if you have the right info.
For further insights and resources on welding, check out What is Welding.
References
- Lincoln Electric. (2020). The Procedure Handbook of Arc Welding (15th ed.). Cleveland, OH: Lincoln Electric Company.
- Blodgett, O. W. (1996). Design of Welded Structures. Cleveland, OH: James F. Lincoln Arc Welding Foundation.
Joe Carter is a retired welding professional with over 40 years of hands-on experience in the industry, spanning ship repair, structural welding, and even underwater projects. Joe is a master of MIG, TIG, and Stick welding. Passionate about mentoring the next generation of welders, Joe now shares his decades of expertise and practical insights to help others build rewarding careers in welding.
DIY Spot Welder, Homemade Tools, Metalworking Projects, Safety Tips, Spot Welding Equipment, Voltage Drop, Welding, Welding Equipment, Welding Techniques, Wire Gauge