Can You Use JB Weld on Plastic? A Guide on Techniques and Limitations
Published on: March 9, 2025 | Last modified: March 4, 2025
By: Joe Carter
Plastic is a versatile material made from synthetic compounds. It’s everywhere—from toys to packaging—thanks to its light weight and durability.
Now, can you use jb weld on plastic? It’s crucial to know this because not all plastics bond well. In my experience, I’ve seen people struggle with repairs because they didn’t choose the right adhesive.
In this guide, you’ll learn about types of plastic in relation to JB Weld, steps to use JB Weld on plastic, factors influencing JB Weld application on plastic, and frequently asked questions. Whether you’re asking can jb weld be used on plastic or how to use jb weld plastic bonder, you’ll find your answers right here.
Contents
Can You Use JB Weld on Plastic?
Yes, you can use JB Weld on plastic, but it’s tricky. Because JB Weld is primarily meant for metal, it might not bond well with some plastics. For best results, try JB Weld plastic bonder; clean surfaces and mix as directed.
What is Plastic?
Plastic is a synthetic material made from polymers. It’s formed through polymerization, where small molecules (Monomers) bond together. In 2020, around 359 million tonnes of plastic were produced globally—enough to fill over 1 million Olympic-sized swimming pools!
Regarding using JB Weld on plastic, I’ve tinkered with JB Weld products and found they bond different materials well. When I fixed a cracked plastic car part, the results were surprisingly solid, but I’ll save the full answer for another day!
I’ve heard friends share their success with repairing outdoor furniture using JB Weld. They say applying it makes repairs simple and effective. Many believe that understanding how to use JB Weld plastic bonder can lead to strong, long-lasting fixes. Whether fixing garden chairs or car bumpers, it seems like a reliable option.
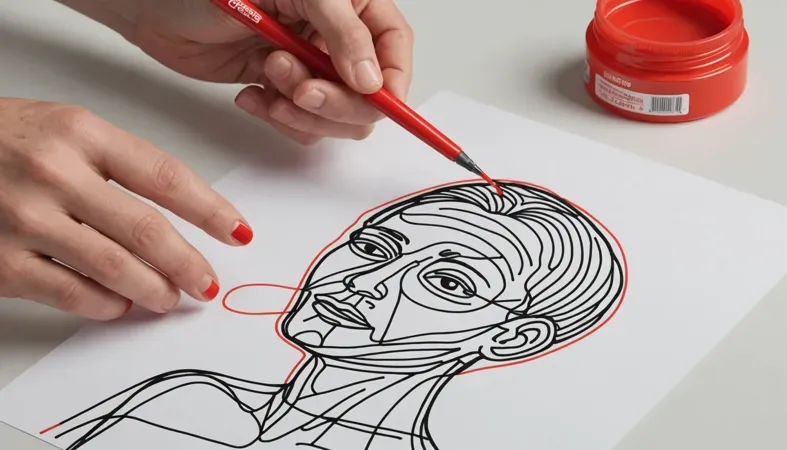
Types Of Plastic in Relation to JB Weld
-
Polyethylene
Polyethylene is a common plastic used in bottles and bags. Unfortunately, JB Weld doesn’t bond well with it. To improve adhesion, clean the surface and roughen it with sandpaper.
-
Polypropylene
Polypropylene is tough and often used in containers and automotive parts. Sadly, it doesn’t bond well with JB Weld. To try bonding, use a primer designed for polypropylene, then apply JB Weld after it dries.
-
Polyvinyl Chloride
Polyvinyl Chloride (PVC) is used in plumbing pipes and vinyl flooring. JB Weld works well on PVC. To use it, clean the surface and apply JB Weld evenly. Allow it to cure for at least 24 hours for best results.
-
Acrylic
Acrylic is a clear, durable plastic used in displays and windows. JB Weld can bond acrylic, but it may cloud the surface. To proceed, lightly sand the area, apply JB Weld, and let it cure completely for 24 hours.
-
ABS Plastic
ABS plastic is strong and used in toys and automotive parts. JB Weld adheres well to ABS. For effective bonding, clean and roughen the surface before applying a generous amount of JB Weld. Let it cure for 24 hours.
That covers the different types of plastic relevant to JB Weld. Let’s now take a look at how to apply JB Weld on plastic.
Steps to Use JB Weld on Plastic
Follow these steps to use JB Weld on plastic successfully for a strong bond!
-
Prepare the Surface
Clean the plastic surface with soap and water to remove dirt and grease. Rinse and dry it. Ensure the area is smooth; you may want to sand it lightly. Aim for surfaces free from oils and residues.
For stubborn residues, use isopropyl alcohol (IPA). Wipe the area thoroughly and let it dry. A cleaner surface creates a better bond. Remember, roughened surfaces add friction, enhancing JB Weld’s grip.
-
Mix the JB Weld
Combine equal parts of JB Weld resin and hardener. You typically need about 1.5 tablespoons (22.5 Ml) of each for small repairs. Use a disposable mixing surface or container. Stir with a small stick for 30 seconds until blended.
When applying JB Weld to galvanized steel, it is crucial to ensure proper safety measures. Galvanized steel involves a protective zinc coating which can cause harmful fumes when welded. To understand why safety precautions are necessary in this context, explore if welding galvanized steel risks.
Be quick but thorough; the epoxy starts curing in about 4 to 6 hours at room temperature (20°C or 68°F). In cooler conditions, it takes longer. Mixing in small batches reduces waste and allows for better control.
-
Apply the JB Weld
Spread the mixed JB Weld evenly onto the prepared surface. Use a small spatula or your gloved finger to ensure good coverage. Fill any cracks or holes completely. A thin layer still provides a strong bond, making it an effective choice for various applications of JB Weld alternatives.
When working with sensitive materials, learning how to weld thin metal can improve techniques for precise applications.
For plastic items under stress, apply enough to fill gaps without overflowing. Letting the epoxy sit for a minute before application thickens it slightly, improving grip on vertical surfaces.
-
Clamp the Parts Together
After applying JB Weld, press the pieces together tightly. Use clamps or weights to hold them in place. For smaller items, rubber bands can work! Ensure the bond is secure for the best chance to adhere well.
Check regularly to ensure they remain in place while curing. For a standard bond, leave it clamped for at least 2 hours or until it sets. No movement will yield the strongest result, so don’t disturb the setup.
-
Allow to Cure
Now comes the waiting game! Allow JB Weld to cure fully before using the joined parts. Full cure can take 15 to 24 hours, depending on temperature and humidity. For best results, I recommend leaving it for 24 hours — patience yields a stronger bond.
For those who are also interested in mastering welding techniques, you may find guidance on how to weld uphill beneficial as it requires understanding complex weld positions and control.
Keep the item in a warm, dry place during curing. Gently warm the area to speed it up slightly, but don’t exceed 28°C (82°F) as heat can compromise the bond. Once cured, your bond should be rock solid!
That covers the procedures for applying JB Weld on plastic. Let’s now take a look at the factors affecting its application.
Factors Influencing JB Weld Application on Plastic
What factors determine JB Weld’s effectiveness on plastic? Here’s a quick rundown.
-
Type Of Plastic
The type and composition of plastic play a significant role. Some plastics, like PVC or ABS, bond better with JB Weld than challenging options like polyethylene or polypropylene, which may repel adhesives due to low surface energy.
-
Surface Preparation
Clean surfaces ensure a strong bond. Scrubbing with isopropyl alcohol (At Least 70% Concentration) or sanding enhances adhesion by increasing the contact area for JB Weld.
-
Environmental Conditions
Temperature and humidity affect the curing process. Ideally, apply JB Weld in temperatures between 50°F and 90°F (10°C to 32°C). Lower temperatures delay curing, potentially leading to weak bonds, while high humidity can cause imperfections. Exploring the factors that lead to porosity in welds can provide a deeper understanding of material bond integrity. Discover more about what causes porosity in welding.
-
Cure Time
The more time you give JB Weld, the stronger the bond. Allowing extra cure time beyond the initial 4-6 hours (For Full Bond Strength at 15°C to 25°C) improves durability, especially under stress. When working with metal surfaces, it’s crucial to apply techniques that ensure a seamless connection in various welding joints, such as the edge joint welding method.
-
Bonding Method
How you apply JB Weld matters. A thicker layer fills gaps but takes longer to cure, while a thin layer adheres quickly but requires more precision.
We’ve wrapped up the factors affecting JB Weld use on plastic. Next up, we’ll look at alternatives for plastic repairs.
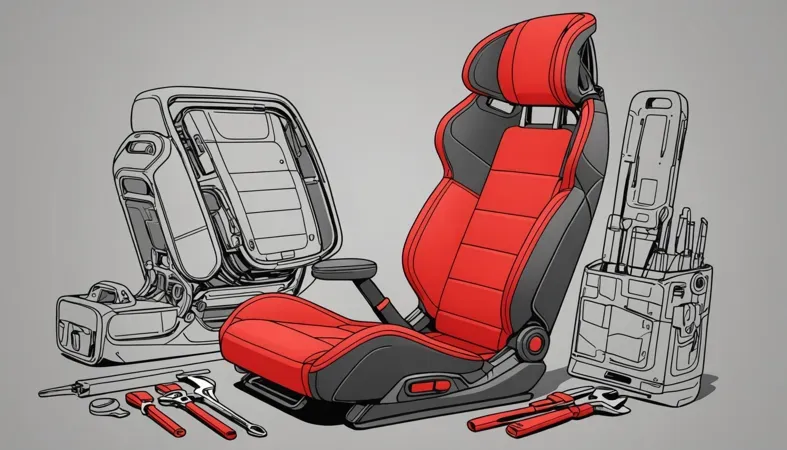
Alternatives to JB Weld for Plastic Repairs
If JB Weld isn’t your go-to for plastic repairs, don’t worry! Here are some alternative adhesives that work well on various plastics.
Adhesive Type | Best For | Cure Time | Strength | Notes |
---|---|---|---|---|
Epoxy | Multiple plastic types | 24 hours | High | Mix resin and hardener; great for strong, permanent bonds. |
Super Glue (Cyanoacrylate) | Small plastic parts | Seconds | Medium | Fast-setting but can be brittle under stress. |
Hot Glue | Lightweight repairs | Minutes | Low | Easy to use but not ideal for high-stress applications. |
Polyurethane Adhesive | Rigid and flexible plastics | 24 hours | High | Strong bond; expand as it cures, filling gaps well. |
Plastic Welding | Selective plastics | Instant (upon melting) | Very high | Use heat to bond plastics; requires skill for best results. |
We covered various alternatives to JB Weld for plastic repairs. Next, we will cover frequently asked questions about these options.
Frequently Asked Questions (FAQs)
Now let us look at some questions I typically get asked about using J-B Weld on plastic.
What Should You Not Use J-B Weld on?
You shouldn’t use J-B Weld on certain materials like flexible plastics. Flexible plastics can’t handle the adhesive’s rigidity. It may not bond effectively, leading to a failure of the joint.
How Long Does J-B Weld Take to Cure on Plastic?
J-B Weld typically takes about 4 to 6 hours to set on plastic. Full cure takes around 15 to 24 hours. Timing varies based on temperature and humidity; warmer conditions speed up curing.
What is the Best Epoxy for Plastic?
The best epoxy for plastic often includes two-part systems like those made for specific plastics. They provide strong bonds and resist harsh conditions, such as heat and moisture. Choose an epoxy that matches your plastic type for best results.
Can J-B Weld Be Used Underwater?
Yes, J-B Weld can be used underwater but only after it cures completely. J-B Weld sets in 4 to 6 hours but it’s best submerged only after 24 hours. This allows it to reach full strength, preventing any bond failure.
How Do You Apply J-B Weld on Plastic?
To apply J-B Weld on plastic, first clean the surfaces well. Mix the resin and hardener, apply it generously, and clamp if needed. A cure time of 15 to 24 hours ensures a strong bond.
Conclusion
We covered various aspects of using JB Weld on plastic, including types of plastic, steps to apply JB Weld, and factors influencing the bond. We also explored FAQs related to whether JB Weld can effectively fix plastic items. The article answered common queries like, “Can you JB Weld plastic?” and “How to use JB Weld plastic bonder?”
So, can you use JB Weld on plastic? Simply put, yes—you can, but it depends on the plastic type. As detailed, not all plastics bond well. For example, a high-strength epoxy like JB Weld works better on hard plastics like ABS. Always check compatibility and follow the application steps for the best results.
If you want to dive deeper and explore more articles like this, visit our homepage at What is Welding for additional expert blogs and valuable welding tips.
Additional Reading
- American Society of Mechanical Engineers. (2019). ASME Section IX: Welding and Brazing Qualifications. New York, NY: ASME.
Joe Carter is a retired welding professional with over 40 years of hands-on experience in the industry, spanning ship repair, structural welding, and even underwater projects. Joe is a master of MIG, TIG, and Stick welding. Passionate about mentoring the next generation of welders, Joe now shares his decades of expertise and practical insights to help others build rewarding careers in welding.
Adhesives, Art, Bonding Techniques, DIY, Jb Weld, Plastic Repair, Safety, Surface Preparation, Welding, Welding Techniques, Welding Tips