How to Operate Welding Machine? Key Steps, Safety Tips, and Techniques
Published on: November 20, 2024 | Last modified: March 4, 2025
By: Joe Carter
A welding machine is a tool that joins metal pieces together using heat. It melts the metal, allowing it to fuse as it cools.
I’ve received numerous inquiries about how to operate welding machine. It’s crucial to learn proper techniques to ensure quality and safety in your projects. From my personal experience, skipping steps can lead to defects and potential hazards.
In this guide, we’ll dive into topics such as identifying welding machine types, essential prerequisites, steps to operate a welding machine, safety tips, techniques, common problems, and aftercare. You’ll also learn how to set up welding machine for SMAW, how to adjust welding machine settings, and more. Let’s get started!
Contents
- How to Operate Welding Machine?
- What is a Welding Machine?
- Types Of Welding Machines
- Prerequisites
- Safety Tips
- Steps to Operate a Welding Machine
- Types Of Welding Techniques
- Factors Affecting the Operation Of Welding Machines
- Advanced Techniques for Operating Welding Machines
- How to Address Common Welding Problems
- Top Benefits You Can Expect
- Real-world Uses for Welding
- Other Options You Can Consider
- Frequently Asked Questions (FAQs)
- Conclusion
- References
How to Operate Welding Machine?
A welding machine is a tool for joining metal parts. To operate a welding machine, connect power, adjust settings (e.g., 100-300 A), and follow safety practices. It’s not too hard! Common uses include fabrication and repair. It’s also crucial to know how to treat welding burns on skin should an accident occur. For more guidance, check out what to do for welding burns on skin.
.
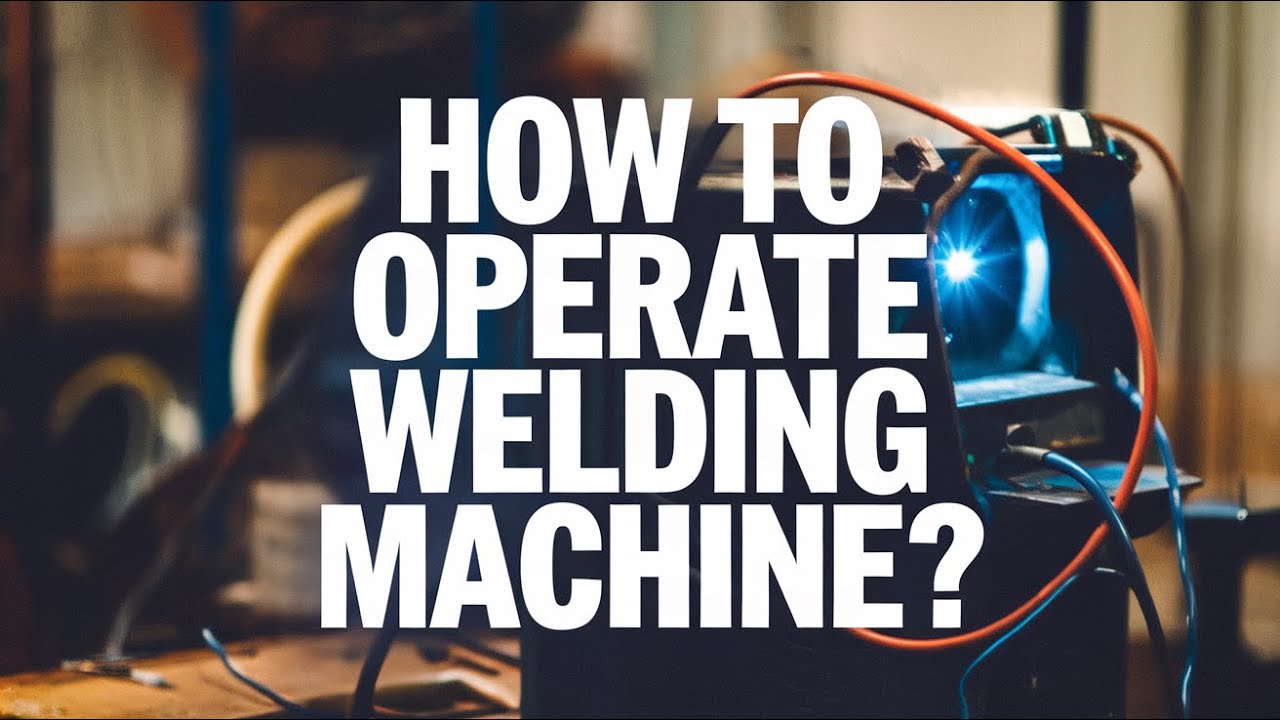
What is a Welding Machine?
A welding machine is an essential tool in metalworking. It uses electrical energy to melt and fuse metals together. There are several types of welding machines, including MIG (Metal Inert Gas) and TIG (Tungsten Inert Gas), which operate at various currents. A typical machine ranges from 90 to 300 amps, allowing effective welding of different materials.
Operating a welding machine isn’t as daunting as it sounds. You need to ensure that your settings are correct for the material you’re working with. From my experience, starting your machine requires a quick check of the voltage and amperage settings—both are crucial for a clean weld. Makes sense, right?
When I first learned to set up a welding machine for SMAW (Shielded Metal Arc Welding), I felt confused. I had to adjust the electrode and ensure the clamp was secure before turning on the machine. If you’re wondering how to operate a welding machine properly, know that the steps greatly impact your weld quality. It’s all about the settings and preparation!
Types Of Welding Machines
What are the types of welding machines, and how do you operate them?
-
MIG Welders
MIG welders use a continuous spool of wire as an electrode. To start a MIG welder, connect the power and gas supply, then adjust the wire speed and voltage settings before striking the arc.
-
TIG Welders
TIG welders use a non-consumable tungsten electrode to melt metal. To operate a TIG welder, set the amperage and gas flow, then move the torch steadily while adding filler metal as needed.
-
Stick Welders
Stick welders, or Shielded Metal Arc Welding (SMAW) machines, use flux-coated electrodes. To use a stick welder, plug it in, set the desired amperage, then strike the electrode against the metal to create an arc, maintaining a proper distance while welding.
If you experience vision discomfort after welding, it’s crucial to know how to treat flash burn in eyes.
-
Multi-process Welders
Multi-process welders handle various types of welding, including MIG, TIG, and Stick. To use one, select the desired process and adjust the settings accordingly. Follow the specific operation steps for that welding method. Comprehensive knowledge about the potential risks is crucial for a successful outcome, which is especially important when learning how dangerous underwater welding is.
-
Plasma Cutters
Plasma cutters slice through metal using a high-velocity jet of ionized gas. To operate, connect to the power and air supply, then set the pressure. Press the trigger to activate the cutter, guiding the torch along the material.
So far we covered the various welding machine types. Let’s look at the necessary prerequisites next.
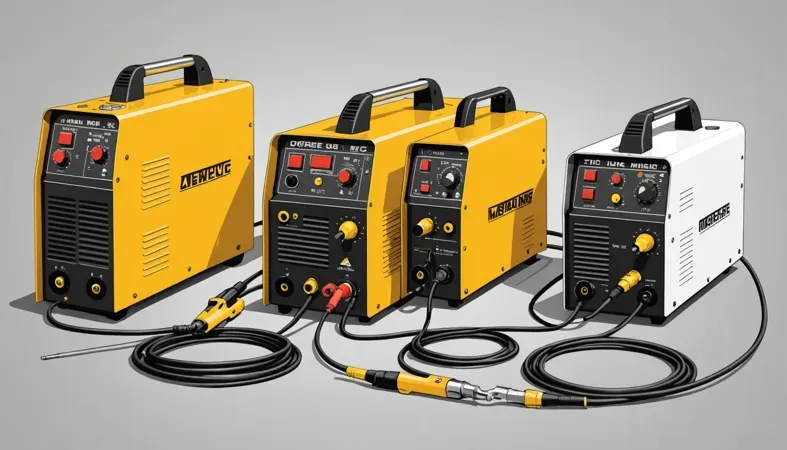
Prerequisites
What do you need to get started?
- MIG Welding Machine: You’ll need a model like the Hobart Handler 210 MVP for efficient MIG welding.
- Gas Cylinders: You’ll need argon or CO2 gas cylinders, such as the Lincoln Electric 80 cu ft, to provide protective gas for the weld.
- Welding Wire: Use ER70S-6 wire, typically 0.030 in (0.76 Mm) in diameter, for a strong joint.
- Workpiece Material: Use steel or aluminum stock up to ⅜ in (9.5 Mm) thick for effective welding.
- Welding Cart: Consider a portable cart like the Miller Multi-Process Welding Cart for easy transport of your gear.
We have now covered the necessary prerequisites. The next section will focus on important safety tips.
Safety Tips
Let’s review essential precautions for using a welding machine.
- Wear Personal Protective Equipment (PPE): Use a welding helmet, gloves, and fire-resistant clothing, like leather gloves, to prevent burns and sparks. I recommend these gloves for their durability.
- Ensure Proper Ventilation: Welding produces toxic fumes. Work in a well-ventilated area to avoid health risks like lung damage. Aim for at least 4-6 air exchanges per hour.
- Check for Gas Leaks: Inspect gas hoses regularly to prevent burns and fire hazards. A simple soapy water test can help detect leaks.
- Stay Focused and Alert: Avoid distractions. Just a moment of inattention can lead to serious injury. Stay mindful of your task and surroundings.
Safety precautions matter! I can’t stress that enough.
We covered safety precautions, gear, and best practices here. We will now cover operating procedures for a welding machine.
Steps to Operate a Welding Machine
Here are the steps to use a welding machine effectively.
-
Turn on the Welding Machine
First, locate the main power switch and flip it to the ‘On’ position. This sends power to the machine, preparing it for operation. For MIG welders, adjust voltage settings between 18V and 30V based on material thickness.
Be aware that different welding types might require different on/off processes. For TIG machines, ensure the gas flow is on before starting.
-
Set the Welding Parameters
Adjust the amperage based on material type and size. A good rule is 1 amp per 0.001 inch (0.0254 Mm) of material thickness. For mild steel, 120-160 amps often works well.
Don’t forget to consider the properties of the materials. Ignoring this can lead to poor welds!
-
Choose Your Electrode or Filler Material
Select the appropriate electrode for your welding process. A .030 inch (0.762 Mm) wire is ideal for MIG welding. For SMAW, consider an E6011 or E7018 electrode based on the job.
Match your filler material with the base material for the best results. Mismatched materials can lead to weak joints — trust me, you don’t want that!
-
Connect the Ground Clamp
Attach the ground clamp to your workpiece for a stable electrical connection. Ensure the clamping area is clean, free of rust or paint, to maintain proper conductivity. A loose connection can cause arc instability.
A bad ground can create various welding issues, including arc spatter. Always double-check this step to avoid problems!
-
Initiate the Arc
For TIG welding, gently scratch the tungsten tip against the workpiece to start the arc; for MIG, just pull the trigger on your gun. Adjust your travel speed — too fast creates weak seams, while too slow may burn through your material. The walking the cup technique can help.
When starting an arc, I struggled with travel speed. Take it slow; you’ll find your rhythm. Consistent motion creates even heat, improving weld quality.
-
Monitor Your Weld Pool
Watch your weld pool closely. Aim for a solid neutral appearance with minimal splatter. The pool should melt evenly and have a bright orange color, but don’t stare too long! Maintain a distance of 1/8 to 1/4 inch (3.175 To 6.35 Mm) from the base material.
As you gain experience, you’ll notice signs in the weld pool that indicate quality or issues. Paying attention here can save you from rework later!
-
Finish and Clean Up Your Weld
After welding, allow the joint to cool naturally. Don’t quench it. Once it cools, use a wire brush or grinder to remove slag or oxidation, ensuring a clean surface for inspection.
A clean joint makes a huge difference! As a beginner, I skipped this step once, and the blow-through was terrible. Always finish strong by cleaning up your work!
We covered how to operate a welding machine. We will now cover different types of welding techniques.
Types Of Welding Techniques
Let’s explore different types of welding techniques: MIG, TIG, Stick, Flux-Cored, and Submerged Arc welding.
-
MIG Welding Techniques
MIG (Metal Inert Gas) welding uses a continuous wire feed as an electrode. You adjust the machine by setting the voltage (Typically 18-26 Volts) and wire feed speed (Around 2-10 M/min). It’s quick and effective for thin materials. Just remember to use a shielding gas like argon or a mix of argon and CO2. To reduce imperfections in your welds, it is essential to know what causes weld spatter.
-
TIG Welding Techniques
TIG (Tungsten Inert Gas) welding requires manually adding filler metal with a tungsten electrode. You control the amperage (usually 10-300 Amps) and set the shielding gas, typically pure argon. This process is great for clean, high-quality welds and is often discussed among professionals when it comes to various types of welding equipment, but it can be challenging for beginners.
When discussing welding processes, it’s crucial to understand the limits of how many times you can weld an alloy wheel.
-
Stick Welding Techniques
Stick welding, or SMAW (Shielded Metal Arc Welding), uses a stick electrode to create an arc. Set up the welding machine with the correct amperage (Usually 40-250 Amps, Depending on the Electrode Size). This method is durable and suitable for windy conditions but requires regular cleaning of slag between passes. Welding can pose certain hazards, so understanding how dangerous is welding is crucial for maintaining safety protocols.
-
Flux-cored Welding Techniques
In flux-cored welding, you use a tubular wire filled with flux. While the wire feeds automatically, adjust the voltage (18-27 Volts) and speed (2-5 M/min). It’s ideal for outdoor work since the flux protects the weld from contamination. Just maintain the arc length for smooth operation!
Choosing the right welding rod involves understanding the specific numbers and what they represent on the welding rod.
-
Submerged Arc Welding Techniques
Submerged arc welding involves a continuously fed consumable electrode and granular flux. Adjust settings like voltage (Generally 18-40 Volts) and travel speed (500-1600 Mm/min). The liquid flux shields the weld, creating deep, strong seams—perfect for thick materials in industrial applications.
I’ve learned that MIG welding offers flexibility and ease of use. It’s an excellent starting point for beginners due to its speed and efficiency. Plus, operating a MIG machine becomes intuitive once you properly set up the voltage and feed speed. When it comes to refining your skills, knowing how to effectively dismantle connections can be crucial, so here is a useful resource on removing unwanted welds.
Factors Affecting the Operation Of Welding Machines
What factors influence effective welding machine usage and operation?
-
Welding Material Type
The material type you’re welding greatly impacts settings and technique. For instance, aluminum requires a higher voltage than steel—holding at 14-16 volts (V) for MIG welding.
-
Welder Skill Level
Your skill level determines how well you can adjust the machine. A beginner may struggle to set optimal parameters, while a professional can quickly adapt to windy conditions or material thickness.
-
Welding Environment
Environmental factors like wind and temperature can alter your process. If you’re outside, wind can affect shielding gas. Ideal conditions are between 14-24°C (58-75°F) for an accurate weld.
-
Equipment Settings
Getting the settings right is crucial. Many machines have specific dials for amperage and wire feed speed to ensure a clean, consistent weld. For example, you might need 130 A for 3/16-inch (4.76 Mm) steel during MIG welding.
-
Power Supply Quality
The power supply can affect arc stability. Fluctuations can create weak welds; a steady supply of around 230-260 V significantly improves arc performance. If you’ve got an unstable supply, consider investing in a quality transformer.
Advanced Techniques for Operating Welding Machines
Ready to elevate your welding game? Let’s explore advanced techniques that can enhance your skills and efficiency.
Your Welding Position Matters
Adjusting your body position can greatly affect your control and precision. Here are some common positions:
- Flat Position: Ideal for most welds; it provides good access and visibility.
- Horizontal Position: Suitable for welding pipes and structural components; it can be tricky but offers stability.
- Vertical Position: Requires practice to maintain a steady hand; ideal for vertical joints.
- Overhead Position: Challenges your coordination; use this for tight spaces with joints above you.
Utilizing a Welding Technique Chart
A welding technique chart helps you choose settings based on your job. Here’s a condensed version:
Material Type | Welding Method | Recommended Amperage | Electrode Size |
---|---|---|---|
Mild Steel | MIG | 120-160 A | 0.030 in (0.76 mm) |
Aluminum | TIG | 150-200 A | 1/16 in (1.6 mm) |
Stainless Steel | Stick | 100-140 A | E7018 |
Cast Iron | Flux-Cored | 80-120 A | 0.035 in (0.89 mm) |
Optimizing Travel Speed
Travel speed plays a crucial role in weld quality. A good rule is:
- Slow and Steady: For thicker materials, aim for 5-10 inches per minute (127-254 mm/min).
- Fast and Focused: For thinner materials, increase speed to 10-15 inches per minute (254-381 mm/min).
I’ve found that maintaining a consistent travel speed prevents burn-through while achieving adequate penetration.
How to Address Common Welding Problems
Let’s look at specific issues that can arise with welding machines.
-
Inconsistent Welds
Welding machine settings can cause inconsistent welds. Check the amperage and travel speed. Adjust these settings until you see even beads.
-
Electrode Issues
Using the wrong electrode can ruin your weld. Ensure you select the right type for the job. Check compatibility and replace if needed.
-
Cooling Problems
A welding machine that overheats can create defects. Look for unusual noises or flickering displays. Run cooling systems and let your machine rest frequently.
-
Wire Feed Issues
A welded joint may fail if the welding machine has wire feed problems. Check the feed speeds and watch for jams. Clean the feeding mechanisms to ensure they move smoothly.
-
Gas Flow Problems
If you’re getting poor penetration, check the gas flow on your welding machine. Ensure correct pressure (Typically 10-20 Cf/h for MIG). Inspect hoses for leaks and replace them if damaged.
Top Benefits You Can Expect
The biggest advantage of knowing how to operate a welding machine is safety. Understanding the right techniques reduces the risk of accidents and injuries.
You’ll also gain many benefits, such as improved precision in your work, reduced material waste, faster project completion, and increased job opportunities in the welding field. A good grasp of how to use a welding machine can enhance your skills and boost your confidence.
Real-world Uses for Welding
I’ve seen people use welding machines for creating metal art. However, there are many unique applications, such as:
- Pipe Welding: Vital in the oil and gas industry, this task connects pipes safely and ensures durability against high pressure. It’s popular in pipeline construction.
- Aerospace Component Fabrication: Used to assemble parts in aircraft, welding provides lightweight strength. This application is crucial for safety in the industry.
- Automotive Frame Repairs: Professionals weld car frames to maintain structural integrity. It’s widely used to repair damage and enhance safety on the road.
- Shipbuilding: In this field, welding machines construct ship hulls. It’s essential for building resilience against rough seas and is highly sought after in marine engineering.
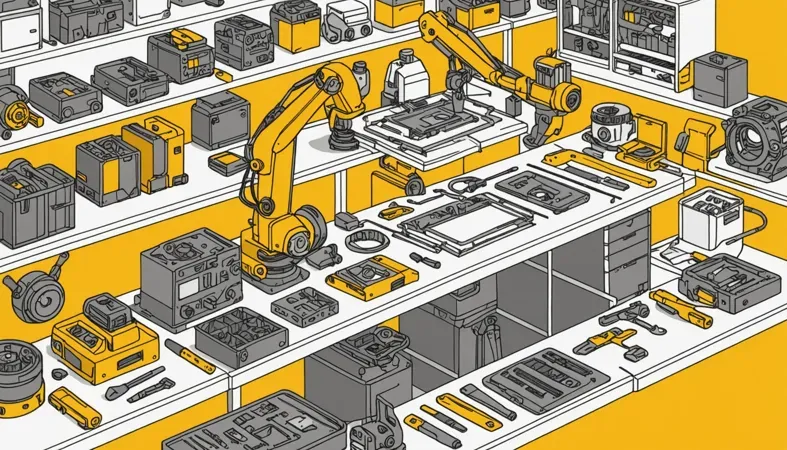
Other Options You Can Consider
When you want to weld but can’t access a traditional welding machine, consider gas tungsten arc welding (GTAW) or MIG welding. These methods, like the Hobart Handler 140 MIG Welder, are favored for their ease of use and portability. If there’s one thing I’ve gained from my journey, it’s that sometimes simpler options save time and money. It’s crucial to stay informed about preventing inhalation of welding fumes to ensure a safer welding experience.
Additionally, submerged arc welding (SAW) offers a clean and efficient way to weld thicker metals with minimal splatter. You might prefer these techniques for specific projects or when working in tight spaces. Always remember, the right tool makes all the difference in your welding experience.
Frequently Asked Questions (FAQs)
Now let us look at some common questions I typically get asked about welding.
How Does a Welding Machine Operate?
A welding machine operates by using electric arc or heat to fuse materials together. The machine converts electrical energy into heat, which melts the base materials, allowing them to join. This process can run at up to 400 amps for heavy-duty tasks, ensuring strong welds. Exposure to fumes and UV radiation during welding raises concerns about health impacts, including the potential risks of welding-related cancer.
What is the Easiest Way to Weld for Beginners?
The easiest way to weld for beginners is through MIG welding. MIG welding is user-friendly because it automatically feeds the filler metal, making it simpler to control. It’s great for thinner materials and perfect for beginners in home projects.
Is the Ground Positive or Negative on a Welder?
The ground on a welder is typically negative. This configuration helps minimize the chance of electric shock and ensures a stable arc. It’s crucial to get this right for safety and proper welding performance.
How to Do Welding Step by Step?
Welding involves several key steps: preparation, setup, welding, and post-weld inspection. Start by cleaning the materials, then adjust your machine settings, and finally weld with steady movements to ensure quality and prevent defects.
How to Use a Welder Machine Safely?
Using a welder machine safely requires to wear protective gear like gloves and a welding helmet. Nearly half of all welding accidents can be prevented by proper equipment, so invest in good quality safety gear and always follow manufacturer guidelines.
Conclusion
Phew, we covered a lot about how to operate a welding machine. We discussed what a welding machine is, different types of welding machines, and the prerequisites for using one. You learned about the steps to operate a welding machine, safety tips, various welding techniques, factors affecting operation, common problems, aftercare, and the benefits of welding.
Hopefully, I was able to impart some of my experience on how to operate a welding machine effectively. Remember, to use a welder machine, you need to set it up properly, turn it on, and adjust the settings based on the job at hand. With the right techniques and a sense of safety, you’ll be welding like a pro in no time.
For further information and in-depth insights, check out What is Welding, where you’ll find a wealth of knowledge on welding techniques, tips, and best practices.
References
- American Welding Society. (2020). AWS A3.0: Standard Welding Terms and Definitions. Miami, FL: AWS.
Joe Carter is a retired welding professional with over 40 years of hands-on experience in the industry, spanning ship repair, structural welding, and even underwater projects. Joe is a master of MIG, TIG, and Stick welding. Passionate about mentoring the next generation of welders, Joe now shares his decades of expertise and practical insights to help others build rewarding careers in welding.
American Welding Society, MIG Welding, Pipe Welding, Safety Tips, TIG Welding, Welding, Welding Machine Operation, Welding Techniques