Can You Weld Black Iron Pipe? | Insights on Welding Techniques and Safety
Published on: November 21, 2024 | Last modified: March 4, 2025
By: Joe Carter
Black iron pipe is a type of steel pipe that’s commonly used in plumbing and heating. It’s called “black” because of the dark iron oxide that forms on it during production.
One question I get asked a lot is can you weld black iron pipe? It’s crucial to know this because it impacts how you’ll connect parts in plumbing and gas lines. In my experience, understanding the weldability of black iron can save time and avoid leaks.
In this guide, we’ll explore black iron pipe properties, its weldability, required preparations, steps for welding, safety precautions, types of welding, factors affecting weldability, common issues during welding, as well as aftercare, inspection, and advanced tips. Plus, we’ll discuss key benefits and applications of black iron pipe, along with alternatives to welding. If you’re wondering can you weld black pipe or how to use it effectively, this article has you covered.
Contents
- Can You Weld Black Iron Pipe?
- What is Black Iron Pipe?
- Types Of Black Iron Pipe and Their Weldability
- Prerequisites
- Precautions
- Steps to Weld Black Iron Pipe
- Types Of Welding for Black Iron Pipe
- Welding Techniques Specific to Black Iron Pipe
- Factors Affecting Weldability Of Black Iron Pipe
- Typical Issues With Black Iron Pipe Welding
- Aftercare, Inspection, and Advanced Tips for Welding Black Iron Pipe
- Key Benefits Of Welding Black Iron Pipe
- Typical Applications Of Black Iron Pipe
- What Are the Alternatives to Welding Black Iron Pipe?
- Frequently Asked Questions (FAQs)
- Conclusion
- References
Can You Weld Black Iron Pipe?
Yes, you can weld black iron pipe. It’s relatively easy if you use the right technique. Stick welding or TIG works best for clean and strong joints. Make sure to clean the surfaces to avoid issues.
What is Black Iron Pipe?
Black iron pipe is a type of pipe made from steel and covered in black oxide scale. It typically measures 1/8 inch (3.2 Mm) to 36 inches (914.4 Mm) in diameter. This pipe is commonly used for gas lines, water supply, and structural applications. With high tensile strength, it can handle pressures up to 2,000 psi (137.9 Bar) in some cases.
Welding black iron pipe is a common question. Many people ask, “Can you weld black iron pipe?” I’ve done it myself, and the process requires specific techniques and care. You need the right welding method to ensure a strong connection, especially with fittings.
I once used black iron pipe for a home project to install a gas line. It performed great! When discussing whether you can weld black iron pipe, I always stress that using the correct approach is essential. Techniques like MIG welding or flux-cored wire can make a big difference in achieving strong joints on fittings.
Types Of Black Iron Pipe and Their Weldability
What types of black iron pipe are there, and how do they hold up to welding?
-
Schedule 40 Black Iron Pipe
Schedule 40 black iron pipe is commonly used for water and gas. You can weld this type by cleaning the surfaces, fitting them tightly, and using a MIG or stick welder with a suitable filler rod or wire.
Mastering upward welding requires precise technique for effective fusion. Discover effective techniques for how to weld uphill for strong welds on vertical joints.
-
Schedule 80 Black Iron Pipe
Schedule 80 black iron pipe has a thicker wall than Schedule 40. Welding is possible with this pipe. Prepare the edges, preheat if necessary, and use a compatible welding rod or wire to ensure a strong joint. For insight into various welding positions, explore the classification of welding techniques.
-
Threaded Black Iron Pipe
Threaded black iron pipe features screwable ends for easy connection. Although it’s not recommended, you can weld this type if needed. Clean the threaded areas thoroughly and use a low-heat setting to avoid damaging the threads.
-
Seamless Black Iron Pipe
Seamless black iron pipe is manufactured without welds, offering strength and durability. Welding is an option here. Ensure the ends are cut cleanly and weld using arc or MIG techniques with proper heat settings.
If you are working with thinner materials, understanding the techniques on how to weld sheet metal can be essential for achieving a strong, durable bond.
-
Welded Black Iron Pipe
This type of pipe is made by welding steel plates together. It’s designed to be welded. Prepare the joints by cleaning the edges, adjust your welder to the right settings, and use an appropriate welding filler.
That covers the types of black iron pipe and their weldability. Let’s now take a look at prerequisites for welding.
Prerequisites
What do you need to get started?
- Welding Machine: You’ll need a MIG welder, like the Lincoln Electric Power MIG 210 MP. It’s essential for achieving proper penetration in black iron pipe.
- Electrode: Use ER70S-6 wire, designed for welding carbon steel, which provides a strong bond for black iron pipe.
- Welding Gas: Use an argon and CO2 mix, such as 75/25. This gas blend stabilizes the arc and reduces spatter.
- Clamps and Fixtures: Heavy-duty clamps, like the Bessey K Body REVO, are crucial for holding pieces in place during welding.
That covers the necessary prerequisites. Let’s now take a look at the essential precautions to keep in mind.
Precautions
Let’s review key safety measures for welding black iron pipe.
- Protective Gear: Always wear flame-resistant gloves and jackets to protect against sparks and burns.
- Ventilation: Ensure good airflow to avoid inhaling harmful fumes. Use local exhaust or large fans to maintain a safe breathing environment.
- Fire Barriers: Place fire-resistant covers or barriers around the work area to reduce fire hazards, especially from flying sparks.
- Electrical Safety: Check all electrical connections for tightness and insulation. Faulty equipment can cause serious injuries or shock.
Always prioritize safety—it’s crucial for enjoyable welding!
We have now covered safety measures and essential precautions. The next section will outline the steps to weld black iron pipe.
Steps to Weld Black Iron Pipe
Now, we’ll cover the steps for welding black iron pipe effectively. It’s essential to follow these closely for successful results.
-
Prepare the Pipe Ends
First, clean the ends of the black iron pipe. Use a wire brush to remove rust and dirt. This ensures a solid connection and minimizes impurities. Aim for a smooth, clean surface free from oils to enhance weld quality.
For those dealing with protective layers on metals, it is important to know whether you can successfully weld zinc plated steel to achieve optimal results in such situations.
If there’s significant corrosion, I usually use a grinder. A clean surface helps the weld penetrate better, strengthening the joint. Remember, proper preparation can save you headaches later.
-
Fit the Pipes Together
Next, align the black iron pipes properly. Ensure the ends match tightly to avoid gaps. Proper alignment is critical for a strong weld. Use clamps to hold them securely; this keeps the pipes stable during the process.
If you’re using fittings, ensure they fit snugly. A tighter fit means less finished weld grinding later. Without proper fittings, the structure may fail at the joints, leading to leaks and cracking.
-
Set the Right Heat Settings
Now, adjust your welding machine. For welding black iron pipe, set your MIG machine to around 20-30 volts and your wire feed speed to about 200-300 inches per minute (5-7.6 Meters Per Minute) to ensure deep penetration.
I recommend starting with low voltage and gradually increasing it as you get used to your setup and the pipe’s thickness. Thicker pipes will require more heat.
-
Weld the Joint
Begin welding by making thorough passes along the joint of the pipes. Hold the welding torch at a 45-degree angle and move it consistently. Aim for a bead height of about 1/8 inch (3 Mm) to ensure sufficient fusion.
As you weld, check the puddle’s shape and monitor for consistent penetration and heat. It’s normal to pause briefly to let the weld pool fill, especially on thicker joints. Keep it steady and don’t rush—it’s about helping the metal fuse properly.
-
Clean Up the Weld
Finally, allow the weld to cool completely before cleaning. Use a wire brush or grinder to smooth rough edges and remove slag if you’re using flux-cored wire. Cleaning highlights your work and reveals imperfections.
Inspect your weld closely after cleaning. Hold it up to the light; a good weld should shine without gaps or air pockets. Remember, tidying up enhances both the appearance and integrity of your work—a win-win!
That covers the steps to weld black iron pipe. Let’s now take a look at the types of welding for black iron pipe.
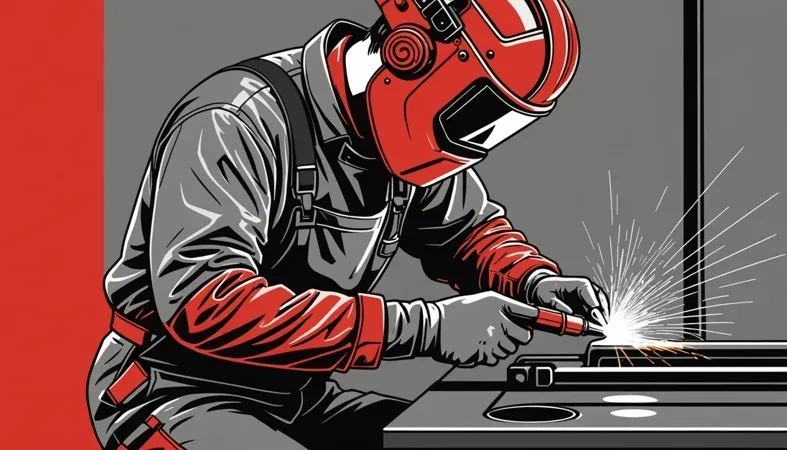
Types Of Welding for Black Iron Pipe
Let’s move on to the different welding methods you can use: MIG, TIG, Stick, Flux-Cored, and Oxy-Acetylene welding.
-
MIG Welding
MIG (Metal Inert Gas) welding is a popular method for joining black iron pipe. It’s fast and requires minimal skill. You can easily weld thicknesses up to about 1/2 inch (12.7 Mm).
-
TIG Welding
TIG (Tungsten Inert Gas) welding allows you to make precise, clean welds. It works well for black iron pipe, especially for thinner sections. For those interested in honing their skills, understanding steel welding techniques can enhance performance, as it takes longer and requires more skill than MIG.
One important aspect to consider for welders is the inherent risks associated with their craft. For more details on the potential dangers involved in this trade, you can explore how dangerous welding is.
-
Stick Welding
Stick welding, or Shielded Metal Arc Welding (SMAW), is versatile for black iron pipe. It works in various positions and outdoors. It can efficiently weld thicker pipes, usually up to about 1 inch (25.4 Mm) or more. Proper technique can reduce common issues such as weld spatter, which involves understanding what causes weld spatter.
-
Flux-cored Welding
Flux-Cored welding is similar to MIG but uses a tubular wire filled with flux. It’s great for outdoor work on black iron pipe since it’s less sensitive to wind. I prefer this method for larger projects due to its deep penetration, which ensures strong joints.
-
Oxy-acetylene Welding
Oxy-Acetylene welding uses a flame to weld or cut metals. It’s suitable for black iron pipe, providing the heat and control needed for various tasks. However, it’s less common today due to alternative methods.
Welding Techniques Specific to Black Iron Pipe
When welding black iron pipe, it’s essential to grasp the specific techniques that best suit this material.
Welding Technique | Suitability | Common Use Cases | Pros | Cons |
---|---|---|---|---|
MIG Welding | Best for thin to medium black iron pipe | Household plumbing, HVAC | Fast and minimal cleanup | Less effective on thicker pipes |
TIG Welding | Great for thin material | High precision work, artistic projects | Clean welds, strong joints | Slower and requires more skill |
Stick Welding | Good for thick pipelines | Outdoor welding, structural applications | Versatile and portable | More spatter and cleanup needed |
Flux-Cored Arc Welding | Effective for outdoor use | Larger projects, industrial setups | Deep penetration | More fumes and requires ventilation |
Oxy-Acetylene Welding | Useful for cutting and repair | Heavy-duty tasks and fabrication | Flexibility in heat control | Less common for routine welding |
Each method has its strengths and weaknesses, making it crucial to choose one based on your project needs. Understanding these techniques will help you achieve stronger, neater welds.
Factors Affecting Weldability Of Black Iron Pipe
What factors influence the ability to weld this type of pipe?
-
Pipe Thickness
Thicker black iron pipes (Over 0.25 Inches or 6.35 Mm) require more heat input. This increases the risk of warping and can lead to issues with weld penetration.
-
Welding Process
The choice of welding method, like MIG or stick welding, greatly impacts quality. MIG welding often delivers smoother welds, while stick welding may struggle with rustier pipes.
-
Surface Cleanliness
It’s important to clean the surface of black iron pipes thoroughly. Dirt, rust, or oil can hinder weld quality and compromise joint strength. A clean surface ensures proper fusion.
-
Welding Environment
Wind or drafts can cool the weld too quickly, leading to cracks. Welding indoors or in a sheltered area provides better control over weld quality.
-
Heat Input
Maintaining proper heat is crucial. Excessive heat may weaken the metal, while too little can result in poor penetration. Monitor temperatures with a proper gauge.
Typical Issues With Black Iron Pipe Welding
Let’s look at issues related to welding black iron pipe.
-
Corrosion Resistance Problems
Black iron pipe has low corrosion resistance and rusts easily. To resolve this, apply a protective coating or paint to guard against moisture.
-
Heat-affected Zone Hardening
Welding black iron pipe can overheat and harden the heat-affected zone. I recommend controlling heat input and using cooler settings for better flexibility.
-
Poor Weld Joint Fit-up
Black iron pipe requires a tight fit for a solid joint. Gaps can create weak welds. Clean edges and align the pipes properly.
-
Faulty Weld Penetration
Inadequate penetration can occur with black iron pipe. Inspect weld seams closely and adjust speed and amperage to ensure full penetration.
-
Warping and Distortion
Welding black iron pipe may cause warping from heat. Check for deformation as you weld. Use stitch welding or cooldown cycles to minimize this issue.
Aftercare, Inspection, and Advanced Tips for Welding Black Iron Pipe
Here’s essential guidance on post-weld care, inspection, and tips for black iron pipe.
Aftercare Tips
After welding black iron pipe, cool it gradually. Rapid cooling can cause cracking. Use a wire brush rated for up to 500°F (260°C) to remove slag and rust.
Inspection Strategies
Inspect joints for signs of porosity or cracks using a magnifying glass. Fogging parts together may reveal hidden voids. I often use NDT (Nondestructive Testing) products like Magnaflux for thorough inspections.
Advanced Expert Tips
If you’re experienced in welding black iron, adjust your heat settings. Preheat to 200°F (93°C) for pipes thicker than 0.5 inches (12.7 Mm). Always use 7018 (Low-hydrogen Electric Arc Welding Rod) for better tensile strength in critical joints.
Key Benefits Of Welding Black Iron Pipe
The main advantage of welding black iron pipe is its strength. I relied on it for a heavy-duty gas line where durability was essential.
It’s also cost-effective, versatile, and resistant to corrosion, making it suitable for various applications. It can withstand high-pressure situations, and the welds are easy to inspect, ensuring a secure connection.
Typical Applications Of Black Iron Pipe
Many welders use black iron pipe for various tasks. It has several applications, including:
- Gas Distribution: Black iron pipes are commonly used for natural gas and propane lines. Their sturdy construction can handle high pressure, ensuring safety and longevity.
- Fire Protection Systems: These pipes are crucial in sprinkler systems. Their ability to withstand high temperatures makes them a popular choice for fire suppression.
- Industrial Piping: Manufacturing facilities often use black iron to transport water, steam, and various fluids due to its durability and corrosion resistance.
- HVAC Systems: Black iron pipes connect steam and chilled water systems, proving effective in heating and cooling applications thanks to their strength and high-temperature tolerance.
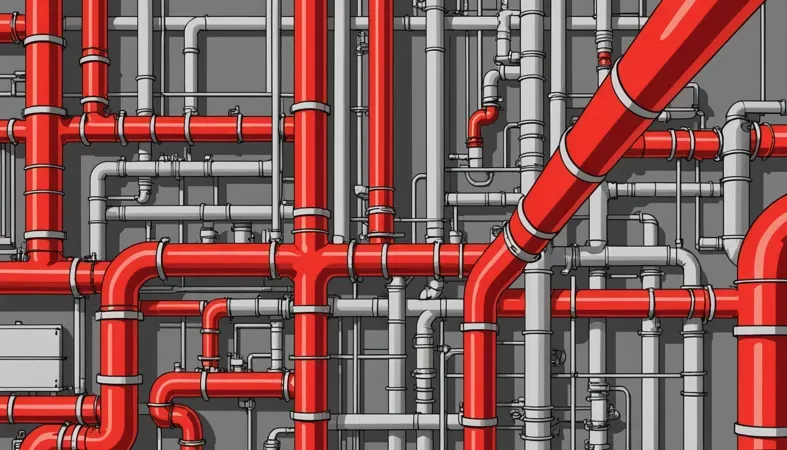
What Are the Alternatives to Welding Black Iron Pipe?
There are alternatives to joining black iron pipe that can achieve similar results. For instance, you can use mechanical fittings such as Victaulic couplings or PVC cement for certain applications. These methods might be preferred in residential settings or where leakage risks are high, as they’re easier and require less specialized skills.
Another option is using threadable pipes and fittings, which allow you to screw pieces together without welding. This method often simplifies repairs or adjustments, making it a go-to solution for many DIY projects. Whether it’s black pipe or galvanized options, these techniques can be both effective and user-friendly.
Frequently Asked Questions (FAQs)
Now let us look at some common questions. I typically get asked about welding black iron and similar pipes.
Is Schedule 40 Black Pipe Weldable?
Yes, schedule 40 black pipe is weldable. Made from carbon steel with a thickness of 0.365 inches (9.27 Mm), it suits various welding methods, like MIG and TIG, due to its excellent strength. Schedule 40 is widely used in many applications, making it a reliable choice for piping.
What Welding Rod for Black Iron Pipe?
For black iron pipe, use an E6010 or E7018 welding rod. The E6010 rod provides deep penetration, while the E7018 offers a smoother weld. These options ensure strong joints and reliable connections, especially in pressure applications.
Is Black Iron Pipe the Same As Black Steel Pipe?
No, black iron pipe is not the same as black steel pipe. Black iron pipe is typically used for gas and water systems, while black steel pipe is used in piping systems requiring higher strength. Largely, both share similar properties due to their steel composition.
Can You Weld Black Stove Pipe?
No, you shouldn’t weld black stove pipe. It’s made from thin carbon steel and often coated with a heat-resistant paint. Welding can create weak spots and lead to dangerous emissions, undermining its main purpose of venting smoke and gases.
Can You Weld Black Oxide Steel?
Yes, you can weld black oxide steel. However, proper preparation is key. The black oxide coating can introduce impurities that affect the integrity of the weld, so clean the surface before starting. You’ll get a better bond and stronger welds this way.
Conclusion
We’ve made it to the end, and I hope it was helpful. We covered what black iron pipe is, its types and weldability, prerequisites for welding, steps to take, precautions, types of welding methods, factors affecting weldability, typical issues, aftercare, inspection tips, key benefits, and applications, along with alternatives. Understanding these aspects can really enhance your skills in welding black iron pipes.
So, can you weld black iron pipe? Yes, you can, and it’s quite straightforward if you follow the right steps. I packed the article with details on factors like types of welding, precautions, and common issues; these insights will guide you. Wishing you success in your welding projects, and don’t forget to choose the right method, whether it’s MIG welding or using flux core!
For further insights and tips on welding techniques and best practices, feel free to visit What is Welding.
References
- American Welding Society. (2015). AWS D1.1/D1.1M: Structural Welding Code – Steel. Miami, FL: AWS.
- Richardson, R. (2010). MIG Welding Guide. Cambridge, UK: Woodhead Publishing.
Joe Carter is a retired welding professional with over 40 years of hands-on experience in the industry, spanning ship repair, structural welding, and even underwater projects. Joe is a master of MIG, TIG, and Stick welding. Passionate about mentoring the next generation of welders, Joe now shares his decades of expertise and practical insights to help others build rewarding careers in welding.
American Welding Society, Black Iron Pipe, Electrical Safety, MIG Welding, Pipe Fittings, Plumbing Techniques, Safety Precautions, Welding, Welding Techniques