What is SMAW Welding? Learn About Processes, Electrodes, and Applications!
Published on: December 9, 2024 | Last modified: March 4, 2025
By: Joe Carter
SMAW stands for Shielded Metal Arc Welding. It’s a popular welding process used to join metals using an electrode coated in flux.
One thing that’s regularly asked of me is what is smaw welding? It’s crucial to follow the guidelines in this process. When I first started welding, I learned that following proper techniques not only makes the joint stronger but also keeps you safe and saves materials.
In this guide, I’ll break down how SMAW welding works, different types of SMAW electrodes, steps for prepping to weld, factors influencing performance, common issues you might face, aftercare tips, use cases, and even alternatives. You’ll gain a clearer understanding of what SMAW welding is used for and how to SMAW weld like a pro.
Contents
- What is SMAW Welding?
- How Does SMAW Welding Work?
- Types Of SMAW Electrodes
- Steps for Preparing for SMAW Welding
- Factors Influencing SMAW Welding Performance
- Benefits and Limitations of SMAW Welding
- Common Issues You Might Encounter
- Aftercare, Inspection, and Advanced Tips for SMAW Welding
- Use Cases Of SMAW Welding
- What Are the Alternatives to SMAW Welding?
- Frequently Asked Questions (FAQs)
- Conclusion
- References
What is SMAW Welding?
SMAW, or Shielded Metal Arc Welding, uses a consumable electrode to create a weld. It’s versatile and works on many metals, making it ideal for construction and repair. You often see it in pipelines and structural steel work.
How Does SMAW Welding Work?
SMAW, or Shielded Metal Arc Welding, is a popular method. It uses an electric arc to melt a filler rod and join two metal pieces. The process typically reaches temperatures over 3,000 °C (5,432 °F). About 95% of welders use this method for its versatility and effectiveness.
The basic principles of SMAW involve creating an arc between the electrode and the workpiece. This generates intense heat, allowing the electrode to melt and fuse the materials. The arc is shielded by gases produced during the process, preventing contamination and ensuring a strong joint.
Get familiar with the different positions for SMAW welding, like flat or horizontal. Proper positioning can significantly affect the quality of your weld. Understanding SMAW welding means seeing that it’s not just about melting metal—it’s about mastering the craft.
Types Of SMAW Electrodes
What are the types of SMAW welding electrodes?
-
Cellulosic Electrodes
Cellulosic electrodes use cellulose as a coating. In SMAW, they create a gas shield that protects the weld. To use them, strike an arc and maintain a steady speed while welding for good penetration. One intriguing aspect is underwater welding, where unique challenges and dangers arise, and these complexities lead to questions about how dangerous underwater welding can be.
-
Basic Electrodes
Basic electrodes have a coating enriched with calcium and sodium. They’re ideal for tough environments in SMAW, helping prevent weld defects. Keep the arc length short and adjust your speed carefully for best results.
-
Iron Powder Electrodes
These electrodes include iron powder in the coating. They improve deposition rates in SMAW by providing more filler metal. Maintain the correct arc length and control the travel speed for optimal results.
-
Low Hydrogen Electrodes
Low hydrogen electrodes reduce moisture in the weld area, making them excellent for high-strength steel in SMAW applications. Dry the electrodes before welding and keep consistent heat input.
-
Rutile Electrodes
Rutile electrodes contain high titanium dioxide content. They’re user-friendly in SMAW, producing a stable arc, suitable for beginners. Maintain a steady angle and speed for an even bead.
We’ve wrapped up the different types of SMAW electrodes here. Next up, we’ll look at the steps for preparing for SMAW welding.
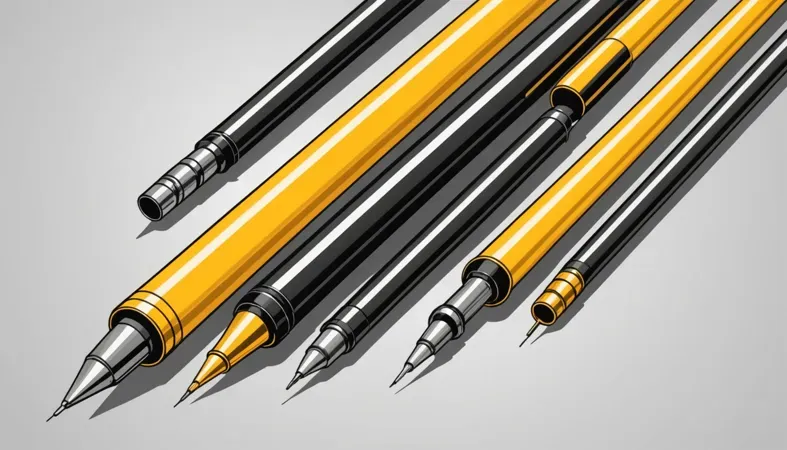
Steps for Preparing for SMAW Welding
Now, we’ll cover the essential steps for using SMAW welding.
-
Set Up Your Work Area
First, clean your workspace. A tidy area reduces accident risks. Keep flammable materials away, especially outdoors. Good lighting is key; aim for 300 to 500 lux for clarity.
Keep a comfortable distance between yourself and the material, typically 3 to 4 ft (0.9 To 1.2 M). Properly align your tools and power source. Staying organized helps you focus on your craft.
-
Prepare the Base Material
Clean the surfaces you’ll weld. Remove rust, oil, and dirt—don’t skip this. Use a wire brush or grinder; a clean surface improves strength and integrity. The SMAW process is effective on thicknesses from 1/8 inch (3.175 Mm) to over 1 inch (25.4 Mm). Proper safety gear is crucial as welding without the necessary protection can have severe consequences on your health, which should highlight the risks of welding without a mask.
Check the joint fit-up. Misalignment can weaken joints. Ensure pieces fit snugly for better penetration when using SMAW. If gaps exist, consider tacking before full welding.
-
Choose Your Electrode
Select an appropriate electrode based on metal thickness and type. For example, E6011 works well on rusty or dirty metals, while E7018 is ideal for structural steel. Ensure the electrode has a matching coating; this affects arc stability and results.
Also, check the diameter. Common sizes, like 1/16 inch (1.6 Mm) to 3/16 inch (4.8 Mm), require different currents. Thinner electrodes need lower currents, while thicker ones require higher. Finding the right balance ensures better bead quality.
-
Adjust Settings on Your Welder
Set your welder for SMAW; typically, output current should be between 60 and 160 amps, depending on electrode size and thickness. Adjust amperage for material thickness—more than 1/4 inch (6.35 Mm)? Increase the amps.
Choosing the right shielding gas is crucial to achieving quality welds, and argon plays an essential role in enhancing arc stability and reducing spatter. To understand more about argon used for in welding, it’s worthwhile to explore its specific applications.
Also, consider your welding position. A flat position requires different settings than overhead. Use higher heat for vertical or overhead welding to achieve good fusion without excessive runoff. Familiarizing yourself with machine settings is crucial to adapting techniques effectively, and you can learn how to operate a welding machine for optimal results in various positions.
-
Test Your Technique
Before starting your project, practice on scrap metal. This helps you adjust your technique. Focus on maintaining a steady hand and consistent speed for smoother welds. Start at a pace of about 2 inches (5.08 Cm) per second.
When you are ready to tackle more complicated positions like vertical welding, it is essential to understand the unique challenges involved by reviewing techniques for welding in vertical positions.
Observe how the electrode burns. If you hear a nice sound, you’re doing well. If it pops or crackles, you may need to adjust your settings.
-
Start Welding
Finally, it’s showtime! Position your electrode 1/8 inch (3.2 Mm) above the base material. This distance is crucial for achieving the correct arc length. If it’s too close, you’ll stick; too far, and you won’t get good penetration.
Maintain a steady angle—typically 10 to 15 degrees from vertical. Control and consistency are key. Keep practicing, and you’ll become a pro with SMAW welding!
We’ve wrapped up the steps for preparing for SMAW welding here. Next up, we’ll look at factors influencing SMAW welding performance.
Factors Influencing SMAW Welding Performance
What factors impact SMAW welding outcomes?
-
Electrode Diameter
A larger diameter increases the amount of deposited metal. For instance, a 3.2 mm (1/8 Inch) electrode can deposit 3-4 kg (6.6-8.8 Lbs) of weld metal per hour.
-
Welding Current
Current settings determine arc stability. An amperage of 100-150 A is typical for 3.2 mm (1/8 Inch) electrodes, affecting penetration and heat input.
-
Travel Speed
Adjust the travel speed based on the material thickness. Slower speeds can lead to deeper penetration, but going too slow risks burn-through.
-
Workpiece Material
The material type significantly influences weld quality. Different steel grades may require specific electrode types, such as E6010 for mild steel, affecting the welding process.
-
Weld Bead Position
The angle and position of the weld bead are important. Welding in a vertical position changes how the molten metal behaves, affecting bead shape and fill.
You should now have a good understanding of factors affecting SMAW welding performance. In the next part, we’ll discuss its advantages and disadvantages.
Benefits and Limitations of SMAW Welding
Let’s explore some of the benefits and limitations of SMAW welding.
Benefits of SMAW Welding
- Versatility: SMAW can weld a wide range of metals, including steel, cast iron, and stainless steel. It’s handy in various sectors, from construction to maintenance.
- Portability: Equipment for SMAW is typically lightweight and can be used almost anywhere, making it perfect for fieldwork.
- Cost-Effective: The setup costs are relatively low compared to other methods like GMAW and GTAW, making it accessible for small shops or DIYers.
- Skill Development: It provides a solid foundation for learning other welding techniques. Mastering SMAW can enhance your overall welding skills.
Limitations of SMAW Welding
- Slower Speed: SMAW generally has slower welding speeds than processes like GMAW, which can extend project timelines.
- Quality Control: It requires a higher skill level to achieve high-quality welds consistently, especially in complex joints or overhead positions.
- Cleanup: SMAW leaves slag that must be cleaned off the weld after cooling, adding extra steps to your process.
- Limited Thin Material: It’s not ideal for very thin materials; GMAW or GTAW might be better suited for such cases.
We’ve wrapped up the advantages and drawbacks of SMAW welding here. Next up, we’ll look at typical challenges you might face.
Common Issues You Might Encounter
Let’s look at specific issues you may face with SMAW (Shielded Metal Arc Welding).
-
Electrode Sticking
SMAW can cause electrodes to stick. You can spot this by observing a dimming arc or a sudden stop in feed. To fix it, adjust the travel speed or increase the current.
-
Poor Arc Stability
Check the electrode type and polarity if you experience poor arc stability in SMAW. A steady arc indicates a good weld bead; adjust accordingly to improve it.
-
Cracking in Welds
Cracking can occur due to rapid cooling in SMAW. Look for visual cracks after welding. Preheating and using the proper filler can help prevent this issue.
-
Inadequate Penetration
In SMAW, inadequate penetration results in a weak joint, indicated by less than expected material fusion. Increasing amperage or decreasing travel speed can enhance penetration.
-
Slag Inclusion
In SMAW, slag inclusions appear as dark spots in the weld. Check for them through visual inspection. Thoroughly clear slag between passes and maintain proper technique to resolve this.
Aftercare, Inspection, and Advanced Tips for SMAW Welding
Here’s useful information on aftercare, inspection items, and expert tips for SMAW.
Aftercare Advice
After completing the SMAW process, allow your workpiece to cool slowly at room temperature—ideally around 20°C (68°F) for 30 minutes. Use a soft cloth to gently remove slag, focusing on joints. Ensure no residual flux remains, as it can cause corrosion or cracking, especially in carbon steel.
Inspection Checklist
Inspect welds visually and with a gauge to check bead width—ideally, maintain 3 to 5 mm (0.12 To 0.20 In) for strong joints. Use a magnetic particle inspection kit, like the Magnaflux, to detect cracks. During a recent inspection, I found a stress fracture that went unnoticed without proper tools.
Expert Techniques
If you’re experienced, consider adjusting electrical strikes. Keep your amperage between 100 and 140 A for optimal penetration. Add a slight weave pattern for joints over 5 mm (0.20 In) thick to control heat input and prevent warping. Trust me, proper techniques make a significant difference.
Use Cases Of SMAW Welding
SMAW welding has several applications, including:
- Pipe Fabrication: Ideal for joining pipes in power plants and refineries due to its strength and versatility. It’s popular in industries handling high pressure.
- Repair Work: Great for on-site repairs of machinery and equipment. Its easy setup and portability make it a top choice for quick fixes.
- Shipbuilding: Used for constructing and repairing ships. Its ability to work in various positions is invaluable in tight spaces.
- Construction Sites: Perfect for welding in heavy construction. The skill level needed and the reliability of SMAW make it ideal for diverse applications.
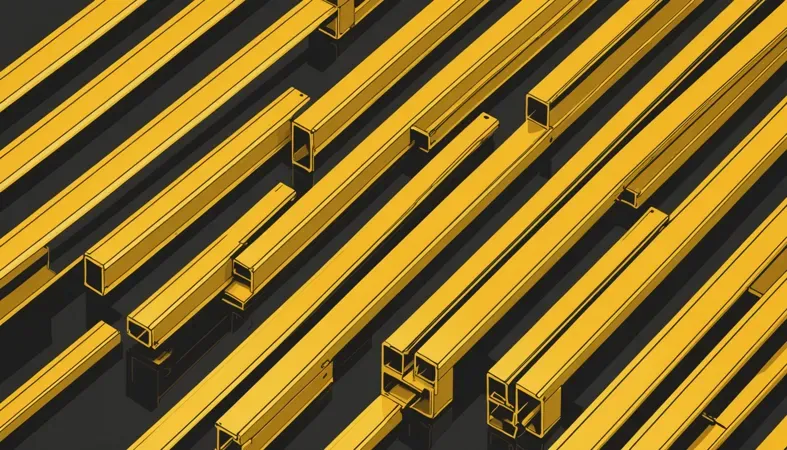
What Are the Alternatives to SMAW Welding?
When looking for alternatives to SMAW welding, consider methods like Gas Metal Arc Welding (GMAW) or Gas Tungsten Arc Welding (GTAW). These techniques might work better in certain applications, such as thinner materials or in controlled environments. For instance, I’ve often found that using a Miller Millermatic 211 for GMAW provides cleaner welds with less cleanup needed afterward.
Another option is Flux-Cored Arc Welding (FCAW), which can offer good results outdoors with poor weather. FCAW uses a tubular wire filled with flux, giving you a similar versatility to SMAW. In my own projects, I’ve seen it shine when welding thicker metals, ensuring strong joints that last.
Frequently Asked Questions (FAQs)
Now let us look at some common questions I typically get asked about SMAW welding.
What is the Difference Between SMAW and Stick Welding?
The difference between SMAW and stick welding is minimal because SMAW stands for Shielded Metal Arc Welding, which is also commonly known as stick welding. Both use an electrode and create an arc to melt the metal. SMAW is versatile, and it works on various materials, making it a popular choice.
What Are the 4 Types Of SMAW?
The four types of SMAW are E6010, E6011, E6013, and E7018. Each type has unique properties and applications. For instance, E7018 is known for its high strength and is often used in structural welding due to its superior mechanical properties.
What is SMAW Vs GMAW Welding?
SMAW vs GMAW indicates two different welding processes: Shielded Metal Arc Welding (SMAW) and Gas Metal Arc Welding (GMAW). SMAW uses a consumable electrode whereas GMAW uses a continuous wire feed. The typical welding speed for GMAW is faster at about 10 to 20 inches per minute (25 to 51 Cm/min) compared to SMAW’s rate of about 5 to 12 inches per minute (13 to 30 Cm/min).
What Does ‘Dig’ Do When Welding Using the SMAW Process?
‘Dig’ in SMAW welding refers to the penetration of the molten weld pool into the base metal. A higher ‘dig’ setting can enhance penetration, useful for thicker materials. Typically, setters adjust it based on the electrode type and base material thickness; for example, E6010 might require more dig than E6013.
What Positions Can SMAW Welding Be Performed in?
SMAW welding can be performed in several positions including flat, horizontal, vertical, and overhead. Each position requires different techniques. For instance, vertical welding can be challenging and often requires a slower travel speed to prevent defects.
Conclusion
We’ve gone through a lot, thank you for sticking it out. We covered what SMAW welding is, how it works, types of electrodes, preparation steps, factors influencing performance, common issues, aftercare tips, use cases, and alternatives. Each of these pieces paints a full picture of the SMAW process.
I trust these insights have been helpful. So, what is SMAW welding? In simple terms, SMAW, or Shielded Metal Arc Welding, is a versatile welding process that uses a coated electrode. It’s great for various positions and applications, making it a go-to for many welders.
If you’re looking for more expert tips and guidance on welding techniques, feel free to visit What is Welding.
References
- American Welding Society. (2020). AWS Welding Handbook: Welding Science and Technology (Vol. 1). Miami, FL: American Welding Society.
Joe Carter is a retired welding professional with over 40 years of hands-on experience in the industry, spanning ship repair, structural welding, and even underwater projects. Joe is a master of MIG, TIG, and Stick welding. Passionate about mentoring the next generation of welders, Joe now shares his decades of expertise and practical insights to help others build rewarding careers in welding.
American Welding Society, Construction, Construction Welding, Filler Metal, Metal Joining, SMAW Welding, Welding, Welding Applications, Welding Electrodes, Welding Techniques