Can You Weld Stainless to Mild Steel? Explore Techniques, Safety, and Tips!
Published on: January 3, 2025 | Last modified: March 4, 2025
By: Joe Carter
Stainless steel is a type of steel that contains chromium, making it resistant to rust and corrosion. It’s popular for its durability and clean look in various projects.
If you thought can you weld stainless to mild steel was a straightforward question, you’d be partly right. It’s essential to know how and when to do this because it affects strength and appearance. In my experience, following the right process saves you from messy results over time.
In this guide, you’ll explore the types of stainless steel and their weldability, essential prerequisites for welding, steps to weld stainless to mild steel, safety tips, welding methods, factors affecting the weld, common problems, aftercare, and advantages. You’ll also learn the applications across various fields and alternatives to welding. Understanding these elements helps you grasp the concept: can you weld mild steel to stainless steel without issues?
Contents
- Can You Weld Stainless to Mild Steel?
- What is Stainless Steel?
- Types Of Stainless Steel and Their Weldability
- Essential Prerequisites to Get Started
- Steps for Welding Stainless to Mild Steel
- Safety Tips
- Types Of Welding Methods for Stainless and Mild Steel
- Factors That Affect Welding Stainless to Mild Steel
- Common Filler Materials for Welding Stainless to Mild Steel
- Typical Problems to Be Aware Of
- Aftercare, Inspection, and Advanced Tips for Welding Stainless to Mild Steel
- Why This is Worth It: Advantages
- Applications Across Different Fields
- Alternatives for Achieving Results Similar to Welding Stainless to Mild Steel
- Frequently Asked Questions (FAQs)
- Conclusion
- References
Can You Weld Stainless to Mild Steel?
Yes, you can weld stainless to mild steel, but it’s tricky. The difficulty lies in their different properties. Use a filler metal like ER309L for the best results, ensuring a strong bond.
What is Stainless Steel?
Stainless steel is an alloy known for its corrosion resistance. It primarily contains iron and at least 10.5% chromium. This chromium forms a thin layer of chromium oxide on the surface, protecting it from rust and oxidation. Additionally, stainless may contain nickel, molybdenum, and other elements that enhance its properties.
When it comes to welding, you might wonder, “Can you weld stainless to mild steel?” This is a common topic in welding circles. I’ve experienced this during a project, and it’s fascinating how the differences in the metals impact the outcome.
I once used stainless for an exhaust system. The combination of heat resistance and strength is unmatched. While working on such a project, I’m often asked, “How do you weld stainless to mild steel?” The right technique and materials make a significant difference in the strength and durability of your weld.
Types Of Stainless Steel and Their Weldability
What are the types of stainless steel, and how do they weld to mild steel?
-
Austenitic Stainless Steels
Austenitic stainless steels, such as 304 and 316, are known for corrosion resistance and excellent weldability. You can easily join these with mild steel. Use a niobium or titanium-based filler to prevent corrosion at the joint.
-
Ferritic Stainless Steels
Ferritic stainless steels, like 430, have less nickel and are more magnetic. Their compatibility with mild steel is limited. To ensure a strong weld, preheat both materials and choose a filler appropriate for mixed-material welding. If you need to undo a weld, understanding methods for removing welds can be crucial for maintaining material integrity and preparing for subsequent procedures.
-
Martensitic Stainless Steels
Martensitic stainless steels, such as 410, are strong and hard. Welding to mild steel can be challenging. Preheat both metals and use a filler rod designed for martensitic steel for a good bond. It’s crucial to understand how to protect yourself from hazardous fumes during the welding process, and one way is to prevent inhaling welding fumes.
-
Duplex Stainless Steels
Duplex stainless steels combine austenitic and ferritic properties. You can weld these to mild steel with care. Always use a filler that matches the duplex’s chemistry to prevent corrosion.
-
Precipitation Hardening Stainless Steels
Precipitation hardening steels are known for their strength. Welding to mild steel is possible, but be cautious. Apply controlled heating and use a suitable filler designed for hardening stainless steel to achieve a strong bond.
Proper techniques must also be applied when joining various types of specialized wires in industrial applications. A comprehensive understanding of how to weld thermocouple wire can significantly improve results.
We covered the various types of stainless steel and their weldability here. Next, we will cover key prerequisites to begin.
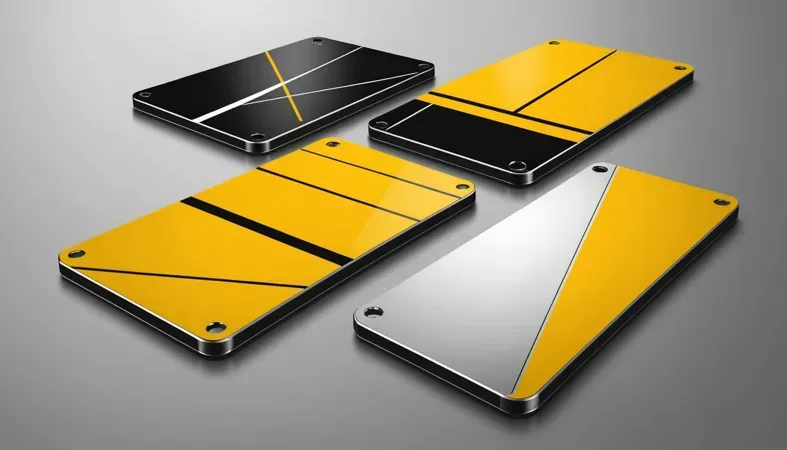
Essential Prerequisites to Get Started
What do you need to weld stainless steel to mild steel?
- MIG Welder: Use a machine like the Millermatic 211; it’s ideal for welding stainless steel to mild steel.
- Stainless Steel Filler Rods: Use AWS ER308L rods, which match the chemistry for a strong weld.
- TIG Welder: A unit like the Everlast Power TIG 250EX works well for a clean, controlled weld.
- Wire Brush: Stainless steel wire brushes are essential for prepping the surface, ensuring better adhesion and a cleaner weld.
We’ve wrapped up the essential prerequisites to get started. Next up, we’ll look at steps for welding stainless to mild steel.
Steps for Welding Stainless to Mild Steel
Now, we’ll cover the steps for successfully welding stainless steel to mild steel.
-
Prepare the Base Metals
Start by thoroughly cleaning both the stainless and mild steel surfaces. Remove any rust, oil, or contaminants using a wire brush or grinder. Aim for a surface with less than 1 microgram of dirt for optimal welding.
Don’t skip the cleaning step; leftover material can lead to poor fusion and weak welds.
-
Select the Right Filler Material
Choosing the correct filler material is crucial. Use a filler rod or wire that matches the stainless steel type, typically 308L for welding to mild steel. This rod melts at about 1400°C (2550°F), ensuring a strong bond.
If you use ER316L wire, it’s more resistant to corrosion but pricier. Weigh your options based on your project’s exposure to elements.
-
Set Welding Parameters
Adjust your welder’s settings for optimal performance. Typically, a voltage of 18 to 22 volts works for MIG welding stainless to mild steel. Set the wire feed speed between 8 to 12 m/min (26 to 39 Ft/min) according to your machine’s specifications.
I’d start with lower settings and adjust based on bead quality. It’s easier to increase settings than to decrease them once you’ve started welding.
-
Begin Welding Technique
Use a weaving or circular motion while welding to ensure proper fusion between the metals. Hold the torch at a 15° angle and maintain a steady pace for consistent bead formation, aiming for a travel speed of around 5 cm/s (2 In/s).
You might face undercutting on the stainless; keep practicing different techniques until you find the right approach for smooth, aesthetic beads.
-
Control Heat Input
Too much heat can warp the metals, so keep it manageable. Aim for a heat input of around 1.5 kJ/cm (1.5 Kj/in). This level helps avoid distortion while ensuring good penetration.
Controlling the heat input keeps the welds strong and prevents stress fractures in the stainless steel. Pay attention to how the metals behave during the process.
You should now have a good understanding of welding stainless to mild steel. In the next part, we’ll discuss safety tips.
Safety Tips
Let’s explore essential precautions for welding stainless to mild steel.
- Eye Protection: Always wear proper goggles or a welding helmet to shield your eyes from sparks. I recommend the Miller Digital Elite. Protecting your eyes from radiation and debris is vital.
- Fume Extraction: Use proper ventilation or fume extractors like the Lincoln Electric 250-CFM cart. This reduces harmful fumes during welding.
- Proper Grounding: Ensure equipment is grounded correctly with a 20’ (6 M) ground cable. This prevents electrical shocks and fire hazards.
- Protective Gear: Wear flame-resistant clothing and gloves. Consider Carolina welding gloves. This offers critical protection against burns and injuries.
Always prioritize safety; it’s a personal responsibility I take seriously.
We’ve wrapped up essential safety tips here. Next up, we’ll look at various welding methods for stainless and mild steel.
Types Of Welding Methods for Stainless and Mild Steel
Let’s discuss different welding methods: MIG, TIG, Stick, Flux-Cored, and Submerged Arc welding.
-
MIG Welding
MIG (Metal Inert Gas) welding is popular for its speed and ease of use. It works well for both stainless and mild steel. This method uses continuous wire from a spool. You can weld stainless to mild steel with MIG by choosing the right gas mix, typically 75% Argon and 25% CO2. It’s crucial to understand the risks of welding without proper safety gear, especially the potential dangers of welding without a mask.
-
TIG Welding
TIG (Tungsten Inert Gas) welding offers more control and is ideal for thin materials. It’s suitable for joining stainless to mild steel, providing greater precision. Use Argon gas for shielding, and be ready to manipulate both the filler rod and torch for a clean bead.
-
Stick Welding
Stick welding is excellent for outdoor projects. It’s versatile and easy to start, allowing you to connect stainless to mild steel. Use a stainless steel electrode and adjust your amperage based on material thickness, typically around 100-130 amps.
-
Flux-cored Arc Welding
Flux-Cored Arc Welding (FCAW) is great for thick metals and outdoor applications. It resembles MIG but uses a tubular wire filled with flux. You can weld stainless to mild steel by selecting the right filler. This method is excellent for structural applications due to its strong, consistent weld.
-
Submerged Arc Welding
This method is ideal for heavy-duty tasks and large production runs. Submerged Arc Welding (SAW) uses granular flux to cover the weld pool, minimizing spatter. It’s less common for stainless to mild steel, as it’s mostly used for thick sections, but can be done with careful setup.
Factors That Affect Welding Stainless to Mild Steel
What factors influence welding stainless and mild steel together?
-
Heat Input
Heat input is critical in welding. Excessive heat can warp the metals; insufficient heat may create a weak bond.
-
Cooling Rate
The cooling rate affects the weld’s integrity. Rapid cooling can cause cracks, especially in stainless steel.
-
Weld Joint Preparation
Prioritize clean edges. Proper preparation minimizes contamination and strengthens the weld.
-
Welding Technique
Your technique is significant. Methods like MIG (Metal Inert Gas) or TIG (Tungsten Inert Gas) affect heat and penetration during the weld.
-
Filler Material Composition
The choice of filler metal is essential. Using compatible materials like ER308L enhances weld strength between stainless and mild steel.
Common Filler Materials for Welding Stainless to Mild Steel
Choosing the right filler material is crucial for achieving a solid weld between stainless steel and mild steel. Here’s a breakdown of some common filler materials suitable for this task.
Filler Material | Type | Properties | Recommended Use |
---|---|---|---|
ER309L | Austenitic | Good corrosion resistance and high strength. Suitable for joining dissimilar metals. | Best for mild to stainless steel welding applications. |
ER308L | Austenitic | Excellent ductility and toughness, ideal for corrosion-resistant applications. | Commonly used for welding stainless steel to mild steel. |
ER316L | Austenitic | Higher resistance to pitting and corrosion due to molybdenum content. | Used where corrosion resistance is critical, like in marine or chemical applications. |
Ni-Rod 55 | Nickel-based | High strength and excellent impact resistance. | Useful in applications exposed to higher temperatures or where strength is a priority. |
ER347 | Austenitic | Stabilized against intergranular corrosion, especially in high-stress applications. | Good for high-temperature applications in industries like aerospace. |
When welding, match the filler to your base materials to enhance the joint’s durability and corrosion resistance. Did you find this helpful for your next welding project?
Typical Problems to Be Aware Of
Here are the unique issues you might face with stainless steel.
-
Cracking Of Welds
Stainless steel can experience hot or cold cracking. Look for visible fissures near the weld. Increase preheat temperatures to 200°F (93°C) for better fusion.
-
Corrosion Issues
Stainless steel isn’t corrosion-proof. Check for dark stains. Use a corrosion inhibitor and ensure proper passivation to protect the surface.
-
Dissimilar Material Strength
Joining stainless steel with other metals may lead to uneven strength. Verify base materials and select compatible filler metals for stability.
-
Inconsistent Weld Quality
Stainless steel can show inconsistent weld beads. Inspect for even width and penetration. Adjust your travel speed and power settings for uniformity.
-
Heat Affected Zone Challenges
Stainless steel often has weakened zones around the weld. Check for discoloration or brittleness. Control heat input and use post-weld treatments.
Aftercare, Inspection, and Advanced Tips for Welding Stainless to Mild Steel
Here’s crucial advice on aftercare, inspection, and tips for successful welding.
Aftercare Tips
After joining stainless and mild steel, clean the weld area promptly. Use a stainless steel brush and a suitable degreaser, like Zep Heavy-Duty Cleaner, for effective residue removal. Check for heat-affected zone (HAZ) discoloration; if present, sand with 220 grit (About 0.1 Mm) to restore the finish. It is important to be aware of potential hazards like weld flash in your welding projects, especially when working with various materials, to ensure safety and quality results. For more information on this topic, explore what weld flash entails.
Inspection
Inspection involves examining the weld for porosity, cracks, or inconsistencies. Use a magnifying glass for surface checks and 4X (Four Times) magnification tools to inspect internal weld defects. I found the Miller XMT 350 very effective at detecting joint fit-up issues.
Expert Tips
Here’s a pro tip: Control heat input precisely; aim for 1 to 1.5 inches (2.5 To 3.8 Cm) per minute to limit distortion. Use 308L filler to maintain corrosion resistance while welding. Keep your electrode angle at 15 degrees to optimize fusion between both metals.
Why This is Worth It: Advantages
The biggest advantage of welding stainless steel to mild steel is versatility. I used it for a custom project where durability was crucial.
This process also offers increased corrosion resistance, cost-effectiveness, strength enhancement, and aesthetic appeal.
Applications Across Different Fields
I’ve known people who use the technique of welding stainless steel to mild steel for various projects. However, it has many unique applications, such as:
- Food Processing Equipment: Stainless and mild steel combinations are popular for fabricating equipment. The stainless part prevents corrosion, while mild steel reduces costs. It’s commonly used in commercial kitchens.
- Exhaust Systems: In automotive applications, welding connects mild steel pipes to stainless steel casings, which helps manage high temperatures efficiently and improves durability.
- Marine Applications: Boats often use mild steel for structural parts and stainless for fittings. This combination fights corrosion in harsh saltwater environments, enhancing longevity and safety.
- Architectural Features: Using stainless trim with mild steel frames creates stylish structural columns that not only look good but also resist rust, making them popular in modern construction.
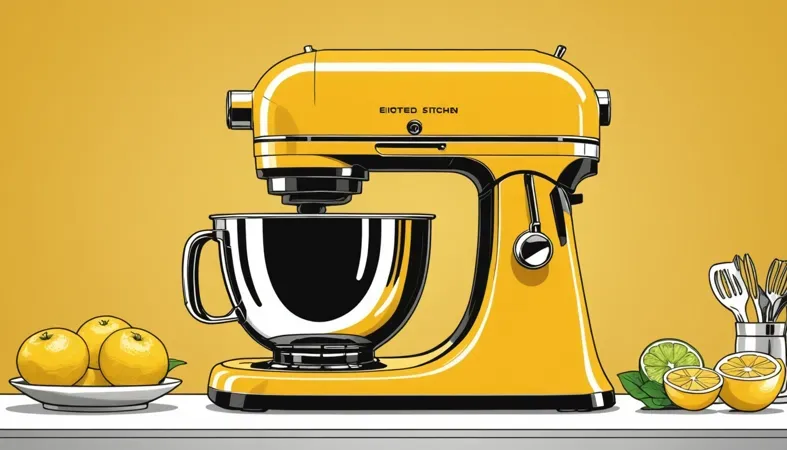
Alternatives for Achieving Results Similar to Welding Stainless to Mild Steel
When you can’t weld these metals together, consider options like brazing or using mechanical fasteners. For example, a high-quality brazing alloy such as AeroSeal can create strong joints without heat distortion. In my professional journey, I’ve found that adhesives, such as Epoxy or Marine Adhesive, work wonders in certain applications, especially in environments where heat might cause warping.
Additionally, using threaded fasteners or clamps is often preferred for their ease and speed. These methods allow you to connect dissimilar metals without the vulnerabilities of welding. If you’re facing specific challenges, these alternatives can save you time and hassle while ensuring a solid connection.
Frequently Asked Questions (FAQs)
Now let us look at some common questions I typically get asked.
What Happens if You Weld Stainless Steel to Mild Steel?
If you weld stainless steel to mild steel, a few issues can arise. The different thermal expansion coefficients can lead to cracking because stainless steel expands more than mild steel. Many welders use a filler that can help bridge the gap between these materials.
What is the Best Way to Weld Mild Steel to Stainless?
The best way to weld mild steel to stainless is through a process like TIG or MIG welding. Using appropriate filler metal helps to minimize corrosion and create a stronger bond. Typically, a filler rod like ER309 is ideal for this task. For projects that require more skill, it’s crucial to understand how to weld uphill.
Can You Weld Stainless Steel and Steel Together?
Yes, you can weld stainless steel and steel together. This requires careful selection of filler material to ensure a solid joint. Good practices include controlling heat input to prevent issues such as warping and cracking.
Can I Weld Stainless Steel With Regular MIG Wire?
No, you can’t effectively weld stainless steel with regular MIG wire. Instead, use stainless-specific MIG wire, like ER308 or ER316, to achieve a proper fusion and maintain corrosion resistance, ensuring the strength and longevity of your weld.
How to Weld Stainless to Mild Steel?
To weld stainless to mild steel, it’s best to use a stainless steel filler material and appropriate techniques. Clean both surfaces thoroughly. A pre-weld treatment like grinding can help optimize adhesion and prevent contaminations.
Conclusion
We are almost done. We covered the types of stainless steel, their weldability, essential prerequisites, safety tips, and steps for welding stainless to mild steel. We also discussed common problems, aftercare, and the advantages of this welding process.
Now, can you weld stainless to mild steel? Simply put, yes, you can, with the right precautions and methods. Using a filler metal designed for both types, like a nickel-based filler, ensures a solid weld that stands up to stress. I hope these welding tips prove valuable to you as you explore your projects.
If you seek further information and guidance, be sure to check out What is Welding for comprehensive insights.
References
- Lincoln Electric. (2020). The Procedure Handbook of Arc Welding (15th ed.). Cleveland, OH: Lincoln Electric Company.
- Cary, H. B., & Helzer, S. C. (2005). Modern Welding Technology (6th ed.). Upper Saddle River, NJ: Pearson.
- American Welding Society (AWS): https://www.aws.org
Joe Carter is a retired welding professional with over 40 years of hands-on experience in the industry, spanning ship repair, structural welding, and even underwater projects. Joe is a master of MIG, TIG, and Stick welding. Passionate about mentoring the next generation of welders, Joe now shares his decades of expertise and practical insights to help others build rewarding careers in welding.
American Welding Society, Filler Material, MIG Welding, Mild Steel, Safety Tips, Stainless Steel, Welding, Welding Applications, Welding Techniques