What Are Welding Cables Made Of? | Composition, Types, Uses
Published on: May 9, 2025 | Last modified: March 4, 2025
By: Joe Carter
CABLES are important components in electrical systems. They transmit power or signals between devices.
People often ask us, what are welding cables made of? Knowing the materials is crucial because it affects the cable’s efficiency and safety. In my experience, using the right type can prevent overheating, ensuring a longer lifespan.
In this guide, you’re gonna learn about what welding cables are made of, how they’re manufactured, the different types available, steps to determine their composition, factors that influence their makeup, and a section addressing frequently asked questions. Also, I’ll touch on whether you can use welding cable for battery cable applications or even house wiring!
Contents
What Are Welding Cables Made Of?
Welding cables consist of flexible copper or aluminum conductors, often insulated with rubber or thermoplastic. They’re durable and resist heat, making them ideal for welding tasks. You’ll spot them in industrial settings and automotive repairs.
When working with welders, it is important to comprehend the power consumption involved in operating these machines, as this insight enhances work efficiency and safety. For a clear understanding, explore how many watts a welder uses.
How Are Welding Cables Made?
Welding cables are made of high-strand copper or aluminum wire. They’re designed to carry high currents—up to 200 amps or more—depending on the cable size. For instance, a 1/0 AWG (American Wire Gauge) cable can handle around 150 amps safely. These cables are also insulated with durable materials, often rubber or PVC, to resist heat and abrasion.
These features provide welding cables with reliability. Their flexibility allows easy maneuvering during welding tasks. Additionally, the insulation prevents electrical shock and short circuits, which is crucial in high electrical load environments.
I recommend using high-strand copper welding cables for better conductivity. If you’re considering them for battery cables, be cautious as higher gauge numbers may not handle the load properly. It’s also important to ask, “Can I use welding cable for battery cable?” Check compatibility for safe use.
Types Of Welding Cables
What types of welding cables are available?
-
Battery Welding Cables
Battery welding cables are designed for high amp (Ampere) applications. They’re typically made of copper for excellent conductivity. Manufacturers combine multiple strands of copper wires inside a jacket for flexibility and durability. Understanding the cost of essential components like welding rods can help optimize your welding setup; find out more about the price of welding rods.
-
Thermoplastic Welding Cables
Thermoplastic welding cables are flexible and resistant to various chemicals. They consist of copper conductors covered with thermoplastic polymer insulation. The copper is drawn into fine wires and coated with heat-resistant thermoplastic for protection. For those needing to connect thermocouples efficiently, understanding how to weld thermocouple wire can be crucial.
-
Rubber Welding Cables
Rubber welding cables offer excellent flexibility and heat resistance. They’re made of stranded copper with rubber insulation that withstands extreme conditions. Manufacturers heat the copper and wrap it with rubber to ensure it can handle tough environments.
-
Silicone Welding Cables
Silicone welding cables are known for their high-temperature resistance. They feature a core of copper wires and an outer layer of silicone rubber. The copper is twisted together and coated with silicone, providing flexibility even in high heat.
Understanding the role of gases in welding processes can significantly enhance the quality of the weld, and using specialized gas mixtures like tri-mix offers specific advantages in certain applications. Learn more about the uses of tri-mix welding gas.
-
Inflatable Welding Cables
Inflatable welding cables are designed for specific welding operations. These cables use specialized insulated copper strands that can inflate or deflate. Builders string copper wires and encase them in an inflatable sheath for adaptability.
So far we covered the different kinds of welding cables. Let’s look at how to determine welding cable composition next.
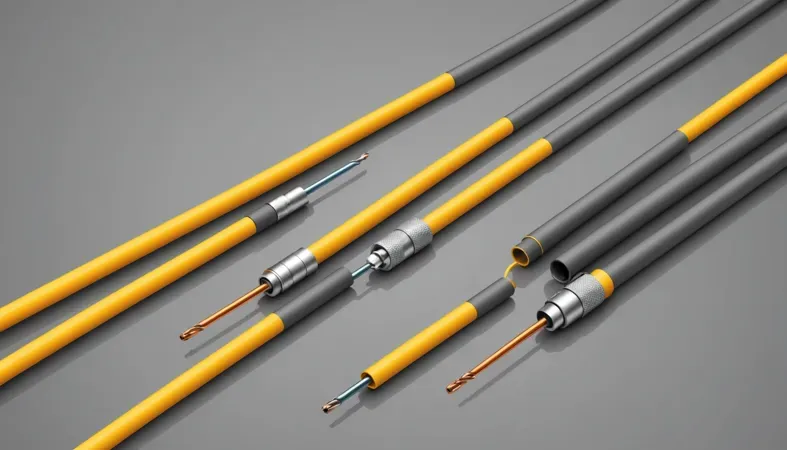
Steps to Determine Welding Cable Composition
Here are the steps to identify the materials in welding cables.
-
Identify the Conductor Material
Welding cables use either copper or aluminum as the conductor. Copper, with 97% IACS (International Annealed Copper Standard) conductivity, is the most common choice due to its efficiency and flexibility. Aluminum is lighter and generally less expensive, but it has about 61% IACS conductivity. Choose the right material based on your needs for optimal performance. When encountering technical issues with your equipment, it’s crucial to understand how to fix a welding machine to ensure continued efficiency and safety.
If you need flexibility, select copper. It’s more robust for high-amperage scenarios, such as a 200 amp (A) application. For mobile setups, aluminum may be better due to its lighter weight, although installation can be more cumbersome.
-
Assess the Insulation Type
Next, examine the insulation material, which is crucial for safety. Most welding cables use thermoplastic elastomer (TPE) or polyvinyl chloride (PVC). TPE offers excellent flexibility and heat resistance, with a temperature range of -50°C to 90°C (-58°F to 194°F). PVC is less flexible but more durable. Understanding the impact of dross formation in welding processes is also important. Learn more about the issues related to dross in your welding projects.
For frequent movement, I recommend TPE insulation to prevent cracking. The choice of insulation significantly affects performance, especially in high-temperature environments.
-
Examine Cable Size
Cable size is critical for current capacity. Welding cables typically range from 6 AWG (American Wire Gauge) to 2/0 AWG. The cable size affects its amperage capacity; for example, a 2/0 AWG cable can handle around 200 A. Check the welding cable size chart to select the appropriate size for your application. For further understanding of specialized techniques, explore the principles of orbital welding processes.
If you’re using your cable for high-demand applications, choose a larger size to enhance system longevity and efficiency, which helps prevent overheating and electrical failure.
-
Check the Jacket Material
Finally, assess the outer jacket. Common materials include rubber and PVC, which protect against environmental factors. Rubber is usually more abrasion-resistant, while PVC provides better chemical resistance. Both offer sufficient protection, but rubber excels in flexibility and durability under harsh conditions.
Choosing the right jacket is important. If your work environment has chemicals or extreme weather, use PVC for chemical resistance and rubber for rugged conditions to avoid future issues.
We covered how to determine welding cable composition. We will now cover the factors that influence welding cable composition.
Factors Affecting Welding Cable Composition
What factors influence the materials used in welding cables? Here’s a closer look.
-
Material Conductivity
The conductivity of welding cable materials directly impacts performance. Copper has an electrical conductivity of 58 MS/m, ensuring efficient energy transfer, while aluminum, often a cheaper alternative, offers about 37 MS/m.
-
Insulation Type
Insulation types determine the cable’s resistance to heat and electrical leakage. Common insulation materials include rubber and PVC, each with different temperature ratings; for instance, rubber can withstand up to 90°C (194°F) while PVC can only handle up to 60°C (140°F).
-
Heat Resistance
Heat resistance affects the cable’s durability during operation. It’s best to use high-heat rated cables for industrial applications to avoid degradation. Cables rated for at least 90°C (194°F) can handle higher temperatures without melting or warping.
-
Flexibility and Maneuverability
Flexibility is crucial, especially in tight spaces. Cables made with finer wires are more flexible, making them easier to maneuver during welding tasks.
-
Environmental Conditions
Cables exposed to harsh environments need robust insulation. Factors like moisture, chemicals, and UV exposure can deteriorate cables, so choosing the right type is essential for longevity.
We’ve wrapped up the factors influencing welding cable composition. Let us turn our attention to maintaining and caring for welding cables.
Maintenance and Care of Welding Cables
Keeping your welding cables in top shape ensures they’re ready when you need them. Here are some essential maintenance tips.
-
Regular Inspection
Inspect your cables for any signs of damage. Look for frayed wires, cuts, or exposed copper. Regular checks, maybe once a month, can help catch issues early.
-
Cleaning
Dust and grime can accumulate on cables, affecting performance. Wipe down your cables with a damp cloth. Avoid abrasive cleaners that can damage insulation.
-
Proper Storage
When not in use, store cables properly. Coil them without kinks or twists to avoid damaging the wires. A cable reel works great for this.
-
Check Connections
Ensure the connections at both ends are secure and free from corrosion. Corroded connectors can lead to resistance, causing overheating.
-
Temperature Awareness
Be aware of the temperature during use. High temperatures can weaken insulation. If you’re in a hot work environment, monitor cable performance closely.
Table of Common Welding Cable Maintenance Practices
Maintenance Task | Frequency | Notes |
---|---|---|
Inspect for Damage | Monthly | Catch issues early to avoid failures. |
Cleaning | As Needed | Use a damp cloth, avoid harsh chemicals. |
Check Connections | Weekly | Ensure tight and clean connections. |
Proper Storage | After Use | Store coiled correctly to prevent damage. |
Temperature Monitoring | During Use | Watch for overheating to ensure safety. |
We covered the maintenance and care of welding cables. We will now cover frequently asked questions about welding.
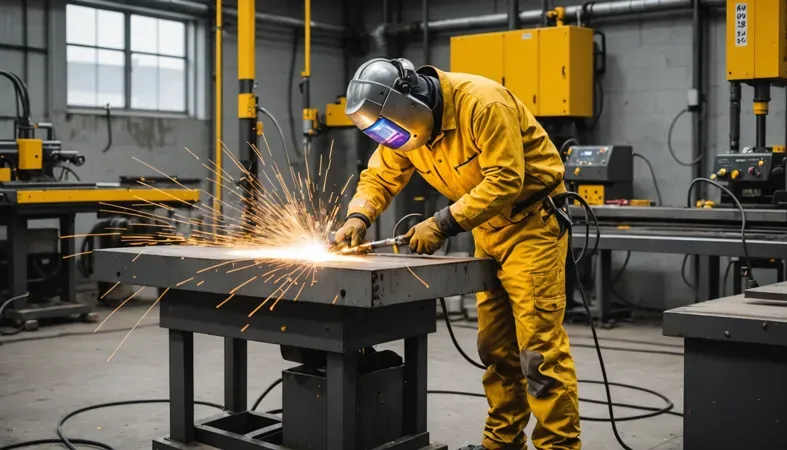
Frequently Asked Questions (FAQs)
Now let us look at some common questions I typically get asked related to welding cables.
Can You Use Welding Cable for Car Audio?
Yes, you can use welding cable for car audio. Welding cable has a high-current capacity, with a rating of up to 600 amps depending on the gauge, making it suitable for handling the power demands of car amplifiers. Additionally, its flexibility ensures easier installation in tight spaces.
Can I Use Welding Cable for Battery Cable?
Yes, you can use welding cable for battery cable. Welding cable conducts electricity efficiently, with low resistance per foot, which is ideal for connecting batteries to various systems. However, ensure it meets the required gauge to handle the battery’s output specifications.
Can Welding Cable Be Used for House Wiring?
No, welding cable shouldn’t be used for house wiring. While it’s flexible and carries high current, it’s not rated for permanent installations in residential buildings. Standard building wire like THHN is better suited as it meets electrical code requirements.
What Type Of Wire is Welding Cable?
Welding cable is often made with stranded copper wire. Stranded wiring allows for greater flexibility, which is necessary in welding applications. Welding cable typically has a rubber or PVC insulation, providing excellent durability in harsh conditions.
What is Welding Cable Used for?
Welding cable is used primarily for connecting welding machines to the workpiece. It’s designed to carry high amperage, usually between 150 to 600 amps, depending on wire gauge, making it particularly efficient for welding processes like MIG and TIG.
Does Welding Wire Have Copper?
Yes, welding wire does contain copper. Most welding wires use copper-coated steel or pure copper to improve conductivity, vital for effective welding. The copper content ensures minimal voltage drop during the welding process, enhancing overall performance.
Conclusion
We’ve gone through a lot, thank you for sticking it out. We covered various aspects of welding cables like their composition, manufacturing methods, different types, key factors affecting their make, and even provided some insights into welding fundamentals. This information should give you a solid understanding of what makes up welding cables.
To explore the factors that determine the strength of a weld, delve into the technical aspects that ensure reliability and durability.
To wrap up, what are welding cables made of? In simple terms, they’re usually constructed from copper or aluminum, with rubber or other flexible insulation. You learned how these materials affect performance and durability, and whether you can use welding cable for other applications like battery cables or house wiring.
If you’re eager to expand your knowledge further into the world of welding, visit What is Welding for more insights.
Additional Reading
- Lincoln Electric. (2020). The Procedure Handbook of Arc Welding (15th ed.). Cleveland, OH: Lincoln Electric Company.
- Norrish, J. (2006). Advanced Welding Processes. Boca Raton, FL: CRC Press.
Joe Carter is a retired welding professional with over 40 years of hands-on experience in the industry, spanning ship repair, structural welding, and even underwater projects. Joe is a master of MIG, TIG, and Stick welding. Passionate about mentoring the next generation of welders, Joe now shares his decades of expertise and practical insights to help others build rewarding careers in welding.
Cable Composition, Cable Types, Electrical Safety, Maintenance Tips, Voltage Drop, Welding, Welding Applications, Welding Cables, Welding Materials, Welding Wire, Wire Gauge