What Does Weld Passivation Do? Discover Protection, Processes, and Tips!
Published on: May 4, 2025 | Last modified: March 4, 2025
By: Joe Carter
Passivation is a chemical process that enhances the corrosion resistance of metals. It typically involves treating the metal with an acid solution to remove impurities, allowing a protective oxide layer to form.
I’ve received numerous inquiries about what does weld passivation do? Understanding this process is vital because it significantly impacts the longevity and strength of your welds. In my experience, proper passivation can prevent rust and corrosion, which is crucial for projects exposed to harsh environments.
In this guide, I’ll cover how weld passivation works, the different types, the necessary steps for passivation, factors affecting its effectiveness, and solutions for common issues. I’ll also discuss inspection and aftercare, applications you should know about, and potential alternatives. Plus, we’ll touch on related topics, like welding fundamentals to help ensure your welding projects are top-notch.
Contents
- What Does Weld Passivation Do?
- How Does Weld Passivation Work?
- Types Of Weld Passivation
- Steps for Weld Passivation
- Factors Affecting Weld Passivation
- How to Address Common Passivation Problems
- Applications You Should Know About
- The Importance of Weld Passivation in Various Industries
- Are There Any Alternatives to Weld Passivation?
- Frequently Asked Questions (FAQs)
- Conclusion
- References
What Does Weld Passivation Do?
Passivation creates a protective layer on stainless steel welds. This process boosts corrosion resistance, ensuring longevity. It’s commonly used in food processing and chemical industries due to its superior durability against harsh environments.
How Does Weld Passivation Work?
Weld passivation is a crucial process for stainless steel. It treats the weld area to enhance corrosion resistance by removing free iron and other contaminants from the surface. About 90% of stainless steel corrosion issues stem from inadequate passivation.
During passivation, a thin layer of chromium oxide forms. This layer acts as a protective barrier, reducing the likelihood of corrosion. It’s an effective way to ensure longevity in metal structures.
I recommend using a weld passivation machine after completing your welds. It makes a significant difference in preventing corrosion. Additionally, if you’re wondering how to avoid porosity in welding, passivation is a great step to maintain weld integrity.
Types Of Weld Passivation
So, what are the types of passivation used in welding?
-
Chemical Passivation
Chemical passivation uses specific chemicals to form a protective layer on metal surfaces. This process enhances corrosion resistance by removing free iron and contaminants. Typically, soak your welds in an acid bath, like citric acid, for about 20 to 30 minutes for best results.
It’s also crucial to understand various welding tools and techniques to ensure optimal results. To delve deeper into such aspects, explore how secondary power impacts welding.
-
Electrochemical Passivation
Electrochemical passivation uses electric current to trigger a protective layer on stainless steel. It effectively reduces the chance of corrosion while keeping the welds clean. To achieve this, submerge the welded steel in a solution and apply low voltage, which produces a titanium oxide layer in about 5 to 10 minutes.
-
Mechanical Passivation
Mechanical passivation involves physical methods, like sanding or brushing, to clean metal surfaces. This technique prevents corrosion by preparing the surface for further treatment. Use a soft abrasive pad to scrub the weld area for a clean finish before applying chemical or electrochemical methods.
-
Thermal Passivation
Thermal passivation uses high temperatures to create a protective layer on welded areas. It’s effective for alloys that need heat resistance. To perform this, heat the stainless steel weld to 300-400°C (572-752°F) for a specific duration, allowing oxidation to improve the protective oxide layer.
Understanding the techniques used in welding can significantly improve welding outcomes. One such technique that enhances the quality and durability of welds is a hot pass in welding.
-
Physical Passivation
Physical passivation creates a barrier layer against environmental factors, like moisture. This method enhances corrosion resistance indirectly. To implement this, apply a physical coating, such as a clear varnish, to the cleaned weld area for added long-term protection.
You should now have a good understanding of the various types of weld passivation. In the next part, we’ll discuss the steps for weld passivation.
Steps for Weld Passivation
Now, we’ll cover steps to enhance corrosion resistance and clean welds.
-
Surface Cleaning
Start by removing contaminants like grease or dirt from the welded area. Use a degreaser or a mix of warm water (40-50°C or 104-122°F) and mild soap. Thorough cleaning is essential for effective passivation. Ensure you cover every nook and cranny to avoid stubborn stains that could compromise the process. Understanding the health implications of welding is crucial for safety, and it’s important to prevent cancer from welding.
Once cleaned, use a non-metallic abrasive pad. This helps eliminate surface oxidation without scratching the stainless steel. I recommend using a clean cloth for the last wipe to ensure no residue remains.
-
Application Of Passivation Solution
Apply a passivation solution containing citric acid or nitric acid. A common mix for stainless steel is about 20-30% nitric acid (200-300 Grams Per Liter). Apply this with a brush or spray, following the manufacturer’s instructions for dwell time, typically 20-30 minutes.
Cover the entire weld and surrounding areas. The solution must remain in contact with the surface to effectively remove free iron and other contaminants. I’ve found that a sprayer provides better coverage for odd-shaped welds than a brush.
-
Rinsing the Surface
Once the dwell time is complete, rinse the area thoroughly with deionized water. Rinse for at least 10 minutes to ensure all residual acid is removed. Clean water is crucial, as any contaminants can trigger corrosion.
I recommend using a high-pressure rinse for larger areas to speed up this process. Effective rinsing ensures the integrity of the passivation and prepares the weld for drying.
-
Drying the Welded Area
After rinsing, dry the welded area with clean, dry air or a soft cloth. Quick drying is vital to prevent water spots and minimize oxidation. Ideally, dry the surface within an hour. In humid conditions, a heat gun can help expedite drying.
Working in a well-ventilated area speeds up evaporation. Don’t let any moisture linger to achieve optimal corrosion resistance.
-
Final Inspection
While we won’t detail the inspection process here, it’s wise to check for any residue or missed spots. Ensure the surface appears uniform and clean. If it looks good, you’ve successfully completed the welding passivation process. For those seeking clearer visibility while working, explore how to see better when welding.
If you see potential issues, don’t hesitate to ask. Early interventions can save time and hassle later on.
That covers the steps for weld passivation. Let’s now take a look at the factors influencing weld passivation.
Factors Affecting Weld Passivation
What factors affect the effectiveness of weld passivation?
-
Material Composition
The type of metal significantly influences passive layer formation. For example, stainless steel grades 304 and 316 passivate better than carbon steel, due to their higher chromium content, usually around 18% (By Weight), which promotes a stable oxide layer.
-
Surface Finish Quality
A smooth surface enhances passivation. Rough surfaces can trap contaminants, preventing effective passivation. Studies show that surfaces clean to 2.5 micrometers (Μm) or less achieve optimum results.
-
Environmental Conditions
Monitor the surrounding environment. Humidity and contaminants can disrupt passivation. High humidity levels, over 70%, can lead to corrosion and weaken the protective layer.
-
Passivation Duration
Longer passivation times are often better. Standard passivation can take 30 minutes to 24 hours, depending on the solution. Longer exposure increases the thickness of the protective oxide layer.
-
Temperature and Humidity Levels
High temperatures can speed up passivation, but excessive heat might damage the weld. Ideally, maintain temperatures around 50°F to 80°F (10°C to 27°C) for optimal results.
That covers the elements influencing weld passivation. Let’s now take a look at tackling typical passivation issues.
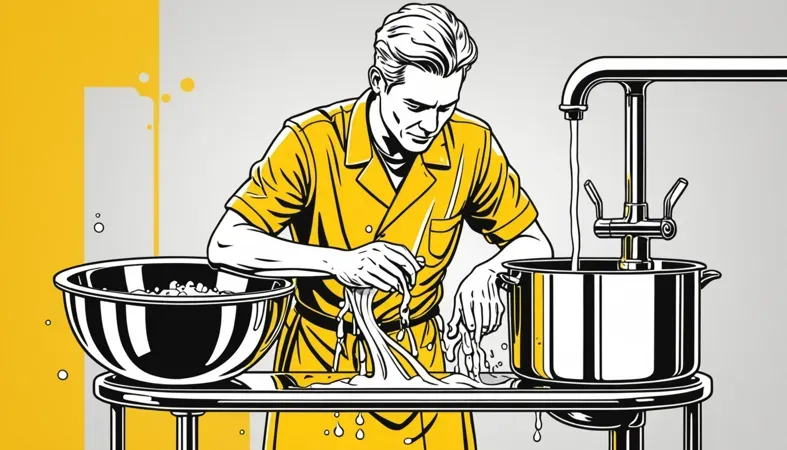
How to Address Common Passivation Problems
Let’s look at specific issues related to passivation.
-
Pitting Corrosion During Passivation
Passivation can cause pitting corrosion, often due to low acid concentration. Check for rusty areas or small holes. To resolve this, increase the acid concentration to 20-40% and repeat the passivation process.
-
Inconsistent Passivation Results
Inconsistent passivation results can arise from contamination. I recommend using a clean, dry cloth before processing. Ensure uniform surface cleanliness for consistent pH levels and outcomes.
-
Improper Surface Preparation
Effective passivation requires thorough surface preparation. Residual oils can hinder activation. Identify any residue and use a degreasing solution in hot water (60°C or 140°F) before applying passivation for optimal results.
-
Contaminated Passivation Solutions
Passivation solutions can become contaminated. Check for cloudiness or floating debris. To resolve this, filter the solution and replace any outdated components to maintain effectiveness.
-
Inadequate Rinsing
Poor rinsing can leave residues after passivation. If you see white streaks or hazy layers, rinse thoroughly with purified water to neutralize chemical activity completely.
That covers common passivation issues and their solutions. Let’s now take a look at relevant applications you should be aware of.
Applications You Should Know About
I’ve known people who use weld passivation for corrosion resistance. It has many applications, including:
- Food Industry Equipment: Passivation prevents rust on stainless steel surfaces in food processing. It’s popular for maintaining hygiene and safety.
- Aerospace Components: In aerospace, it enhances corrosion resistance on critical parts. Engineers value it for ensuring reliability under harsh conditions.
- Marine Applications: Weld passivation is essential for boats and ships to resist ocean corrosion. It’s recognized for extending equipment life.
- Chemical Processing Plants: This process maintains the integrity of tanks and pipes. Industry professionals trust it to reduce failures and maintenance costs.
The Importance of Weld Passivation in Various Industries
Understanding where weld passivation shines can elevate your welding projects.
Industry | Application | Benefits of Passivation |
---|---|---|
Food Industry | Processing equipment | Maintains hygiene, prevents rust |
Aerospace | Components and structures | Enhances reliability and durability |
Marine | Boats and ships | Protects against ocean corrosion |
Chemical Processing | Pipes and tanks | Reduces maintenance costs, prevents failures |
- Healthcare: Passivated surfaces in medical devices help prevent contamination and enhance safety.
- Architectural Applications: Exterior stainless steel features benefit from corrosion resistance, keeping them aesthetically pleasing and structurally sound.
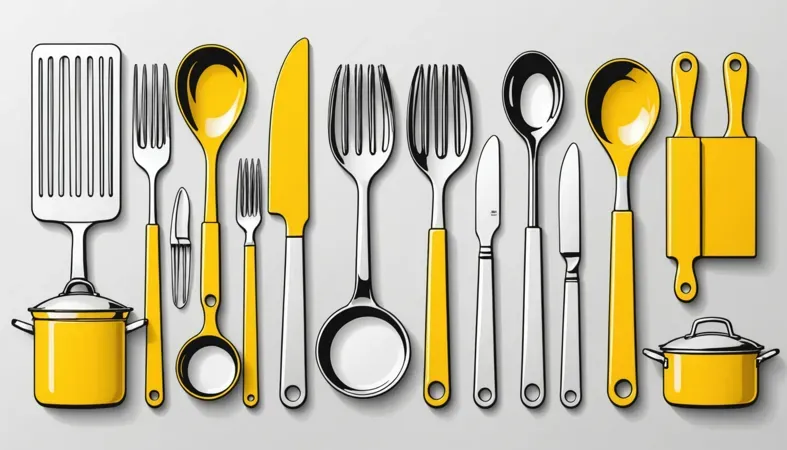
Are There Any Alternatives to Weld Passivation?
There are several alternatives to achieve the same effects as weld passivation. For instance, using a weld passivation machine can profoundly enhance corrosion resistance without passivation solutions. Products like Citrikote® offer chemical processes that effectively coat and protect welds while preventing rust.
In some cases, physical treatments such as shot peening can also improve surface integrity and reduce porosity. After all, having been through similar situations myself, I know these methods can be effective when traditional passivation might not fit your schedule or budget.
Frequently Asked Questions (FAQs)
Now let us look at some common questions I typically get asked.
How to Prevent Porosity in Welding?
To prevent porosity in welding, ensure proper gas shielding and clean surfaces. Contaminants like oil, moisture, or rust can lead to gas pockets trapped in the weld. Keeping surfaces clean boosts weld quality significantly and can reduce repair costs by up to 30%.
In a similar vein, understanding power requirements is crucial when considering modifications to welding equipment, such as converting a 220 welder to 110.
How to Avoid Blow Holes in Welding?
You can avoid blow holes in welding by controlling travel speed and arc length. Too fast of a travel speed can trap gas. For example, aim for a travel speed of 60-80 inches per minute (152-203 cm/min) to maintain consistency. Understanding proper welding guidance is crucial for achieving optimal results.
Additionally, understanding how to minimize other common issues is crucial, so learning ways to prevent spatter in welding can further enhance your welding quality.
Can You Weld Over Porosity?
No, you can’t weld over porosity without fixing it. Welding over porous areas leads to weak spots and can compromise the weld’s integrity. Inspect the weld and use proper techniques to fix any porosity before proceeding. Choosing the right shielding gas is essential to prevent porosity and achieve a strong weld, and you can find helpful information about what gas is used for welding.
How to Fix Pinholes in Welds?
To fix pinholes in welds, first, grind or sand down the affected areas. You should then reweld, using the right technique and settings. This process ensures a sound, clean weld free of cavities. For precision in welding, understanding how many 1/8 7018 rods you need is crucial.
What Happens if Stainless Steel is Not Passivated?
If stainless steel is not passivated, it can corrode more quickly due to oxidation. Passivation enhances corrosion resistance by forming a thin oxide layer on the surface, significantly improving durability and lifespan.
Conclusion
You made it to the end. We covered what weld passivation does, how it works, the types available, steps for passivation, factors that affect it, and how to address common problems. We also looked at aftercare, inspection tips, applications, and possible alternatives.
So, what does weld passivation do? In simple terms, it improves your welds by creating a protective layer that fights against corrosion, especially in stainless steel. It helps ensure strength and reliability, which is crucial for your projects. Wishing you success in your welding projects and remember, proper passivation can save you from issues like porosity and blow holes.
For those interested in expanding their knowledge on welding techniques, feel free to explore What is Welding.
References
- American Society of Mechanical Engineers. (2019). ASME Section IX: Welding and Brazing Qualifications. New York, NY: ASME.
- American Welding Society. (2015). AWS D1.1/D1.1M: Structural Welding Code – Steel. Miami, FL: AWS.
Joe Carter is a retired welding professional with over 40 years of hands-on experience in the industry, spanning ship repair, structural welding, and even underwater projects. Joe is a master of MIG, TIG, and Stick welding. Passionate about mentoring the next generation of welders, Joe now shares his decades of expertise and practical insights to help others build rewarding careers in welding.
American Welding Society, Corrosion Resistance, Metal Protection, Passivation Processes, Stainless Steel, Weld Passivation, Welding, Welding Equipment, Welding Quality, Welding Techniques