What is a Good Welding Helmet? Key Features, Types, and Tips
Published on: May 10, 2025 | Last modified: March 4, 2025
By: Mark Carter
A welding helmet is a protective gear that shields your eyes and face while you weld. It gets darker when you strike an arc, keeping your vision safe from bright flashes.
So, if you are wondering what is a good welding helmet, you’re not alone. Finding the right helmet is crucial for your safety and comfort. Trust me, after a long day of welding, a good helmet makes a world of difference!
In this article, we’ll discuss what makes a good welding helmet, how it works, the different types available, steps for choosing the best options, key factors to consider, common issues, aftercare tips, and viable alternatives. Plus, we’ll answer questions like what is the lightest welding helmet and where can I buy a welding helmet.
Contents
- What Makes a Good Welding Helmet?
- How Does a Good Welding Helmet Work?
- Types Of Welding Helmets
- Steps to Choosing a Good Welding Helmet
- Essential Features to Look for in a Good Welding Helmet
- Factors Influencing a Good Welding Helmet
- What Could Go Wrong: Common Issues
- Aftercare, Inspection, and Advanced Tips for a Good Welding Helmet
- Applications Of Welding Helmets
- Alternatives That Might Work Better
- Frequently Asked Questions (FAQs)
- Conclusion
- Additional Reading
What Makes a Good Welding Helmet?
A quality welding helmet features a dark lens that shields your eyes from sparks and UV rays. It’s crucial for routine tasks like MIG and TIG welding, ensuring comfort and safety during long hours on the job.
How Does a Good Welding Helmet Work?
A good welding helmet protects your eyes and face from harmful UV and IR radiation. It has a lens that darkens automatically based on light intensity, usually within 1/25,000 of a second. Many helmets meet minimum eye protection standards like ANSI Z87.1 in the U.
S. Shade levels typically range from 9 to 13, helping you choose the right option for your welding needs.
For experts, it’s crucial to consider the helmet’s response time, weight, and comfort. Auto-darkening lenses with a fast response time enhance safety and visibility while you weld. A lightweight helmet is generally more comfortable and reduces neck fatigue during long welding sessions.
Consider features that suit your welding style. Think about the best welding helmet for your budget and choose a reputable brand. A solid helmet truly makes a difference in your welding experience!
Types Of Welding Helmets
What types of welding helmets should you know about?
-
Auto-darkening Welding Helmets
These helmets darken automatically when welding starts. Choose one with a fast switching speed, ideally less than 1/25,000 seconds. For top performance, look for an adjustable shading range of DIN 9 to 13. Brands like Lincoln Electric VIK offer great features. Selecting the right welding helmet is crucial, but determining what kind of welder you need can be equally significant.
-
Passive Welding Helmets
Passive helmets have a fixed shade lens. For good protection, select a lens shade of at least DIN 10. Check for durable materials like polycarbonate. Popular brands like ESAB A60 Sentinel provide strong options.
-
Solar-powered Welding Helmets
These helmets recharge the lens using solar panels. A reliable model includes a battery backup for extended use. Look for at least 20-40 hours of continuous use. Models like ESAB 07000008 are known for quality.
-
Digital Welding Helmets
Digital helmets feature advanced settings and options. A good model allows customizable modes for versatility. Seek models with memory functions and data displays; Optrel Crystal 2.0 is a solid choice.
-
Hybrid Welding Helmets
Hybrid helmets combine passive and auto-darkening features. Look for easy switching between modes. Check for adjustable sensitivity and delay settings; brands like ESAB often provide excellent hybrids.
We’ve wrapped up the various types of welding helmets here. Next up, we’ll look at how to choose a good welding helmet.
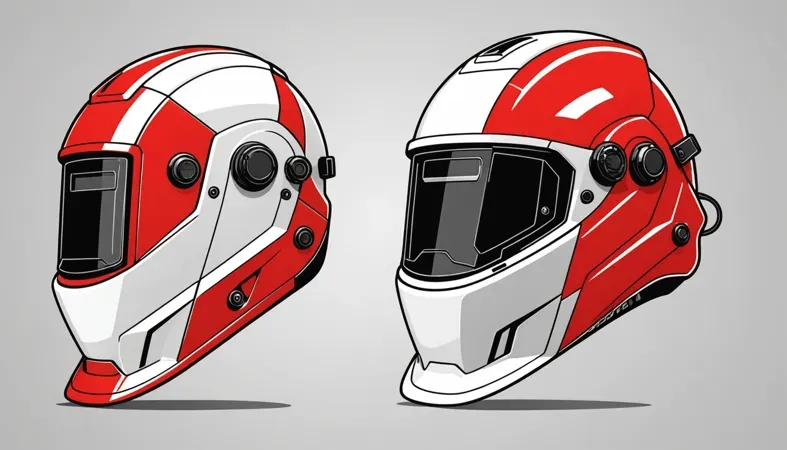
Steps to Choosing a Good Welding Helmet
Here are steps to find the best helmet for your needs.
-
Assess Your Welding Needs
First, determine what type of welding you’ll be doing: MIG, TIG, or Stick. Different jobs require different helmets. If you’re primarily doing MIG, a helmet with an adjustable shade of 9 to 13 is ideal. Identify your typical amperage (Usually Between 120 A and 300 A), as this also influences helmet selection.
Consider your work environment. If you’re welding outdoors in bright sunlight, choose a helmet with high UV protection. For dimly lit spaces, look for options with good optical clarity ratings (1/1/1/1 is the Best) to improve visibility while you work.
-
Choose the Right Lens Type
Choose between passive and auto-darkening lenses. Passive lenses have fixed shades, while auto-darkening ones adjust based on brightness. Shade numbers vary, with #10 providing good protection for most operations. For advanced scenarios, consider auto-darkening helmets that react in milliseconds, such as those from Lincoln Electric.
Look for helmets with two sensors for better arc detection. Some models let you adjust sensitivity levels. I’d recommend helmets with a wide viewing area (Approximately 10 Cm Wide) for better visibility during complex projects.
-
Confirm Comfort and Fit
Don’t overlook comfort. An adjustable headband can make a big difference during long work shifts. Find a model that fits snugly but isn’t too tight. Most welding helmets weigh around 1.5 lbs (0.68 Kg), reducing fatigue.
Check for ventilation options. Helmets like the Optrel Crystal 2.0 have built-in airflow systems to keep you cool. A helmet might fit well now, but if it doesn’t breathe, you’ll stop using it due to discomfort.
-
Review Brand Reputation and Features
Look for established brands like ESAB or Lincoln Electric, known for quality and durability. Reading reviews about models such as the ESAB A60 Sentinel W can provide insights on long-term wear and functionality.
Check warranty terms. A good warranty should last three years or more, covering damages beyond your control, indicating confidence in quality. Researching brands can save you money and frustration in the long run.
-
Gauge Cost Vs. Features
Finally, decide your budget without compromising safety. A good, affordable welding helmet ranges from $50 to $150. Look for models that effectively balance cost and features to get the best helmet within your budget. When considering difficult welding positions such as overhead work, it is essential to understand the techniques involved, which can be explored further in this guide on welding upside down.
You can often find highly rated helmets discussed in forums like Reddit, especially in beginner threads. Your final selection should prioritize essential features while being cost-effective.
We covered the process of selecting a suitable welding helmet. Next, we will explore the key features to consider.
Essential Features to Look for in a Good Welding Helmet
Understanding key features can help you find the perfect helmet for your welding tasks.
Feature | Description | Importance |
---|---|---|
Auto-Darkening Lens | Lens automatically darkens when welding starts, with response times less than 1/25,000 seconds. | Improves visibility and reduces eye strain. |
Shade Range | Lens shades typically range from DIN 9 to DIN 13. | Ensures proper protection against UV/IR rays. |
Viewing Area | A larger viewing area provides better peripheral vision. | Enhances overall visibility and control while welding. |
Comfort Features | Includes adjustable headgear and ventilation systems. | Increases comfort during extended use; reduces fatigue. |
Weight | Ideal helmets weigh around 1.5 lbs (0.68 kg). | A lightweight design prevents neck strain during long jobs. |
By focusing on these features, you’ll ensure that your helmet not only protects you, but also enhances your overall welding experience.
So far we covered the key features of a quality welding helmet. Next, let’s look at the factors that impact helmet selection.
Factors Influencing a Good Welding Helmet
What factors determine the quality of a welding helmet?
-
Welding Technique Considerations
Your welding technique directly influences helmet choice. Different techniques generate varying light levels, so you need a helmet with adjustable settings to protect your eyes effectively. For example, MIG (Metal Inert Gas) welding creates less UV radiation, while TIG (Tungsten Inert Gas) welding demands higher protection levels.
-
Visor Size and Coverage
A larger visor improves visibility and protection from sparks and UV light. Many helmets offer a lens size of around 2.5 x 4.5 inches (6.4 X 11.4 Cm), but bigger lenses significantly enhance your field of view. Consider your work environment when choosing the size.
-
Brand Reputation
.
Stick with trusted brands like Lincoln Electric or ESAB. They often deliver superior quality and safety features. Choosing a helmet from a reputable brand means you’ll likely get reliable customer support and warranty options.
-
Price Point and Budget
Setting a budget is essential before buying a helmet. Decent helmets start around $40, but investing $150 or more can provide superior safety features and comfort. Consider how often you’ll use it to determine your spending limit.
-
Durability and Material Quality
The helmet’s construction materials affect its lifespan. Choose helmets made of high-quality plastics or composites that can withstand heat and impact. A good helmet should last for years, so check for certifications like ANSI (American National Standards Institute) and ISO (International Organization for Standardization) for added assurance.
You should now have a good understanding of elements affecting a quality welding helmet. In the next part, we’ll discuss potential problems and common challenges.
What Could Go Wrong: Common Issues
Let’s look at specific problems that can occur with a welding helmet.
-
Inadequate Protection
If your welding helmet doesn’t fit properly, it won’t protect you well. Look for cracks or gaps. To fix this, adjust the straps or choose a snugger model that meets ANSI Z87.1 standards.
-
Lens Clarity Issues
Check the lens for scratches or fog, as this can hinder visibility while welding. Clean it with a soft cloth or replace it if it’s too damaged.
-
Comfort Problems
If your welding helmet feels heavy, it can cause neck strain. Consider lightweight options around 1.5 lbs (0.68 Kg). Choose helmets with adjustable padding for added comfort during longer jobs.
-
Inconsistent Darkening Response
If your welding helmet dims too slowly, it could lead to eye strain. Check the auto-darkening settings and replace the batteries if needed. Some welders prefer helmets with a sensitivity adjustment feature!
-
Battery Life Limitations
If your welding helmet relies on batteries, monitor their lifespan. An average auto-darkening helmet battery lasts 200-300 hours. Keep spares handy to ensure uninterrupted work.
Aftercare, Inspection, and Advanced Tips for a Good Welding Helmet
Here’s key advice for keeping your welding helmet in top condition.
Aftercare Tips
After using your welding helmet, remove particles and debris with a soft, dry cloth. Gently clean the visor with warm, soapy water (30 °C or 86 °F) to avoid scratches. Regularly check for buildup that could affect filtration—replace inner filters every 30 hours of use for optimal performance.
Ensuring proper wiring is crucial when setting up your equipment, and you can explore more about how to wire a Lincoln 225 welder effectively for safe and efficient operation.
Inspection Checklist
Start inspection by examining the auto-darkening lens sensitivity. Test adjustment settings using a standard product like an AiPM lens checker. Every week, check battery life—most lithium batteries last about 500-800 hours. I use a Miller Digital Elite and frequently inspect the grinding mode for accuracy.
Expert Tips
If you’ve welded for years, consider upgrading your shade selection based on the material. Use a variable shade lens for better adaptability across projects—choose between 5-13 for different processes. Ensure comfort by customizing the headgear settings to distribute weight, allowing for uninterrupted 10-12 hour sessions—your productivity depends on it.
Applications Of Welding Helmets
Welding helmets are used in various tasks across the industry. They have unique applications, such as:
- Automotive Repair: Welders use helmets to protect themselves while repairing car frames. The helmet shields them from sparks and intense light, making it popular in auto body shops.
- Pipeline Welding: Specialized helmets are crucial for welders working on pipelines. They often work in tough environments, and a good helmet protects their eyes from UV (Ultraviolet) exposure.
- Artistic Metal Sculpting: Artists wear welding helmets when creating metal sculptures. The variety of styles results in helmets that are both functional and visually appealing.
- Aerospace Manufacturing: In this field, workers need helmets with high-quality filters. These helmets are designed for precision welding, making them invaluable on the production floor.
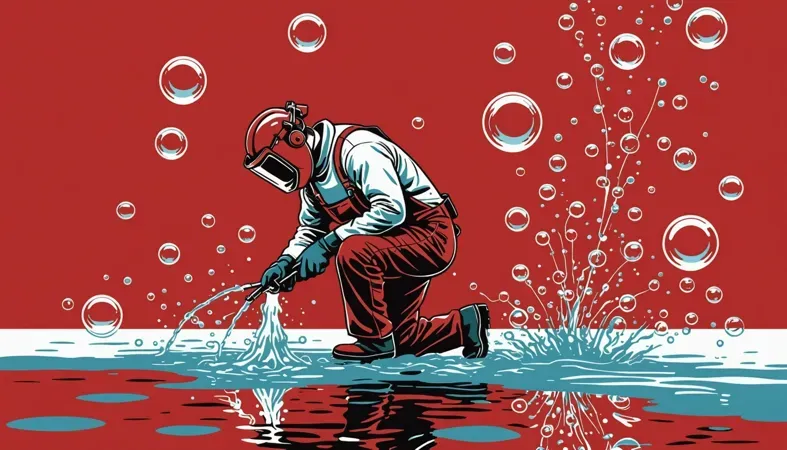
Alternatives That Might Work Better
When searching for welding protection, consider alternatives like face shields or even fixed shade hoods. These options can offer broader vision and a more lightweight feel. Products such as Optrel Crystal 2.0 provide excellent visibility without the weight of some traditional welding helmets.
Reflecting on my past experiences, it’s clear that sometimes simplicity wins. For instance, if you’re doing light-duty soldering, a fixed shade such as the Lincoln Electric VIK can be just as effective and more budget-friendly. So, don’t overlook these alternatives—sometimes the best solution isn’t the most obvious one!
Frequently Asked Questions (FAQs)
Now let us look at some questions I typically get asked about welding helmets.
What is the Best Type Of Welding Helmet?
Many ask, what is the best type of welding helmet? The best type of welding helmet combines auto-darkening and passive features. A good helmet should have a shade range of at least 9 to 13, protecting against harmful UV/IR rays, which can reach as high as 16,000 lux during welding.
Does a Good Welding Helmet Make a Difference?
Yes, a good welding helmet makes a significant difference. With better visibility and quicker reaction times, an auto-darkening lens can reduce eye strain by up to 80%. This can lead to better precision and control, improving overall welding results.
What is the Best Welding Helmet for the Money in 2024?
The best welding helmet for the money in 2024 is often one with excellent features at a reasonable price. You’ll find quality helmets ranging from $150 to $300 that offer high protection levels and durability, making them a great investment.
Where Can I Buy a Welding Helmet?
You can buy a welding helmet at various places. Check local hardware stores, online platforms like Amazon, or specialized welding supply websites. Prices typically start around $20 for basic models to $1,000 for high-end units, so match your needs with your budget.
How to Choose a Welding Helmet?
Choosing a welding helmet involves knowing your needs. Look for aspects like weight, comfort, and the type of welding you’ll do. Helmets under 1.5 kg (3.3 Lbs) are comfortable for long jobs, while adjustable settings enhance usability based on your work.
Conclusion
You made it to the end. We covered what makes a good welding helmet, how it works, the different types available, steps to choose one, factors to consider, common issues, aftercare, and alternative options. We also discussed practical applications and answered FAQs, all to help you make an informed choice.
So, what is a good welding helmet? A quality welding helmet offers safety, comfort, and functionality. Look for features like a proper shade rating (9-13), adjustable headgear, and lightweight materials. These details ensure you’re protected while keeping you comfortable during long jobs.
To further enhance your welding knowledge, feel free to explore our homepage: What is Welding
Additional Reading
- Lincoln Electric. (2020). The Procedure Handbook of Arc Welding (15th ed.). Cleveland, OH: Lincoln Electric Company.
Mark is a skilled welding engineer specializing in advanced metal joining technologies and process design. With a formal education in welding engineering and a background rooted in practical experience, Mark bridges the gap between theory and application. He is passionate about making technical concepts accessible, empowering welders to embrace innovation while mastering essential skills. Mark combines his scientific expertise with a commitment to supporting the welding community alongside his uncle, Joe.
Auto Body, Auto-darkening Lens, Certification, Construction, Helmet Features, Protective Gear, TIG Welding, Welding, Welding Helmet, Welding Safety, Welding Techniques