What is 2G Welding? Understanding Position, Techniques, and Preparation
Published on: February 21, 2025 | Last modified: March 4, 2025
By: Tyler James
2G welding refers to a specific position where the weld joint lies horizontally, and the welder works from the top side. It’s commonly used for welding pipes and plates.
I regularly hear the question, what is 2g welding? Understanding this position is crucial for achieving strong joints. From my experience, it influences not just the weld’s quality but also a welder’s technique and comfort while working.
In this guide, we’ll cover the basics of 2G welding, explore how it works, discuss the types involved, walk through the preparation steps, and identify the factors that can affect the process. Plus, we’ll tackle questions like what does 2g mean in welding and the specifics of a 2g weld test.
Contents
What’s 2G Welding?
2G welding refers to a horizontal weld position. This technique joins metals with the torch angled horizontally, ensuring gravity aids the weld process. It’s commonly used in pipe welding and structural applications due to its stability and ease of access.
If you’re considering the appropriate equipment for various welding tasks, you may want to explore what size welder you need.
How Does 2G Welding Work?
2G welding refers to a specific welding position, mainly horizontal. In this position, the welder lays the joint flat while the plate remains horizontal. The weld is done from above and often involves materials like steel and aluminum. A typical 2G weld test measures the ability to control heat and filler metal, ensuring a strong joint. Statistics show that over 70% of welded structures use this position for its efficiency.
This welding position showcases several technical skills. Welders often use techniques like stringer beads or weave patterns. Controlling the amperage—usually between 90 to 150 amps—is crucial for maintaining bead shape and avoiding defects.
I recommend practicing in the 2G position if you’re starting out. It’s a great way to build your confidence! A 2G weld test can help you assess your skills in executing horizontal welds effectively.
Types Of 2G Welding
-
Gas Tungsten Arc Welding (GTAW)
GTAW, or TIG welding, uses a non-consumable tungsten electrode. In 2G welding, this method provides strong, high-quality welds on plate positions. To implement GTAW, create an arc between the tungsten electrode and the workpiece while adding filler material as needed.
-
Shielded Metal Arc Welding (SMAW)
SMAW, or stick welding, employs a consumable electrode covered in flux. It’s efficient for various metals in 2G welding, making it versatile. To use SMAW, strike the electrode against the metal, generating heat that melts both the electrode and the base metal.
-
Flux-cored Arc Welding (FCAW)
FCAW uses a tubular wire filled with flux to shield the weld. It’s ideal for construction in 2G welding when speed and penetration are crucial. To perform FCAW, feed the wire into the welding machine, create an arc, and let the flux melt and protect the weld pool from contaminants. Understanding the composition of welding rods is essential for selecting the right materials for your project, and you can explore more about what welding rods are made of.
-
MIG (Metal Inert Gas) Welding
MIG welding employs a wire electrode and an inert gas to protect the weld. In 2G welding, it offers fast speeds and ease of use. To execute MIG welding, feed a continuous wire into the weld pool while the gas shields the area from the atmosphere.
-
TIG (Tungsten Inert Gas) Welding
Similar to GTAW, TIG welding also uses a non-consumable tungsten electrode for high precision. It finds applications in thin metals in 2G welding. To perform TIG welding, keep the arc steady, control the filler wire addition, and maintain a consistent angle for the best results.
We covered the various types of 2G welding techniques here. Next, we will cover the steps needed to prepare for 2G welding.
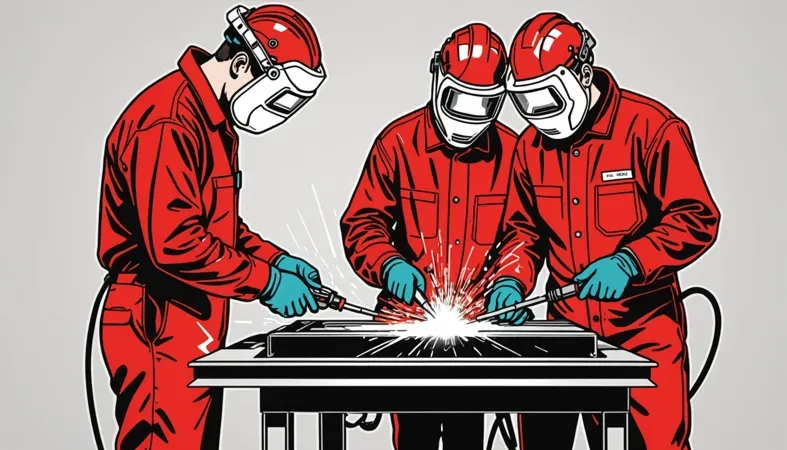
Steps to Prepare for 2G Welding
Here are the essential steps for achieving a solid 2G weld.
-
Set Your Vertical Workpiece
Position your workpiece vertically. This is crucial for the 2G welding position. Ensure it’s stable—any wobbling will affect the weld quality. Use clamps to secure it; good clamps really keep everything tight.
Mastering vertical welding is essential for achieving optimal results in projects requiring this technique, and to learn more about how to weld vertical, refer to this comprehensive resource on how to weld vertical.
Check that the joint fits snugly. A proper fit reduces the chances of inclusions or defects. Aim for a gap of about 1/8 inch (3.2 Mm) when welding thick metal. A consistent gap improves penetration.
Sometimes welding isn’t necessary for joining metals effectively. Explore methods to bond metal to metal without welding for a seamless finish.
-
Adjust Your Welder Settings
Set your welder’s voltage and amperage based on the metal thickness. For carbon steel, start with around 70-100 amps. Higher amperage can cause burn-through, while too low might result in weak welds. For detailed instructions on settings and techniques, it’s important to monitor the heat—aim for a nice bead. This can help ensure you achieve effective welding guidance.
To better understand the role of direct current electrode positive, you can explore more about what DCEP means in welding.
Thickness matters! For thinner metals, reduce the settings to prevent warping. Test on a scrap piece first to avoid mistakes—don’t go in blind.
-
Establish Welding Speed
Begin with a steady speed and maintain a consistent arc length. A typical travel speed for 2G welding is about 5-12 inches per minute (12.7-30.5 Cm/min). Adjusting your speed can significantly affect penetration and bead width; experiment until it feels right. Understanding various welding methods can enhance these techniques and help improve overall efficiency, different types of welding demonstrate unique advantages.
If you’re too fast, you might end up with insufficient fusion. Too slow? You’ll see excessive buildup and possible burn-through. It might take a few practice runs, so don’t hesitate! Find that sweet spot!
-
Persevere With Your Technique
Maintain a steady hand for consistency. In the 2G position, I prefer the weave technique, moving the torch back and forth to create a wider bead. Keep an even pressure—like painting a wall with consistent strokes!
Visualize your weld pool while working and maintain a clear view. Remember, practice makes perfect! If you’re unsure, turn it down slightly and take your time until you’re comfortable.
We covered the steps to prepare for 2G welding. Next, we will cover the factors influencing 2G welding.
Factors Influencing 2G Welding
What factors influence the 2G welding process and its outcomes?
-
Material Thickness
Material thickness affects penetration depth. Thicker plates (Over 1 Inch or 25.4 Mm) require more heat and slower speeds to achieve solid welds.
-
Welding Position
The 2G position means welding horizontally. This position can be tricky, requiring skill to prevent sagging or inconsistent beads.
-
Electrode Type
I recommend using E7018 electrodes for their ease of use and good arc stability. Variations like E6010 also perform well for different applications, impacting weld quality and penetration.
-
Welding Speed
Welding speed directly affects heat input. Slower speeds increase heat, which can lead to burn-through or distortion in thin materials.
-
Heat Input
High heat input can improve fusion but may cause issues like warping. A heat input range of 10-25 kJ/m (3.8-9.6 Kj/ft) is recommended for optimal results in 2G welding.
We have now covered the factors affecting 2G welding. Next, we will examine the advantages of 2G welding.
Benefits of 2G Welding
Understanding the benefits of 2G welding can elevate your skills.
-
Efficiency
2G welding enhances efficiency. With a horizontal position, you can work faster, reducing the time it takes to complete a weld.
-
Access
This position grants better access for the welder. You can see the joint clearly, helping to maintain bead control.
-
Strength
Welds made in the 2G position often have excellent fusion. Gravity assists during the welding process, leading to stronger joints.
-
Versatility
It’s great for various materials. Whether you’re welding steel or aluminum, the 2G position works well.
-
Skill Development
Practicing in the 2G position builds your overall welding skills, preparing you for more complex positions in the future.
We’ve wrapped up the advantages of 2G welding here. Next up, we’ll look at comparing different welding positions.
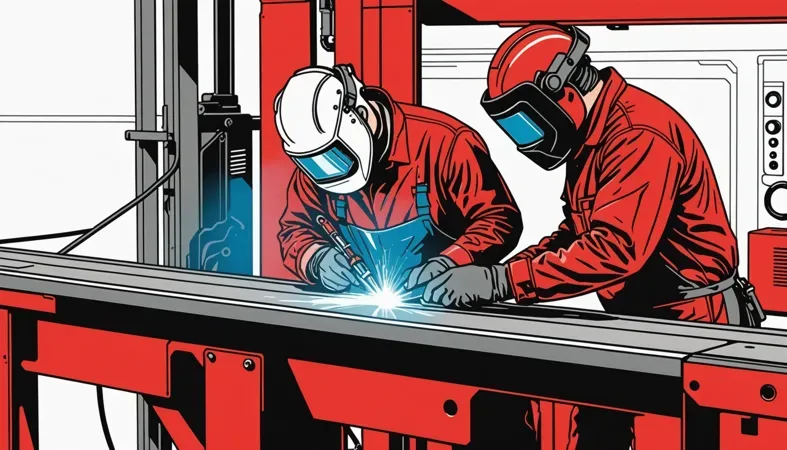
Comparison of Welding Positions
Position | Difficulty Level | Common Applications | Recommended Techniques |
---|---|---|---|
2G | Intermediate | Pipes, structural elements | Weave, stringer beads |
3G | Advanced | Vertical joints | Upward techniques |
4G | Expert | Overhead joints | Precision control required |
5G | Advanced | Pipes in fixed position | Rotary techniques |
Frequently Asked Questions (FAQs)
Here are some questions I typically get asked about welding.
What Does 2G Mean in Welding?
2G in welding means the horizontal welding position. This position is critical as it affects weld quality and is often used for pipe welding. In this position, welders typically have gravity working against them, requiring skill to maintain a weld bead. Discover the versatility of machines like a multi-process welder to maximize efficiency and adaptability in various welding positions.
What is a 2G Weld Test?
A 2G weld test evaluates a welder’s ability to perform in the 2G position. It often involves welding plates or pipes horizontally during inspections. Two levels of difficulty exist: a basic test and an advanced test, impacting certification and job opportunities.
What is 5G in Welding?
5G in welding refers to the fixed vertical position, usually for pipe welds. Welders face challenges with bead alignment, making technique vital. Achieving a proper bead can significantly impact the integrity and strength of the weld joint. Understanding different types of welds is crucial, especially when it comes to utilizing groove welds effectively.
What is 3G in Welding?
3G in welding means the vertical welding position. This position helps welders practice upward techniques, which impact strength and penetration. It’s often a requirement for certifications and job performance in structural applications.
What Does the G Stand for in 2G in Welding?
The ‘G’ in 2G welding stands for ‘position.’ This system includes various welding positions like flat, horizontal, vertical, and overhead. Understanding positions helps welders choose the right technique, essential for skill development and job success.
Conclusion
We’ve made it to the end, and I hope it was helpful. We covered what 2G welding is, how it works, different types, preparation steps, and factors that influence it. We also addressed common questions about what 2G means in welding, the 2G position, and weld tests.
So, what is 2G welding? In simple terms, it’s a horizontal welding position. It involves laying the pipe or metal in a fixed position and welding along a single joint. Wishing you success in your welding projects and remember, understanding these details can really enhance your skills in the 2G welding process.
If you’re eager to learn more and dive deeper into the world of welding, feel free to visit What is Welding, where you can find a wealth of resources related to all aspects of welding.
Additional Reading
- National Fire Protection Association. (2022). NFPA 51B: Standard for Fire Prevention During Welding, Cutting, and Other Hot Work. Quincy, MA: NFPA.
- Lincoln Electric. (2020). The Procedure Handbook of Arc Welding (15th ed.). Cleveland, OH: Lincoln Electric Company.
Tyler is a passionate DIY welder and self-taught metal artist with years of hands-on experience transforming raw materials into functional and artistic creations. Specializing in MIG welding, Tyler crafts everything from custom furniture to outdoor sculptures, blending creativity with technical skill. Committed to making welding accessible, Tyler shares practical insights and project inspiration to help beginners and hobbyists confidently explore the world of metalworking.
2G Welding, Horizontal Welding Position, MIG Welding, Pipe Welding, Types Of Welds, Welding, Welding Preparation, Welding Skills, Welding Techniques, Welding Types