What is a Groove Weld? Exploring Types, Applications, and Quality Factors
Published on: March 14, 2025 | Last modified: March 4, 2025
By: Joe Carter
A groove weld is a type of welding joint that connects two pieces of metal at their edges. It’s commonly used for its strength and efficiency in joining thicker materials.
I get asked all the time, what is a groove weld? Knowing this plays a huge role in ensuring strong connections in various projects. From my experience, proper groove welds can really boost structural integrity and simplify repairs down the line.
In this guide, we’ll explore how a groove weld works, different types of groove welds, steps to create them, factors influencing their quality, common issues you might face, aftercare, inspection, and advanced tips. We’ll also discuss use cases, alternatives to groove welding, and answer frequently asked questions. Plus, we’ll touch on related concepts like what is groove welding and what is groove angle in welding.
Contents
- What is a Groove Weld?
- How Does a Groove Weld Work?
- Types Of Groove Welds
- Steps to Create a Groove Weld
- Understanding Groove Weld Dimensions
- Factors Influencing Groove Weld Quality
- Common Issues You Might Encounter
- Aftercare, Inspection, and Advanced Tips for Groove Welds
- Use Cases Of Groove Welds
- Alternatives for Groove Welding
- Frequently Asked Questions (FAQs)
- Conclusion
- References
What is a Groove Weld?
A groove weld fills a joint between two pieces of metal. It uses a specific shape, like a V or U, to ensure strong bonds. You often find these in heavy-duty structures because they provide excellent strength and support. For welders looking to adapt their equipment based on power requirements, information on how a 220 welder can be converted to 110 can be particularly beneficial.
How Does a Groove Weld Work?
A groove weld joins two pieces of metal by creating a V or U-shaped groove along their edges. The groove angle typically ranges from 60° to 90° (1.05 To 1.57 Radians). To ensure full penetration, the groove depth should match the material thickness, usually 0.8 times its thickness in millimeters (2/3 Of Its Thickness in Inches).
In groove welding, you can use filler metal to fill the joint and stabilize the bond, which strengthens the connection by forming a thicker weld bead in high-stress areas. The groove’s dimensions significantly impact the weld’s strength and durability.
It’s crucial to get the groove dimensions right. Measuring groove welds can prevent weak joints that might lead to failures. A square groove weld design is often the most effective method as it provides solid edge contact, enhancing strength.
Types Of Groove Welds
What are the types of groove welds?
-
Butt Groove Welds
Butt groove welds join two pieces of metal end-to-end. This type uses a beveled edge to create a stronger joint. Prepare the edges with a 37.5° angle using a cutting torch before welding for an optimal fit. When selecting an appropriate electrode, understanding classification specifics like electrode classification E316-16 can significantly influence welding outcomes.
-
Corner Groove Welds
Corner groove welds strengthen the corners of structures. This method involves welding two pieces where they meet at right angles. Brace the materials at a 90° angle, then apply the weld into the corner for stability.
-
Edge Groove Welds
Edge groove welds connect two metal pieces along their edges. They’re often used with thicker materials and require a beveled edge. Ensure the edges are clean and angled before aligning and welding along the edge.
Choosing the right welding machine for such tasks can significantly enhance the quality of your welds. For advice on selecting the best welding machine, consider factors like power output, ease of use, and compatibility with different materials.
-
V-groove Welds
V-groove welds use a V-shaped groove to create a joint. They’re ideal for thicker metals needing strong connections. Form a V angle of about 60° on the edges, ensuring a snug fit before applying heat. For consistent results in such welds, it’s beneficial to understand the capabilities of a DC inverter welding machine.
-
J-groove Welds
J-groove welds create a semi-circular notch for better penetration. This method is great for load-bearing applications. Cut a J shape on the edges to allow for deep penetration when welding.
That covers different groove weld types. Let’s now take a look at the steps for creating a groove weld.
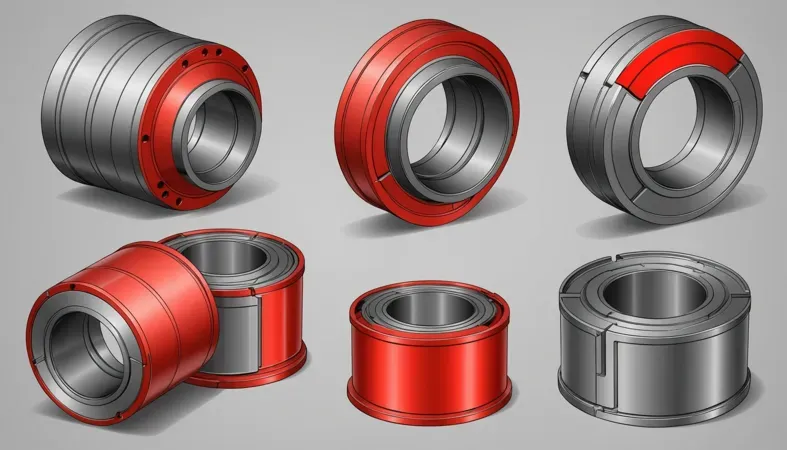
Steps to Create a Groove Weld
Here are the steps to successfully make a groove weld.
-
Prepare the Base Material
Clean the base metals thoroughly before welding. Use a grinder or wire brush to remove contamination, like paint, rust, or oil. A clean joint avoids defects and saves you headaches later!
Check the joint’s fit-up. Ensure parts sit flush against each other. A tight fit helps the weld pool form correctly and maximizes structural integrity. Aim for a gap of 1/16 inch (1.6 Mm) or less for ideal conditions.
-
Select the Proper Filler Material
Choose a filler rod that matches the base metal’s properties. For example, if you’re working with mild steel, opt for ER70S-6 filler for a strong joint. Use a filler size that fits the groove angle—typically, 3/32 inch (2.4 Mm) works well for many applications. The type of groove weld may dictate specific filler choices.
Consider the groove angles to match with the filler rod. A V-groove usually requires a matching filler for optimal penetration. Mixing fillers can lead to weak welds, so stick with compatible materials!
-
Set Up the Welding Equipment
Adjust electrode settings according to material thickness. For instance, a 0.035-inch (0.89 Mm) electrode works well for materials up to 1/4 inch (6.35 Mm) thick. Set voltage and amperage as per the manufacturer’s guidelines. This ensures proper arc and flow during welding. Understanding concepts like the meaning of DCEP can enhance your welding technique.
Check gas flow settings if using MIG welding. A flow rate of 15 to 25 cubic feet per hour (CFH) is usually adequate. Proper nozzle calibration is crucial; incorrect settings can lead to poor bead appearance and increase the risk of porosity.
-
Execute the Welding Process
Begin welding with a consistent travel speed. For a groove weld, aim for about 8 to 12 inches per minute (203 to 305 Mm/min) depending on the thickness and type of groove. Keep the torch at a 10 to 15-degree angle toward the direction of travel, as recommended in the welding fundamentals. This improves penetration and bead shape.
For those exploring various techniques and their applications, consider reviewing the different types of welding.
Move your hand smoothly. Any jerks can cause uneven beads or undercuts. I’ve experienced how inconsistent beads can lead to project rework—forming good habits results in better outcomes!
-
Inspect the Finished Weld
Examine the bead for uniformity and penetration once you’re done. Look for even width and height without cracks or undercuts. A 1/16 inch (1.6 Mm) excess of bead height can be acceptable. Catching flaws early saves time later on.
If you spot issues, rework them immediately—don’t leave it for later! The sooner you fix it, the better the overall outcome in the long run.
We’ve wrapped up the steps for creating a groove weld here. Next up, we’ll look at groove weld dimensions.
Understanding Groove Weld Dimensions
Groove weld dimensions are crucial for achieving quality welds. Here’s a closer look at how to specify and work with them.
Dimension Type | Typical Range | Importance |
---|---|---|
Groove Angle | 60° – 90° | Influences penetration and joint strength. Wider angles can enhance access for welding. |
Groove Depth | Minimum 0.8 x Material Thickness | Ensures full penetration, critical for heavy-duty applications. For example, a 10 mm (0.4 in) thick plate needs a groove depth of at least 8 mm (0.32 in). |
Bead Width | 1.5 – 2 times the electrode diameter | Wider beads can improve weld strength but may introduce heat distortion. Aim for a balanced approach. |
Travel Speed | 8 – 12 inches per minute (203 – 305 mm/min) | Choosing the right speed prevents defects like undercutting or poor penetration. |
By understanding these dimensions, you can significantly improve the quality and performance of your groove welds. Whether you’re working on structural projects or intricate fabrications, precise measurements help ensure durable and effective joints.
You should now have a good understanding of groove weld dimensions and their significance. In the next part, we’ll discuss factors affecting weld quality.
Factors Influencing Groove Weld Quality
What factors influence groove weld quality and performance?
-
Material Thickness
Thick material needs deeper penetration for proper fusion. For example, with 10 mm (0.4 In) material, a groove weld’s depth should match that thickness to avoid lack of fusion.
-
Welding Position
The welding position—flat, horizontal, or vertical—affects the technique. For instance, a vertical groove weld can cause slag buildup if not done accurately.
-
Welder Experience Level
Skilled welders master control over the arc, heat settings, and travel speed. These elements crucially affect the size and quality of a groove weld, especially with variable groove angles.
-
Welding Technique Used
Different techniques, like stringer beads versus weave patterns, impact weld integrity. For example, V-groove and U-groove welds require specific approaches for proper fill and penetration.
-
Environmental Conditions
Wind, moisture, and temperature can significantly affect a groove weld. Extreme conditions may lead to incomplete fusion or porosity, compromising overall weld quality.
That covers the elements affecting groove weld quality. Let’s now take a look at frequent problems you may encounter.
Common Issues You Might Encounter
Let’s look at some specific problems related to groove welds.
-
Incomplete Fusion
Incomplete fusion occurs when the base metal doesn’t fully join with the filler. Check for gaps or incomplete melting at the joint. To fix it, increase heat and adjust travel speed for better penetration.
-
Cracking
Groove welds can crack, especially if not cooled properly. It’s critical to observe uniform heating and cooling to prevent this. Look for visible cracks and adjust preheat and control post-weld cooling to resolve the issue.
Mastering these techniques helps in reducing the risk of defects such as crater cracks, which often occur when improper cooling practices are followed. You can explore more about what causes crater cracks in welding to further understand this issue.
-
Excessive Heat-affected Zone
A wide heat-affected zone (HAZ) can damage adjacent metal and weaken integrity. Identify it by examining hardness variations. Reduce the HAZ by using lower heat input during welding.
-
Poor Penetration
Poor penetration means inadequate melting into the base material. Inspect for uneven surfaces. Improve this by adjusting your groove angle and ensuring proper arc stability.
-
Weld Porosity
Poor penetration means inadequate melting into the base material. Inspect for uneven surfaces. Improve this by adjusting your groove angle and ensuring proper arc stability.
Aftercare, Inspection, and Advanced Tips for Groove Welds
Here are some essential aftercare, inspection techniques, and expert tips specific to groove welds.
Aftercare Guidelines
After groove welding, cool the joint naturally; avoid water quenching. Clean up immediately—use a wire brush to remove scale, slag, and debris. Store welded parts in dry areas to prevent rust or corrosion, ideally at temperatures below 70°F (21°C) and 50% humidity.
Inspection Suggestions
Inspect welds at 100x magnification for micro-cracks and metal integrity. Use ultrasonic testing devices to measure depth in thicker materials; aim for a compliance error below 5%. For reliable results, consider using a brand like Sonatest.
Expert Recommendations
If you’re experienced, preheat base materials to 30-50°F (16-27°C) of the specified interpass temperature. Optimize parameters; manage travel speed and limit molten pool size to reduce defects. Also, use a specialized welding electrode, like E7018, for better handling on varying thicknesses during challenging overhead applications.
Use Cases Of Groove Welds
People use groove welds for heavy-duty structures. They have many applications, such as:
- Bridges: Groove welds provide exceptional strength for structural joints due to their penetration capabilities. They’re popular for supporting heavy loads.
- Pipelines: They’re extensively used to join pipes. The deep penetration creates a watertight seal, essential for safely transporting fluids.
- Shipbuilding: Groove welds are crucial for hull and frame joints in this industry. They maintain integrity against harsh marine environments.
- Steel Fabrication: Common in fabrication shops for assembling steel components. Their reliability and strength make them a preferred choice in manufacturing processes.
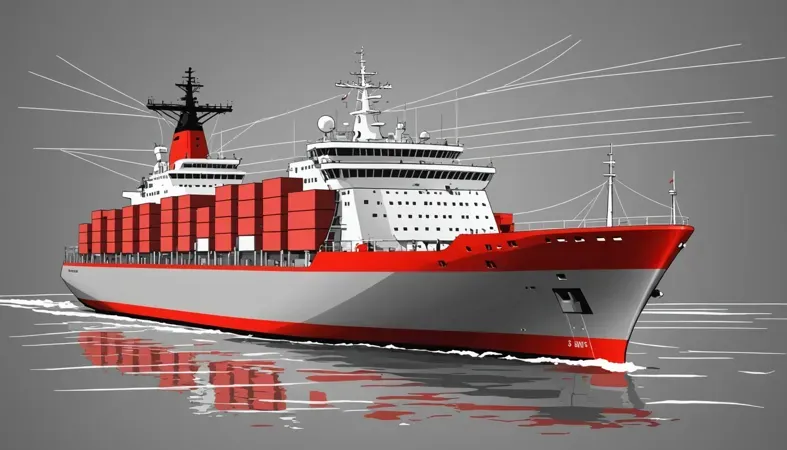
Alternatives for Groove Welding
There are several alternatives to groove welding that can achieve similar results. Techniques like butt welding or fillet welding can be preferred in tight spaces or for certain joint types. Products such as Lincoln Electric’s Super Arc can also help ensure a strong bond when groove welds aren’t practical.
Additionally, you might consider using adhesives or TIG welding for specific applications. For instance, TIG machines from Miller, like the Multimatic 215, provide precise control over heat input, making them great for thinner materials. Switching methods can lead to excellent results while adapting to your project’s unique needs.
Frequently Asked Questions (FAQs)
Now let us look at the most common questions I typically get asked in the welding world.
What’s the Difference Between a Fillet and a Groove Weld?
The difference between a fillet and a groove weld lies in their shapes and applications. Fillet welds are triangular, joining two surfaces, often at right angles, while groove welds involve a prepared edge for better penetration. Groove welds are used for thicker materials and generally have a higher strength rating.
What is a Square Groove Weld?
A square groove weld is a type of groove weld where the edges of the joint are perpendicular to the base metal. This design enhances penetration and strengthens the joint. Typically, a square groove allows for full fusion, making it ideal for heavy structural applications.
What is the Groove Angle in Welding?
The groove angle in welding refers to the included angle between the two edges of the joint. Typically, this angle ranges from 60° to 90° depending on the materials and weld requirements. Proper groove angles improve weld quality by facilitating better molten metal flow. For those interested in the detailed processes involved in fabrication, exploring the metal fabrication and welding techniques can be quite beneficial.
How Are Groove Welds Measured?
Groove welds are measured by their dimensions and penetration depth. The width and height are crucial; common full penetration welds may require up to 5 mm (0.2 In) depth in steel. Accurate measurements ensure that the weld meets strength and quality specifications.
What Are Single Groove Welds With Metal Backing Used for?
Single groove welds with metal backing are often used for deep or narrow joints. The metal backing plate helps support the weld pool, reducing distortion. This approach is beneficial in thick plate applications and can speed up the welding process.
Conclusion
We covered groove welds, how they work, the types available, the steps to create them, and factors that influence their quality. We also talked about common issues you might encounter and the aftercare, inspection, and tips for better results. Lastly, we reviewed use cases and alternatives for groove welding.
In summary, a groove weld is a method of joining metal pieces using a joint preparation that allows for a larger weld area. It often involves angles and configurations like square groove welds, ensuring strong and reliable joints. Happy welding when you work on your groove welds, and remember, these techniques make your projects more resilient.
For additional insights on welding techniques and best practices, feel free to explore What is Welding.
References
- Parmar, R. S. (1997). Welding Engineering and Technology. New Delhi, India: Khanna Publishers.
- American Petroleum Institute. (2018). API 1104: Welding of Pipelines and Related Facilities. Washington, DC: API.
Joe Carter is a retired welding professional with over 40 years of hands-on experience in the industry, spanning ship repair, structural welding, and even underwater projects. Joe is a master of MIG, TIG, and Stick welding. Passionate about mentoring the next generation of welders, Joe now shares his decades of expertise and practical insights to help others build rewarding careers in welding.
Groove Weld, Manufacturing Processes, Metal Joining Techniques, MIG Welding, Structural Integrity, Types Of Welds, Welding, Welding Quality, Welding Technique, Welding Techniques