What is Stellite Welding? Explore Process, Types, and Applications
Published on: November 18, 2024 | Last modified: March 4, 2025
By: Joe Carter
Stellite welding is a specialized process used to apply tough, hard coatings to metal surfaces. It’s vital for enhancing wear resistance and extending the lifespan of components.
One question I was asked a lot is, what is stellite welding? It’s important because it significantly improves the wear and tear your equipment faces. In my experience, using stellite has saved me time and money, reducing the need for frequent repairs.
In this guide, I’ll cover what stellite welding is, how it works, the different types available, essential steps for effective application, factors that can affect the process, common issues, tips for aftercare and inspection, typical applications, and other options to consider, including what is a welding stinger.
Contents
- What is Stellite Welding?
- How Does Stellite Welding Work?
- Types Of Stellite Welding
- Steps for Stellite Welding
- Factors Affecting Stellite Welding
- Typical Issues With Stellite Welding
- Aftercare, Inspection, and Advanced Tips for Stellite Welding
- Typical Applications Of Stellite Welding
- Other Options You Can Consider
- Frequently Asked Questions (FAQs)
- Conclusion
- References
What is Stellite Welding?
Stellite welding uses a cobalt alloy to create strong, wear-resistant surfaces. The alloy can withstand high temperatures and corrosion, making it perfect for heavy-duty applications like turbine blades. It’s often used in aerospace and energy sectors.
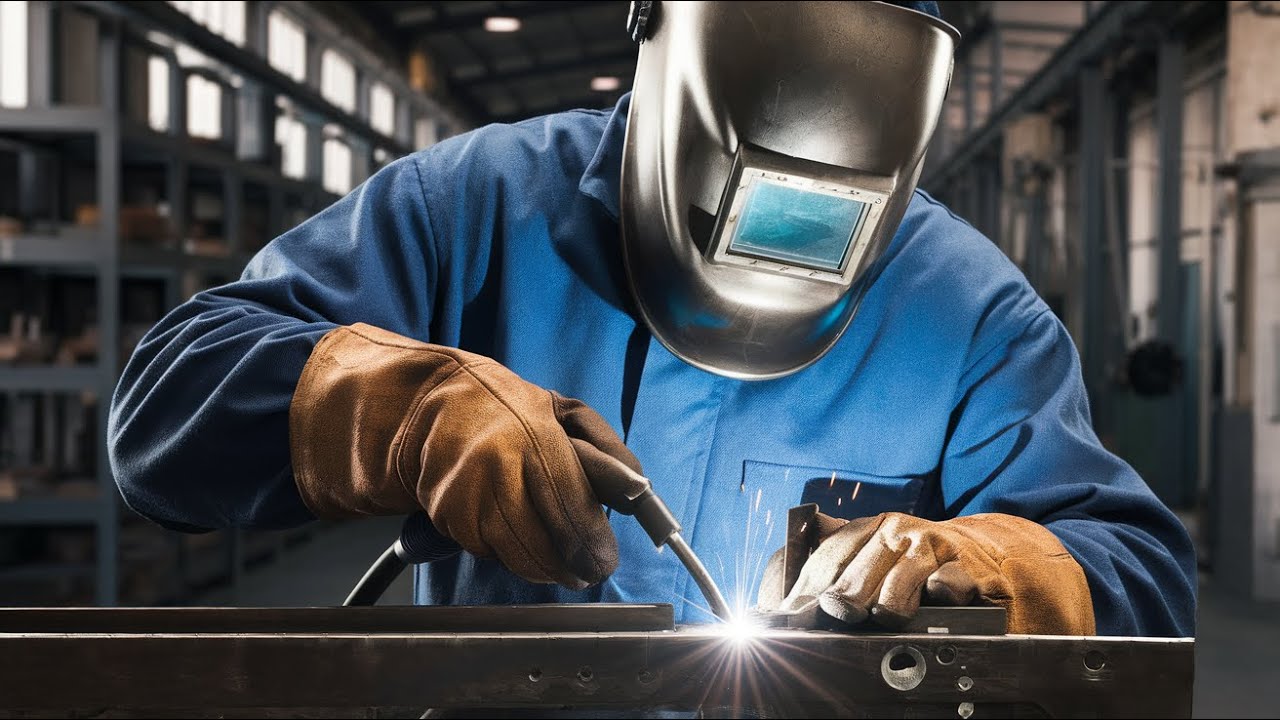
How Does Stellite Welding Work?
Stellite alloys to metal surfaces to improve wear resistance and corrosion protection. Stellite is a cobalt-chromium alloy known for its high melting point of about 1,500°C (2,732°F). This technique typically uses a stinger, an electrode that transfers the welding material. High heat fuses the Stellite alloy to the underlying metal, creating a strong surface.
Technically, Stellite welding uses filler materials primarily made of Stellite 6, which consists of about 58% cobalt, 28% chromium, and 5% tungsten. This durable combination provides excellent abrasion and erosion resistance.
I’ve been down this road before and can say Stellite welding is a game changer for high-wear applications. In my last project, I used a Stellite 6 welding rod for turbine components, and the finish was impressive. It’s crucial to understand the stinger’s role in this process, as proper use ensures reliable results and reduces spatter.
Types Of Stellite Welding
What are the types of stellite welding?
-
Gas Tungsten Arc Welding
This method uses a non-consumable tungsten electrode to join metals. In stellite welding, it provides an excellent finish and control. You create an arc between the tungsten and the base metal, then introduce a filler rod, often a Stellite 6 rod, to achieve a strong bond. When welding different metals, it’s crucial to understand potential hazards such as dangers of welding galvanized steel.
-
Plasma Arc Welding
This technique generates a high-temperature plasma arc for welding. It’s especially useful for stellite welding due to its precision. You ionize the gas passing through a nozzle to create a powerful arc that melts the metal, allowing fine control over your weld, which is a hallmark of specialized welding.
Understanding the significance of electrode classification can enhance the quality of your welds, especially E316-16 classification details.
-
Submerged Arc Welding
This process uses a continuously fed electrode beneath a layer of flux. It’s effective for thicker materials in stellite welding. Ensure the arc is submerged in the flux, which keeps contaminants away and enhances weld quality. If you’re dealing with residual heat effects, understand welding burns on skin.
-
Shielded Metal Arc Welding
This common method uses a consumable electrode coated in flux. It’s effective for stellite welding in various positions. You strike an arc between the electrode and the base material, and the flux coats the weld, preventing oxidation while cooling. Understanding the different welding processes can provide deeper insights into techniques like this one.
Understanding the role of shielding gases is crucial in welding because they protect the weld from atmospheric contamination and influence weld quality. Learn more about what gas is used for welding.
-
Electron Beam Welding
This process uses a focused beam of electrons in a vacuum to melt metals. It’s ideal for stellite welding due to its deep penetration. Create a vacuum chamber, generate an electron beam, and direct it onto the metals to form a precise and strong joint. A welder must also ensure that their equipment is correctly adjusted to protect their vision and improve accuracy, such as adjusting a welding helmet.
We’ve wrapped up the different types of Stellite welding here. Next up, we’ll look at the steps for Stellite welding.
Steps for Stellite Welding
Follow these stellite welding steps closely!
-
Select Materials
Begin by selecting the right stellite alloy for your project. Stellite 6 is popular due to its excellent wear and corrosion resistance, making it ideal for tooling. Check compatibility with the base metal; using the wrong materials can lead to poor adhesion. Examine the chemical composition to match job requirements. For example, Stellite 6 contains about 60% cobalt, 28% chromium, and 6% tungsten.
-
Prepare Surface
Clean the surface thoroughly before welding. Remove rust, grease, and contaminants using a grinder or sandblaster for a clean, rough surface finish. Aim for a surface roughness of at least 0.25 mm (0.01 Inches) to improve bonding. Without proper preparation, you risk weak joints and premature failure. It is crucial to understand the dangers of welding without adequate protection, and one must be aware of welding without a mask.
-
Choose Electrode
Choose the right stellite welding rod based on your application. The amperage (Åmperes) depends on the material thickness; typically, set your machine to 50-120 A for most applications. I’ve noticed that too low a current leads to poor deposits. Always refer to the manufacturer’s specifications; for example, use Stellite 6 rods for gaps less than 3 mm (0.12 Inches).
-
Set Equipment
Set up your welding equipment correctly. Adjust the parameters: use carbon dioxide (CO2) shielding gas at a coverage rate of about 12-18 L/min. Fine-tune your travel speed and arc voltage to match rod thickness, as this can impact weld bead quality. Ensure the settings align with your joint type for optimal performance.
-
Execute Welding
Start welding by maintaining a steady hand for a consistent weld pool. Use a weaving motion if necessary to control heat input; aim for a speed of 150-300 mm/min (6-12 Inches/min) to achieve good penetration. Monitor the bead appearance closely; uniform color indicates proper technique. After welding, let it cool slowly to avoid cracking. If you’re interested in creating your own welding equipment, consider exploring how to make an arc welder with a microwave transformer.
So far in this section we covered the steps involved in stellite welding. In the next section we will talk about the factors that influence stellite welding.
Factors Affecting Stellite Welding
What factors influence performance and quality in stellite welding?
-
Material Composition
The material used in stellite welding greatly affects its properties. For instance, Stellite 6 consists of about 60% cobalt, 30% chromium, and smaller amounts of tungsten and carbon. This mix significantly boosts wear resistance and hardness.
-
Welding Technique
The technique you choose, such as TIG or MIG, can dramatically change the results. Each method has specific requirements; for example, TIG welding needs precise control, which impacts how the filler material enters the weld pool.
-
Temperature Control
Temperature control is crucial! If the weld pool gets too hot (Above 1,500°C or 2,732°F), it can cause unnecessary dilution, compromising strength. Maintaining proper heat input helps achieve uniform hardness.
-
Coating Thickness
The thickness of the stellite coating plays a key role in performance. A thicker coating offers better wear resistance but requires more specific welding parameters. For example, a 0.5 mm (0.02 Inch) thick layer enhances durability for high-stress applications.
-
Welding Speed
Your welding speed affects the bead profile and penetration depth. A slower speed may increase fusion but risks overheating, while a faster speed could lead to poor bonding. Aim for a balanced approach based on your equipment and materials.
We covered the factors influencing Stellite welding techniques. Next, we will cover common problems encountered during Stellite welding.
Typical Issues With Stellite Welding
Now, let’s look at unique challenges with stellite welding.
-
Adhesion Problems
Stellite welding can suffer from poor adhesion. Look for distinct layers where the metal doesn’t bond. Fix this by ensuring the surface is clean—aim for less than 0.1 mm (0.004 In) oxide removal!
-
Cracking During Cooling
Cracks often form during cooling in stellite welding. Watch for visible cracks or a dull surface. The solution? Slow the cooling process using heat blankets or controlled airflow.
-
Inconsistent Weld Quality
Stellite welding might display variable bead width or penetration. Look for uneven surfaces. Improve consistency by maintaining a steady travel speed, typically 12-15 in/min (30-38 Cm/min). Keep your movement steady!
-
Thermal Distortion
Thermal distortion can warp base metals. Watch for bending or lifting along edges during or after welding. Use multi-pass techniques and cooler temperatures to control heat input.
-
Porosity in Welds
Porosity can introduce tiny holes in welds. These may appear during inspection or weaken the weld. Resolve this by ensuring clean gas coverage—argon levels should be >=98%!
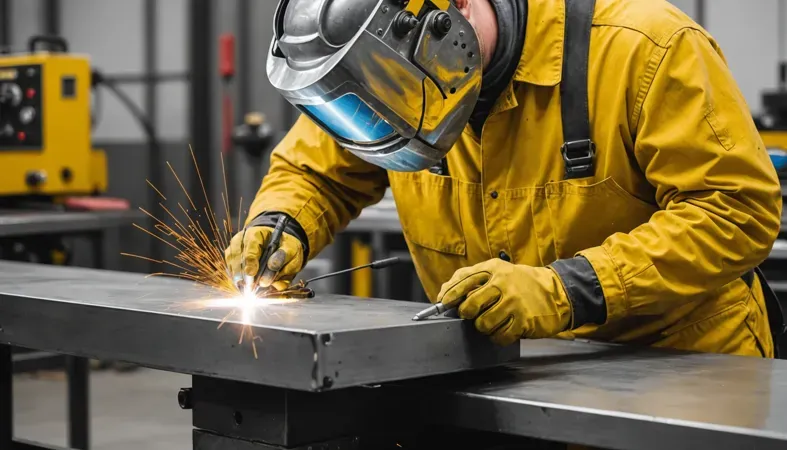
Aftercare, Inspection, and Advanced Tips for Stellite Welding
Here are essential aftercare, inspection, and advanced tips for stellite welding to enhance your results.
Aftercare Tips
After stellite welding, cool your weld quickly, but avoid thermal shock. Use a water-cooled jig at about 23°C (73°F) to reduce distortion. Maintain a clean surface by wiping with a solvent like acetone; contaminants can compromise your weld’s integrity.
Inspection
Inspect the weld using a portable ultrasonic thickness gauge, such as GE’s USM-36. Measure at 10 mm (0.4 In) intervals around the weld joint to check the integrity of the Stellite layer. These gauges provide accurate feedback on delamination or material loss.
Expert Tips
Adjust the arc length to about 4 mm (0.16 In) for optimal penetration. Use a preheat treatment between 150°C and 300°C (300°F to 570°F) to reduce residual stress. Controlling travel speed, ideally between 1.5 and 3 IPM (38 to 76 Mm/min), can significantly improve the final quality.
Typical Applications Of Stellite Welding
Stellite welding is known for its durability and heat resistance. Here are some common uses:
- Aerospace Components: Used for turbine blades to withstand extreme temperatures and reduce wear.
- Oil & Gas Industry: Ideal for valve seats and pumps, offering exceptional corrosion resistance in sour environments.
- Mining Equipment: Applied to cutting tools and drill bits, enhancing lifespan and performance in harsh conditions.
- Medical Devices: Perfect for surgical instruments, ensuring sharpness and durability, crucial for precise operations.
Other Options You Can Consider
Several alternatives can achieve results similar to stellite welding. For instance, you might look into using coatings like tungsten carbide or chrome carbide, which offer excellent wear resistance. These options are often preferred for cost-effectiveness or when working with materials that demand a gentler touch.
I’d like to share what has consistently worked for me as well. Products like the Stellite 6 filler rod or even the Thermal Spray method can yield impressive results depending on your project requirements. Each method has its own advantages, so choose based on your specific needs and the materials you’re working with.
Frequently Asked Questions (FAQs)
Now let us look at some FAQs I typically get asked.
What is the Purpose Of Stellite?
The purpose of Stellite is to provide a hard, wear-resistant surface for various applications. Stellite’s cobalt-chromium alloy excels in high-temperature environments, making it ideal for cutting tools and engine components. Its hardness can reach 450-600 HV (Vickers Hardness), depending on the specific grade used.
What is the Hardness Of Stellite Welding?
The hardness of Stellite welding can range between 40 to 60 HRC (Rockwell Hardness Scale). This makes it highly abrasion-resistant, allowing it to withstand extreme wear and tear. For comparison, tool steels typically reach a maximum of 65 HRC, showing Stellite’s impressive hardness.
Is Stellite Hard to Machine?
Yes, Stellite is hard to machine due to its toughness and high hardness. Specific cutting tools and techniques are essential for machining Stellite effectively. Typically, carbide tools with proper cooling and slower feed rates are recommended for best results.
What Are the Different Types Of Stellite?
Different types of Stellite include Stellite 1, Stellite 6, and Stellite 21, among others. These varieties offer unique compositions suited for specific applications like wear resistance or high-temperature strength. For example, Stellite 6 is popular in valve and wear-resistant applications.
What is a Stinger in Welding?
A stinger in welding refers to the anode clamp that holds the electrode in SMAW (Shielded Metal Arc Welding). It connects the welding machine output to the electrode. Using a proper stinger lets you maintain an arc and efficiently transfer heat with maximum control.
What is a Welding Stinger?
A welding stinger is the same as a stinger; it’s the tool that holds the electrode while you weld. It needs to be sturdy and electrically conductive to ensure a good connection. This helps you keep a stable arc for better weld quality.
Conclusion
I hope this was worth your while. We covered what stellite welding is, how it works, the different types of stellite welding, the steps involved, factors affecting the process, common issues, aftercare and inspection tips, typical applications, and other options available. Each of these points helps to paint a clear picture of stellite welding.
I hope these welding tips prove valuable to you. In short, stellite welding is a specialized process that uses stellite alloys to create strong, wear-resistant joints. With the right techniques and understanding, you can tackle complex applications in industries like aerospace and automotive.
For further insights into the world of welding, feel free to explore our homepage: What is Welding.
References
- American Welding Society. (2015). AWS D1.1/D1.1M: Structural Welding Code – Steel. Miami, FL: AWS.
- Lancaster, J. F. (1999). The Physics of Welding (2nd ed.). Oxford, UK: Pergamon Press.
- Blodgett, O. W. (1996). Design of Welded Structures. Cleveland, OH: James F. Lincoln Arc Welding Foundation.
Joe Carter is a retired welding professional with over 40 years of hands-on experience in the industry, spanning ship repair, structural welding, and even underwater projects. Joe is a master of MIG, TIG, and Stick welding. Passionate about mentoring the next generation of welders, Joe now shares his decades of expertise and practical insights to help others build rewarding careers in welding.
American Welding Society, Cobalt Alloys, Metal Coating, Stellite Welding, Wear Resistance, Welding, Welding Applications, Welding Equipment, Welding Techniques, Welding Tips