How to TIG Weld Stainless Steel? Techniques, Tools, and Tips
Published on: December 30, 2024 | Last modified: March 4, 2025
By: Joe Carter
TIG stands for Tungsten Inert Gas. It’s a precise welding process that uses a non-consumable tungsten electrode to create an arc and melt the base metals.
I’m often asked about how to tig weld stainless steel, and it’s a crucial skill. Welding stainless steel requires attention to detail because it ensures strong, clean joints. In my experience, following proper techniques can mean the difference between a solid weld and a weak one.
In this article, I’ll cover the types of TIG for welding stainless steel, what you need to get started, key steps, important precautions, different welding techniques, factors affecting the process, common issues, aftercare tips, benefits, applications, and possible alternatives. I want you to walk away with a better understanding of how to weld tig stainless steel with confidence.
Contents
- How to Tig Weld Stainless Steel?
- What is TIG?
- Types Of TIG for Welding Stainless Steel
- Prerequisites: What Do You Need?
- Steps for How to TIG Weld Stainless Steel
- Precautions
- Types Of Welding Techniques for Stainless Steel
- Factors Affecting TIG Welding Of Stainless Steel
- Common Issues in TIG Welding Of Stainless Steel
- Aftercare, Inspection, and Advanced Tips for TIG Welding Stainless Steel
- Common Alloys Used in TIG Welding Stainless Steel
- Benefits Of TIG Welding Stainless Steel
- Applications You Should Know About for TIG Welding
- Alternatives for Achieving TIG Welding Results
- Frequently Asked Questions (FAQs)
- Conclusion
- References
How to Tig Weld Stainless Steel?
TIG stands for Tungsten Inert Gas welding. To tig weld stainless steel, use a welder set at 99 to 150 amps, with a 2% thoriated tungsten electrode. It’s ideal for thin materials and requires practice to master.
What is TIG?
TIG stands for Tungsten Inert Gas welding. It’s a precise process that uses a non-consumable tungsten electrode. This electrode generates an arc with the base metal. Usually, argon or helium is the shielding gas, which ensures a clean weld by preventing contamination.
When you think about TIG welding stainless steel, you’re looking at a technique that requires finesse. I’ve tried it and found that controlling the heat is crucial. With settings usually between 10 and 250 amps, you must adjust according to the metal thickness, which can range from 0.031 in (0.8 Mm) to 0.250 in (6.35 Mm).
Friends have shared their experiences tackling challenging projects, like pipe welding. It’s interesting that titanium and some aluminum alloys can also be welded using TIG. Curious about how to TIG weld stainless steel? The key is mastering the settings and technique for a solid joint.
Types Of TIG for Welding Stainless Steel
What types of TIG can you use for stainless steel?
AC TIG Welding
AC (Alternating Current) TIG welding uses both positive and negative polarity. For stainless steel, set your welder to low frequency and adjust the balance. Use a pure tungsten electrode and argon gas for shielding.
DC TIG Welding
DC (Direct Current) TIG welding is often preferred for stainless steel. Set your machine to DCEN (Direct Current Electrode Negative). Use a 2% thoriated tungsten electrode and a flow rate of 15-20 CFH (Cubic Feet Per Hour) of argon gas. Precision in handling equipment is crucial for different materials, so explore the techniques for welding thin metal.
Pulsed TIG Welding
Pulsed TIG welding delivers energy in bursts. Set the machine to pulse mode for stainless steel. This method controls heat; start with a pulse rate of 1-3 Hz for tighter areas.
Hybrid TIG Welding
Hybrid TIG combines TIG with MIG (Metal Inert Gas) processes for greater efficiency. Set it to low amperage and increase the travel speed. This method requires 95% argon with 5% CO2 for shielding gas.
Orbital TIG Welding
Orbital TIG welding automates the process in a circular motion. For stainless steel, ensure fixtures are secure. You should preset the weld parameters, typically around 100-150 A, for optimal results. Mastering specific techniques is essential, especially when it comes to understanding how to weld vertical.
You should now have a good understanding of various TIG techniques for welding stainless steel. In the next part, we’ll discuss essential requirements.
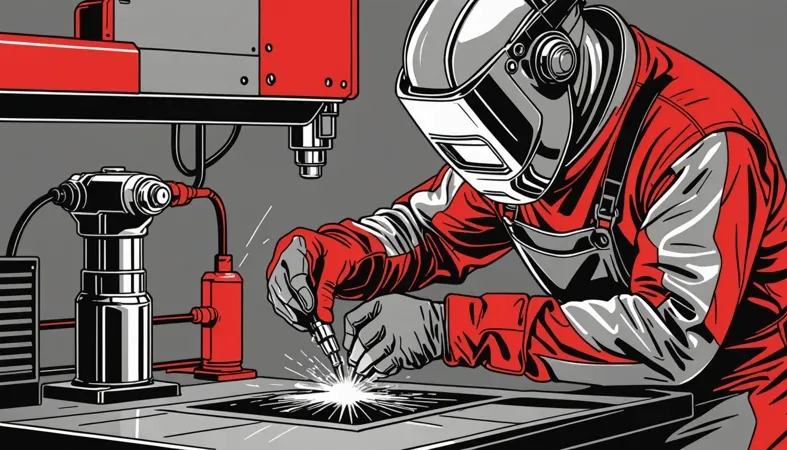
Prerequisites: What Do You Need?
What do you need to start TIG welding stainless steel?
- TIG Welder: You need a welder like the Lincoln Electric Square Wave TIG 200 for precise, clean welds.
- Tungsten Electrode: Use 2.4 mm (3/32 in) pure tungsten, such as the ZT-31. It’s vital for stable arcs and accurate welding.
- Argon Gas: Obtain high-purity argon gas, about 99.998%. This protects the weld pool from oxidation and contamination.
- Filler Rod: Choose a stainless steel filler rod, like ER308L, with a 1.6 mm (1/16 in) diameter. It’s necessary for strong joints and compatibility with most stainless steels.
- Chipping Hammer: Use a chipping hammer like the Forney 75752. It removes slag for smoother finishes.
We have now covered the necessary requirements for TIG welding. Next, we’ll discuss the steps for TIG welding stainless steel.
Steps for How to TIG Weld Stainless Steel
Now, we’ll cover the essential steps for mastering TIG welding with stainless steel. Follow each step closely for the best results.
Prepare the Work Area
Ensure your workspace is clean and clutter-free. This minimizes distractions during controlled arc welding. Avoid dim lighting—you need to see your weld pool clearly. For optimal results, it’s important to understand various techniques and ensure proper setup in your projects, which is why familiarizing yourself with different welding processes can be beneficial. Securely position your workpiece to prevent movement during the process.
Choose the Right Equipment
Select a TIG welding machine compatible with stainless steel, preferably a DC unit. I recommend machines rated at least 200 amps for better versatility, especially with thicker materials. Use a 2.4 mm (3/32 Inch) tungsten electrode, the standard for stainless steel. Invest in a quality gas lens to improve shielding gas coverage. Mastering different welding positions is crucial and to effectively execute welding in less accessible orientations, explore techniques for welding overhead.
Select the Correct Filler Material
Identify the right filler rod based on the stainless steel grade you’re welding. For most austenitic stainless steels, a 308L rod works well. I suggest 0.8 mm (0.031 Inch) for thin workpieces to minimize distortion. Choosing the wrong filler can lead to poor fusion or discoloration.
Set the Machine Parameters
Set your machine to a higher frequency, around 100 Hz, for better arc stability. Maintain a voltage between 10 and 15 volts and adjust the amperage based on material thickness: 100 amps for 1.5 mm (0.06 Inch) is a good starting point. Efficient cooling of your tungsten is essential for consistent performance. If you’re welding thicker sections, consider using a pulse feature for better control.
Clean the Stainless Steel Surface
Thoroughly clean the surfaces to be welded. Use a wire brush or a dedicated stainless steel cleaner to remove oils, grease, and corrosion. Clean in the direction of the metal grain to avoid scratches that might affect the weld. Wipe it down with acetone; it dries quickly and leaves no residue.
Begin Welding
Start your arc at a 15-degree angle and maintain a consistent speed. Encourage a steady travel speed for smooth bead formation. Keep the torch about 1/8 inch (3 Mm) from the workpiece for optimal results. Adjust your angle based on joint design; for a butt joint, aim to maintain an even push.
So far we covered the steps for TIG welding stainless steel. Let’s look at the precautions to take next.
Precautions
Let’s cover key safety measures for your TIG welding project.
- Wear a proper welding helmet: It protects your eyes from bright arcs. I recommend the 3M Welder’s Helmet for a good fit.
- Use appropriate gloves: Heat-resistant gloves protect your hands from sparks. Consider Miller Welding Gloves for excellent protection.
- Keep your workspace clean: A tidy area reduces hazards. An uncluttered 3ft x 3ft (0.91m X 0.91m) space is ideal.
- Avoid flammable materials: Keep combustibles at least 35 feet (10.7m) away. Use a fireproof blanket around your work area.
Always prioritize safety—it’s about looking out for yourself.
We’ve wrapped up precautions for welding stainless steel here. Let us turn our attention to types of welding techniques.
Types Of Welding Techniques for Stainless Steel
Let’s move on to welding types. We’ll cover TIG, MIG, Stick, Plasma Arc, and Electron Beam techniques.
TIG Welding
TIG (Tungsten Inert Gas) welding is precise. It uses a non-consumable tungsten electrode to produce the weld. You can easily control the heat, making it great for thin stainless steel—ideal for projects like stainless steel exhausts. Typical amperage settings range from 25 A to 200 A.
An important technique involves the second weld layer which is commonly known as the hot pass in welding.
MIG Welding
MIG (Metal Inert Gas) welding offers speed and versatility. It uses a continuous wire feed for the electrode. It’s suited for thicker stainless steel, with a feed rate of about 1-20 inches/min (25-508 Mm/min). It’s great for machinery or structural applications.
Stick Welding
Stick welding, or Shielded Metal Arc Welding (SMAW), is simple and effective. It uses a coated electrode to create the arc. It’s robust for outdoor work and can handle rusty surfaces, though it may require more clean-up afterward. Stick welders usually operate at around 70 A to 200 A.
Plasma Arc Welding
Plasma Arc Welding (PAW) allows for deep penetration and high precision. It creates an ionized gas to carry the arc, providing a clean and focused weld. This method is mainly used in high-end applications, with typical amperage around 50 A to 500 A.
Electron Beam Welding
Electron Beam Welding (EBW) uses a beam of electrons to create welds in a vacuum. This method provides deep penetration with minimal distortion. While it’s not common, settings often vary from 200 A to over 800 A, making it efficient for high-tech industries.
Factors Affecting TIG Welding Of Stainless Steel
What factors impact the methods for welding stainless steel with TIG?
Material Thickness
Thicker materials require higher amperage. For example, materials over 3 mm (0.12 In) may need 150-200 amps.
Joint Preparation
Clean, well-prepared joints promote better penetration. A root gap of 1-3 mm (0.04-0.12 In) is ideal.
Shielding Gas Type
Use 100% argon for stainless steel. It’s crucial for preventing oxidation and ensures a clean weld.
Welding Speed
A faster speed can lead to weaker welds. Slower speeds allow better control and penetration, especially in thin sections.
Tungsten Electrode Type
Your choice of tungsten matters. For stainless steel, use a 2% lanthanated or thoriated tungsten for optimal arc stability.
Common Issues in TIG Welding Of Stainless Steel
Let’s look at unique problems you might face with TIG welding.
Heat-affected Zone Discoloration
TIG welding can cause discoloration in the heat-affected zone (HAZ). Look for gold, blue, or dark brown hues. Use a cooler welding speed and adjust your heat settings to around 100–200 °C (212–392 °F) to resolve this.
Weld Cracking
Cracks may appear after TIG welding. If you notice them, ensure you’re using the correct filler material. I recommend preheating materials above 150 °C (302 °F) to minimize this risk.
Porosity in Welds
Porosity in TIG welds often arises from contamination. Check for small holes in the weld bead. Maintain a clean working surface and use argon gas with at least 99.98% purity to resolve it.
Inadequate Penetration
TIG processes sometimes result in inadequate penetration. Identify this issue if the weld isn’t thoroughly fused. Adjust your angle to 15° and the amperage to between 120–140 A for deeper penetration.
Filler Material Contamination
Using contaminated filler material in TIG can ruin your welds. Look for inconsistent appearances in the weld beads. Keep consumables clean and free from rust or grease.
Aftercare, Inspection, and Advanced Tips for TIG Welding Stainless Steel
Here’s key information on what to do after welding stainless steel with TIG.
Aftercare Tips
After completing your TIG weld, clean the area with a stainless steel brush or suitable abrasive pad. Use products like 3M Clean-N-Strip to remove oxidation effectively. Finally, check the welded seam for contaminants. Remember, your job’s success depends on this meticulous aftercare!
Inspection Guidelines
Inspect your welds visually for consistent bead width—aim for 1/16 inch (1.58 Mm) to 1/8 inch (3.17 Mm). Use a quality ultrasonic tester to identify internal flaws. I prefer the Sonatest model for precision in assessing integrity.
Expert Tips
If you’re experienced, try using pulse settings for better heat control. Adjust your amperage to achieve a bead profile of 0.125 to 0.25 inch (3.17 Mm to 6.35 Mm) in width. Don’t settle for aesthetics—calculate the penetration! Aim for 70% penetration to ensure good weld strength.
Common Alloys Used in TIG Welding Stainless Steel
When you tackle TIG welding stainless steel, it’s vital to choose the right alloy. Different stainless steel grades have unique properties affecting your weld. Here’s a quick overview.
Alloy Type | Common Usage | Welding Filler Rod | Corrosion Resistance |
---|---|---|---|
304 | General purpose, kitchen equipment | ER308L | Excellent |
316 | Marine environments, chemical processing | ER316L | Superior |
2205 | Oil and gas applications | ER2209 | Outstanding |
410 | High hardness applications | ER410 | Moderate |
430 | Food processing and kitchen fixtures | ER430 | Good |
Selecting the right filler rod is crucial for achieving the desired mechanical properties and corrosion resistance. For example, use ER308L for 304 stainless steel to ensure a solid bond. What alloy will you choose for your next project?
Benefits Of TIG Welding Stainless Steel
The main benefit of TIG (Tungsten Inert Gas) welding stainless steel is precision. Friends have told me how it worked wonders for their projects, delivering clean, strong seams every time.
Moreover, TIG welding offers versatility, control over heat input, a cleaner process, and less distortion. These factors help achieve high-quality welds that resist corrosion and look great.
Applications You Should Know About for TIG Welding
TIG welding is used for precise applications across various industries. It has many uses, including:
- Food Processing Equipment: TIG welding is crucial for making stainless steel tanks and pipes, as it maintains smooth surfaces and prevents contamination.
- Marine Applications: It’s used to fabricate boat hulls and fittings due to its resistance to saltwater corrosion and high strength.
- Aerospace Components: Professionals rely on TIG welding for lightweight structural parts because it creates strong, clean welds without defects.
- Automotive Exhaust Systems: Many manufacturers prefer TIG for stainless steel exhaust systems due to its durability and aesthetic quality.

Alternatives for Achieving TIG Welding Results
There are alternatives to get similar results when you’re working with stainless steel. For instance, MIG welding, such as using a Lincoln Electric MIG welder, can be quicker and easier for some projects. If you’re looking to repair stainless steel exhaust systems, Plasma arc welding is another option that yields clean results.
Also, consider using oxy-fuel welding for thin stainless steel. It’s a bit different but can be effective, especially for thin materials. Each method has its perks—like cost or speed—so pick what’s best for your project!
Frequently Asked Questions (FAQs)
Now let us look at some common questions I typically get asked about TIG welding.
What is the Best TIG Setting for Stainless Steel?
The best TIG setting for stainless steel is around 100-140 amps (Depending on Material Thickness). Thinner steel needs lower amps, while thicker steel requires more heat. Power settings affect your weld quality; balance is crucial for a clean finish without overburning.
Can I Weld Stainless Steel With a TIG Welder?
Yes, you can weld stainless steel with a TIG welder. TIG welders are known for precision and control, making them perfect for stainless projects. The welder can work with various electrode types that help achieve strong, clean seams in stainless steel.
What Current Do You TIG Weld Stainless Steel?
You typically use DC (Direct Current) for TIG welding stainless steel. DC provides a consistent arc, which is essential for clean welds. For thinner materials, use lower current—about 55-70 amps (Per 1/8 Inch, 3.2 Mm) helps prevent burn-through.
What Rod Do I Use to TIG Weld Stainless Steel?
You should use ER308L filler rod to TIG weld stainless steel. This rod has high corrosion resistance and excellent strength. It is versatile, suitable for welding 304 and 308 stainless steel grades, and ensures a strong bond.
Can You Tig Weld Aluminum to Stainless Steel?
No, you can’t directly TIG weld aluminum to stainless steel. These metals have different thermal properties and expand at different rates. Using a special filler material, like an aluminum-bronze, and a transition joint can help, but it’s not a straightforward process.
Conclusion
We covered various aspects of how to TIG weld stainless steel. We discussed what TIG is, types of TIG for stainless steel, prerequisites, steps for welding, precautions, techniques, factors affecting the process, common issues, aftercare, and the benefits and applications of TIG welding. We also looked at alternatives and tackled frequently asked questions.
TIG welding stainless steel involves a few key steps. You’ll need a TIG welder set to about 120-180 amps, a tungsten electrode, filler rod, and clean joints. I hope these welding tips prove valuable to you as you get started on your own TIG welding projects.
For further insights and resources about welding techniques, feel free to explore more on our homepage at What is Welding.
References
- Lincoln Electric. (2020). The Procedure Handbook of Arc Welding (15th ed.). Cleveland, OH: Lincoln Electric Company.
- British Standards Institution. (2018). BS EN ISO 9606-1: Qualification Testing of Welders. London, UK: BSI.
Joe Carter is a retired welding professional with over 40 years of hands-on experience in the industry, spanning ship repair, structural welding, and even underwater projects. Joe is a master of MIG, TIG, and Stick welding. Passionate about mentoring the next generation of welders, Joe now shares his decades of expertise and practical insights to help others build rewarding careers in welding.
Metalworking, MIG Welding, Pipe Welding, Stainless Steel, TIG Welding, Welding, Welding Equipment, Welding Gloves, Welding Safety, Welding Techniques