What Are the 5 Basic Types Of Welding Joints? Learn About Their Functions!
Published on: May 12, 2025 | Last modified: March 4, 2025
By: Joe Carter
Welding joints are connections made between two pieces of metal. They create a strong bond that holds them together.
People are frequently curious about what are the 5 basic types of welding joints. Understanding these joints is crucial because they affect the strength and durability of your work. From my experience, using the right joint can save you time and material in your projects.
In this article, we’ll cover how the five basic welding joints work, the steps to understanding them, factors that affect their performance, common issues, inspection and aftercare tips, real-world applications, and alternatives to welding joints. This will give you a comprehensive look at what are the 5 basic welding joints and help you become a better welder.
Contents
- What Are the 5 Basic Types Of Welding Joints?
- How Do the 5 Basic Types Of Welding Joints Work?
- Steps to Understanding Welding Joints
- Factors Affecting Basic Welding Joints
- Real-world Uses for Welding Joints
- Common Issues With Welding Joints
- What Are the Alternatives to Welding Joints?
- Final Thoughts
- Frequently Asked Questions (FAQs)
- Conclusion
- References
What Are the 5 Basic Types Of Welding Joints?
Welding joints connect different metal parts. Common types include butt, lap, corner, edge, and T-joints. Each has unique strengths suited for specific applications like construction or automotive, ensuring durability and stability.
How Do the 5 Basic Types Of Welding Joints Work?
Butt Joints
Butt joints connect two pieces of metal edge to edge. They’re often used in plate welding and are common in pipelines, where strength is crucial. To create a solid joint, you typically apply heat and filler material, achieving up to 90% of the base material’s strength.
Corner Joints
Corner joints form at right angles, where two members meet, resembling a picture frame. Welding requires precise alignment for a secure bond. When made correctly, corner joints can hold loads effectively, so attention to detail is essential.
Tee Joints
Tee joints occur when one member rests on another, forming a T shape. This type is common in structural steel projects, serving as connection points for beams and braces. A well-executed tee joint distributes weight effectively, enhancing stability.
Lap Joints
Lap joints overlap two pieces of metal, providing a larger area for welding. This type is popular in sheet metal applications, allowing for easy filling of gaps with weld material, making the process simpler to manage.
Edge Joints
Edge joints connect the edges of two workpieces. They’re useful when other joint types can’t be used and require finesse. Proper technique ensures a strong seal at the junction of the materials.
So, what are the five basic types of welding joints? They are butt joints, corner joints, tee joints, lap joints, and edge joints. Welding joints not only connect materials but also play a significant role in handling stress. For instance, butt joints are ideal for high-stress applications.
From my experience, choosing the right joint type is vital. The right joint can make or break a project’s integrity. Understanding joints is a cornerstone of successful welding.
Steps to Understanding Welding Joints
What are the different types of joints in welding?
-
Butt Joint
A butt joint joins two ends of metal together. It’s one of the simplest welding joints. To make a butt joint, align two flat pieces so their edges touch, then weld along the seam using methods like MIG or TIG welding.
-
Lap Joint
A lap joint overlaps two metal pieces, allowing for a strong bond and easy assembly. To create a lap joint, place one plate over another and weld along the edges. This is great for sheets or plates requiring strength. When considering how to handle more challenging materials, you might wonder, can you weld cast iron.
-
Corner Joint
In a corner joint, two pieces meet at a 90-degree angle. This is common in frames and boxes. To weld a corner joint, position the two pieces to form the corner, then fuse the edges from the outside with short, continuous welds.
When dealing with angled joints, achieving precision in your welds can improve structural integrity, especially when learning how to weld 45-degree angles.
-
Edge Joint
An edge joint connects the edges of two pieces, often for thin sheets. This setup supports sheets well. To form an edge joint, align the edges of the plates side by side and weld along the edges.
-
Tee Joint
A tee joint occurs when one piece is perpendicular to another, forming a T shape. It’s used in structures. To create a tee joint, position the piece on top of the other and weld the intersection area to secure it.
We’ve wrapped up the steps for understanding welding joints. Next up, we’ll look at factors influencing basic welding joints.
Factors Affecting Basic Welding Joints
Material Thickness
Joint Design
Welding Position
Heat Input
Welding Environment
Now, we’ll cover the steps to understand the five basic types of welding joints. Each step will guide you in creating effective joints for your project.
-
Understand Butt Joints
Start by examining butt joints. They connect two pieces of metal end-to-end, ideal for thick materials. For metals around 6 mm (0.24 In) thick, a V or bevel preparation aids penetration. Ensure your torch is at the right angle to avoid undercutting.
When welding butt joints, set the current based on thickness. For example, around 90 amps for 6 mm (0.24 In) steel typically works. Proper fit-up is vital; no gaps ensure better-quality seams.
-
Learn About Lap Joints
Next, dive into lap joints. They overlap, typically joining two plates at angles. Maintain at least a 1.5 times thickness overlap, especially for sheets under 3 mm (0.12 In) thick. This creates stronger bonds and better tensile support.
Fill the joint fully; using stringer beads avoids excess heat that could distort the metal. The torch angle and travel speed significantly affect penetration—the more controlled they are, the neater the joint.
-
Explore Corner Joints
Now, focus on corner joints, useful for joining two pieces at a right angle. Proper fit is key, as gaps lead to weak welds. Aim for a 90-degree angle, and consider a bevel for better access with thicker materials.
Use a good fill technique—pulsing your arc can eliminate burn-through. Don’t rush; a gradual travel speed results in cleaner corners. You’ll notice a difference after practicing a few runs.
-
Highlight Edge Joints
Edge joints are important too, especially when joining two flat surfaces edge-to-edge. These joints can create weaker connections, so increase your heat input. Prepping edges with a small bevel boosts weld penetration.
For thin materials, precision is necessary. A width of 0.5 mm (0.02 In) typically ensures proper penetration. Control your speed to maintain a solid weld nugget, ensuring strength.
-
Master T-joints
Finally, master T-joints, where one piece connects perpendicularly to another. These joints can be tricky but are common in frames and structures. Use a high amperage setting for heavy-duty applications to ensure deep penetration. An alignment jig is helpful while you weld.
When moving along the joint, make short passes to minimize distortion and shrinkage, which can complicate cross-sectional pressure points. Typically, 1/8 in (3.17 Mm) steel requires about 150 amps for optimal results.
That covers the elements influencing basic welding joints. Let’s now take a look at practical applications for welding joints.
Real-world Uses for Welding Joints
Here’s some practical advice on aftercare, inspection, and tips for your welding joints.
Aftercare Tips
After sealing your joints, clean heat-affected areas with a wire brush or grinder. Use a 10% acetic acid (Vinegar) solution to counteract oxidation. If corrosion is a risk, apply a protective coating shortly after welding to prevent moisture damage. It’s crucial to address skin injuries caused by welding promptly to avoid complications; find out how to treat welding burns.
Inspection Guidelines
Inspect welds with a magnifying glass for cracks smaller than 0.5 mm (0.02 Inch). For fillet joints, measure leg length, aiming for at least 3 mm (1/8 Inch) for adequate strength. I use an ultrasonic testing tool, like the UT-200, to detect subsurface flaws effectively. To ensure comprehensive understanding of weld diagrams and their specifications, you might find it helpful to learn about reading weld symbols.
Expert Tips
If you’re experienced, adjust your electrodes to a 15-degree angle for better penetration. Preheat thicker materials over 6 mm (1/4 Inch) for 15-30 minutes to reduce warping. Lastly, maintain proper thermal cycling between passes for optimal structural integrity.
We’ve wrapped up practical applications, advantages, and examples of welding joints here. Next up, we’ll look at frequent challenges with welding joints.
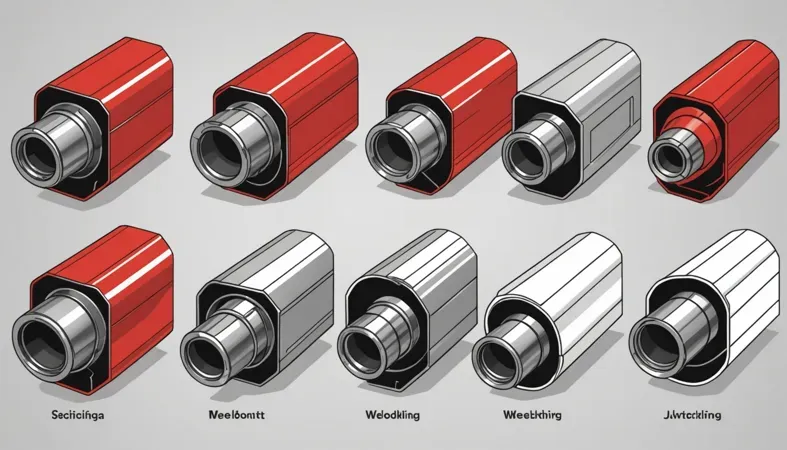
Common Issues With Welding Joints
Poor Joint Alignment
Inadequate Penetration
Weld Cracking
Incomplete Fusion
Porosity
What factors affect welding joint types? Understanding them is crucial for strong welds.
-
Material Compatibility
Different materials react differently during welding. For example, mixing aluminum with steel often results in poor weld quality.
-
Welding Technique
The technique you choose impacts the final result. Stick welding and MIG yield very different joint qualities. Each method has its quirks.
-
Heat Control
Temperature is vital in welding. Too much heat can cause warping, while too little may not melt the joint completely.
-
Environmental Conditions
Welding outdoors or in damp areas can be problematic. Moisture can lead to porosity in the weld, affecting its strength.
-
Joint Design
Simple joints are easier to weld. Complexity can lead to more issues, especially with seal welding. The joint type should match your process.
That covers common problems found in welding joints. Let’s now take a look at alternatives to welding joints.
What Are the Alternatives to Welding Joints?
I’ve known people to use welded joints for structural steel tasks. However, there are many alternatives, including:
- Butt Joint: Used for joining two plates edge-to-edge in shipbuilding. It’s popular for its high strength and low weight, which are crucial for marine vessels.
- T Joint: Common in fabricating frames and brackets. It provides stability and structural integrity, essential for constructing heavy machinery.
- Lap Joint: Ideal for joining overlapping materials in piping systems. Its ease of fabrication makes it a popular choice in the oil and gas industry.
- Corner Joint: Frequently used in furniture and duct fabrication. It creates clean 90-degree angles, enhancing both aesthetic appeal and strength.
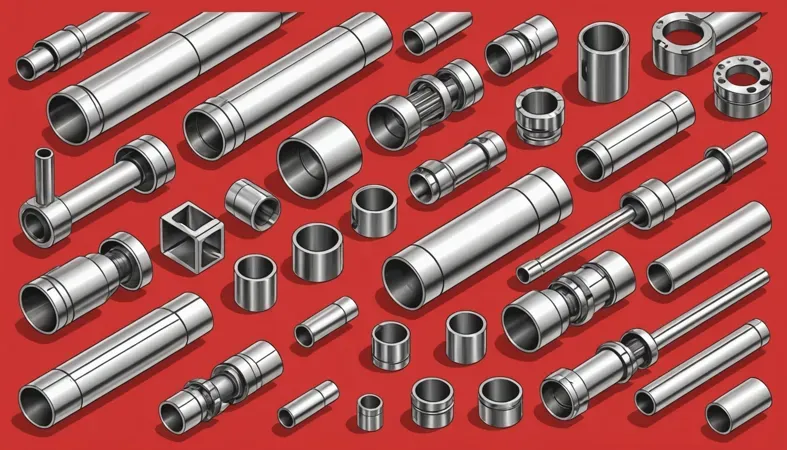
Final Thoughts
While understanding traditional welding joints is crucial, there are alternatives to achieve similar results. For example, adhesive bonding with products like Loctite or epoxy can work where heat isn’t suitable, especially on sensitive materials. I’ve seen this approach shine in automotive applications, where a seamless finish is vital. For those considering diverse methods involving welding, it’s also interesting to explore the cost of welding rods.
Another option is using mechanical fasteners, such as rivets or bolts, especially in cases where disassembly is needed later. Over time, I’ve observed that these methods can provide strong connections while avoiding the challenges that welding sometimes presents. Choosing the right method often depends on your materials and conditions. When welding on vehicles, it is crucial to know what to disconnect beforehand.
Frequently Asked Questions (FAQs)
Now let us look at some questions I typically get asked.
What is the Strongest Type Of Weld Joint?
The strongest type of weld joint is a butt joint. A butt joint allows pieces to be welded end-to-end, providing high strength and minimal heat zones. In structural applications, this joint type can support loads up to 40,000 pounds (18,144 Kg) per inch of weld. It is crucial to understand how welding rods should be stored to maintain their effectiveness, which you can explore further by learning about proper storage techniques.
What Are the Advantages Of Using MIG Welding?
MIG welding offers several advantages, including speed and ease of use. It’s perfect for thicker materials and provides a clean, strong weld without much cleanup. MIG can achieve welding speeds of 20 inches (50 Cm) per minute, making it suitable for production work.
How Do Welding Joints Affect Weld Quality?
Welding joints significantly affect weld quality as different joint designs influence penetration and fusion. For example, a V-joint can enhance penetration in thicker metals, ensuring weld strength. Proper joint design can increase weld durability and minimize defects.
What Materials Can Be Welded Together?
You can weld a variety of materials, including steel, aluminum, and stainless steel. Proper welding techniques and filler materials are vital for achieving strong bonds. Did you know different materials require different welding processes, like TIG for aluminum?
How Do I Choose the Right Welding Process?
Choosing the right welding process depends on several factors. Consider material type, thickness, and position. For instance, MIG is ideal for thicker metals, while TIG suits thinner materials due to its precision. Understanding the appropriate process for each situation can significantly improve results, which is where practical welding guidance becomes invaluable.
Conclusion
We’ve reached the end, and I appreciate you sticking around. We covered the five basic types of welding joints: butt, lap, T, corner, and edge. Additionally, we discussed how they work, critical factors affecting them, common issues, aftercare, inspection tips, real-world uses, and even alternatives. If you’re looking to expand your knowledge further, understanding welding fundamentals can provide you with valuable insights and techniques.
In summary, the five basic types of welding joints—butt, lap, T, corner, and edge—each serve specific purposes in metal joining. Understanding these joints is essential for effective welding because they affect strength and durability. Now you know what they are, how they function, and why they’re crucial in various applications.
For additional resources and expert insights on welding techniques, tips, and best practices, be sure to visit What is Welding.
References
- American Welding Society. (2020). AWS Welding Handbook: Welding Science and Technology (Vol. 1). Miami, FL: American Welding Society.
Joe Carter is a retired welding professional with over 40 years of hands-on experience in the industry, spanning ship repair, structural welding, and even underwater projects. Joe is a master of MIG, TIG, and Stick welding. Passionate about mentoring the next generation of welders, Joe now shares his decades of expertise and practical insights to help others build rewarding careers in welding.
Adhesive Bonding, American Welding Society, Metalworking, MIG Welding, Structural Integrity, Types Of Welding, Welding, Welding Applications, Welding Joints, Welding Techniques