What is Short Circuit MIG Welding? Understanding Process, Types, and Factors
Published on: December 16, 2024 | Last modified: March 4, 2025
By: Joe Carter
Short circuit MIG welding is a welding technique that uses a low voltage to create a short circuit between the welding wire and the metal. This process produces molten metal that quickly bridges the gap to create a strong bond.
People are frequently curious about what is short circuit MIG welding. Understanding it’s crucial because it’s widely used in various industries. I’ve used this method in my projects, and it’s all about achieving clean, strong welds with minimal spatter.
In this guide, you’ll learn about how short circuit MIG welding works, the different types involved, and the steps to achieve an effective weld. Additionally, I’ll cover the factors affecting short circuit MIG welding, followed by answers to frequently asked questions. You’ll get a thorough understanding of this technique, including insights into what is short arc welding.
Contents
- What is Short Circuit MIG Welding?
- How Does Short Circuit MIG Welding Work?
- Types Of Short Circuit MIG Welding
- Steps to Achieve Short Circuit MIG Welding
- Factors Affecting Short Circuit MIG Welding
- Benefits of Short Circuit MIG Welding
- Common Uses of Short Circuit MIG Welding
- Frequently Asked Questions (FAQs)
- Conclusion
- Additional Reading
What is Short Circuit MIG Welding?
Short circuit MIG welding uses a low-voltage, high-current process to create a short circuit between the wire and workpiece. This method allows for excellent control and penetration. It’s often used for thin materials and in automotive applications due to its efficiency.
How Does Short Circuit MIG Welding Work?
Short circuit MIG welding, also known as short circuit transfer welding, involves continuously feeding a wire electrode. When the wire touches the workpiece, it creates a short circuit that interrupts the welding arc. This process happens at low arc voltages, typically between 15-25 volts. The low voltage ensures heat concentration is ideal for thin materials, usually less than 3 mm (0.118 In).
The melted wire creates a molten pool that transfers droplets of molten metal to the base material. This method offers excellent control, allowing welders to work at various positions and angles. It also minimizes spatter while ensuring a strong bond.
I once used short circuit MIG welding on a project with thin steel sheets. I found the process straightforward and manageable, even for tight joints. Compared to other methods, such as spray transfer welding, short circuit MIG offers more versatility for both beginners and experienced professionals.
Types Of Short Circuit MIG Welding
What are the types of this welding technique?
-
Gas Metal Arc Welding (GMAW)
GMAW is a common welding method that uses a continuous wire feed. It involves short circuit transfer, meaning the wire touches the weld pool. To perform this, feed the filler wire into the pool to create a quick electric arc that melts both the wire and base material.
-
Pulsed MIG Welding
Pulsed MIG welding alternates between high and low currents. This technique helps control heat and minimize defects. To use this method, adjust your welder to send pulses, allowing the wire to short circuit briefly at high amps and then cool at low amps, creating strong, stable welds. To fully understand this process and its components, it’s essential to know what items make up a basic semiautomatic welding system.
-
Flux-cored Arc Welding (FCAW)
FCAW uses a tubular wire filled with flux to produce welds. This technique can work well without shielding gas. To carry out FCAW, feed the flux-cored wire into the joint while initiating a short circuit. The flux creates a gas shield as the wire melts, resulting in a solid weld. If your equipment encounters issues during this process, understanding how to fix a welding machine can be crucial to maintaining effective operations.
-
Single Pass Welding
Single pass welding means completing the joint in one go. It’s efficient and suitable for thinner materials. To execute single pass welds, control your speed and wire feed, maintaining a short circuit for quick melting and solid bonding through the joint.
-
Multiple Pass Welding
This technique involves welding in multiple layers. It’s ideal for thicker materials. To use this method effectively, short circuit on the first pass, then build up layers by reapplying the weld in overlapping sections until you achieve the desired thickness and strength.
We’ve wrapped up the different types of short circuit MIG welding here. Next up, we’ll look at the steps to achieve it.
Steps to Achieve Short Circuit MIG Welding
Here are the steps to master short circuit MIG welding effectively.
-
Select the Right Equipment
Choose a MIG welder with short circuit transfer capabilities. Look for a unit that can handle wire diameters between 0.023 in (0.6 Mm) and 0.035 in (0.9 Mm) for optimal results. Selecting solid wire is crucial as it melts easily during short circuit MIG welding. Ensure you have a compatible gas, typically a blend of argon and carbon dioxide. Selecting the right equipment is essential, especially when considering the best cheap MIG welder options available.
-
Prepare the Workpiece
Thoroughly clean your workpiece to remove rust, oil, or other contaminants. Use a wire brush or grinder for a clean surface. Ensure the pieces fit snugly to reduce gaps that can lead to poor penetration. For thicker materials, align them properly to achieve a solid weld bead. Always wear protective gear to safeguard your eyes and skin from welding hazards, as welding without a mask can result in severe injuries.
-
Set Proper Parameters
Adjust the voltage and wire feed speed according to your material’s thickness. For example, use a wire feed speed of 200 to 350 inches per minute (5 to 9 M/min) with a voltage of around 15 to 20 volts for 0.030 in (0.8 Mm) wire. Incorrect settings can cause spatter or lack of penetration, so be proactive. Use a test piece to perfect your settings if you’re unsure.
-
Begin Welding Process
Start your arc by bringing the torch close to the workpiece. Move the torch in a slow, steady motion, maintaining a consistent distance. Pay attention to the puddle’s size and shape; it should be smooth and reflective. Moving too fast means weak fusion, while moving too slow risks burn-through.
-
Inspect Weld Quality
Check for uniformity in the bead width and perpendicularity to the base material. Look for signs of popping, which indicate inconsistent welding parameters. If necessary, adjust the settings and practice on scrap until you’re satisfied with the results. Strong welds will have a consistent color and a tidy appearance.
We’ve wrapped up the steps for achieving short circuit MIG welding here. Next up, we’ll look at factors influencing this process.
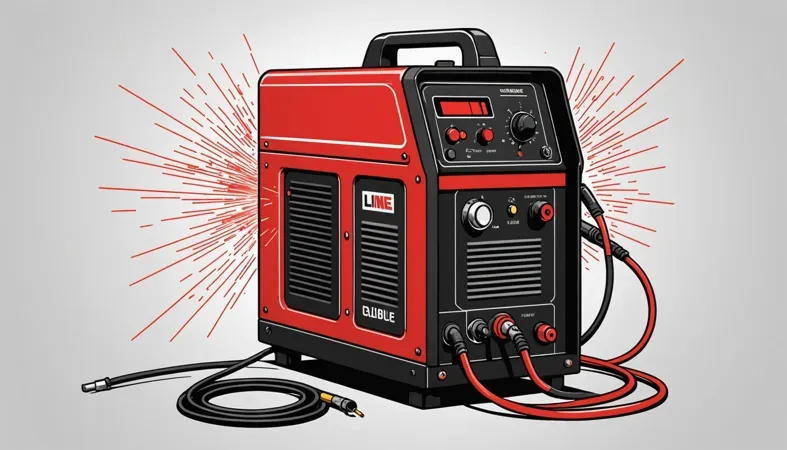
Factors Affecting Short Circuit MIG Welding
What factors impact the efficiency and quality of short circuit MIG welding?
-
Wire Type and Diameter
Choosing the right wire is crucial. A typical diameter ranges from 0.023 in. (0.6 Mm) to 0.045 in. (1.2 Mm); smaller wires provide better control in short circuit MIG welding.
-
Shielding Gas Composition
A mix of argon and CO2 affects stability. A gas ratio of 75% argon to 25% CO2 enhances puddle fluidity, which is essential for short circuit transfer welding.
-
Welding Speed
Welding speed influences heat input. A travel speed of 12 to 18 in/min (300 to 460 Mm/min) yields the best results for short circuit MIG welding.
-
Material Thickness
Material thickness dictates amperage requirements. Thin materials (Like 18 Gauge or 1.2 Mm) need around 80-100 amps for effective short circuit transfer.
-
Electrode Angle
The electrode angle is crucial for penetration. An angle of 10-15 degrees is ideal for maintaining a stable arc during short circuit welding.
That covers the elements influencing short circuit MIG welding. Let’s now take a look at the advantages of short circuit MIG welding.
Benefits of Short Circuit MIG Welding
Short circuit MIG welding offers several advantages that make it a popular choice among welders.
Benefit | Description | Impact |
---|---|---|
Minimized Spatter | This method generally produces less spatter compared to other welding techniques. | Cleaner welds mean less cleanup and rework. |
Versatility | Effective on various materials like steel, stainless steel, and some aluminum alloys. | Gives you a broader range of projects to tackle. |
Cost-Effectiveness | Lower equipment costs and reduced gas usage lead to savings. | Save money on both equipment and consumables. |
User-Friendly | Ideal for beginners, with straightforward techniques and settings. | Quicker learning curve promotes confidence in new welders. |
Excellent Control | Welder can easily control heat input and puddle size. | Enhances joint quality and reduces defects. |
We covered the advantages of short circuit MIG welding here. Next, we will cover its typical applications and uses.
Common Uses of Short Circuit MIG Welding
Here are some typical applications where short circuit MIG welding shines:
- Automotive Repair: Great for thin sheet metal repairs on cars and trucks.
- Fabrication: Widely used in manufacturing environments for building structures.
- Home Projects: Perfect for DIY enthusiasts tackling home repairs or fabrications.
- Metal Art: Artists use it to join various metal pieces for sculptures and installations.
- Construction: Useful in joining steel components in building frames.
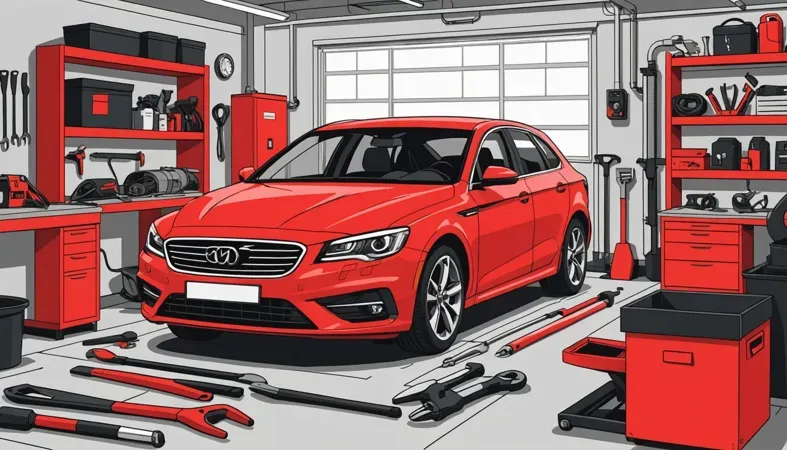
Frequently Asked Questions (FAQs)
Now let us look at some common queries I typically get asked.
What is the Difference Between Pulse MIG and Short Circuit MIG?
The difference between pulse MIG and short circuit MIG is in how the welding current flows. Pulse MIG uses a waveform that sends bursts of current, ideal for thinner materials, while short circuit MIG produces a stable arc by creating a short circuit between the electrode and the workpiece.
What Weld Defect is Most Common With Short Circuit MIG?
The most common weld defect with short circuit MIG is lack of fusion. This happens when inadequate heat connects the base metals, resulting in weak joints. Studies suggest that up to 20% of flaws in MIG welds can stem from this issue.
How Many Short Circuit Cycles Does a MIG Welder Undergo in a Second?
A MIG welder utilizing short circuit welding can undergo up to 200 short circuit cycles in one second. This rapid cycling helps in making consistent and efficient welds, especially in production environments. If you’re setting up a Lincoln Electric welder it is essential to configure it properly to achieve optimal performance and safety. Learn more about how to set up a Lincoln Electric welder for your specific needs.
What Types Of Materials Can Short Circuit MIG Weld?
Short circuit MIG can weld mild steel, stainless steel, and some aluminum alloys. These materials generally have melting points below 2000°F (1093°C), making them suitable for this technique.
Is Short Circuit MIG Welding Cost-effective?
Yes, short circuit MIG welding is cost-effective due to lower equipment costs and reduced shielding gas usage. You might save up to $0.05 (USD) per foot when welding compared to other methods.
Conclusion
Phew, we covered a lot. We talked about what short circuit MIG welding is, how it works, the different types, steps for achieving it, and factors that affect its performance. Plus, we answered some common FAQs to give you a well-rounded understanding.
Hopefully, I was able to impart some of my experience on what short circuit MIG welding really is. In simple terms, it’s a process where a continuously fed wire creates a short circuit to join metals, making it efficient for thinner materials. We discussed specifics like the way it operates, its advantages, and key factors that can influence your results.
For those eager to expand their knowledge on welding techniques, tips, and best practices, be sure to check out What is Welding, which has a wealth of information to deepen your understanding.
Additional Reading
- ISO. (2017). ISO 3834: Quality Requirements for Fusion Welding of Metallic Materials. Geneva, Switzerland: ISO.
- American Petroleum Institute. (2018). API 1104: Welding of Pipelines and Related Facilities. Washington, DC: API.
Joe Carter is a retired welding professional with over 40 years of hands-on experience in the industry, spanning ship repair, structural welding, and even underwater projects. Joe is a master of MIG, TIG, and Stick welding. Passionate about mentoring the next generation of welders, Joe now shares his decades of expertise and practical insights to help others build rewarding careers in welding.
Gas Metal Arc Welding, MIG Welding, MIG Welding Benefits, Short Circuit MIG Welding, Welding, Welding Materials, Welding Process, Welding Techniques, Welding Wire, Wire Diameter