What Gas Do You Use to Weld Aluminum? Gas Types, Weldability, and Tips
Published on: November 21, 2024 | Last modified: March 4, 2025
By: Joe Carter
Aluminum is a lightweight metal that’s strong, durable, and used in many industries. You’ll find it in everything from cars to airplanes to cans.
It’s a question I’m often asked: what gas do you use to weld aluminum? Choosing the right gas is super important for a good weld. From my experience, using the wrong gas can lead to weak joints and defects.
In this guide, I’ll cover important topics like types of aluminum and their weldability, steps to weld aluminum, factors influencing gas selection, and frequently asked questions. You’ll learn everything you need about what gas is used to weld aluminum, what gas to use for welding aluminum, and much more!
Contents
What Gas Do You Use to Weld Aluminum?
Welders typically use argon for aluminum. This inert gas prevents oxidation, ensuring a clean weld. It’s ideal for projects like automotive parts or aircraft components, where precision and strength are crucial.
Why Gas Used to Weld Aluminum?
When welding aluminum, the preferred gas is argon’s properties. Argon is an inert gas that prevents oxidation and protects the weld area. This results in cleaner welds with fewer defects, improving strength and appearance. Using argon can increase weld integrity by up to 40% compared to using no gas.
Many professionals recommend a pure argon setup. However, you can also mix argon with 5% helium for added heat input in certain applications. This is particularly helpful when working with thicker aluminum sections.
The right gas is crucial when welding aluminum. Poor gas choices can lead to cracks and weak joints. Using argon not only improves the weld’s appearance but also enhances performance and longevity!
Types Of Aluminum and Their Weldability
So, what types can you use for welding?
-
2011 Aluminum
This alloy is known for its excellent machinability. When welding 2011 aluminum, use pure argon gas. Set the gas flow rate to about 15-20 cubic feet per hour (Cfh) for a clean, stable arc. Adjust as needed for wind or drafts. Selecting the appropriate welding rod can enhance weld quality significantly, and it’s essential to know what welding rod to use for achieving the best results.
-
6061 Aluminum
6061 is versatile and commonly used in structural applications. For welding, 100% argon gas works best. Maintain a flow rate of 15-25 cfh to ensure proper shielding and avoid contamination.
-
6063 Aluminum
This alloy is often used in architectural applications due to its finish and formability. Argon gas is ideal for welding. Set a flow rate of around 10-20 cfh to protect the molten weld while keeping the area ventilated. Choosing the right welding equipment is crucial for beginners seeking smooth and precise operations, making it important to identify good welders for beginners.
-
7075 Aluminum
7075 is a high-strength material popular in aerospace applications. For welding, a mix of argon and helium works well. Use about a 25% helium blend at 15-25 cfh for optimal penetration and heat, ensuring effective shielding.
-
5052 Aluminum
Known for its corrosion resistance and weldability, 5052 aluminum is commonly used in marine applications. Argon gas is recommended for welding this type. Set your gas flow rate to 15-20 cfh and inspect the puddle for quality.
We have now covered the various types of aluminum and their weldability. Next, we will discuss the steps for welding aluminum.
Steps to Weld Aluminum
Now, we’ll cover steps for choosing the right gas in aluminum welding.
-
Prepare the Aluminum Surface
Start by cleaning the aluminum thoroughly. Use a wire brush, grinder, or chemical cleaner to remove old paint or oxidation. This ensures better weld penetration. Remember, aluminum oxide melts at a higher temperature than the aluminum base metal. A shiny surface aids in the process.
For welders curious about undergoing MRI procedures with their profession’s potential impacts in mind, understanding the safety considerations of a welder getting an MRI is crucial.
.
I recommend using a stainless-steel wire brush specifically for aluminum. I can’t stress enough how important this prep step is for avoiding weld defects. Ensure the surface is dry before moving to the next step to prevent contamination during welding. When dealing with different types of welding equipment, it is essential to know how to hook up a Miller suitcase welder for seamless operations.
-
Select the Appropriate Gas
For aluminum welding, the most common gas is argon. It offers excellent arc stability and reduces spatter. A mixture of helium and argon can also be suitable, especially for thicker materials, as it increases heat input. You can mix argon and helium in a ratio ranging from 75/25 to 50/50, depending on the thickness. Understanding the different types of welding gas can also help ensure optimal results in your projects.
A crucial aspect of multi-pass welding is executing a proper hot pass to ensure strong bonding and remove any trapped slag in the weld, which highlights what a hot pass in welding entails.
When selecting gas, react based on the application. For general welding, pure argon is preferred, while thicker sections benefit from the added heat of the helium blend. Always check your welding machine’s specifications to ensure it’s compatible with your gas choice.
-
Set Up the Welding Equipment
Next, set your machine for aluminum welding. Ensure your TIG torch or MIG gun is fitted properly with the correct electrode and nozzle size. For TIG, a 1.6 mm (1/16 Inch) diameter tungsten typically works well for most thin aluminum. For MIG, a larger wire diameter, like 0.8 mm (0.030 Inch), suffices for thin materials. Understanding how arc control affects MIG welding performance is crucial, as it can significantly impact the quality and precision of your welds by managing the stability and penetration of the arc during the welding process.
Ensure your regulators are adjusted for the right gas flow—typically around 15 to 25 cubic feet per hour (CFH). I can’t stress how critical it is to maintain adequate flow; insufficient gas coverage leads to oxidation and poor weld quality.
-
Adjust the Welding Parameters
Adjust your voltage and amperage based on aluminum thickness. A good starting point for TIG welding is 1 amp per 0.001 inch (0.025 Mm) of thickness. If using MIG, set the voltage according to the manufacturer’s guidelines and fine-tune it based on your machine’s output.
Get familiar with how your machine behaves at different settings. Too little power causes weak welds, while too much can burn through the material. I highly recommend running a few test beads to fine-tune your parameters before tackling your main project.
-
Begin the Welding Process
Start the welding process, maintaining a steady travel speed. For TIG welding, hold the torch about 3 mm (1/8 Inch) from the workpiece. Move consistently to avoid burn-through, especially in thinner aluminum. For MIG, the arc should be short, ideally about 6 mm (1/4 Inch). Investing in reliable welding machines can ensure better performance and precise results; explore more about the cost of welding machines.
Pay attention to the puddle; it should appear fluid. If you see excessive spatter, adjust your gas or pacing. Practice makes perfect—if the weld isn’t coming out right, feel free to adjust your speed, angle, or pause to let the material cool.
So far we covered the process of welding aluminum. Let’s look at the factors that affect gas selection for aluminum welding next.
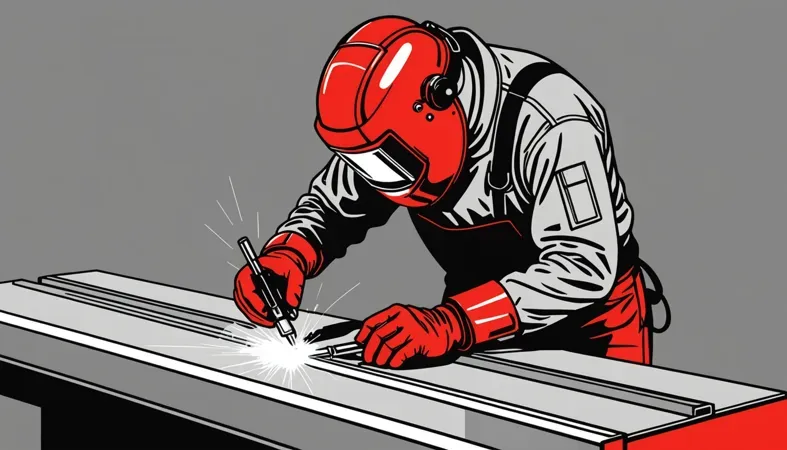
Factors Influencing Gas Selection for Welding Aluminum
What factors influence gas choices for aluminum welding?
-
Type Of Aluminum Alloy
The aluminum alloy’s grade affects your gas choice. Alloys like 6061 or 4047 may require different gases for optimal results.
-
Welding Process Used
The welding process—like MIG or TIG—determines the gas type. TIG generally uses pure argon (100%), while MIG may use a mix of argon and helium.
-
Thickness Of Material
The material’s thickness impacts your gas choice. Thicker aluminum (Over 3/16 Inch or 4.76 Mm) often needs helium mixed with argon for better penetration.
-
Environmental Conditions
Wind or temperature can disrupt the shielding gas’s effectiveness. In windy conditions, use a gas that offers better coverage and stability.
-
Welding Position
Flat or vertical positions may influence gas flow and effectiveness. Optimize gas usage based on the welding angle to ensure proper shielding.
We covered the factors affecting gas choice for aluminum welding. We will now cover selecting gas for various welding methods.
Choosing Gas for Different Welding Techniques
It’s essential to select the right gas not only for the material but also for the welding technique you’re using. Here’s how different methods impact the gas choice:
Welding Technique | Recommended Gas | Gas Benefits | Typical Flow Rate (CFH) |
---|---|---|---|
TIG Welding | 100% Argon | Stable arc, minimal contamination | 15-25 |
MIG Welding | Argon/Helium Mix (75/25) | Better heat transfer, high penetration | 20-30 |
Spool Gun Welding | 100% Argon | Effective shielding for strong welds | 15-25 |
Resistance Welding | No gas needed | Direct metal-to-metal contact | N/A |
By understanding the connection between gas types and welding methods, you’ll improve your welding efficiency. Selecting the right gas can make the difference between a flawless weld and a failed project. If you want to deepen your knowledge, consider learning about various welding processes that can enhance your skills. So, keep these tips in mind when setting up!
We’ve wrapped up selecting gas for various welding techniques here. Let us turn our attention to common questions and answers.
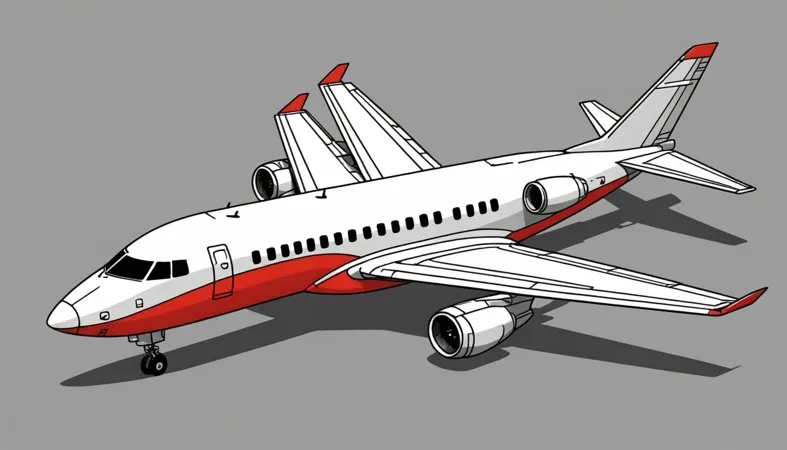
Use argon gas for optimal aluminum welding results.
Frequently Asked Questions (FAQs)
Now let us look at some common questions I typically get asked.
What is the Best Gas for Welding Aluminum?
Yes, argon (Ar) is the best gas for welding aluminum. Argon creates a stable arc and reduces oxidation, which is crucial when welding light metals like aluminum. In fact, using pure argon can enhance weld appearance by up to 30%.
What Gas Do You Use to Weld Aluminum With a Spool Gun?
You use argon gas when welding aluminum with a spool gun. This gas provides excellent shielding, helping to produce strong, clean welds. Additionally, argon’s lower welding costs can save you up to 20% per job compared to other gases.
Is Helium or Argon Better for Aluminum Welding?
Argon is generally better for aluminum welding, though helium has its benefits too. Argon is cheaper and offers more stability, while helium can help with heat transfer in thick aluminum, improving penetration by 15% in select applications.
Can I Use a MIG Welder for Aluminum?
Yes, you can use a MIG welder for aluminum welding. MIG welding is faster and more efficient, making it well-suited for aluminum thicknesses ranging from 1.6 mm to 10 mm (1/16 Inch to 3/8 Inch).
How Thick Can You Weld Aluminum?
You can weld aluminum up to 10 mm (About 0.4 Inches) thick effectively. Beyond this, preheating and advanced techniques may be necessary for optimal results. Always consider the right filler material to match the thickness for a strong weld.
Conclusion
We covered several key points about gas for aluminum welding. We discussed what gas is used, types of aluminum and their weldability, steps to weld aluminum, and factors influencing gas selection. We also tackled common questions in the FAQ section.
So, what gas do you use to weld aluminum? In short, pure argon is your best bet. It provides a stable arc and helps prevent contamination, especially when welding thin aluminum sections. Remember, using argon keeps your welds clean at pressure levels around 70-80 kPa (10-12 Psi) for optimal performance.
For further exploration of welding techniques and tips, be sure to visit What is Welding for comprehensive guides and tutorials.
References
- Occupational Safety and Health Administration (OSHA): Welding, Cutting, and Brazing: https://www.osha.gov/welding-cutting-brazing
Joe Carter is a retired welding professional with over 40 years of hands-on experience in the industry, spanning ship repair, structural welding, and even underwater projects. Joe is a master of MIG, TIG, and Stick welding. Passionate about mentoring the next generation of welders, Joe now shares his decades of expertise and practical insights to help others build rewarding careers in welding.
Aluminum, Argon Gas, MIG Welding, TIG Welding, Welding, Welding Equipment, Welding Techniques, Wire Diameter